Industrial laser systems have standardized around a common design—a fiber-coupled infrared laser paired with application-specific processing optics. This approach streamlines interoperability and reduces development costs, enabling system integrators to focus on specialized optics. However, this standardization also limits performance in certain applications, such as laser wire deposition. Here, blue lasers, with their superior absorption by reflective metals and higher energy efficiency, hold distinct advantages.
Optimizing industrial laser systems: Beyond the conventional approach
Industrial laser systems have largely converged on a standardized design: a fiber coupled infrared laser connected to a variety of processing optics, tailored for applications ranging from Laser marking through Additive Manufacturing to welding and cutting.
This standard factor brings several benefits to its users, including enhanced interoperability and reduced development costs. By standardizing the laser source, which can be supplied by various manufacturers, system integrators can focus only on developing the specific processing optics required for different applications.
However, this standardized approach also comes with limitations, especially when striving for optimal performance in specialized processes. A prime example is laser wire deposition. In this process, the advantages of shorter wavelength lasers, particularly those in the blue spectrum, are well-documented. Blue lasers offer higher processing speed and stability across a wide range of metals and they consume less energy for the same operation due to the higher absorption of blue light.
Further, they allow for the processing of highly reflective materials (Copper, Aluminium, Gold) which reflect the vast majority of infrared light. Despite these benefits, the adoption of blue laser sources in this sector has been slow, limited by their high cost, which is several times that of near-infrared (NIR) lasers of similar output power.
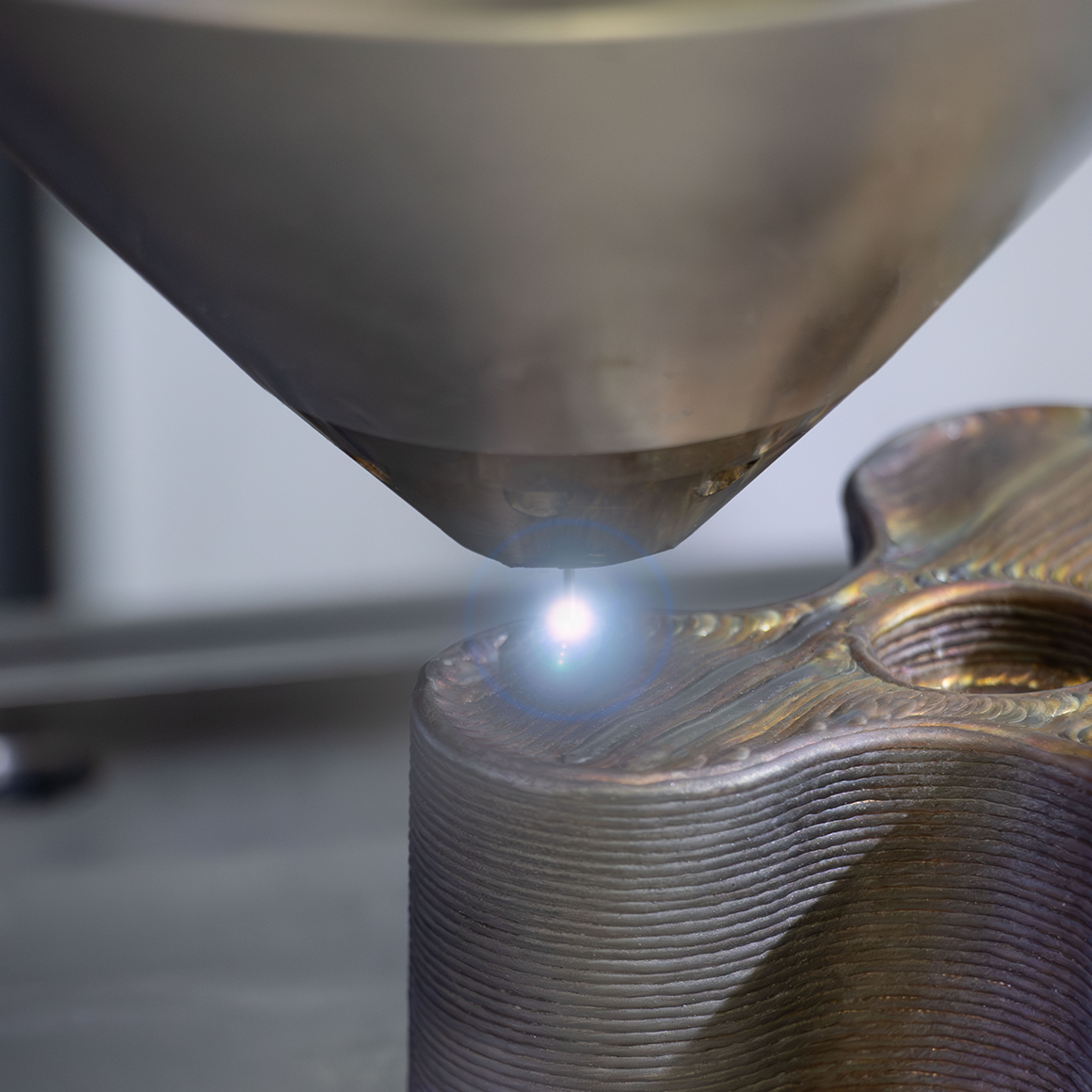
Challenges with Blue Laser sources
The significant cost difference stems from the challenges of fitting blue lasers into the conventional fiber-coupled laser format. Blue laser emitters are less powerful and generally have worse beam quality compared to NIR lasers. This makes the internal alignment necessary to pack the light into a single fiber with high beam quality complex and costly.
In laser wire deposition, processing optics typically split a single laser beam into various beamlets, which then impinge on the wire from multiple directions, allowing for uniform material deposition.
Meaning that for a conventional laser wire deposition system, we first need to solve the complex challenge of combining multiple low powered laser emitters within the laser source and then develop a complex processing head that splits the single laser beam into multiple beams to melt and deposit the filler material.

A customized approach for Blue Lasers
A more effective solution would therefore be to develop a customized laser that directly outputs multiple beams for laser wire deposition. This concept, initially demonstrated with NIR lasers, shows even greater promise for blue lasers where the challenges of beam combining are greater.
Further benefits of the direct usage of multiple laser beams can be realized thanks to the improved energy distribution of such systems. The output from direct diode lasers tends to be more homogeneous than the Gaussian distribution of fiber-coupled devices. This homogeneity leads to better energy utilization and higher process efficiency, ensuring that all areas of the spot receive sufficient energy without excessive and insufficient concentration in certain areas.
Integration and practical benefits
At a system level, integrating the laser source into the processing head offers additional practical benefits. With this approach, only electrical and cooling connections are required for the deposition head, eliminating the need for high-power fiber optics. This simplification enhances robustness and ease of handling while reducing the risk associated with uncontained fiber failures.
Since the laser light is generated within the laser-safe processing environment of the system, it mitigates potential hazards associated with damaged laser fibers in non laser safe environments.

Blue lasers in Meltio’s additive solutions: A new era for metal additive manufacturing
Meltio is advancing metal additive manufacturing with its innovative blue laser technology. By integrating blue lasers at a 450 nm wavelength, Meltio systems achieve enhanced energy absorption across a broad spectrum of metal materials, opening up new possibilities for metal 3D printing. The two systems featuring blue laser technology are the Meltio M600 and the newly upgraded Meltio Engine Blue, equipped with the Meltio Engine Integration kit for Vertical Machining Centers and for Industrial Robots.
In Wire-Directed Energy Deposition (DED), high-power lasers melt and deposit metal wire as filler material. Meltio’s blue lasers are optimized for metal absorption, offering distinct advantages over traditional infrared lasers:
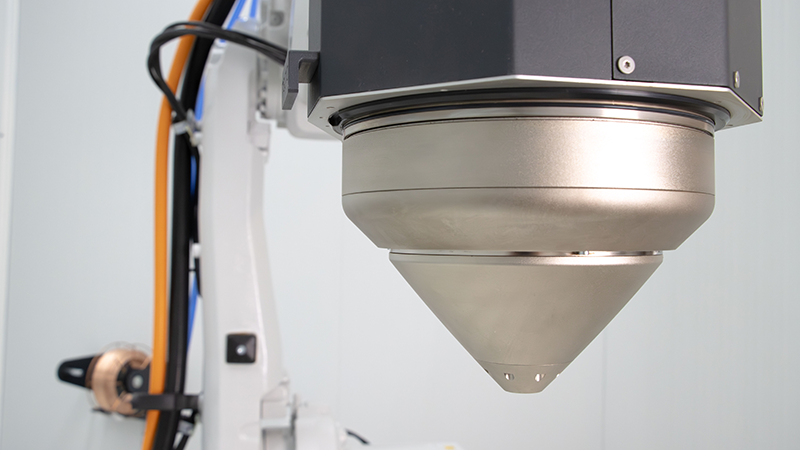
Superior metal absorption for higher efficiency
Blue lasers enable metals to absorb better. With their wavelength reduced to 450 nm, they are optimal for absorption, directing more laser energy to heat and melt the metal, achieving a faster and more efficient deposition. This optimal absorption enhances the entire deposition process, making it both faster and more precise.
Faster and greener printing
Now achieving higher speeds in metal 3D printing while simultaneously reducing energy consumption is possible. Blue laser technology allows for faster deposition without increasing laser power, helping Meltio systems create parts faster while using the same energy. This results in not only quicker production cycles but also a more environmentally sustainable process.
Expanded material versatility
Traditional laser wavelengths often limit the range of printable metals. Blue lasers, however, significantly broaden material compatibility. With improved light absorption across different metals, blue lasers support a wider variety of materials, allowing manufacturers to print difficult-to-process metals, explore new alloys and composites. This versatility unleashes greater creativity and innovation for applications in diverse industries.
TIP: Discover how Meltio’s unique technology can help your manufacturing needs.
Conclusion
While the standardized fiber laser coupled with processing optics remains a reliable choice for many industrial applications, specialized processes like laser wire deposition can significantly benefit from customized laser solutions such as those developed by Meltio. By moving towards directly outputting multiple laser beams and integrating the laser source into the processing head, systems achieve better performance, process highly reflective materials, improve energy efficiency and safety without breaking the bank.
The promise of blue lasers, despite their current cost challenges, highlights the potential for continued innovation and optimization for process specific industrial laser systems.