In the world of precision engineering, material selection is crucial for achieving durability, performance, and efficiency. Meltio’s advanced additive manufacturing technology revolutionizes the production of high-performance components by leveraging industry-leading alloys such as Invar, Nickel 718, and Nickel 625. These materials offer exceptional properties, from minimal thermal expansion for cryogenic and aerospace applications to superior strength and corrosion resistance for energy and marine industries. By overcoming the limitations of traditional manufacturing, Meltio enables more efficient production, optimized material usage, and enhanced design flexibility.
In this blog, we take a closer look at Nickel 718—its unique characteristics, real-world applications, and how Meltio’s innovative approach is redefining manufacturing across multiple industries.
1. Introduction to Nickel types
In this section, we explore three key nickel-based alloys—Invar, Nickel 718, and Nickel 625—each tailored for specific applications and performance requirements. From precision measuring instruments to aerospace components and high-temperature industrial systems, these alloys redefine the boundaries of engineering possibilities.
- Meltio Invar:
This alloy is named for its exceptionally low coefficient of thermal expansion, maintained from -250 °C to approximately 200 °C, making it ideal for measuring equipment and cryogenic applications.
Invar, a nickel-iron alloy, is prized for its high dimensional stability and minimal thermal expansion across a broad temperature range. These properties make it indispensable in precision instruments, scientific measuring devices, cryogenics, composite molds, and aerospace components.
- Nickel 718:
A high-strength nickel superalloy with a broad operating temperature range, offering excellent crack resistance and superior corrosion protection.
Nickel 718 is renowned for its exceptional mechanical properties in both high and low-temperature environments, making it ideal for demanding applications in aerospace, energy, and marine industries. Due to its challenging machinability with conventional methods, 3D printing enhances its versatility, enabling a wider range of applications.
- Nickel 625:
Nickel 625 is a high-performance superalloy known for its exceptional strength, corrosion resistance, and thermal stability across a wide temperature range. Widely used in aerospace, chemical processing, and the naval industry, it withstands extreme conditions and harsh environments. Notably, its superior weldability makes it particularly well-suited for cladding and repairing components exposed to high temperatures or requiring enhanced corrosion protection.
TIP: Download our printable materials list!
1.1. Nickel 718 superalloy
In the world of materials engineering, few alloys have achieved as much prominence as nickel 718. It is a nickel-chromium superalloy recognized for its impressive mechanical strength, its ability to withstand extreme temperatures and its resistance to corrosion. These properties have made it a key material in industries such as aerospace, energy and advanced manufacturing. In this article, we will explain what makes Inconel 718 so special and why it remains an irreplaceable choice in critical applications.

2. What makes Nickel 718 special?
- High mechanical strength
It hardens by precipitation of phases such as γ′ (Ni₃(Al,Ti)) and γ″ (Ni₃Nb), which allows it to maintain excellent mechanical strength at temperatures approaching 750°C without losing structural stability.
- Corrosion and oxidation resistance
Nickel 718 maintains its integrity in hostile environments, such as jet engines and nuclear reactors, where conventional materials would quickly fail.
- Enhanced weldability
Unlike many other nickel superalloys, nickel 718 has a low tendency to weld cracking, which facilitates its use in additive manufacturing and component repair processes.
2.1. Applications in various industries
Nickel 718 is widely used in various industries due to its balance between mechanical strength, thermal stability and corrosion resistance.
Aerospace industry
- Turbine discs and blades in jet engines
- Engine casings
- Aircraft structural components
Energy and nuclear industry
- Nuclear reactor parts
- Extreme environment power generation systems
Oil and gas industry
- Valves and piping for high pressure and corrosive environments
- Drilling tools
2.2. Parts made of Nickel
Gas Turbine Blade
Challenges of traditional Gas Turbine Blade manufacturing
Gas turbine blades are traditionally produced using investment casting, CNC machining, heat treatments, and coatings, followed by rigorous inspection.
However, while investment casting allows for complex geometries, it often results in defects like porosity and inclusions, requiring extensive post-processing. Additionally, traditional methods struggle with intricate internal features, such as cooling channels, limiting design flexibility. Also, this multi-step process leads to long lead times, high production costs, and increased defect rates, making conventional manufacturing both resource-intensive and time-consuming.
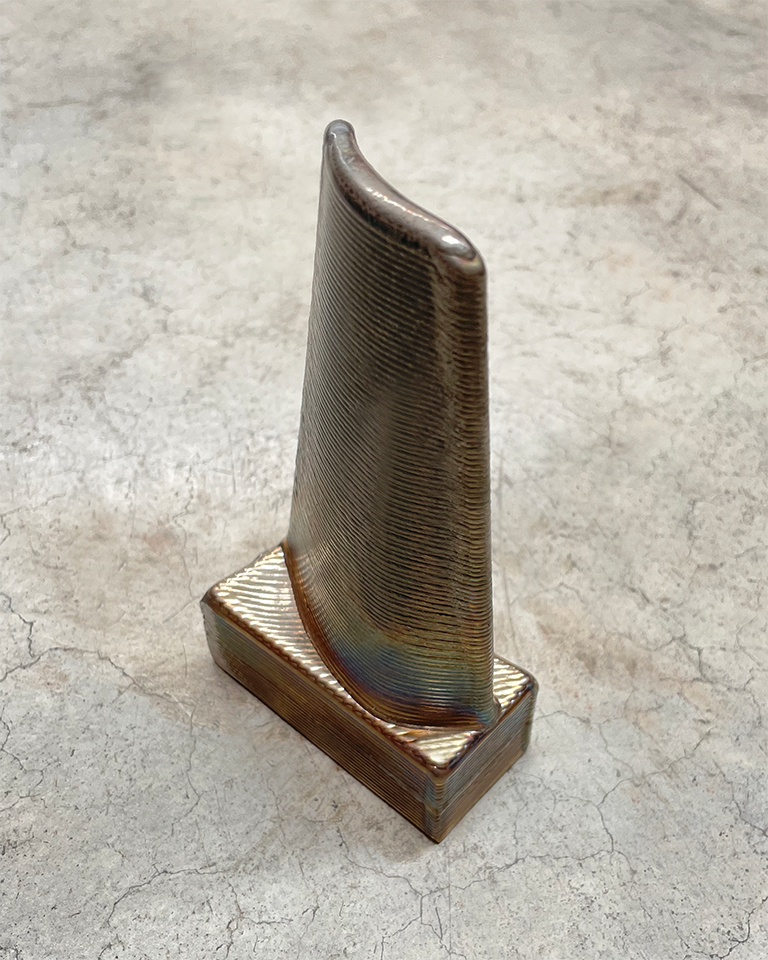
Meltio’s additive manufacturing advantage
Meltio’s additive manufacturing technology transforms turbine blade production by optimizing material usage, enhancing performance, and reducing costs. Unlike traditional methods, AM directly deposits Nickel 718, minimizing waste while refining grain structures for superior strength and fatigue resistance. The technology also enables advanced cooling designs, integrating complex internal channels that improve heat dissipation and turbine efficiency.
– Dual material pipe
Challenges of traditional Dual material pipe manufacturing
Conventional dual-material pipe production is a multi-step process that involves bimetallic welding, casting, machining, and post-weld heat treatment, all of which add complexity, labor costs, and material waste. Welding dissimilar metals requires specialized techniques, often introducing defects that demand rigorous quality control and testing, further increasing lead times and expenses. Additionally, traditional methods restrict design flexibility, limiting the ability to create seamless material transitions and optimized geometries.
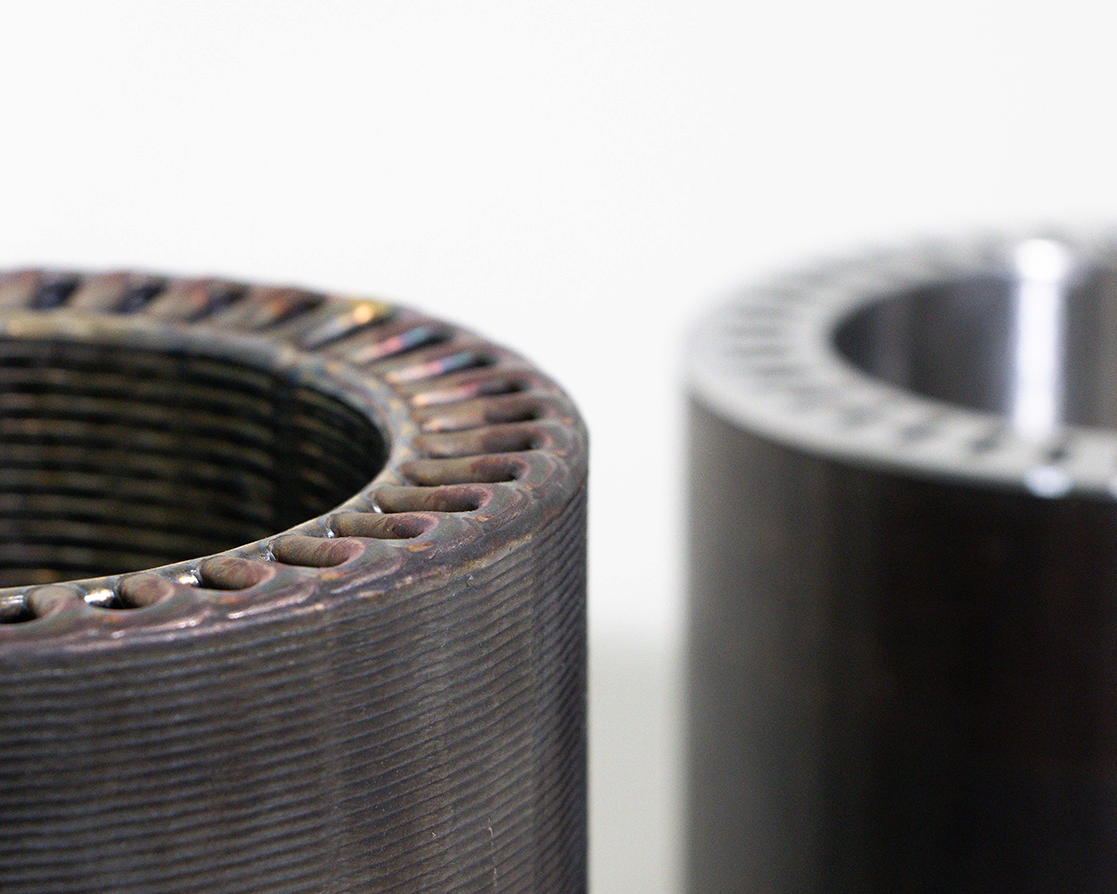
Meltio’s additive manufacturing advantage
Meltio’s additive manufacturing technology revolutionizes dual-material pipe production by enabling precise material deposition, significantly reducing waste and optimizing the use of high-cost alloys like Inconel 718. By achieving metallurgical bonding between materials, it eliminates weak points common in welded assemblies, enhancing structural integrity and durability. The streamlined process removes the need for complex joining techniques and extensive post-processing, cutting both production time and costs while offering greater design flexibility for more efficient and high-performance components.
– DM Combustion Chamber
Challenges of traditional Dual material pipe manufacturing
Traditional manufacturing involves multiple steps: laser cutting, forming (bending, stamping, press forming), and welding (TIG, EBW), adding complexity and time.
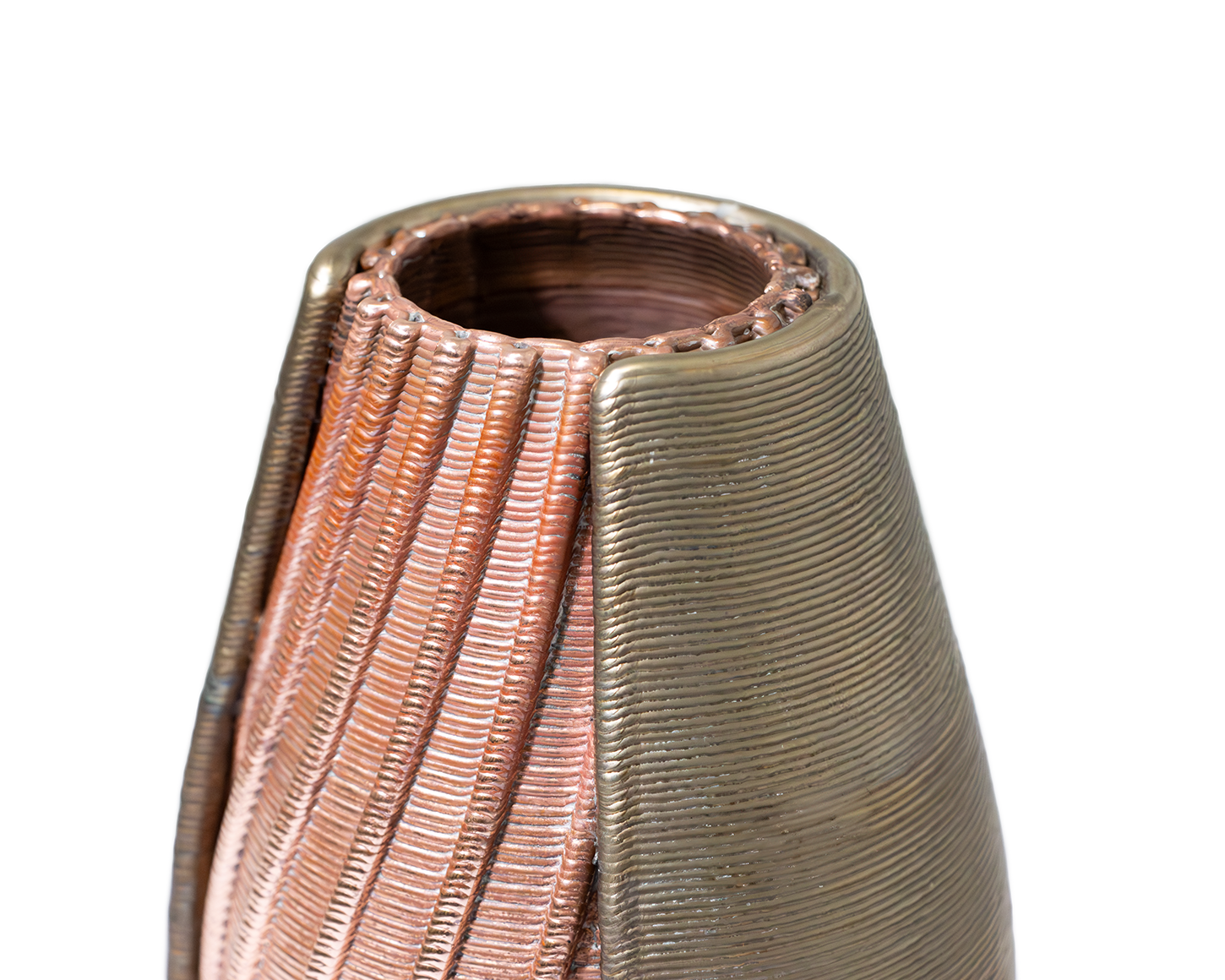
Meltio’s additive manufacturing advantage
Meltio’s deposition process streamlines production into a single-step 3D printing method by crafting a part in its near-net shape. Another important capability that enhances the production process of this part when using Meltio’s technology is the Dual Material capability of our systems, where different materials can be used in a single printing process.
This allows the interior to be printed with CuCrZr for efficient heat transfer and the exterior with Inconel 718 for structural integrity in high temperatures.
By optimizing production and minimizing post-processing, additive manufacturing drastically reduces lead times and costs. Meltio’s technology delivers exceptional high-temperature strength and precise dimensional accuracy, establishing a new benchmark for performance and reliability in advanced manufacturing.
TIP: Download the Meltio Applications catalog!
Nickel 718 in Meltio systems
Laser and wire additive manufacturing is known to be a manufacturing where there are rapid temperature changes. These uncontrolled cooling from melting temperatures after the laser passes determine the type of final microstructure the parts will have. This cooling, coupled with the fact that there is a clear temperature gradient parallel to the manufacturing direction, results in anisotropic microstructures.
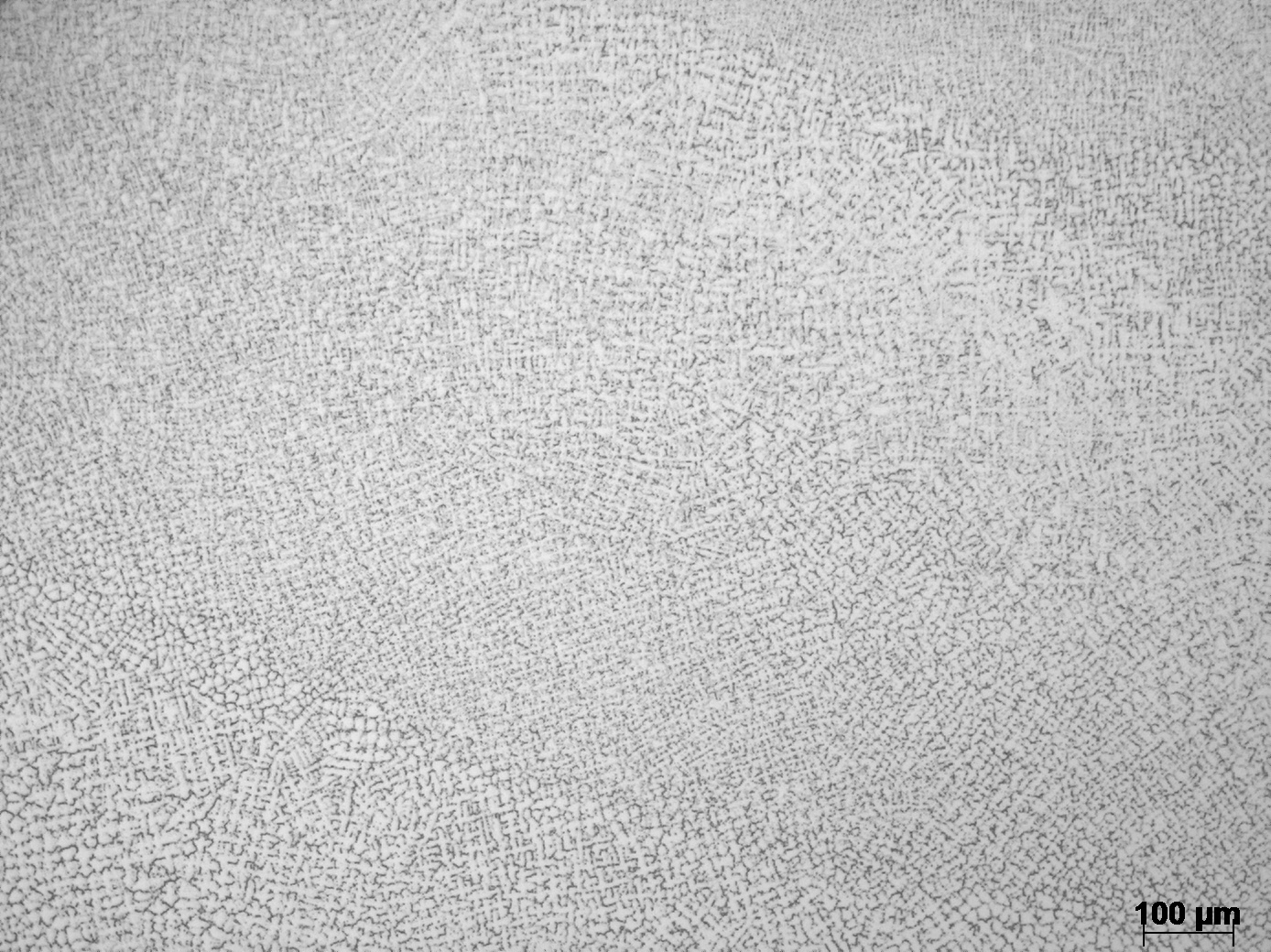
Microstructure of Nickel 718 in as-printed state
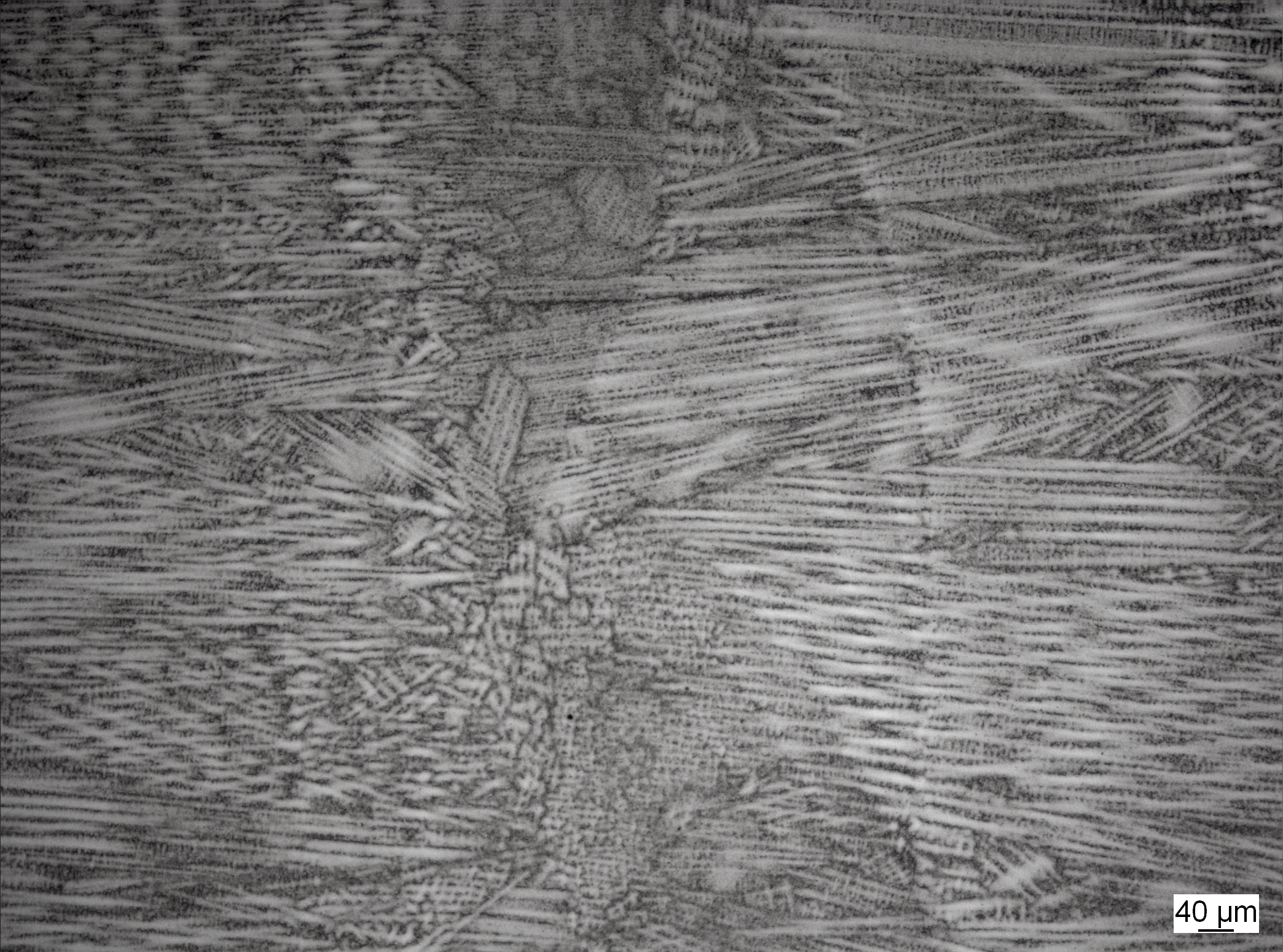
Microstructure of Nickel 718 after solubilisation and aging heat treatment
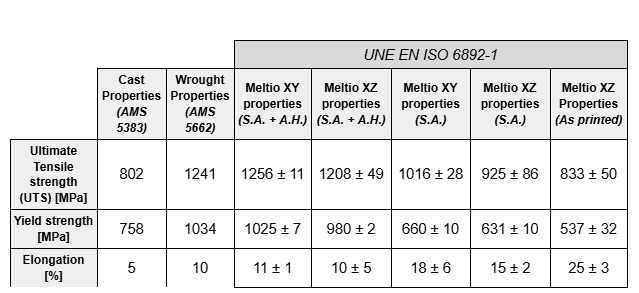
Tensile mechanical properties of Meltio Nickel 718
If we stop to look at the resulting microstructure after fabrication, delta phase dendrites (Ni₃Nb) can be observed aligned along the fabrication direction within the gamma nickel matrix (γ). The delta phase is a niobium-rich intermetallic phase that forms during the solidification process and heat treatments, and its presence can influence the microstructure of the material, especially its ductility and mechanical strength.
Under further magnification, additional intermetallic phases have been identified along with the presence of gamma prime (γ′-Ni₃(Al,Ti)), which is a key hardening phase in this superalloy. It is the combination of the γ′ phase and the γ″ phase that gives the alloy its exceptional mechanical strength and thermal stability. However, the delta phase, when present in excess, can negatively affect ductility and reduce the creep resistance of the material.
This is why, in order to find the balance point between all the aforementioned phases that makes the mechanical behavior of the alloy optimal, all parts made of this alloy must always be subjected to solubilization heat treatment and subsequent aging.
These findings are relevant for evaluating material quality and optimizing manufacturing and heat treatment parameters to achieve an adequate balance between mechanical strength, ductility and creep resistance in critical applications.
Conclusion
Meltio’s additive manufacturing technology is redefining the production of high-performance components by harnessing the exceptional properties of nickel-based superalloys like Meltio Nickel 718. By overcoming the limitations of traditional manufacturing, Meltio enables greater design flexibility, reduced material waste, and enhanced mechanical performance across industries such as aerospace, energy, and marine applications.
The microstructural analysis of Nickel 718 parts produced with Meltio systems highlights the importance of optimized heat treatments to achieve a balance between strength, ductility, and creep resistance.