Additive manufacturing (AM), commonly known as 3D printing, is a groundbreaking technology that is transforming the modern manufacturing industry. Among its various applications, metal-based AM has emerged as a key player in producing high-performance mechanical systems for industrial production.
This disruptive technique constructs components with intricate geometries through a precise layer-by-layer process. By optimizing material usage and streamlining production, AM significantly reduces waste and minimizes the number of manufacturing steps. Metal AM, in particular, has garnered considerable attention in the aerospace industry due to its exceptional material utilization efficiency, short production cycles, and minimal need for post-processing.
Titanium and its alloys, such as 316L stainless steel, AlSi10Mg, and Ti–6Al–4V, are widely used to create dense, high-performance components. In this blog, we’ll explore titanium in depth—its remarkable mechanical properties, key applications, and the industries that rely on its strength and versatility.
TABLE OF CONTENTS
- Titanium: Strength, adaptability and efficiency
- Ti-6A4I-4V Alloy
- Challenges in traditional Titanium manufacturing
- Advantages of 3D printing with Titanium using Meltio
- Challenges of traditional titanium manufacturing
- Why Meltio’s 3D printing is a smart choice
- Main applications forTi64 industry
- Microstructure of Ti64 printed on Meltio systems
- Meltio mechanical properties
- Parts manufactured with Titanium
- Conclusion
1. Titanium: Strength, adaptability and efficiency
Over the past decade, additive manufacturing (AM) has evolved from rapid prototyping and small-scale production to large-scale mass production. Several widely used alloys, including 316L stainless steel, AlSi10Mg, and Ti–6Al–4V, have been successfully employed to produce dense, high-performance components.
As above-mentioned, one of the most significant advantages of AM from a materials perspective is its near-net-shape forming capability.
The W-LMD technology produces parts with exceptional microstructure and a density of 99.998%, surpassing the properties of castings and rivaling those of forgings.
By building components layer by layer based on digital models, AM enables the production of metallic parts with complex geometries in a single step, eliminating the need for labor-intensive and costly machining processes. This is particularly beneficial for hard-to-machine materials such as titanium alloys and superalloys, which are traditionally challenging and expensive to process.
Due to their high cost and poor machinability, titanium alloys are primarily used in high-end applications. However, AM presents a transformative opportunity to reduce processing costs for these materials, thanks to its high degree of design freedom and efficiency. Titanium and its alloys have garnered significant interest in metal AM, largely because of the high machining costs associated with conventional manufacturing. In the past, impurity control—especially oxygen contamination, posed a challenge for AM-produced Ti alloys. However, recent advancements in AM technologies, such as directed energy deposition (DED), have significantly improved impurity management.
Moreover, AM-processed Ti-alloy parts often exhibit superior mechanical properties compared to their wrought or cast counterparts, primarily due to the unique microstructures formed during the AM process. These advancements further solidify AM’s potential in revolutionizing the production of titanium alloys and other hard-to-machine materials.
Titanium undergoes an allotropic transformation at 882°C, transitioning from a close-packed hexagonal structure to a more open body-centered cubic structure. This transformation allows for complete phase changes during heat treatments. Additionally, titanium exhibits a remarkable ability to dissolve other elements through either substitution or interstitial mechanisms. Depending on the number of bonding electrons of the introduced element, one of the two allotropic phases tends to be stabilized.
One of the most outstanding properties of titanium and its alloys is their exceptional corrosion resistance. This is due to titanium’s rapid reaction with oxygen, which forms a thin, impermeable oxide layer on the surface. This protective layer acts as a barrier, significantly enhancing both oxidation and corrosion resistance.
2. Ti-6AI-4V Alloy
Ti64, a titanium alloy composed of 90% titanium, 6% aluminum and 4% vanadium, has diverse applications in industry due to its excellent mechanical properties, corrosion resistance and high temperature resistance.
Ti-6Al-4V is the most widely used titanium alloy in industrial applications, accounting for approximately half of all titanium metal production. Its widespread use is attributed to its excellent balance of mechanical properties, corrosion resistance, and high-temperature performance. Additionally, it is highly machinable and can have its properties tailored through heat treatments, making it a versatile choice across various industries.
3. Challenges in traditional Titanium manufacturing
Traditional titanium manufacturing presents a number of challenges that hinder its efficiency and cost-effectiveness. The machining of titanium, for instance, is notoriously difficult due to its propensity to wear down tools quickly. This leads to frequent tool replacements and increased operational costs. Additionally, the material itself is expensive, and subtractive processes, where material is cut or drilled away, result in significant waste. Titanium also poses a challenge in terms of weldability; it is highly susceptible to oxidation, particularly in the absence of a controlled atmosphere, complicating the welding process and further increasing production costs.
4. Advantages of 3D printing with Titanium using Meltio
On the other hand, the advent of 3D printing technology, particularly with systems like Meltio, offers notable advantages. One of the primary benefits is the reduction in material waste. Unlike traditional subtractive manufacturing, 3D printing only uses the material necessary for the creation of the part, making it a more sustainable option.
Furthermore, 3D printing offers unparalleled design flexibility, allowing for the creation of complex geometries that would be difficult or even impossible to achieve through conventional methods. This flexibility not only enhances design possibilities but also reduces the need for multiple manufacturing steps, further cutting costs. Lastly, 3D printing with Meltio delivers superior energy efficiency when compared to traditional methods like forging and machining, making it a more environmentally friendly and cost-effective alternative.
5. Challenges of traditional titanium manufacturing
Manufacturing titanium using traditional methods comes with several difficulties that increase costs and complexity.
Difficult machining
Wire feedstock is a cost-effective welding commodity that reduces both material consumption and finishing time
High costs
Thanks to its higher material efficiency, the process is faster whilst requiring lower laser power
Welding issues
Titanium oxidizes easily when exposed to air, so welding requires a controlled atmosphere, adding another layer of difficulty and expense.
6. Why Meltio’s 3D printing is a smart choice
3D printing with Meltio offers a modern approach that solves many of these challenge:
Less material waste
Unlike traditional cutting methods, 3D printing builds parts layer by layer, using only the material needed.
More design flexibility
Complex shapes and intricate geometries are easier to produce, allowing for more innovation.
Lower costs
Reducing material waste and simplifying production steps help cut down overall expenses.
Better energy efficiency
Compared to forging and machining, 3D printing consumes less energy, making it a more sustainable option.
With these advantages, 3D printing with Meltio is a game-changer for titanium manufacturing, making the process more efficient, cost-effective, and environmentally friendly.
TIP: Know more about compatible and Meltio materials by downloading the Meltio Materials Printable List.
7. Main applications for Ti64 industry
- Aerospace industry
Aerospace components must endure harsh operating conditions while remaining lightweight. Titanium alloys are highly favoured in the aerospace sector due to their excellent strength-to-weight ratio, fracture toughness, fatigue resistance, and outstanding corrosion resistance.
- Automotive industry
It is used in the manufacture of high-performance parts, such as engine components (valves, pistons) and suspension systems, especially in high-performance vehicles due to its lightweight and fatigue strength.
- Energy industry
Ti64 is used in wind turbine components where mechanical and corrosion resistance is required in extreme environments. In power plants, Ti64 is used to manufacture components that operate at high temperatures, such as generator parts and heat exchange systems.
- Marine industry
Ti64’s resistance to corrosion makes it suitable for applications in the marine industry, especially in the manufacture of components that will be in contact with seawater
- Defense industry
Ti64 is also used in military applications due to its resistance to impact and high temperatures, in armored vehicle components and armaments, where durability and strength are essential.
TIP: Check out Meltio’s Defense webpage!
8. Microstructure of Ti64 printed on Meltio systems
The microstructure of Ti64 in additive manufacturing is dominated by rapid solidification and grain growth directionality. Unlike forged Ti64, which exhibits an equiaxial structure, columnar and acicular structures are observed in additive manufacturing due to the high cooling rate.
In the microstructure of Ti64 printed with Meltio technology, well-defined grain boundaries are observed, characteristic of a solidification process in the molten state without subsequent heat treatment. In our process, the heat input favors the growth of columnar grains in the deposition direction.
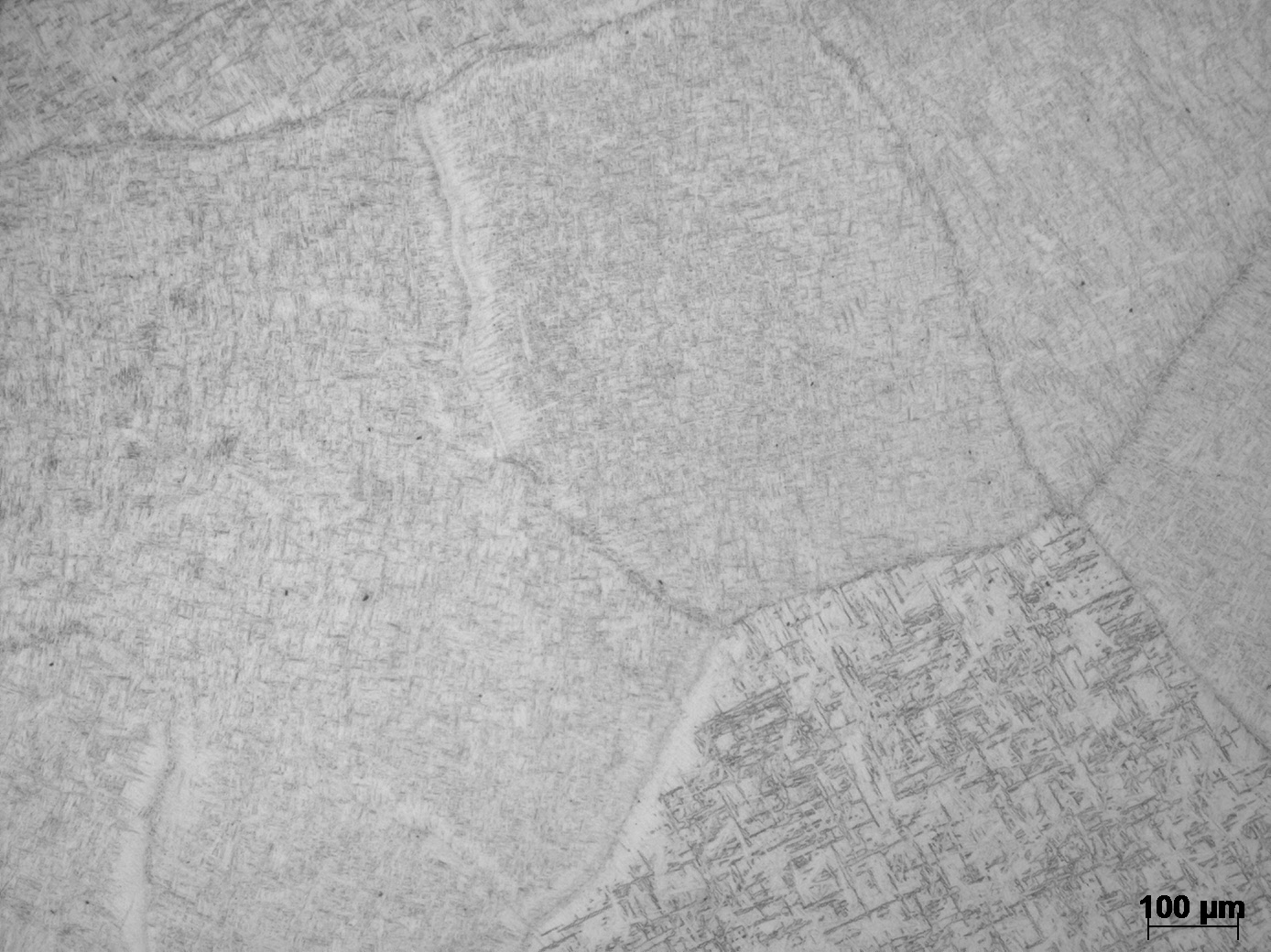
Within the grains, a network of acicular structures can be distinguished, indicative of the formation of martensitic α’ phase. In LWDED, rapid cooling prevents the transformation into a balanced microstructure of α and β phases, which favors the appearance of α’. This phase confers high mechanical strength to the material, but at the cost of lower ductility and fracture toughness compared to heat-treated materials.
Also, no clear regions with intergranular β phases are apparent. A heat treatment as described in the Ti64 datasheet would allow the transformation of the microstructure into a more balanced distribution of α and β, improving the ductility and fatigue strength of the material.
9. Meltio mechanical properties
As can be seen in the following table, the use of our Meltio M600 system with an inert chamber improves the properties of titanium due to the absence of oxides in the microstructure. The presence of these oxides decreases the ductility of the alloy, impoverishing the mechanical properties. The table also shows how the use of heat treatment favors the equilibrium between the α and β phases, increasing ductility and possibly fatigue life.
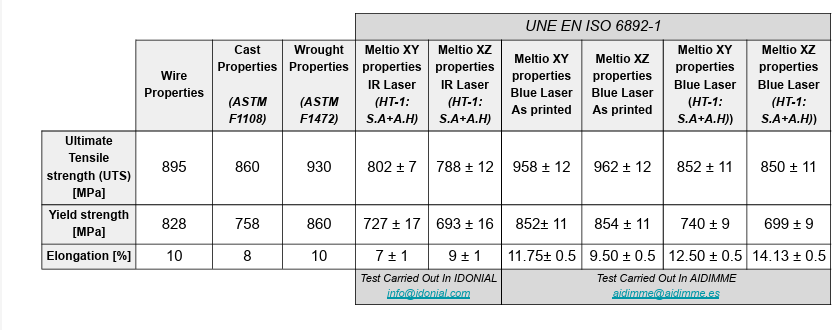
10. Parts manufactured with Titanium
CAR KNUCKLE
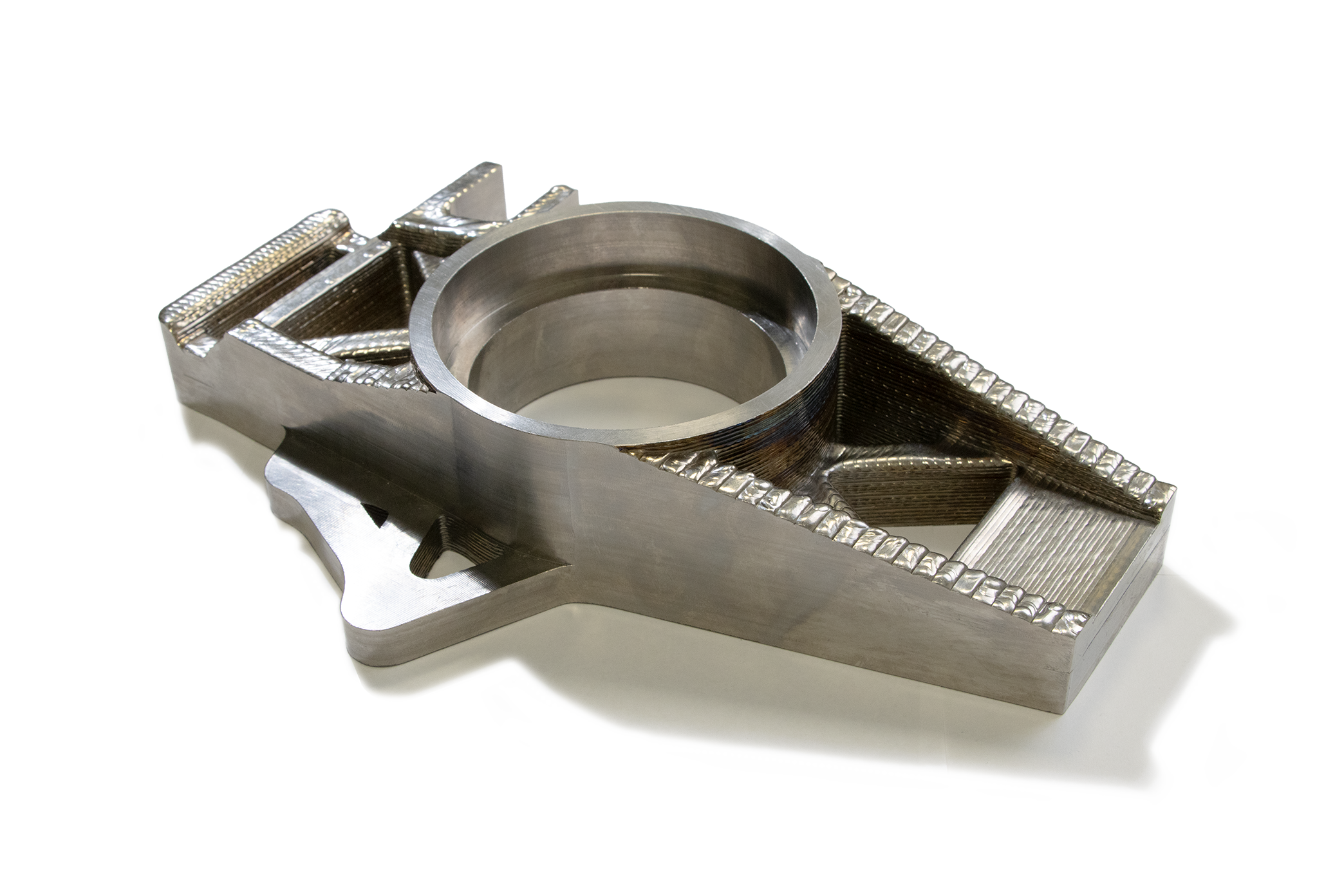
Traditional manufacturing
Forging: Metal is heated and shaped under pressure. Ideal for simple parts but requires machining for precision.
Casting: Molten metal is poured into molds. Works for complex shapes but still needs machining for final specs.
CNC Machining: Parts are carved from solid blocks. Highly precise but costly and time-consuming for small runs.
Meltio’s Additive Manufacturing
Design flexibility: Allows for complex geometries and intricate shapes that are difficult with traditional methods.
Weight reduction: Creates lightweight parts, lowering unsprung mass, improving handling, and enhancing suspension responsiveness.
Material options: Can use advanced materials like Titanium for strength and lightness.
Rapid production: Quick turnarounds for small batches and prototypes, with no need for expensive tooling or molds.
Cost-effective for low volumes: No need for costly setup, making it ideal for small batches or custom designs.
TITANIUM AIRCRAFT FLAP ACTUATOR
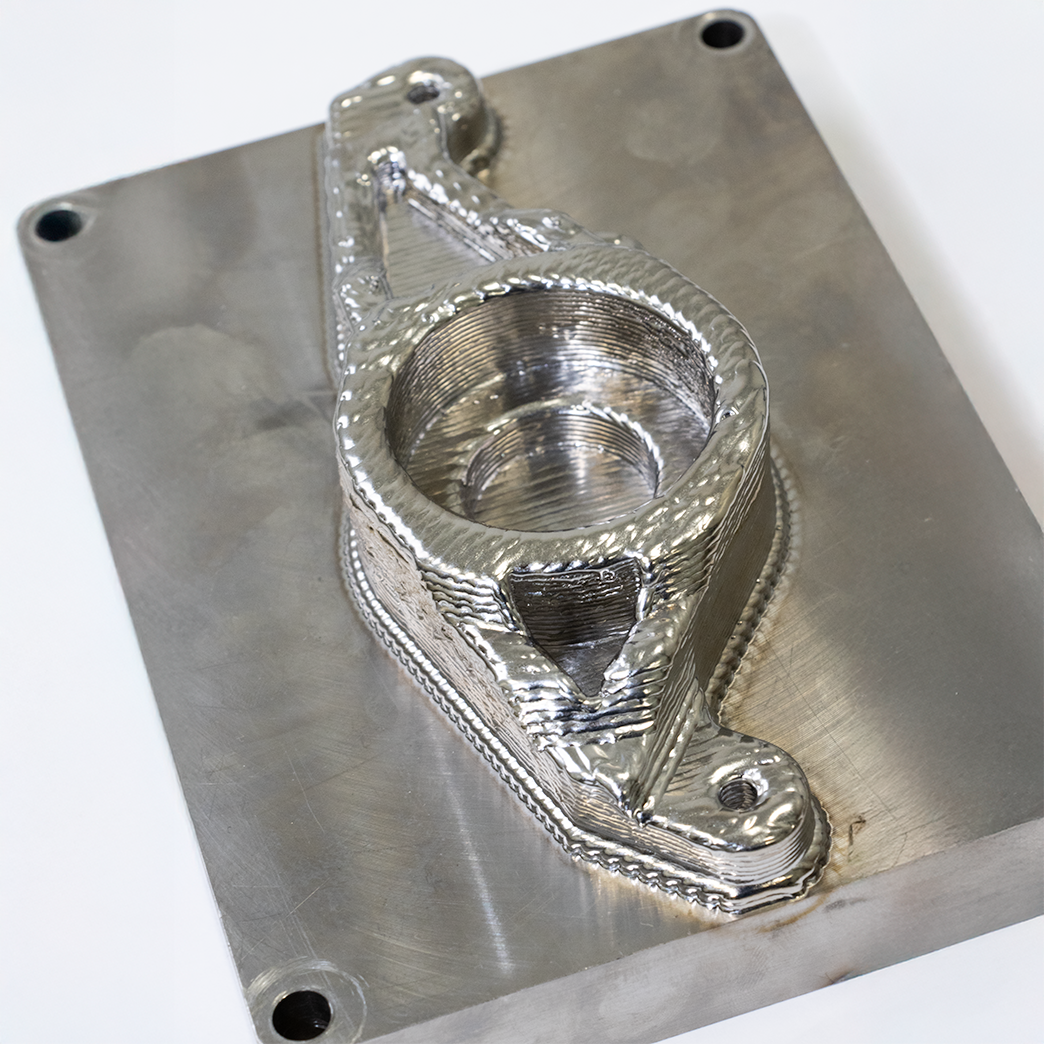
Titanium is notoriously expensive—not just in raw material costs but also in machining due to the high wear rate of cutting tools. What if there were a way to reduce both material waste and machining time?
Impac Systems Engineering found an outstanding solution with the Meltio M600. Precision and repeatability are crucial for aerospace components, and the Meltio M600 delivered near-net-shape parts with 99.8% density, meeting industry standards.
By comparison, machining the same part from a billet would take approximately 4 hours of machining alone—without factoring in material waste. The M600’s hybrid approach saves material, extends tool life, and optimizes production time—proving that in manufacturing, time is money.
4.5 hours
Print time
2.5 hours
Machining time
7 hours
Total time
COMPLIANT MECHANISM
Architectural innovation is reaching new heights with 3D-printed titanium! Thanks to Meltio’s wire-laser metal additive manufacturing, designers and engineers are reimagining how structures are built.
One of the most exciting applications comes from Studio Angius at the AA School of Architecture (AADRL). Their project, Alchemist, explores adaptive and mobile architecture, integrating topology-optimized titanium components to push the boundaries of design, efficiency, and sustainability.

Using Meltio’s wire-laser metal deposition technology, these 3D-printed titanium elements showcase:
Structural efficiency
Precision printed materials with minimal material waste.
Material optimization
Near-net shape manufacturing for sustainable fabrication.
Controlled flexibility
Angular adaptability up to ±12° without compromising structure.
Seamless adaptation
Design to respond dynamically to environmental forces.
Innovative motion
Components enginereed to move with 227N of applied force.
Conclusion
The development of new alloys tailored for additive manufacturing (AM) is becoming increasingly crucial. Furthermore, since AM is a near-net-shaping technology, it is also possible to create innovative structures using this process. Traditional manufacturing methods like molding, casting, forging, and machining typically generate significant material waste, involve lengthy production times, and incur high costs.