Reaching where traditional manufacturing cannot
In the context of today’s military and industrial operations, the need for reliable and efficient manufacturing solutions has never been higher. Traditional supply chains often fail to meet the urgent demands of operatives, especially in conflict zones where logistics are complicated and a lack of parts can bring important missions to a halt. Aware of these challenges, Meltio offers innovative additive manufacturing solutions to overcome critical shortfalls in defense logistics and maintenance.
Supply chain disruptions can have serious consequences, leaving operatives without critical components at critical times. Meltio’s technology offers on-site manufacturing solutions to address these challenges, providing the ability to produce parts directly at the point of need. This innovation benefits not only defense logistics, but also sectors such as oil and mining, where delays due to missing parts can be costly.
The problem was addressed with Snowbird’s Meltio system, SAMM Tech, which integrates Meltio’s metal wire-directed energy deposition (DED) print Head with a FANUC-controlled CNC system into a portable shipping container, allowing on-demand production of critical components anywhere and alleviating this problem.
This is a Department of Defense-approved directed energy deposition (DED) technology that uses standard welding wire and eliminates the need for additional steps such as heat treatment, improving the efficiency and speed of part production. In addition, the choice of safe raw materials, such as the use of compressed argon gas, reflects Snowbird and Meltio’s commitment to safety and ease of use in the work environment.
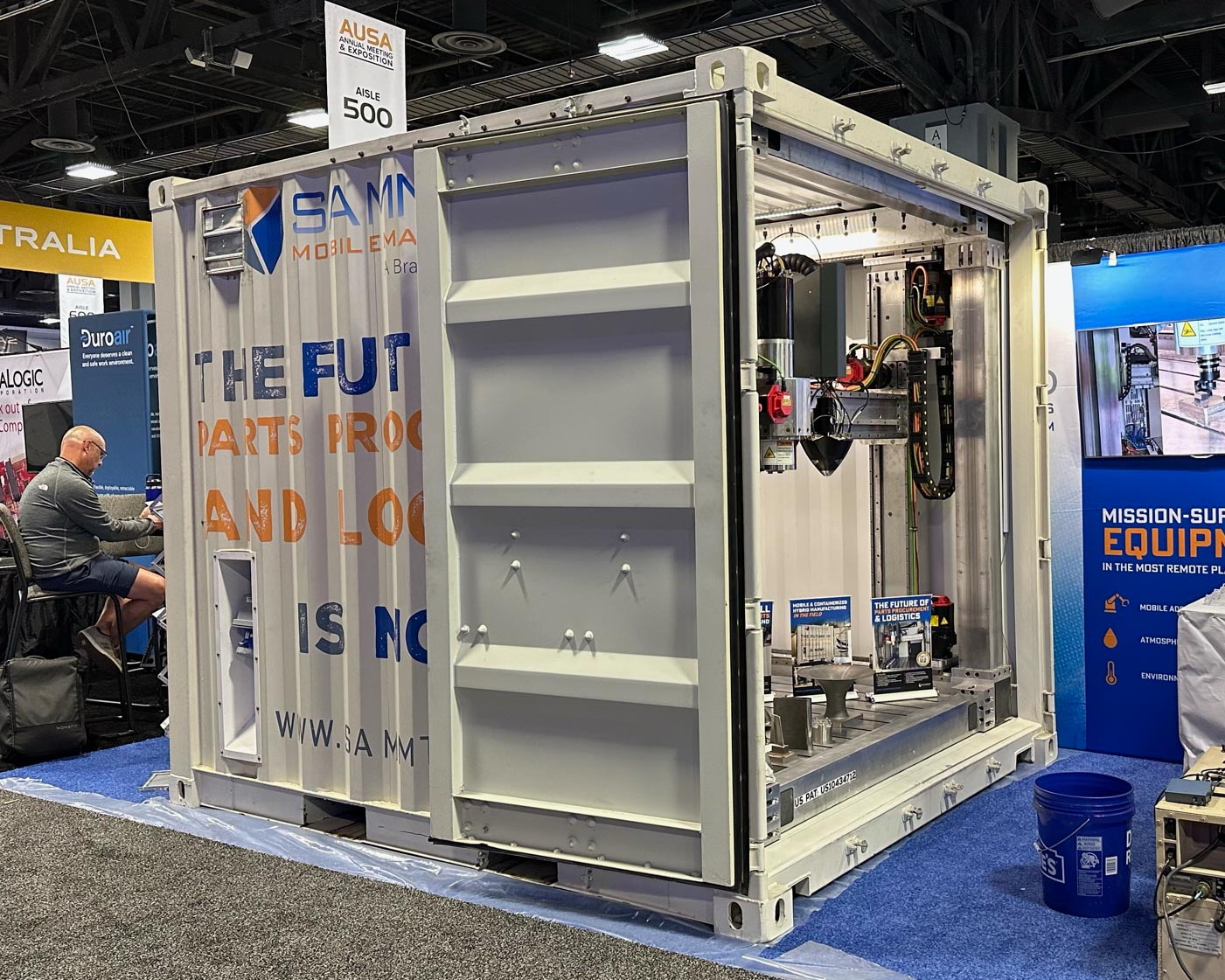
Consolidating our position in the defense sector: The essential role of Meltio technology
3D printing, or additive manufacturing (AM), has been and continues to be an area of great interest to the Department of Defense in recent years. In January 2021, the U.S. Department of Defense unveiled its first Additive Manufacturing Strategy. This strategy aims to establish common principles and a framework to facilitate the development and implementation of this technology. The purpose is to support the modernization and improve the readiness of military forces.
This need for the use of metal 3D printing has become more noticeable after what happened recently aboard the Somerset, the first ship to use AM. We tell you about it:
When the team of engineers from the Consortium for Advanced Manufacturing Research and Education (CAMRE) took their Meltio metal hybrid 3D printer aboard the Somerset as part of the experimentation sector of Exercise Rim of the Pacific 2024, they had no idea they would soon be called upon to solve a real-world engineering incident.
Hours after boarding, a critical component of the reverse osmosis pump, which generates clean water for the crew -an absolute necessity for ships spending extended periods at sea-broke down.
«What we didn’t expect was that we would have the opportunity to directly help ship readiness so soon», said Lt. Charles Wallace, a mechanical engineer at the Naval Postgraduate School, and one of the team members on board «Especially for something as mission-essential as a reverse osmosis pump, where if you run out of water you’re going to be coming home pretty quick.».
What advantages has additive manufacturing brought on board this vessel?
The advantages of successfully implementing additive manufacturing on ships include saving time, money and space, as well as allowing equipment repair and replacement in a contested environment. In the case of the Somerset, if the reverse osmosis pump had failed during its 6-month deployment, it would have reduced its ability to produce potable water for sailors and Marines.
Somerset had a single hybrid metal machine on board, combining subtractive and additive manufacturing from Meltio, the DED manufacturing unit from Snowbird Additive Mobile Manufacturing Technology (SAMM Tech). It is worth remembering that, as a rule, both additive and subtractive manufacturing are involved in the construction of a replacement part. Before testing the model at Somerset, this meant switching between different machines, but combining the two processes streamlined the overall workflow.
With this solution, DED-3D printed components require no post-processing or heat treatment, making the SAMM Tech with the Meltio head a very suitable machine for military applications that require metal parts at short notice. Parts can therefore be 3D printed, milled and finished on the same machine.
The hybrid machine represents a step forward for the military, as explained by Wallace «The benefit of a system like this is that you’re able to computerize [a component], send the code, then once you’ve printed something, it becomes replicable»
Not only is 3D printing faster and safer than traditional machine repair, but replacement parts are often stronger as well. Welding is almost as strong or stronger than the original metal. AM is essentially building by welding, which means that the replacement pump will potentially exceed the strength of the previous version.
3D printing will directly help the Somerset achieve something that was previously impossible: the creation, repair and replacement of vital equipment at sea. While the Department of Defense may face a number of material readiness challenges in the future, there is no doubt that advanced manufacturing will be part of future solutions. 3D printing opens up new avenues to ensure that the U.S. Navy can provide continuous security and stability from anywhere, at any time. The aim is to reduce the delivery time of critical parts from days to hours.
TIP: Discover how Meltio’s unique technology is helping armed forces around the globe.

Benefits of using Meltio metal 3D printing for defense
Directed energy deposition (DED) technology is at the forefront of additive manufacturing and is transforming the production of complex metal components. Unlike traditional methods using powders, DED uses standard welding wire as the raw material, offering unparalleled versatility and cost-effectiveness. This wire, available in a variety of alloys, provides manufacturers with a wide range of materials, from stainless steel to titanium, allowing the creation of customized parts according to specific needs. This flexibility is applicable to multiple industries, such as aerospace, automotive and defense, where precise material selection is crucial.
The collaboration between Snowbird and Meltio has resulted in the SAMM Tech platform, which integrates Meltio’s DED technology. This integration has enabled Snowbird to offer a deployable and versatile additive manufacturing solution that can operate in any environment. Whether producing critical components for military operations or supporting industrial applications in remote locations, SAMM Tech represents a disruptive innovation in additive manufacturing. In the face of increasing pressures to maintain operability in dynamic and challenging environments, Snowbird and Meltio are positioned at the forefront by providing solutions that help operators overcome obstacles and meet their mission objectives.
Safety
The use of welding wire in DED technology improves safety and reduces dust-related risks. The use of inert compressed gases, such as argon, reduces the likelihood of fires during transport and fabrication. This safety feature not only protects personnel and equipment, but also ensures continuous production, improving operability in high-risk environments. In addition, the precise deposition of metal layers with DED technology minimizes material waste, optimizing the use of resources and promoting sustainability in manufacturing processes.
Precision in manufacturing
By harnessing a focused energy source, DED achieves exceptional precision in layer-by-layer metal deposition, enabling the creation of intricate parts with mechanical properties. This precision extends to large-scale component manufacturing, where DED excels at delivering high-quality results with minimal post-processing requirements.
The ability to produce complex geometries and integrate multiple materials into a single part highlights the versatility of DED and its suitability for demanding applications. As industries continue to embrace additive manufacturing for its efficiency and agility, DED stands out as a proven solution to meet the evolving needs of modern manufacturing.
Hybrid manufacturing
Create highly complex parts with machining tolerances in the same process. This synergy offers several significant advantages. First, it reduces overall production time by combining both processes into a single workflow, eliminating the need to transfer parts between different machines. Second, it enables the repair and modification of existing components by adding new material on top of already machined structures, optimizing the use of resources and extending part life.
In addition, the ability to integrate multiple materials in a single hybrid operation allows the creation of components with improved mechanical properties and additional functionalities, tailored to the specific needs of various industries, such as aerospace, automotive and defense.
Part repair and Feature Addition
Meltio technology offers numerous advantages by enabling the repair and upgrade of existing parts. By extending the life of expensive components and significantly reducing material and labor costs, Meltio not only promotes more sustainable practices by minimizing waste and the need to produce new parts, but also optimizes operational efficiency by facilitating on-site repairs, reducing downtime.
In addition, Meltio’s “feature addition” feature adds new features to parts by depositing perhaps more costly material in critical areas and less costly material in the rest of the part, allowing for modifications, customizations and refurbishments without the need to manufacture new parts. This design flexibility and the ability to adapt and enhance existing components transforms parts management, offering cost-effective, sustainable and adaptable solutions that improve efficiency and durability in industrial environments.
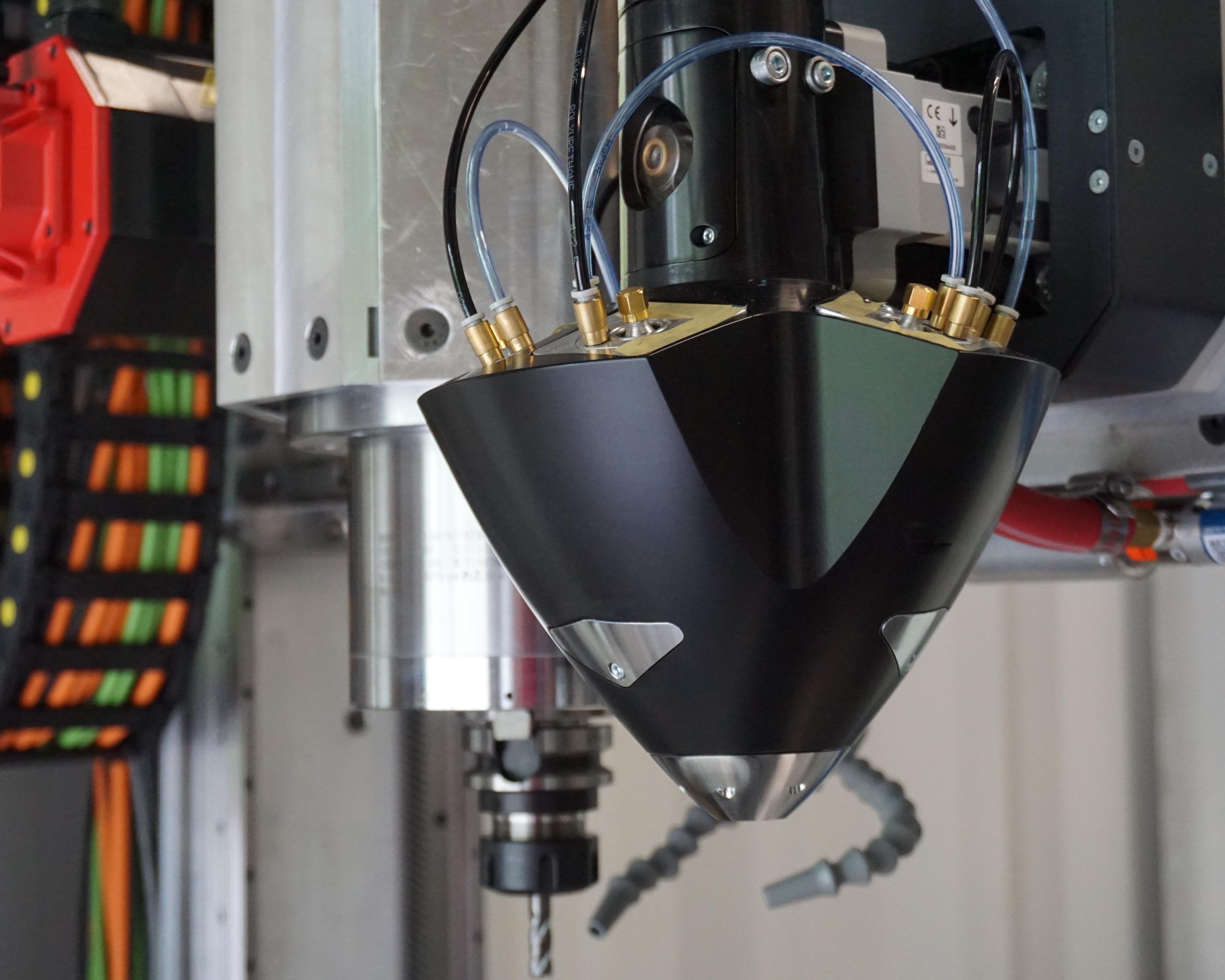
Conclusion
Meltio offers the defense sector a robust and adaptable solution that optimizes the production, repair and customization of parts, thus strengthening the effectiveness and sustainability of military operations.