Fuji-Koshuha, headquartered in Osaka, introduced the Meltio Engine Robot in 2023. Since its founding in 1958, the company has specialized in high-frequency hardening and laser cladding technologies. The reason they introduced the Meltio Engine Robot Integration, which can repair and cladding existing parts, and handle large-scale modeling of over 1m in size, was that there was a market potential that could be realized by combining the technology that Fuji-Koshuha has cultivated up to now with the low running costs of Meltio’s 3D printers.
3DPC, one of Meltio’s trusted sales partner, spoke with Goto Mitsuhiro, President and CEO of Fuji-Koshuha, about the process that led to the introduction of Meltio Engine Robot Integration, the reasons for its adoption, and even the unexpected changes that its introduction has brought about.
TABLE OF CONTENTS
- Background to the introduction of Meltio Engine Robot Integration
- Reasons for deciding to purchase the Meltio Engine Robot Integration
- “Good quality is a given”: The benefits are cost and delivery time
- Side-effects felt after introducing Meltio Engine Robot
- “We have our sights set on the global market, not just the Japanese market.”
Background to the introduction of Meltio Engine Robot Integration
Fuji-Koshuha originally specialized in a technology called high-frequency hardening, but about 15 years ago they started working on a technology called laser hardening. After that, they started incorporating laser cladding and precision laser cladding, and they also started working on 3D printers.
Laser hardening uses a laser, while laser cladding is a technology that uses powder to coat the surface. It can be used to create shapes, but there was an issue with using a laser to create a powder coating, as the powder would have a low yield. By chance, they came across something that seemed to solve that issue at an exhibition and decided to buy it.
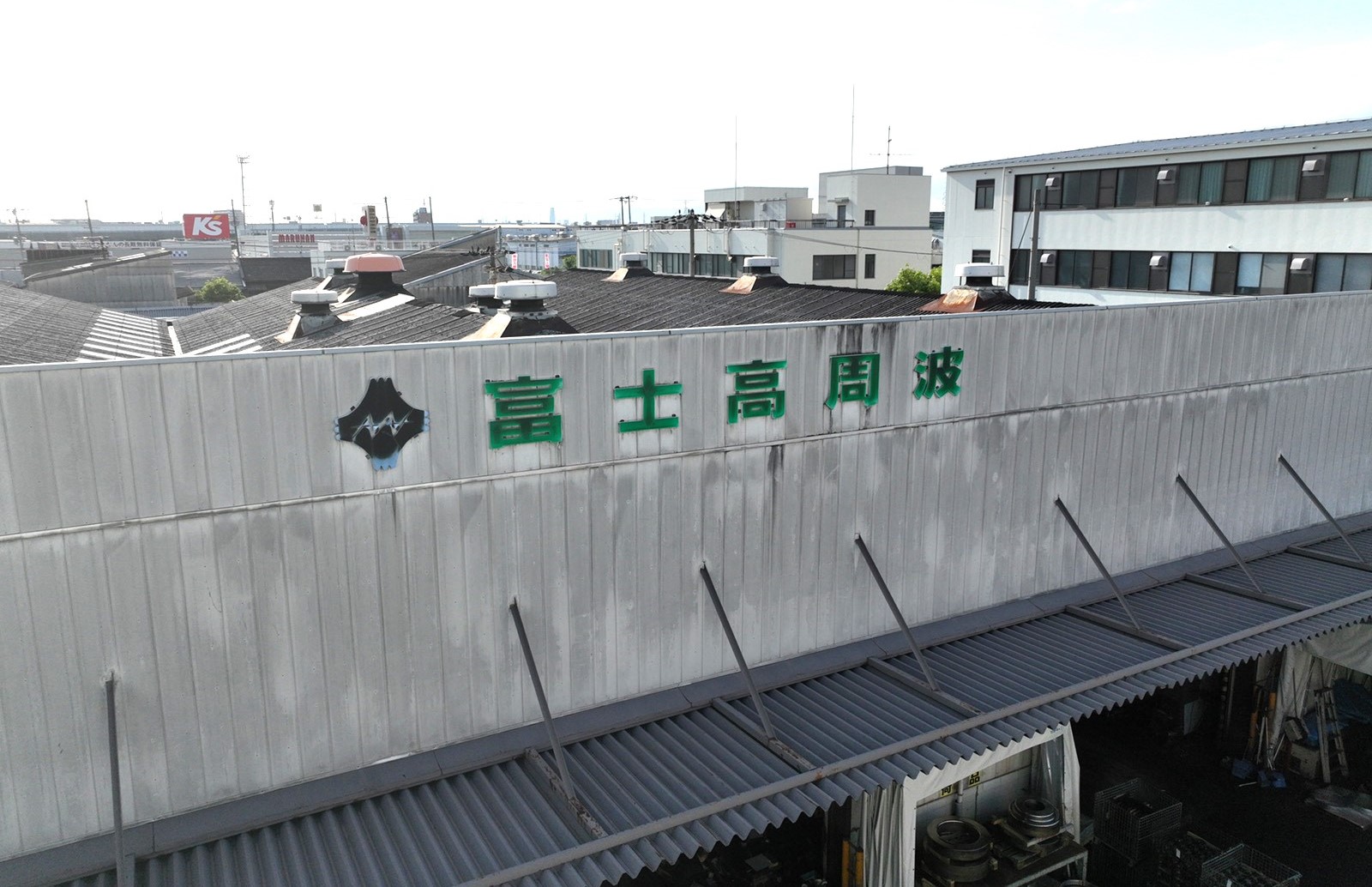
Reasons for deciding to purchase the Meltio Engine Robot Integration
Printing more than palm-sized objects
Fuji-Koshuha’s always felt that the challenge in the 3D printing industry is that it can only make palm-sized objects. As typified by powder bed fusion, most are palm-sized. Whereas palm-sized objects were the norm in the metal 3D printing industry, Meltio can print objects of 1.5m or 2m in size. It can be done with a powder bed, but the price is doubled.
However, the Meltio system is cheap and can handle large-scale 3D printing, and since it uses wire instead of powder, it can eliminate yield problems. They were attracted to the fact that there is no waste of material.
Not only metal 3D printing
Fuji-Koshuha aims to create a market for large-scale metal 3D printing, which doesn’t exist yet. They also started laser cladding, which no one in Japan was doing at the time. If they can create a market and become a pioneer, profits will come naturally.
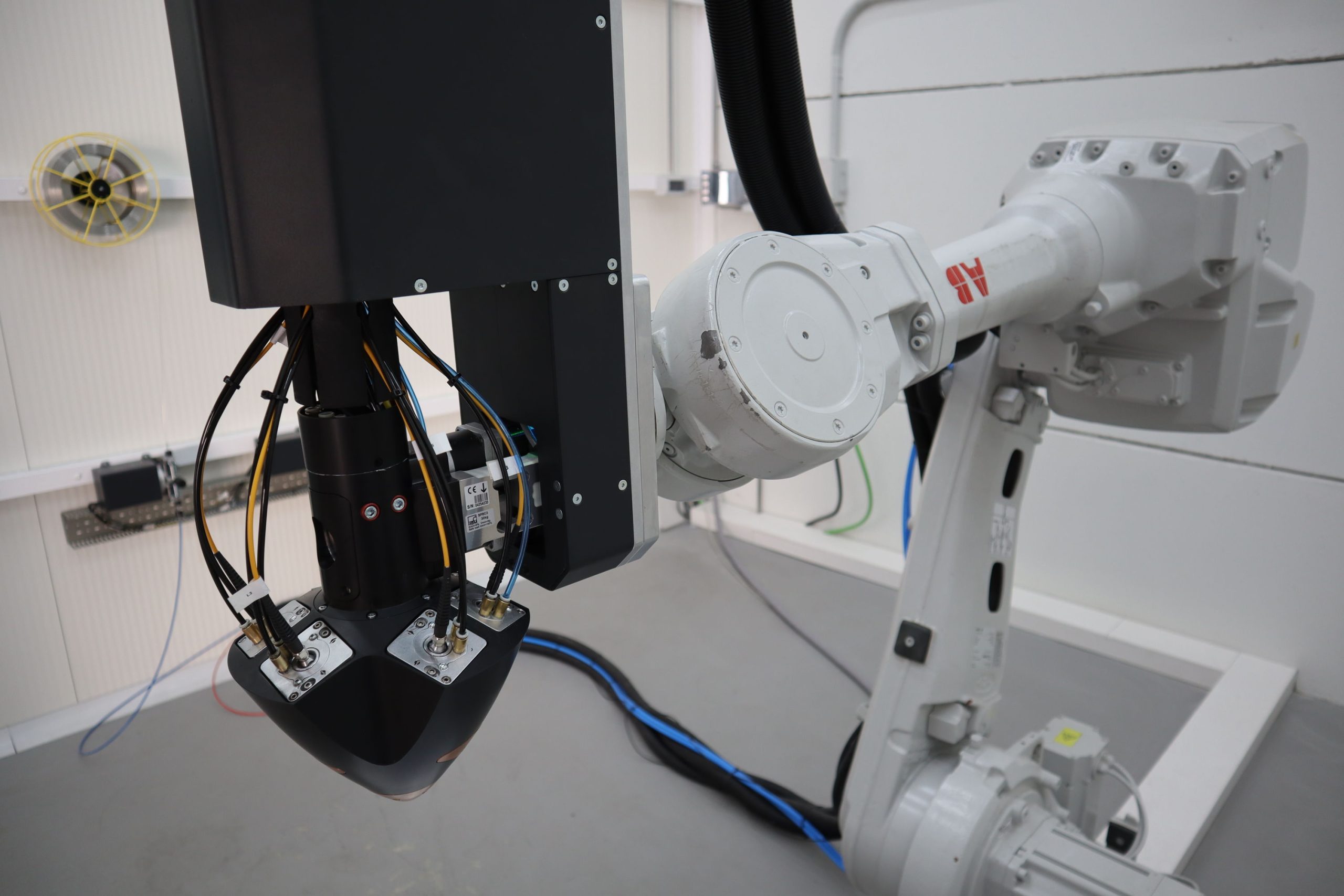
Faster printing time
In the case of metal, finishing processing is still required whether you use a powder bed or Meltio, but Meltio’s DED is still faster. If finishing processing is required anyway, it would be better to have a faster printing time.
Multi-beam modeling
The reason they decided on Meltio was because it uses multi-beam modeling. Other companies use single-directional lasers. Fuji-Koshuha’s laser cladding uses multi-lasers, so they were fully aware of the pros and cons of multi-lasers. They think multi-lasers are overwhelmingly more suitable for modeling.
Easy-to-use
The hurdle of working with metal remains high. After all, it is humans who operate the robot. Therefore, it may be difficult for a complete beginner to work on metal modeling, but for people who have a good understanding of metal, Meltio modeling will be a very easy-to-use technology.
Best-material consumption
When comparing DED powder and DED wire, the yield is completely different. Wire can consume 100% of the material, but powder can only consume about 60%, with 40% being discarded.
TIP: Check the advantages of using wire over powder.
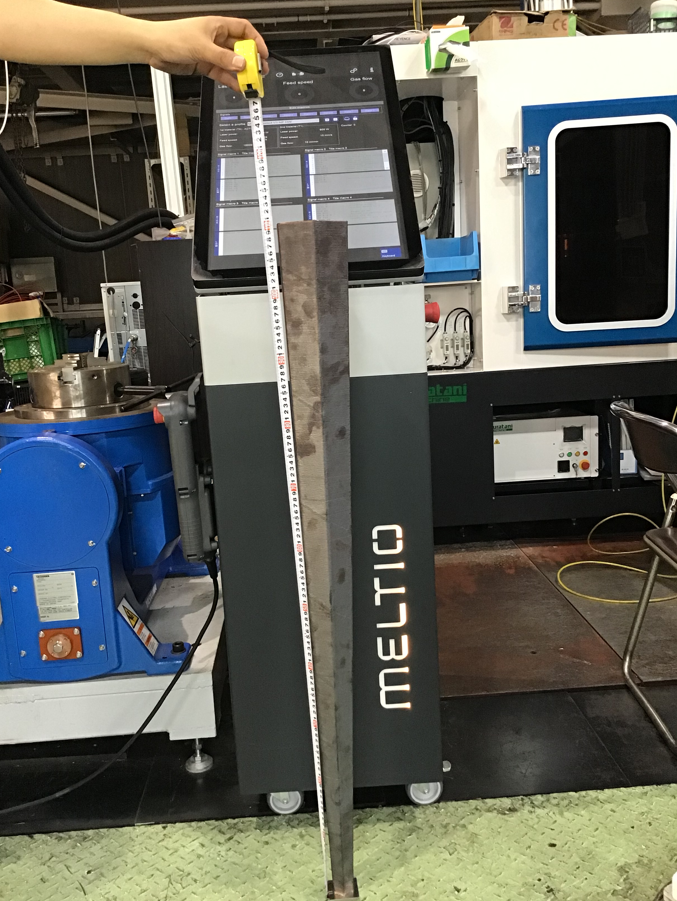
“Good quality is a given”: The benefits are cost and delivery time
There are two benefits that make customers happy: cost and delivery time. “Good quality” doesn’t work in the Japanese market, where “good quality is a given.” In the Japanese manufacturing industry, which boasts “the best quality in the world,” what’s important is cost and delivery time.
To make one large part up to 2m, it usually takes at least three months, including material procurement and cutting. However, Meltio can make it in three or four days to a week.
However, unfortunately, customers prioritize cost over delivery time. So even if you appeal to “short delivery time” without eliminating costs, it won’t resonate with customers. That’s where technology like topology optimization comes in. Meltio comes with a solid grasp of technologies like topology optimization, CAE analysis, and strength analysis.
By making full use of Meltio’s technology, Fuji-Koshuha can appeal to customers by saying:
“Parts that previously cost 1 million yen can now be made for 900,000 yen, with the option of a one-week delivery, when previously took 3 months.”
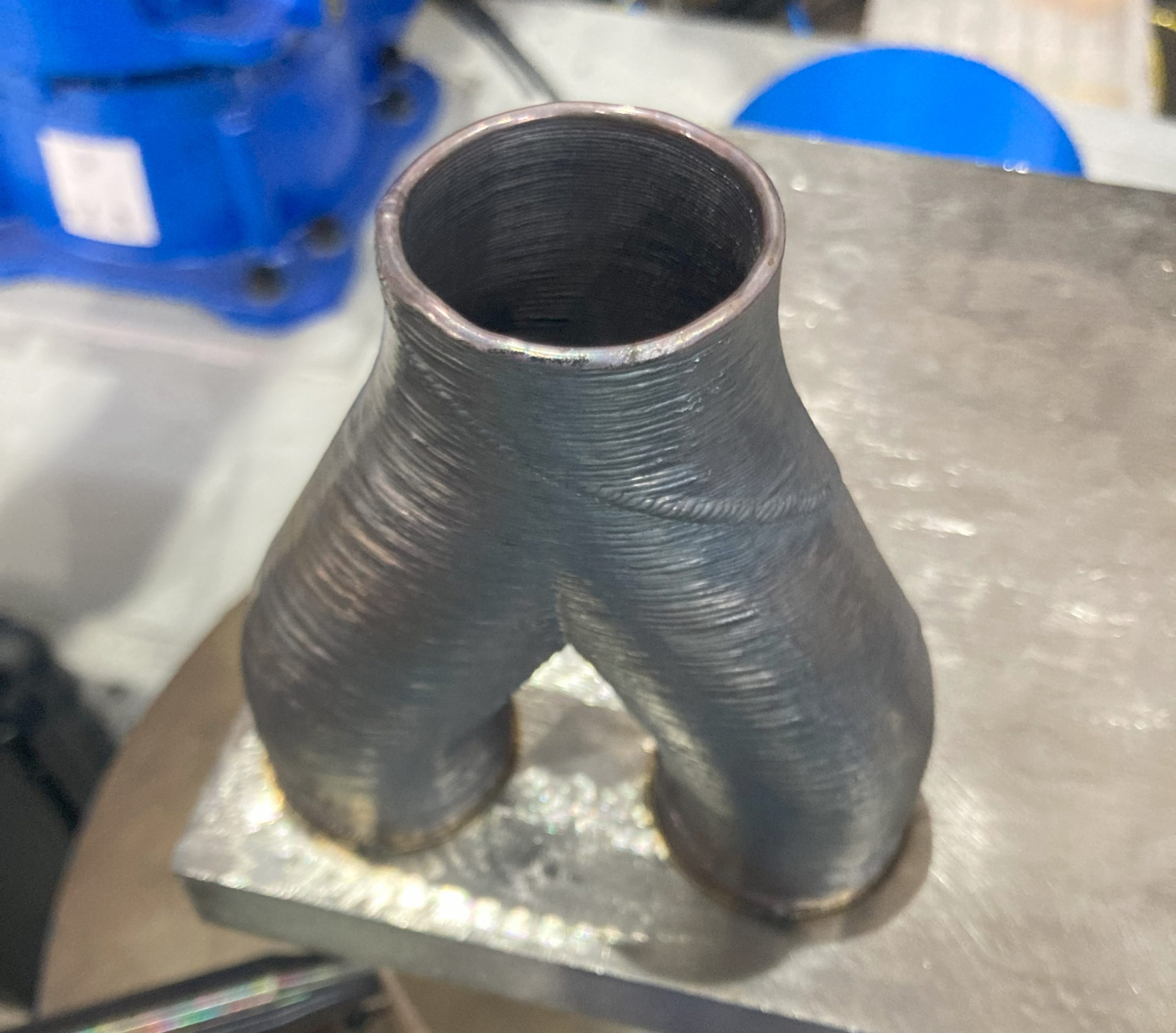
Side-effects felt after introducing Meltio Engine Robot
More popularity, more skilled personnel
Since they introduced Meltio, they’ve become more popular. Thanks to the image of “cutting-edge technology”, people who would not have come there before are now coming to interview.
They have already hired one person for Meltio, and another is scheduled to join them in June. Until now, most of their employees were high school graduates, but they are now accepting applications from university graduates.
Meltio members have high academic ability, with one from Osaka Sangyo University and another from Kyoto University, and the next one to come is Nagoya University.
Increase in inquiries
It’s only been a couple of months since they put it on their website, so they haven’t seen a sudden increase in inquiries yet, but they’ve seen an increase in the number of people coming to visit their company.
“ It’s not interesting to try to do something that already has an answer. It’s interesting because there is no answer.”
Fuji-Koshuha doesn’t have a specific part in mind, but it could become a variety of industrial equipment and parts like a large metal molded product about 1.5m in size.
President Goto thinks of making chairs and dining table sets. The concept is not “something made with 3D modeling,” but “a dining set that can be used for 100 years.” Most of the time, the reason a table breaks is the joints, but 3D printing has no joints. That’s why it’s less likely to break. President Goto would be the happiest if he could sell a “100-year-old dining set that can be used by my grandchildren” for about 1 million yen.
“We have our sights set on the global market, not just the Japanese market.”
Fuji-Koshuha wants to create a 3D printing industry that can make large objects. Regarding CAE analysis and topology optimization, they are currently working with a startup company from Nagoya University in which they have invested.
In the future, they will work with Nagoya University and others to acquire design technology and create a company that specializes in wire DED and powder DED topology optimization and CAE analysis. The company was just launched in late February of this year.
President Goto deeps down into the future of Fuji-Koshuha: ” I think the ideal business model would be for us to receive requests from companies for product topology optimization and CAE analysis, design it, and sell the drawings along with the CAM path data. I would like to provide all of this to customers who buy Meltio. I think there are still inconsistencies between companies, such as “We can do powder bed but not DED” or “We can do wire DED but not powder DED,” so there are no companies in Japan, at least, that can comprehensively handle everything, so I would like to create that market, and eventually I am considering not only the Japanese market but also the world.”
TIP: Discover how to expand your manufacturing capabilities with the Meltio Engine Robot Integration here.