Wire-Laser
Metal Deposition
Metal Additive Manufacturing
Wire-Laser Metal Deposition is a Directed Energy Deposition (DED) process that functions by precisely stacking weld beads on top of one another in wire form when introduced into the laser generated melt pool.
Wire-Laser Metal 3D Printing
Meltio’s a disruptive Directed Energy Deposition technology apart from traditional metal manufacturing methods and competing additive systems.
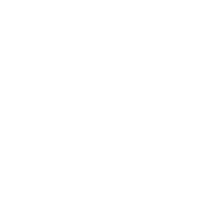
Safe & Reliable
The bulk of the 3D printing process is built around wire, the safest, cleanest, and easiest to work with metal feedstock.
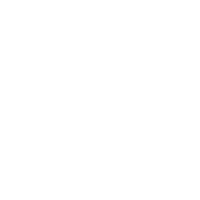
Integration Ready
Turn an existing CNC or robotic platform into a hybrid manufacturing system with no inherent size constraints.
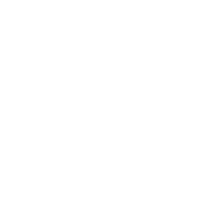
Multi-Material System
Print dual wire for hard-facing or anti-corrosion applications, or wire and dual-wire to create new alloys on the fly.
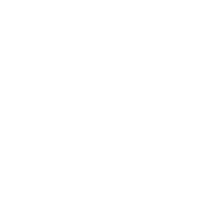
Accessible
The only metal 3D printing process able to deliver fully dense and affordable metal parts within a few hours.
Multi-laser Blue Deposition Head
Enhance performance and reliability
Augmented energy delivery efficiency reduces energy consumption, making it a cost-saving process, thanks to the blue laser diodes.

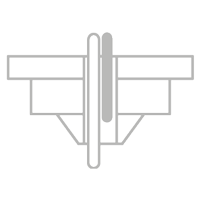
Blue Light
450 nm light improves energy absorption and printing efficiency across the metal material spectrum.
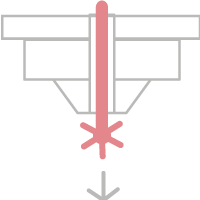
Hotwire Compatible
The deposition head is developed to used with an optional hotwire supply to increase the deposition rate and allow for more materials to be processed.
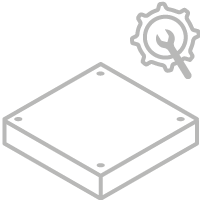
No Calibration
It arrives aligned from the factory for maximum printing repeatability and minimal maintenance.

High Efficiency
The energy consumption per component is reduced significantly, resulting in a greener and more cost-efficient process.
Multi-laser IR Deposition Head
Make accesible repair works
It comes packaged in a compact deposition head, a host of multiple lasers, and capable of processing single, dual and quad wire simultaneously.

Integrated Wire Feed/s
Critical for high process reliability and unique to Meltio. Short distance from feeder to process is necessary for maximum wire feeding precision.
Shield Gas Ring
The head prevent oxidation through a large nozzle ring with very good gas distribution just a few millimeters from the melt pool.
Easy to Service
All wear parts like the wire nozzle and protective optic assembly are very easy and low-cost to replace.
Coaxial Wire Feed
Can print geometries in any direction. Wire comes through the center of the melt pool thanks to the distributed laser system.
Distributed Laser System
A total of 1,2 kW of laser power distributed across six 200 W lasers. It provides an extremely long service life, low optical densities.
Integrated Process Control
Sensors monitor the laser fibers and the deposition process. The system will regulate automatically if an irregularity is detected, or put itself on hold in critical conditions.
Unlimited Third-party Material Choice
Stainless Steels:
Excellent strength and corrosion resistance.
Mild Steels:
Cheap and ductile, with unparalleled machinability and weldability.
Carbon Steels:
High impact strength, retain hardness at high temperatures.
Titanium Alloys:
Highest strength to weight ratio and corrosion resistance.
Nickel Alloys:
High versatility, outstanding heat and corrosion resistance.
Copper & Aluminum:
Under Development. Let me know when they are available.