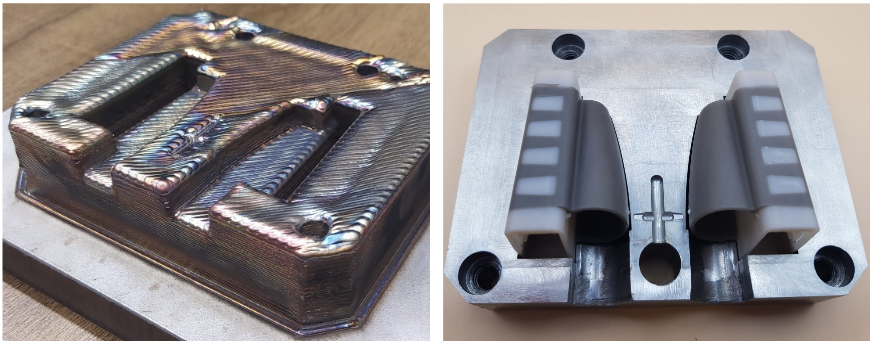
The EU Project imPURE managed to develop a methodology to reuse existing pilot lines for manufacturing medical materials through design and development of modular molds for injection molding. An Additive Manufacturing-enabled approach for fast repurposing of industrial IM lines was established and validated. A base master die was adapted to receive, align, clamp and release inserts of standard dimensions so that different dies could be quickly changed, thus reducing cost per die and setup time of each product.
CONIFY selected AISI-420 martensitic stainless steel for manufacturing mold inserts for oximeters, due to good corrosion and wear resistance. Poor ductility and toughness, together with AM-induced anisotropy, were the main challenges to address. CONIFY defined a multi-step methodology, combined with CFD simulation, to study the effect of different process parameters, validated through printing trials, to identify the process window in MELTIO M450 multi-material wire-laser metal 3D printer.
During 9-hour full scale printing of modified 3D models, to account for post-processing, the fine tuning of optimum parameters was selected as the approach for fast on-demand manufacturing. Raw material cost was another key-factor for assessing the value of the processes, where the cost for powder was at least 5-8 times higher than the commodity welding wire employed in the Meltio M450. Post AM Annealing heat treatments were necessary to reduce HRC values from 57 to 28.
The annealed inserts were subsequently machined to achieve the desired design features. For the final post-processing stage, CNC and die-sinking EDM and tool finishing were employed (Ra = 0.025 μm). The dimensional accuracy of the as-printed inserts was evaluated through 3D scanning to perform Digital Geometric Dimensioning and Tolerancing analysis. It was observed that the resulting average deviation between the as-deposited part and model was approximately 0.38 μm. The manufacturing IM trials successfully produced 1,000 sets of oximeters, verifying the quality of the DED molds and the overall methodology for rapid IM tooling manufacturing.
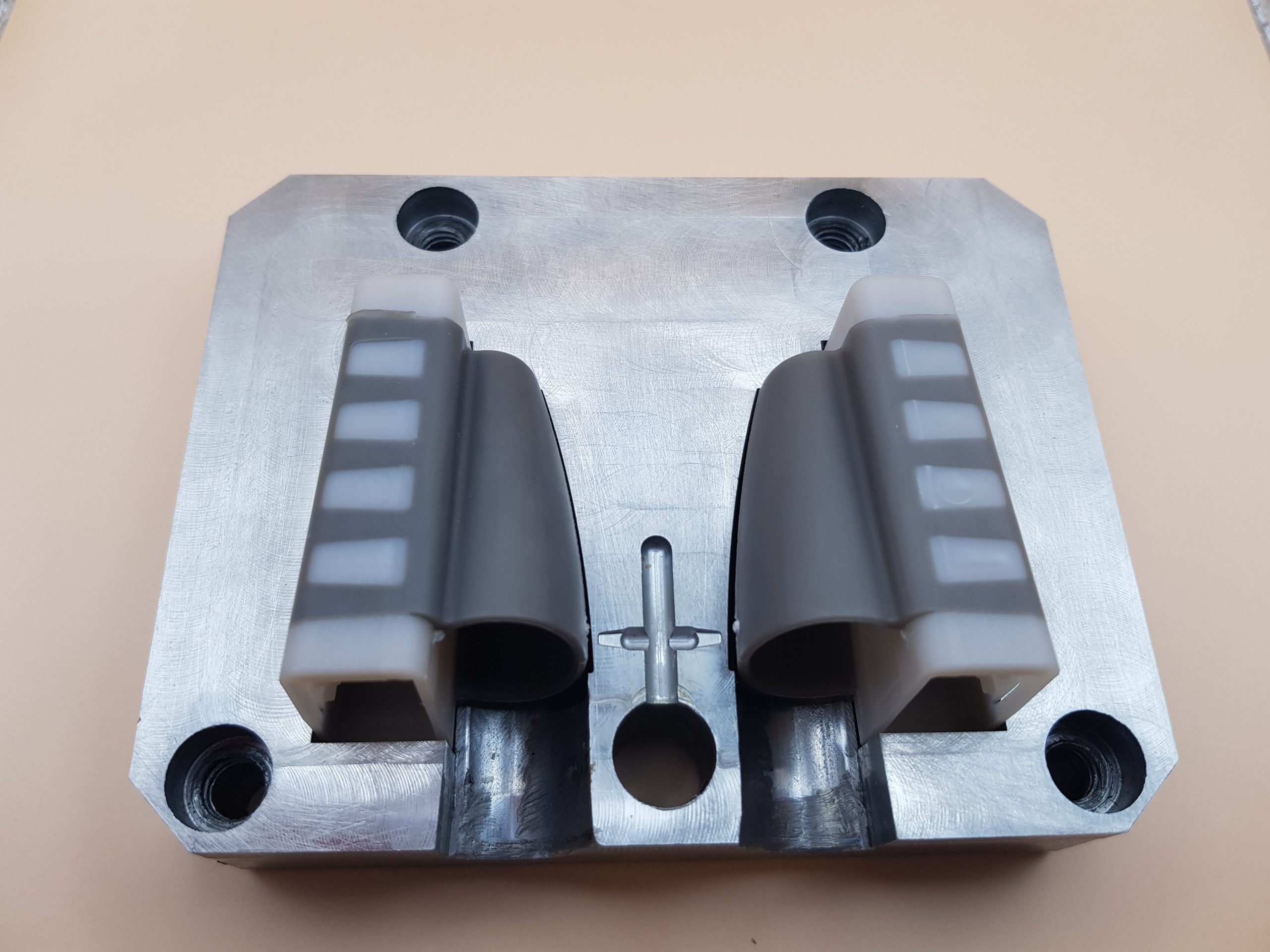