Steel is one of the most versatile and essential materials in modern industry. This metal has proven to be indispensable due to its combination of strength, ductility and adaptability. However, not all steels are the same; their properties and applications vary significantly depending on their chemical composition and microstructure.
In this blog, we will explore two broad categories of steels: carbon and alloy steels, each with sub-classifications based on their chemical content and constituent elements. These details determine not only their physical characteristics but also their performance in various industrial applications.
We’ll also spotlight Meltio Stainless Steel, a revolutionary material that combines the corrosion resistance of stainless steel with advanced manufacturing techniques. Meltio Stainless Steel stands out as a game-changer in industries that demand both precision and resilience.
1. Introduction to Steel types
Steel comes in many types, classified based on the alloying elements present. When carbon is the primary alloying element, and others are present only in lower concentrations, the steel is categorized as carbon steel.
Other types of steel are named according to specific characteristics, such as:
- The dominant element in their composition (e.g., silicon steels).
- Their suitability for certain treatments (e.g., case-hardening steels).
- Enhanced properties they offer (e.g., stainless steels).
- Their intended application (e.g., structural steels).
These classifications help us understand how variations in composition influence the properties and uses of different steels.
Carbon steel is one of the most widely used types of steel. Its straightforward composition and adaptability make it a cornerstone of numerous industries, offering solutions for everything from structural applications to precision tools.
1.1. The three main types of carbon steel
In this section, we’ll explore the three main subcategories of carbon steel: low-carbon steels, medium-carbon steels, and high-carbon steels.
- Low-carbon steels (< 0.25% C):
These are commonly called mild steels or irons. These steels are soft, ductile and easy to work. Due to their low carbon content, they have a lower hardness, but excellent workability. They are ideal for structural applications such as beams, rolled sections and pipes.
- Medium-carbon steels (0.25%-0.60% C):
This type of steel combines higher strength and hardness with good machinability. For this reason, it is commonly used in the manufacture of parts subject to moderate stresses, such as shafts, gears and springs.
- High-carbon steels (> 0.60% C):
With a higher carbon content, these steels achieve high levels of hardness, although they sacrifice some ductility. They are mainly used in cutting tools, blades and high-strength wires.
1.2. Alloy steels: Designed for performance
Unlike carbon steels, alloy steels contain additional elements in significant proportions, such as chromium, nickel, molybdenum and vanadium. These elements give the steel specific properties, such as corrosion, wear or heat resistance, making them ideal for demanding applications.
According to alloy level:
- Low alloy steels (< 5% alloying elements):
With a slightly enriched composition, these steels achieve a noticeable improvement in strength and hardness, without compromising too much on ductility.
- High alloy steels (> 5% alloying elements):
These steels, like stainless steel, are noted for their high resistance to extreme conditions, including corrosive environments and high temperatures. They contain more than 10.5% chromium, which acts as a barrier against oxidation.
1.3. Classification by main alloying element
Each alloying element imparts distinct properties to the steel, enhancing its performance for specific applications:
- Chromium
- Nickel
- Molybdenum
- Vanadium
- Manganese
2. Meltio Stainless Steel
Meltio’s 316L austenitic stainless steel is actually known in the industry as 316LSi. This steel is a variation of the standard composition with extra silicon in the composition to improve some of its properties. This material has become a benchmark in the additive manufacturing industry, especially when advanced weldability and corrosion resistance characteristics are required.
TIP: Download our printable materials list!
2.1. What makes Stainless Steel so special?
The key to this steel lies in its chemical composition. Like 316L, it has a low carbon content (‘L’ for Low Carbon), but the ‘Si’ represents its higher silicon content (between 0.65% and 1.0%). This combination gives it unique properties:
– Increased corrosion resistance: It is excellent against aggressive chemical environments, such as acids and salt water.
– Improved weldability: Thanks to silicon, cleaner and more uniform weld seams are formed.
– Reduced risk of intergranular corrosion: The low carbon prevents the formation of carbides at the grain edges after welding.
Austenitic stainless steels (so called because they are formed by austenite grains), are the most versatile of the whole family of stainless steels. They have better anti-corrosion properties than ferritic and martensitic steels and a high ductility due to their tightly packed crystalline structure (face-centred cubic). This makes these steels suitable for a variety of applications, even in cryogenic environments.
On the other hand, these steels are not ferromagnetic, so they will not have strong interactions with magnets like ferritic and martensitic steels. Neither can they be hardened by thermal treatment (quenching) because the allotropic change from austenite to martensite that occurs in other types of steels is not possible.
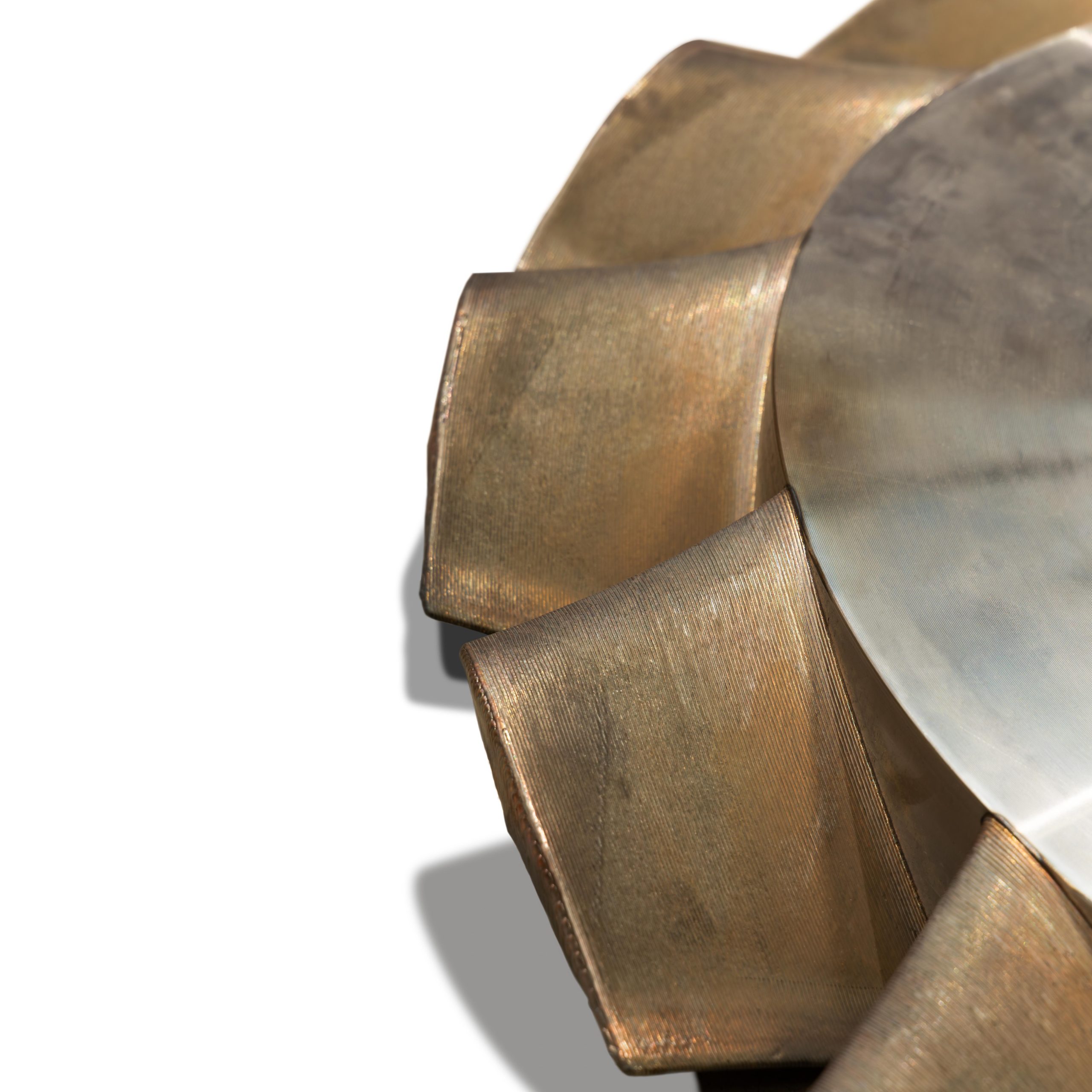
2.2. Application sectors
Thanks to its exceptional corrosion resistance, high tensile strength and versatility, 316LSi stainless steel is widely used in a multitude of applications in a variety of industries:
– Food and pharmaceutical industries: Food and pharmaceutical industries: 316LSi stainless steel’s hygienic properties and ease of cleaning make it ideal for food processing equipment, storage containers and piping systems. Its corrosion resistance ensures product integrity and prevents contamination.
– Chemical industry: The material’s resistance to a wide range of chemicals, including acids, makes it suitable for tanks, reactors and other equipment exposed to aggressive environments.
– Marine and offshore: Its high resistance to saltwater corrosion makes 316LSi indispensable for shipbuilding and offshore, where it is used for components exposed to harsh marine environments.
– Medical devices: 316LSi’s biocompatibility and corrosion resistance make it a perfect material for surgical implants, instruments and other medical devices that come into contact with the human body.
– Architecture and construction: Architecture and construction: The aesthetic appeal, durability and corrosion resistance of this material make it ideal for architectural elements, facades and structural components.
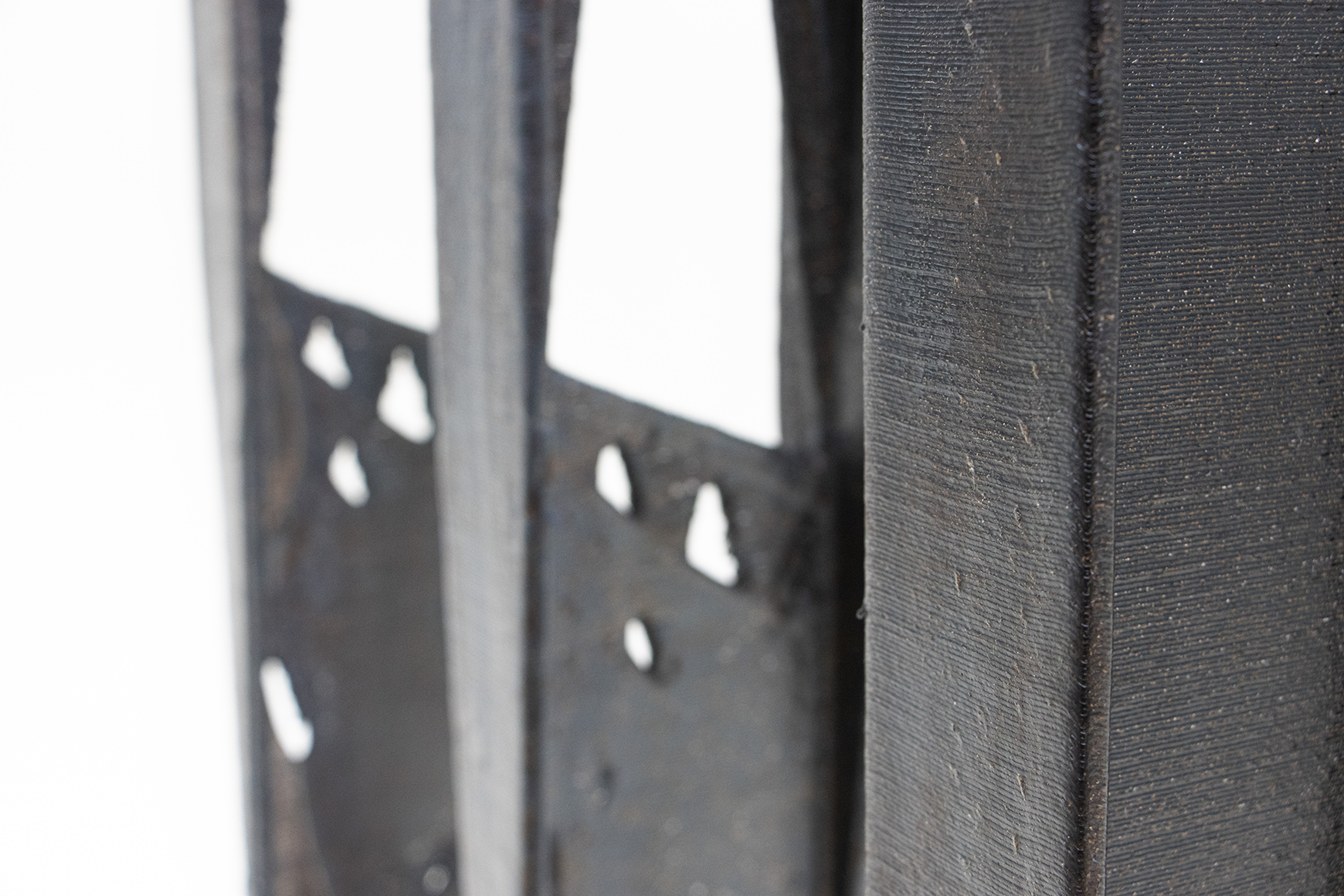
– Automotive and aerospace: 316LSi’s high strength-to-weight ratio and resistance to high temperatures make it suitable for automotive and aerospace applications, where weight reduction and performance are critical.
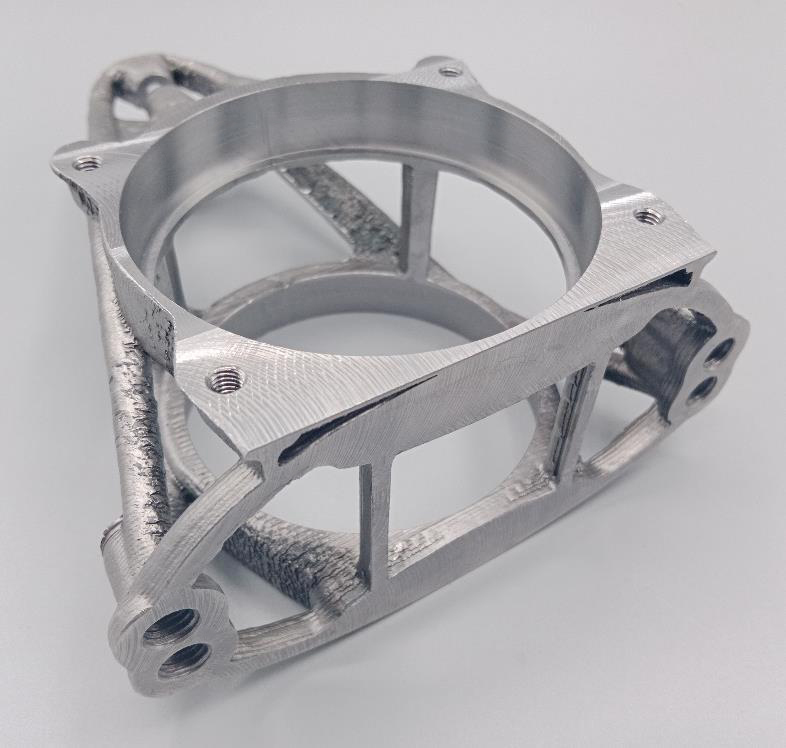
– Energy industry:: The material’s resistance to high temperatures and pressures makes it suitable for components in power generation and oil and gas applications.
– Consumer goods:: 316LSi stainless steel is used in the production of various consumer goods, such as cookware, cutlery and jewellery, due to its aesthetic appeal, durability and ease of maintenance.
TIP: Download the Meltio Applications catalog!
2.3. Stainless Steel 316L in Meltio Systems
Laser and wire additive manufacturing is known to be a manufacturing where there are rapid temperature changes. These uncontrolled cool-downs from melting temperatures after the laser passes determine the type of final microstructure the parts will have. These coolings, added to the fact that there is a clear temperature gradient parallel to the direction of fabrication, result in anisotropic microstructures.
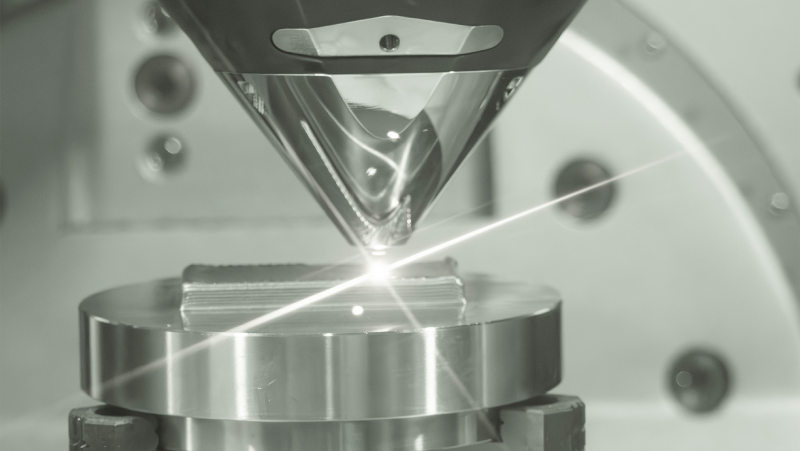
Meltio 316L stainless steel is no exception. According to the experiments carried out on Meltio systems, despite finding better results than can be found in other types of DED technology with other energy sources with higher heat input such as WAAM, a slight preferential growth along the direction of fabrication can be observed.
This means that, when carrying out mechanical tests, there is a slight difference between the tensile strength between the planes parallel and perpendicular to the manufacturing of the parts.
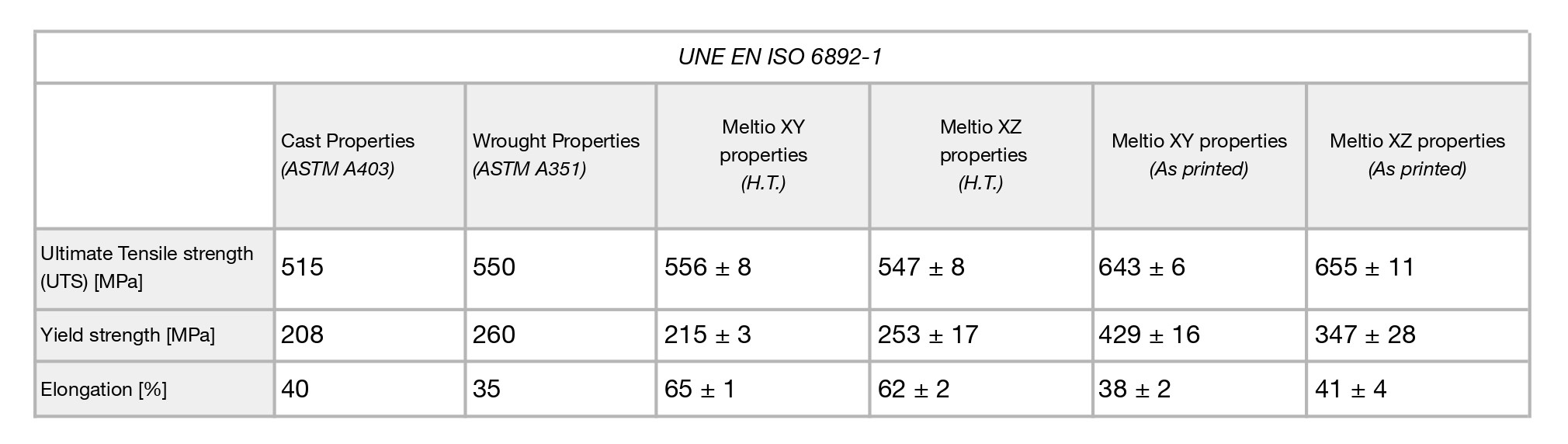
Tensile mechanical properties of Meltio 316L steel
If we stop to analyse the microstructure of the steel in the as-printed state, we can observe that most of the microstructure is austenite grains, this is positive, because this phase is the one that transfers most of the positive properties to the alloy. Due to the rapid cooling process, small grains of delta ferrite (stable phase at high temperatures), which has been trapped between the austenite grains during cooling, are also observed. This can be detrimental because it leaves the alloy slightly weakened by various factors: Corrosion, hot cracking, ductile-brittle transition at low temperatures, among others…
If the project requirements do not allow the presence of delta ferrite, it can be eliminated by austenitisation heat treatment. The material is heated to a temperature where the delta ferrite is eliminated in favour of austenite and then cooled again. This heat treatment not only removes the delta ferrite, but also serves to reduce the anisotropy created during manufacture.
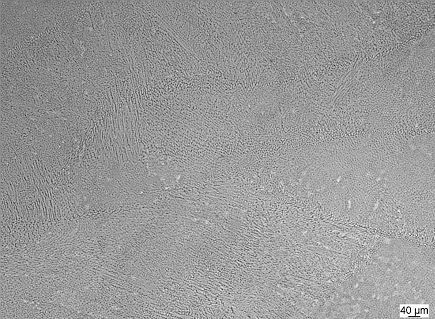
Microstructure of 316L in as-printed state
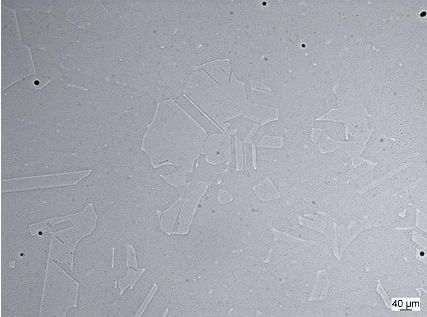
Microstructure of 316L after austenitising heat treatment
3. Meltio Applications made with Meltio 316L
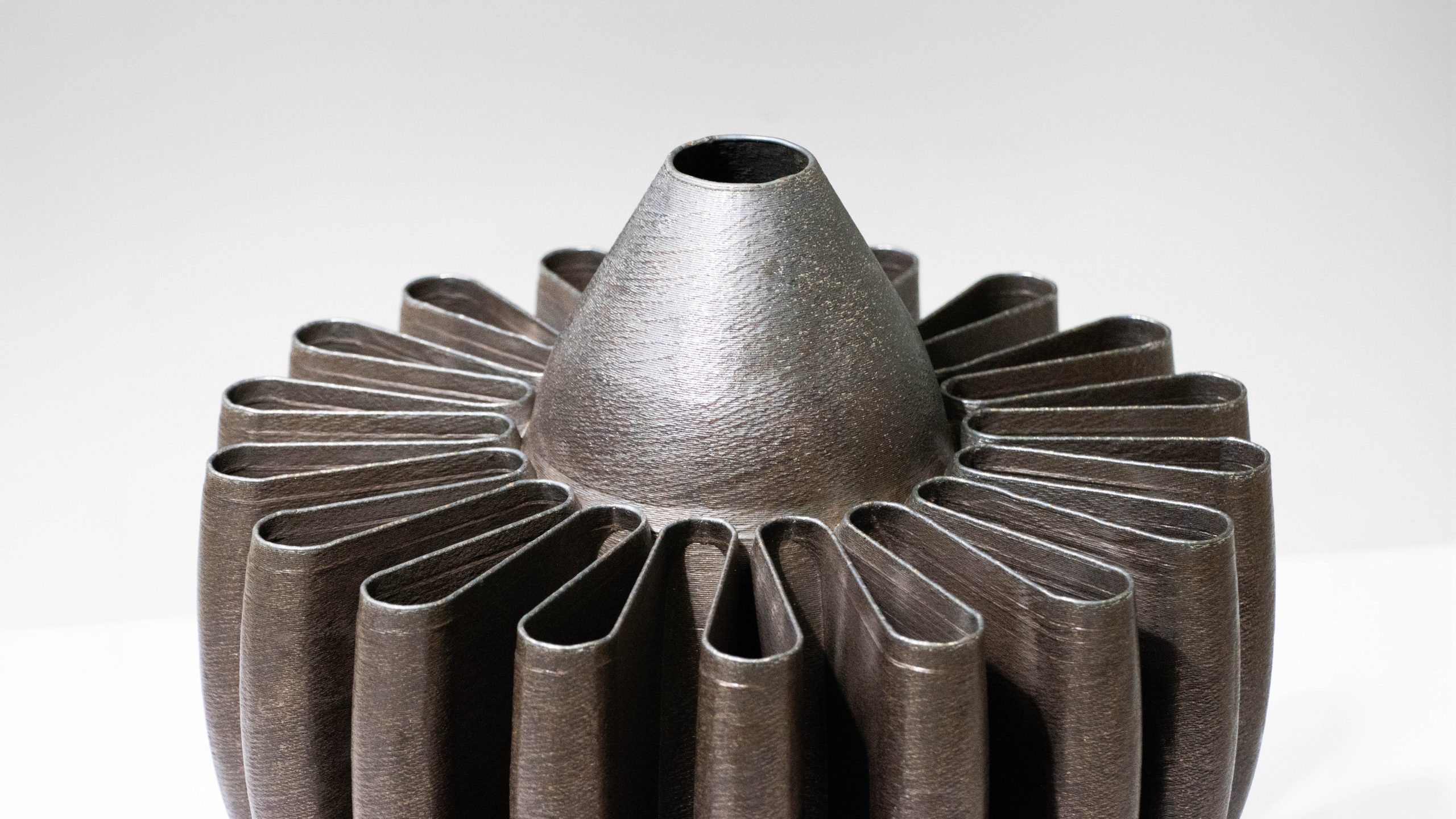
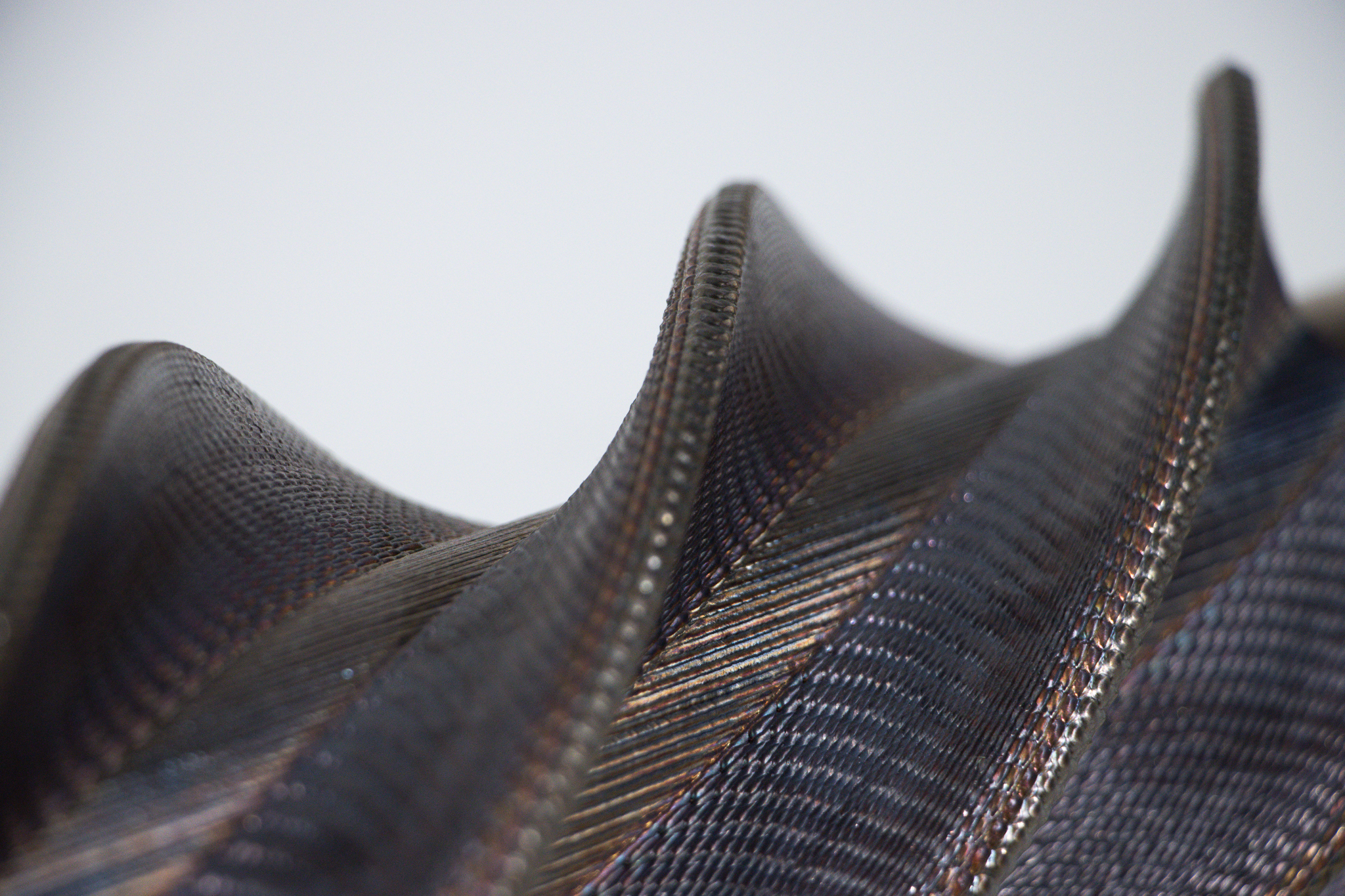
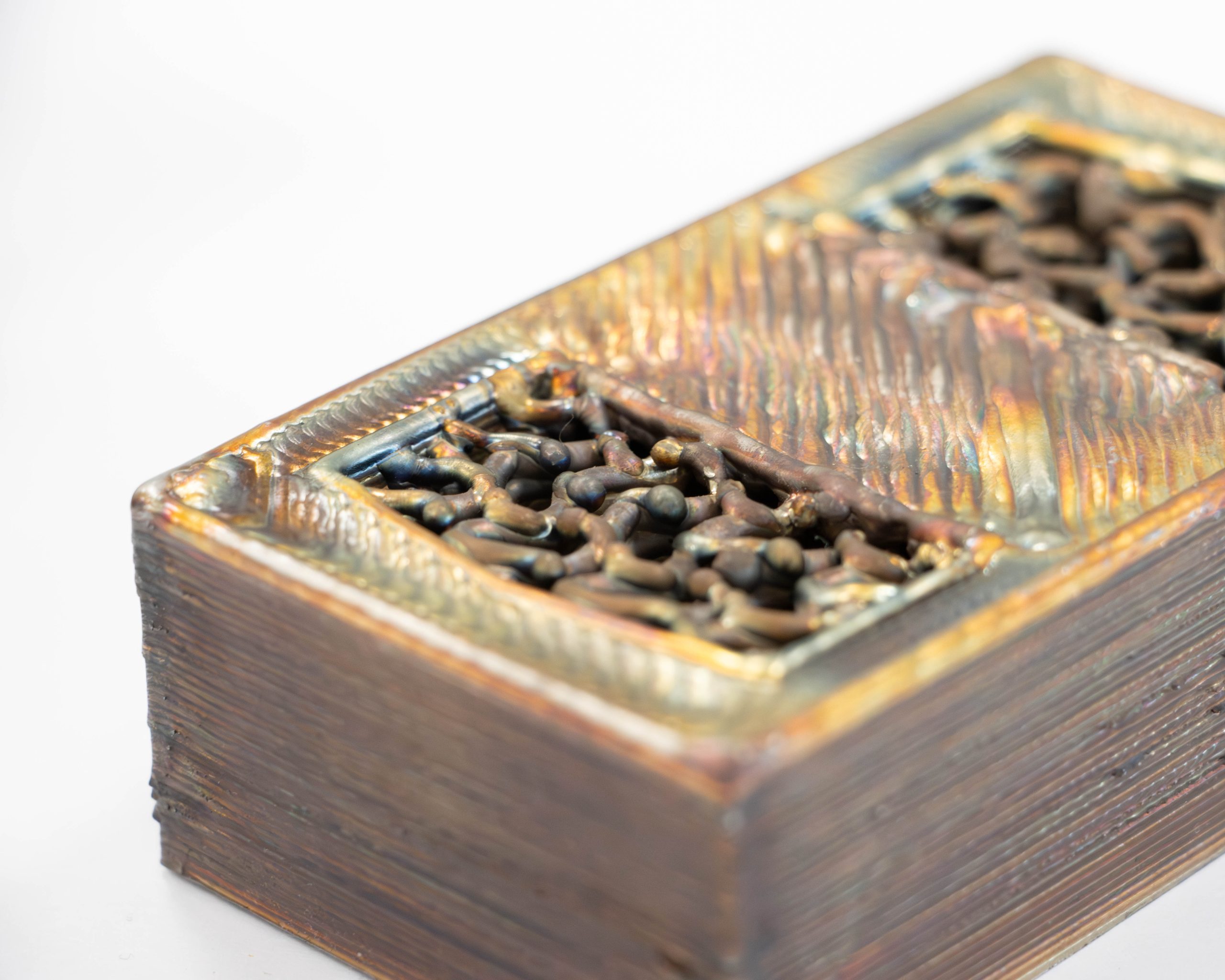
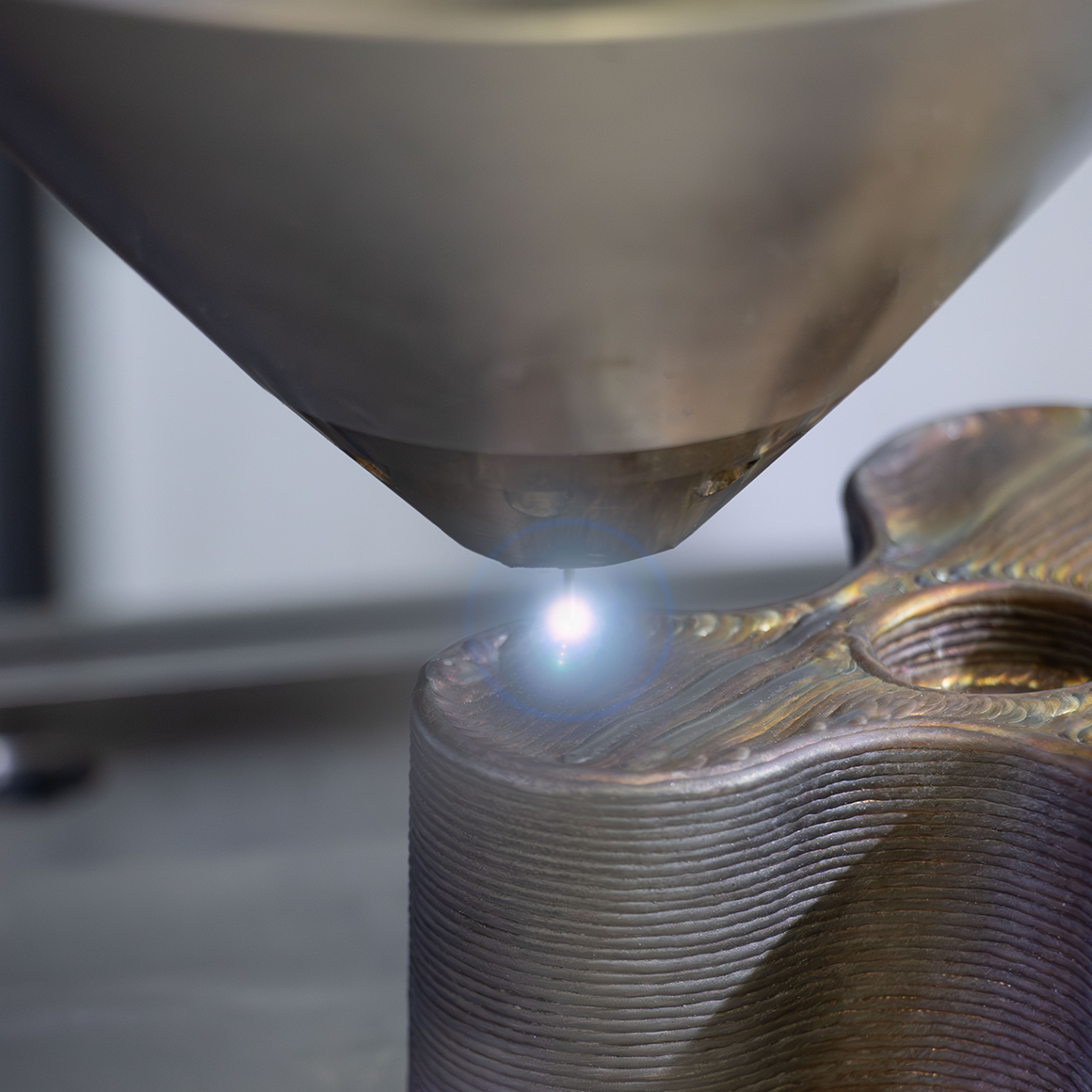
Conclusion
Meltio Stainless Steel is taking stainless steel to the next level. By leveraging cutting-edge additive manufacturing technology, Meltio Stainless Steel offers enhanced precision and flexibility in production, opening new possibilities for industries requiring custom parts, complex geometries, and superior material performance.
As the demand for high-performance materials continues to grow, Meltio Stainless Steel represents a significant leap forward, offering innovative solutions for the most demanding applications. Whether you’re designing parts for aerospace components, or precision engineering, Meltio Stainless Steel is set to redefine what’s possible with stainless steel.