Due to recent advancements in processes and systems, Additive Manufacturing (AM) has garnered significant attention in Industry and Research. The complexity and resolution achieved are the primary factors that determine the choice of an AM process.
In AM, new technologies have emerged, each offering unique capabilities and applications. Today, we’re focusing on one prominent method: Wire Arc Additive Manufacturing (WAAM).
In this blog, we’ll delve into this technique and the issues and common challenges associated with WAAM, uncovering the complexities and exploring potential solutions and innovations in metal AM.
1. Introduction to WAAM, Powder Bed Fusion and Meltio’s Wire-Laser Metal Deposition process (W-LMD)
Among the different metal additive manufacturing (AM) techniques, these can be broadly categorized into two main families: Powder-based and Wire-based. In the powder-based category, key methods include Powder Bed Fusion (PBF) and Laser-Powder Directed Energy Deposition (DED). In the wire-based category, notable techniques are Wire Arc Additive Manufacturing (WAAM) and Meltio’s Wire-Laser Metal Deposition (W-LMD) are the most employed in industrial settings.
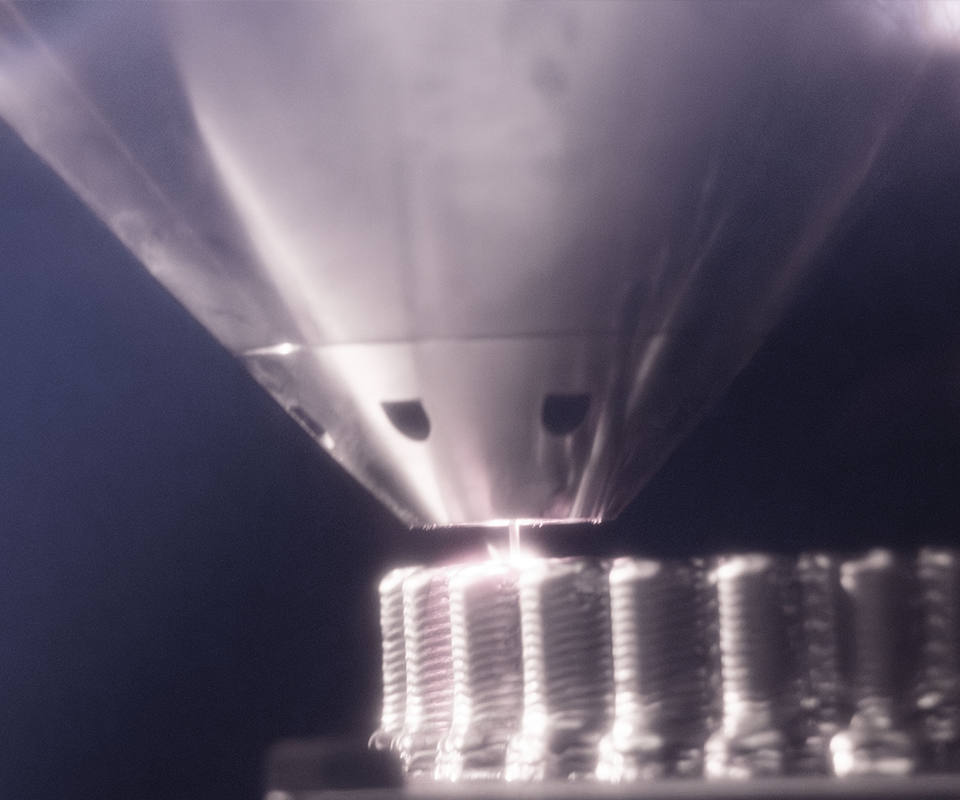
The Powder Bed Fusion (PBF) process utilizes either a laser or electron beam as a heat source to selectively irradiate and fuse metal powder particles, melting them point by point to form the final part.
In contrast, Wire Arc Additive Manufacturing (WAAM) operates similarly to the welding process by using a metal wire as the feedstock and an electric arc as the energy source. In this method, the electric arc melts the wire, which is deposited layer by layer onto a surface, such as a build plate or an existing part. The process is shielded by an inert gas, which prevents oxidation and helps control the properties of the metal, much like in welding.
Through this layer-by-layer method, a complete 3D object is gradually constructed, or existing parts are repaired. Post-processing steps such as CNC machining or surface polishing can be applied to enhance precision and finish quality. Additionally, heat treatment is often used to relieve any residual stresses in the printed components.
Printing process with Meltio and WAAM technology
A standout in the realm of Directed Energy Deposition (DED) is Meltio’s W-LMD process. This cutting-edge technique harnesses multiple laser beams to melt and deposit metal wire onto a build platform with remarkable precision. The W-LMD process is distinct for its ability to focus heat into an extremely narrow zone, which minimizes the heat-affected area and enhances the metallurgical properties of the final product. The result? Parts that boast superior strength, uniformity, and overall quality.
Laser-based AM processes, including PBF and W-LMD, are particularly renowned for their excellent surface finishes and precise geometries.
However, despite the advances, WAAM and LP-DED face their own set of challenges. Today, we’ll focus on WAAM, examining the hurdles it faces and how Meltio can address them.
2. Wire Arc Additive Manufacturing (WAAM): Limitations and solutions
In simple terms, Wire Arc Additive Manufacturing (WAAM) is a 3D printing process that uses metal wire as the raw material. This wire is fed into a machine where it is melted by an electric arc—similar to traditional welding.
Now that we’ve covered a brief description of WAAM, it’s time to delve into its specific challenges and discover how Meltio can solve these issues effectively. Most of the possible defects in the WAAM process are related in some way to parameters such as power, deposition speed, wire feed speed, the correct choice of material and porosity defects in WAAM (such as small holes, voids, or pores throughout the structure).
We’ll explore how Meltio’s advanced technology can overcome the limitations of WAAM, offering more precise and efficient solutions for complex manufacturing needs:
1. Higher material deposition and poorer tolerances:
In general, the WAAM process allows the manufacture of large structural components with moderate complexity, but presents challenges when it comes to creating more complex and detailed geometries. Although WAAM offers a high material deposition rate, the surface finish is less refined, making it difficult to print certain delicate internal structures. In addition, post-processing in WAAM is more laborious, as there is a greater amount of material to be removed. As a consequence, more material is wasted due to poorer tolerances.
On the other hand, Meltio’s technology allows more complex and finer geometries to be produced much more easily than WAAM, although the manufacturing process is slower. Thanks to Meltio’s ability to produce higher quality near-net-shape parts, subsequent machining is less, as the resulting part is much closer to the final design, reducing the amount of wasted material and improving accuracy.
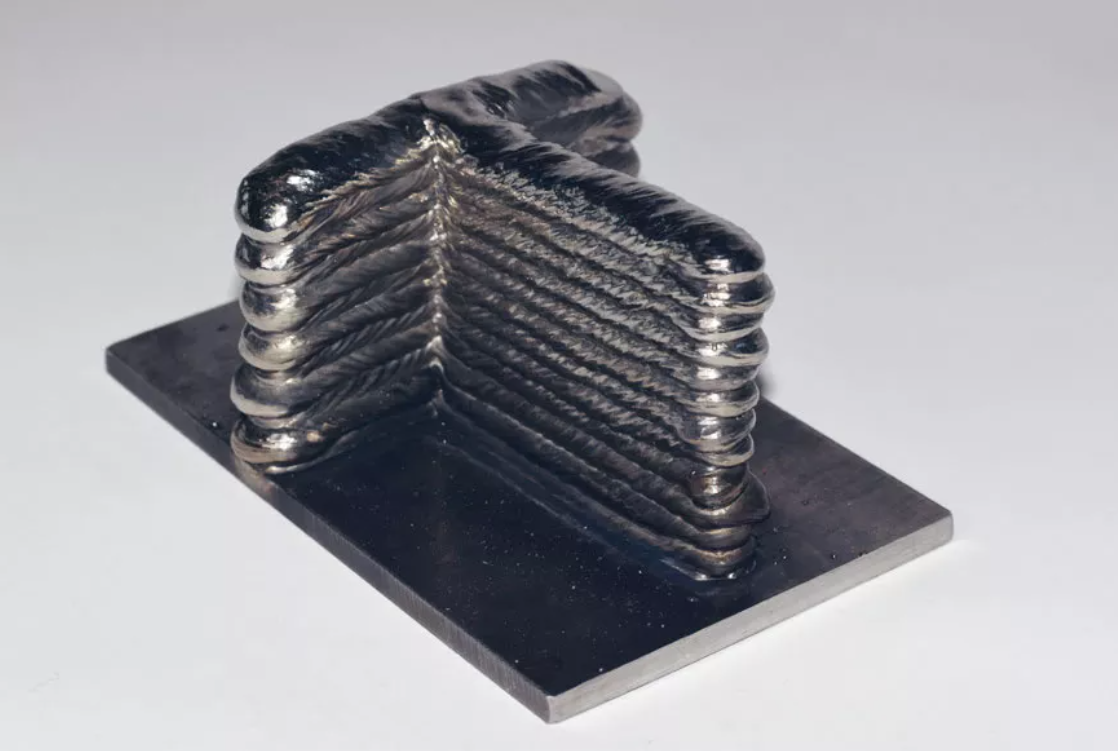
Manufactured with WAAM
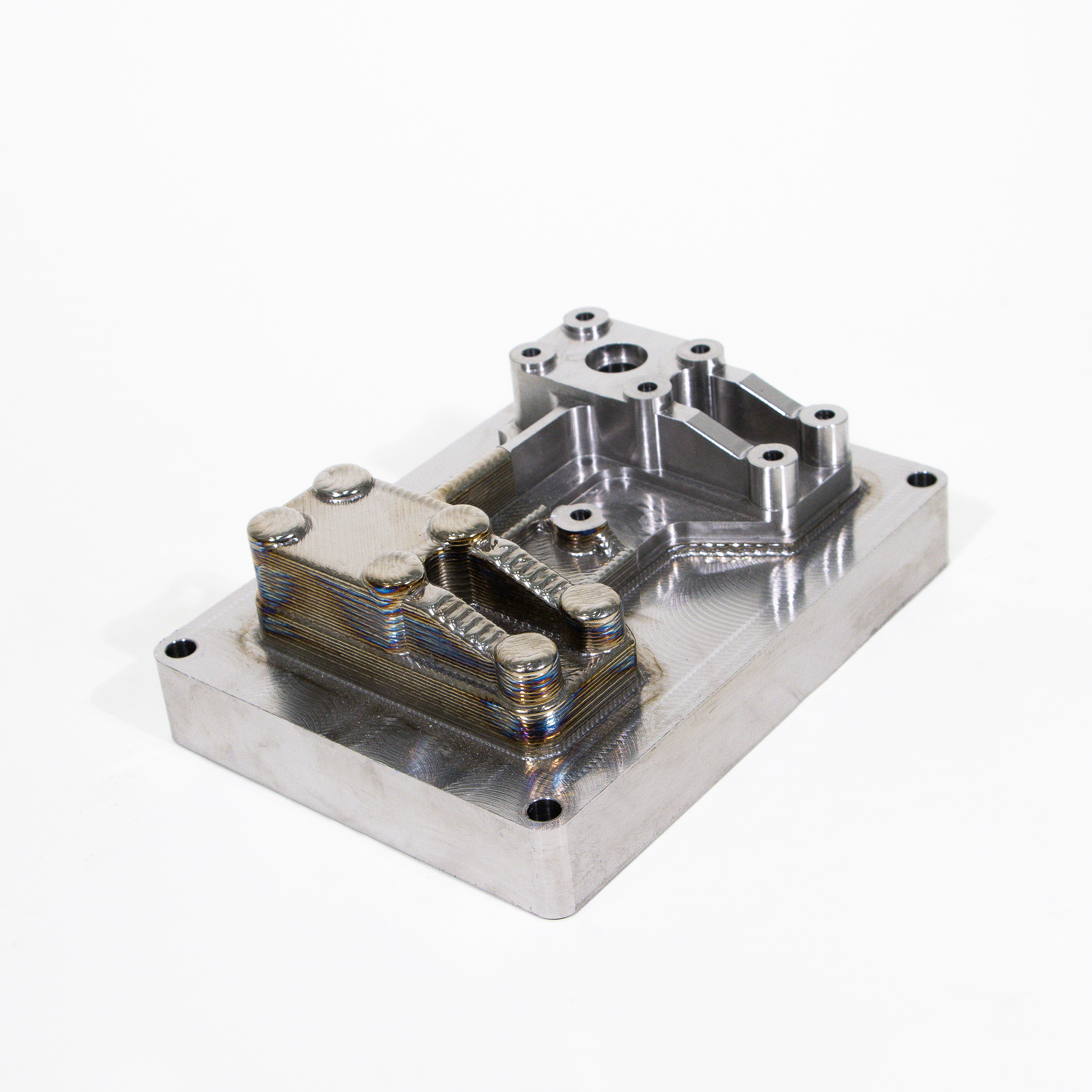
Manufactured with Meltio
2. Unfavourable correlation between mechanical properties and heat input
Wire-Arc Additive Manufacturing often suffers from prolonged heat exposure, as a consequence of higher energy inputs. This high energy input can cause larger grain structures and negatively affect both material properties and the accuracy of the final component. The deposition rate is not as realistic because it is usually necessary to add more cooling time between layers to avoid these problem. In contrast, Meltio presents a compelling advantage over WAAM due to its lower energy input, which offers a key advantage as it results in a finer and more uniform microstructure thanks to the lower overall temperature of the part during the manufacturing process.
Another drawback of the high energy input in WAAM is the increased dilution in multi-material components, this effect can be critical in repair applications.
TIP: An example of the excellent dilution that Meltio technology can achieve can be found in these Inconel 625 and H11 datasheets!
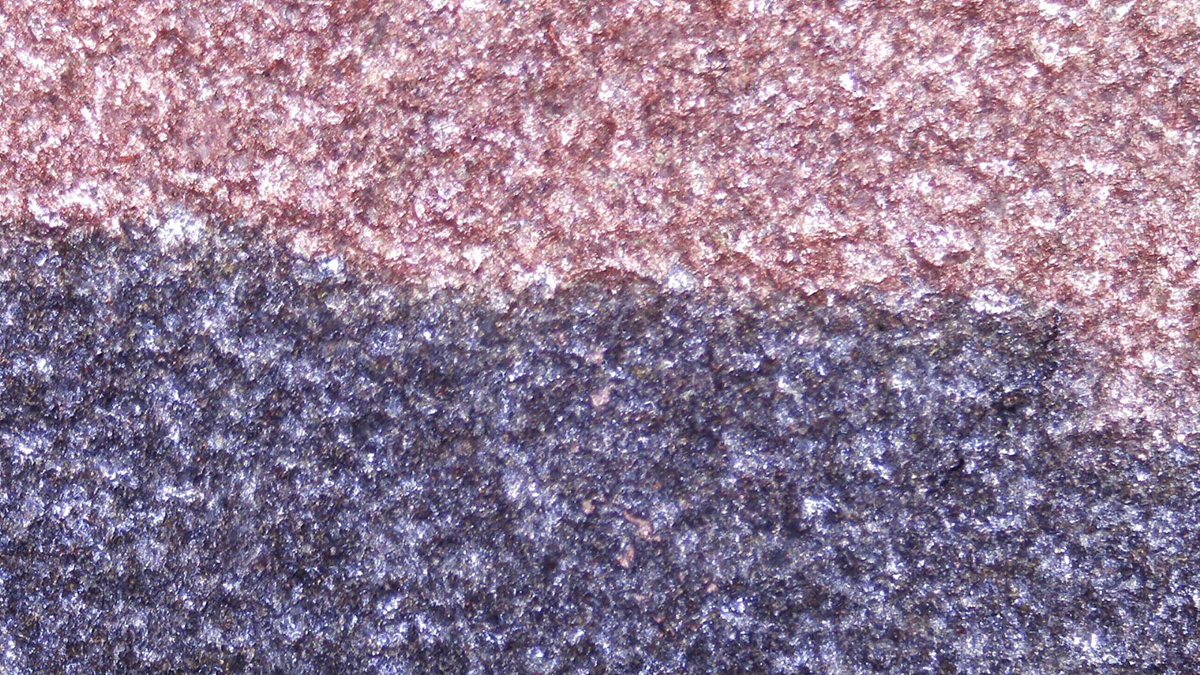
3. Consumable use during print
Wire-Arc Additive Manufacturing often suffers from prolonged heat exposure, as a consequence of higher exposure is the need to replace some parts as the contact tips and nozzles.
For consistent success in WAAM (Wire Arc Additive Manufacturing) print jobs, regular maintenance of consumable parts is essential. Key components like contact tips, nozzles, and diffusers wear out or get dirty over time and should be checked frequently to ensure optimal performance. Contact tips typically require replacement after 10-15 hours of use, while nozzles last around 25-30 hours, depending on the type and the material used. Staying proactive with these replacements helps maintain weld quality, prevents defects, and extends the lifespan of your equipment, ultimately leading to more efficient and reliable results. (See more information here).
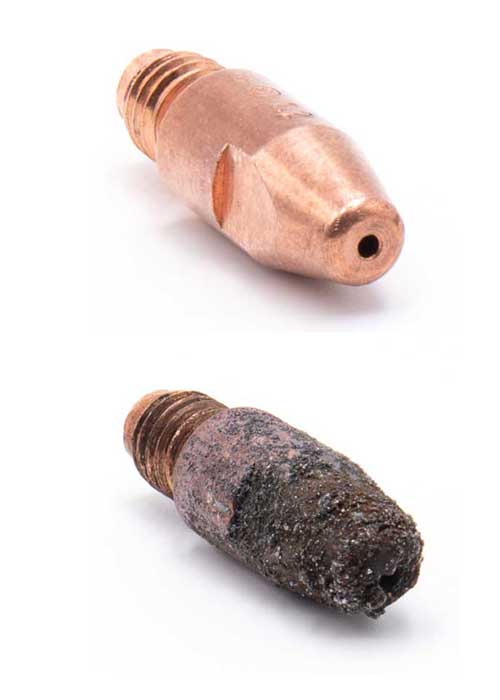
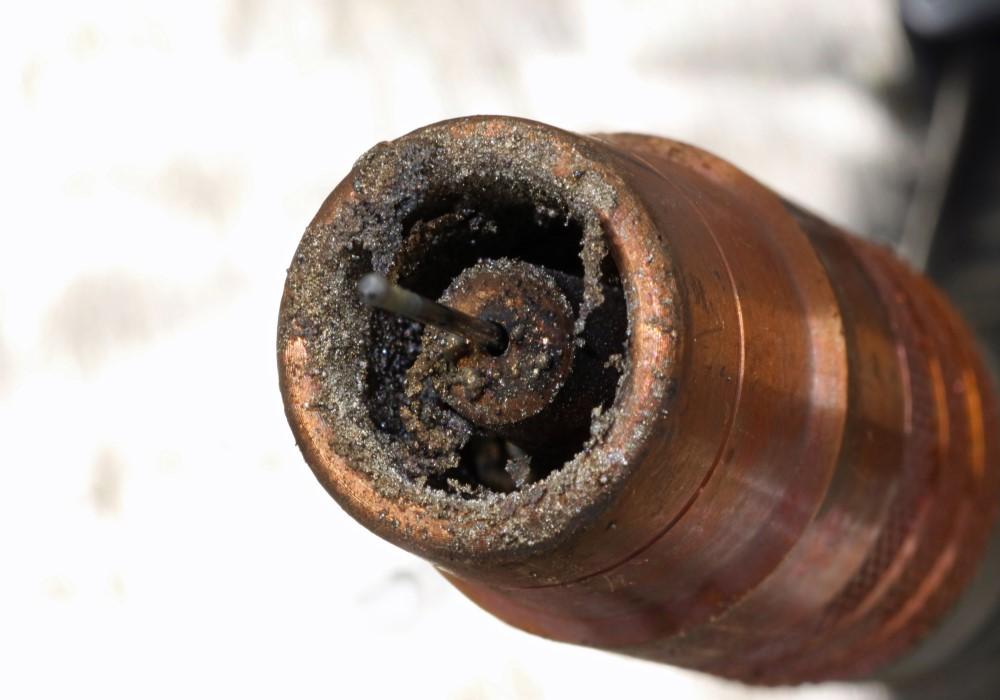
In contrast, with Meltio, the nozzle, a vital component, typically lasts around 336 hours of printing before requiring replacement.
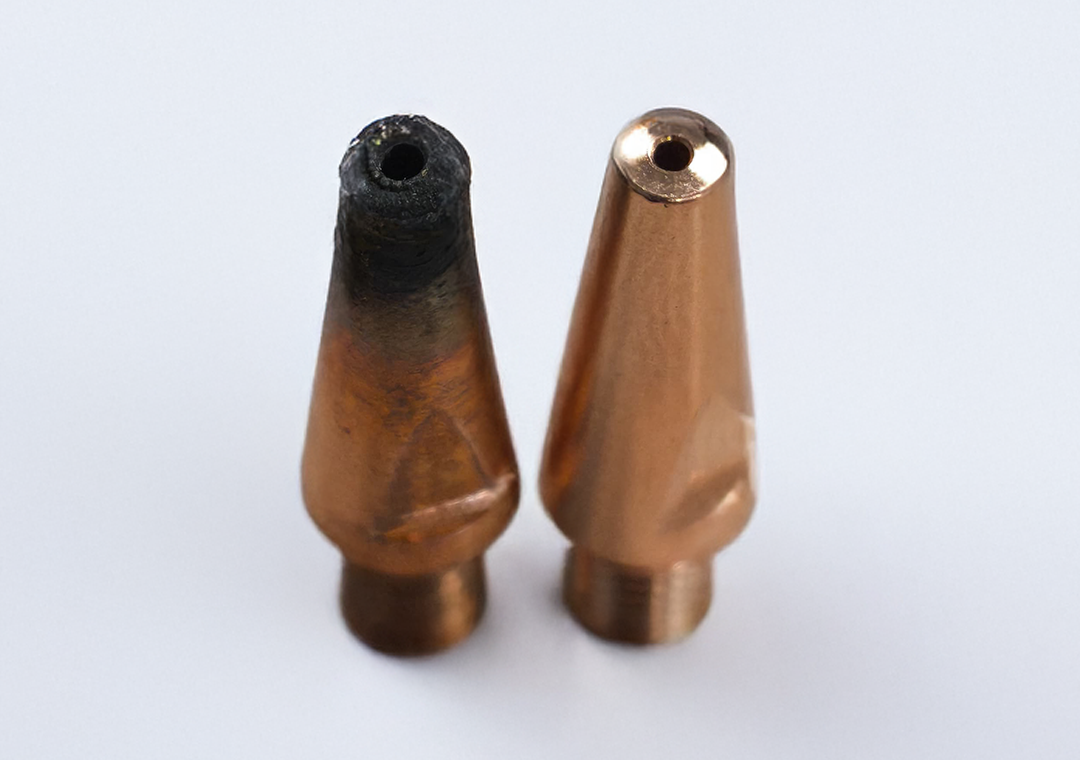
4. The challenge of an open ecosystem. Lack of reliability
Unlike WAAM, where components like the robotic arm, print head, slicer software, and materials are purchased separately, Meltio offers a fully integrated solution. This includes the Robot Cell, software, continuously developed materials, and the robotic arm within a single package.
Because we have this closed ecosystem of equipment, software, and machines, one advantage of working specifically Meltio, we offer significant advantages by eliminating common problems, by pre-testing it for you. This streamlined system ensures, avoiding defects such as porosity and poor material deposition. However, other technologies, which may not have an ecosystem such as Meltio, may be more prone to problems or setbacks in the early stages of development.
A customer can quickly integrate Meltio’s technology into their manufacturing process, thanks to its user-friendly design. In fact, some of our clients have begun testing new materials in less than a week, demonstrating the system’s ease of use and adaptability.
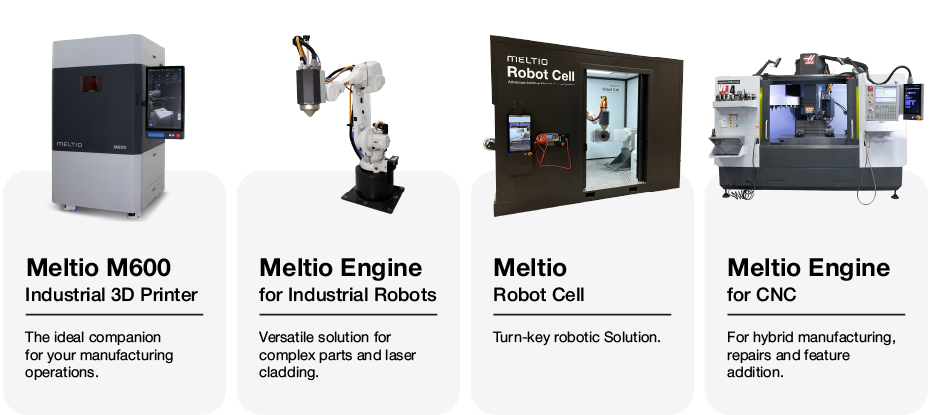
When it comes to wire selection, Meltio eliminates the guesswork by rigorously testing and validating the wires we offer, exclusively tailored to Meltio technology, ensuring optimal quality and reliability with our system.
Currently, we are focused on identifying key factors that enhance hardness and overall performance. Our ultimate goal is to provide a superior user experience that consistently meets and exceeds expectations.
Conclusion
In conclusion, while WAAM is a well-established and valuable industrial technology, key differences with laser-based methods can influence its effectiveness in the industrialization of these technologies.
Wire Arc Additive Manufacturing presents challenges related to efficiency, cost, and product quality, but Meltio’s advanced solutions provide a clear path to overcoming these obstacles. By addressing common defects, optimizing workflows, and reducing material waste and repair costs, Meltio enhances both productivity and reliability. As discussed throughout this blog, integrating Meltio’s technology not only strengthens the structural integrity of the final product but also streamlines manufacturing processes, ensuring timely delivery and greater overall efficiency.