Laser wire deposition’s latest coaxial architecture, in which a wire-based feedstock is fed into a laser-generated melt pool to build 3D parts, provides a lower-cost, cleaner, and faster way to generate large and complex metal components with excellent material properties.
Laser wire deposition systems for additive manufacturing typically consist of a centrally fed material, with the nozzle positioned vertically to the workpiece and an arrangement of laser beams converging on the material at a set distance. In some cases, these are beamlets from a high- and single-power laser being split up or independent beams from separate laser sources.
In these systems, the alignment of the laser and wire at the focal spot must be controlled. If the material and the laser focus is not perfectly positioned, there is a strong likelihood that defects will form in the workpiece because the material does not receive sufficient heating to fully fuse with the beads around it.
This alignment step is typically carried out by eye and requires significant operator experience and patience. With laser wire deposition systems becoming a more broadly accepted technology, the user base is shifting from research-oriented technology centers and universities to production-oriented operators in the machine shop and manufacturing industry. With this change, ease-of-use and system setup time are also evolving, and manual alignment is no longer acceptable.
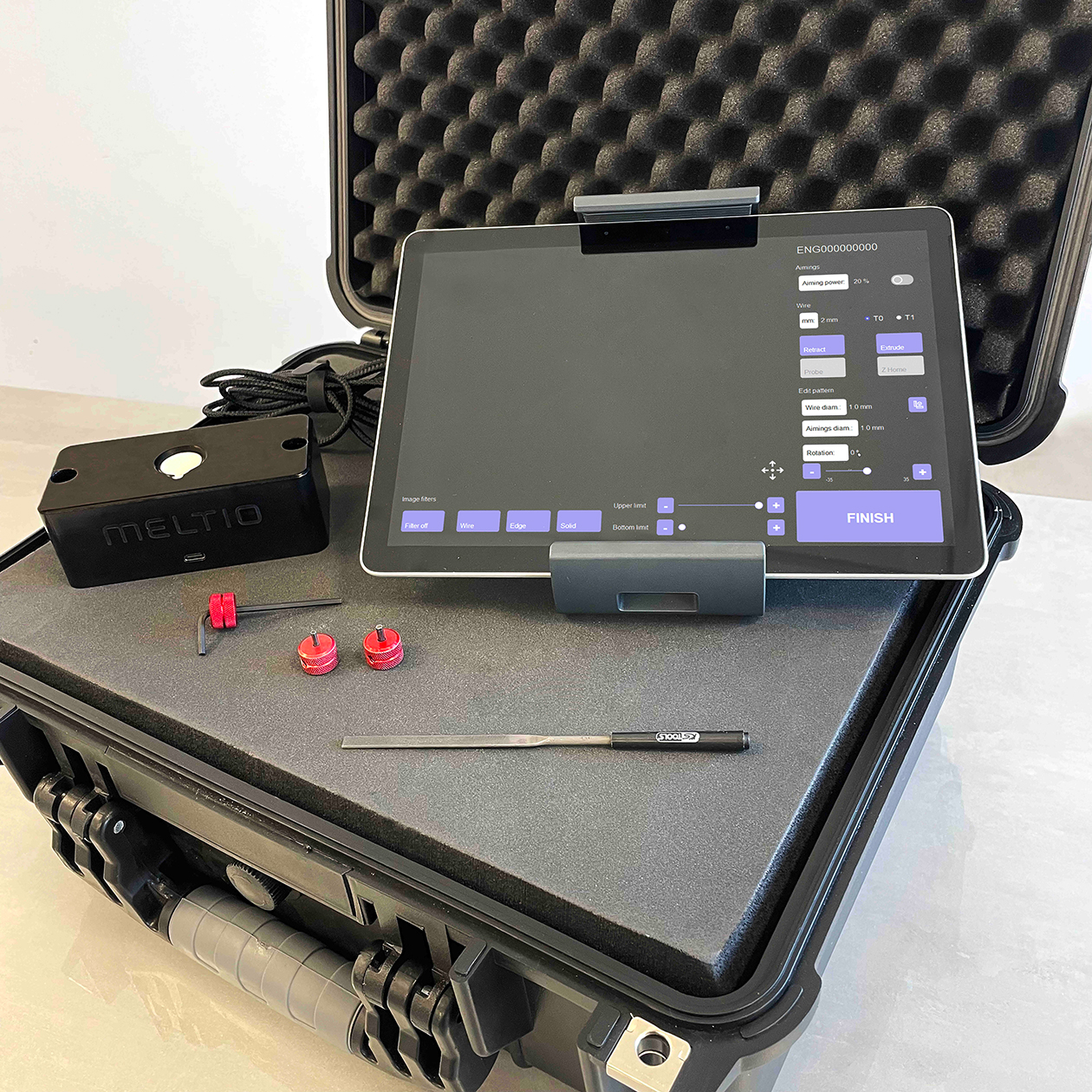
Because wire-based metal 3D printers offer an advantage over powder-based solutions such as fast turnaround time when the material is changed and no clean-up is required, a wire straightener-based system would be insufficient for users. This prompted Meltio to develop a tool to precisely determine the position of both the laser spots and material, while also guiding the operator to adjust each laser to its ideal position. The benefit of this standalone tool is that legacy Meltio systems can connect and function with a simple software update.
System architecture
The Meltio system’s printhead consists of six adjustable optical assemblies—light is coupled into it from six separate laser sources and a fixed wire nozzle. Its deposition head has a dual-wire material feeding system to accurately control the amount of material dispensed into the melt pool at any given time. This deposition head has a set of sensors to measure and regulate the printing process based on material force and material conductivity.

Adjustment of the lasers is carried out through a system of precision screws that allow each optical assembly to be precisely rotated and locked into position once the final alignment is reached, similar to the adjustment of kinematic optical mounts. Each laser is equipped with a visible light pilot/aiming laser with only a few milliwatts of power that can be used to guide the laser alignment rather than the main beam in the infrared domain.
The system for alignment is required to pick up the position of the individual spots, as well as the position of the welding wire. Meltio designed a solution based on a camera along with optical and image filters. It is delivered with a tablet and mounting solution for 3D printers or robotics integrations so the user has the viewing screen in the correct location during alignment. This alignment process allows the operator to control the relevant printer functions, which enables the pilot lasers and material feeders to make the process as hassle-free as possible.
The alignment process begins by setting the camera in the machine. After this, the nozzle automatically pushes out material until it touches the sensor surface of the camera. The camera then locates the wire position. Next, the aiming lasers are enabled and a grid is drawn on the tablet screen—indicating the ideal position of each laser. Once adjustment is complete, a picture can be saved to record the correct laser alignment.
This system allows users without previous experience with laser systems to precisely adjust it within 10 minutes—significantly reducing the need for technical support.
Despite being a small part of the overall laser wire deposition system, laser alignment tools play a big role in reducing operator error and increasing system reliability and consistency.