Additive manufacturing, commonly known as 3D printing, has transformed the landscape of production, design, and innovation. Among its advanced techniques, Directed Energy Deposition (DED) shines as a leading method for constructing and repairing high-performance metal parts. In this realm, Meltio has emerged as a pioneering solution, offering a unique approach by using wire-laser metal additive manufacturing for unmatched precision and versatility.
This blog will explore the groundbreaking potential of additive manufacturing, delve into the distinctive strengths of DED technology, and showcase how Meltio’s WLM-DED process is redefining what’s possible in industrial applications.
TABLE OF CONTENTS
- What’s Additive Manufacturing
- Pros of Additive Manufacturing
- Additive Manufacturing Technologies
- Directed Energy Deposition (DED): An advanced Additive Manufacturing process
- Wire +Laser, a new DED combination: WLM-DED
- Why is this Wire-laser Metal combination a smart choice?
- The benefits of Meltio’s WLM-DED process
- Conclusion
1. What’s Additive Manufacturing (AM)?
The term “Additive Manufacturing” refers to the process of making physical objects in 3D by extruding material, layer by layer, to obtain desired shapes. For manufacturers, additive manufacturing often refers to the industrial use of 3D printing for tasks such as tool and die building, prototyping and design validation, as well as short-run production of end-use parts.
Using additive technologies (AM), geometry is obtained by adding material from virtual geometry, without the use of preforms (conformal techniques) and without subtracting material (subtractive techniques), allowing parts to be obtained directly from a 3D CAD file, “printing” them in a fully controlled manner on a surface.
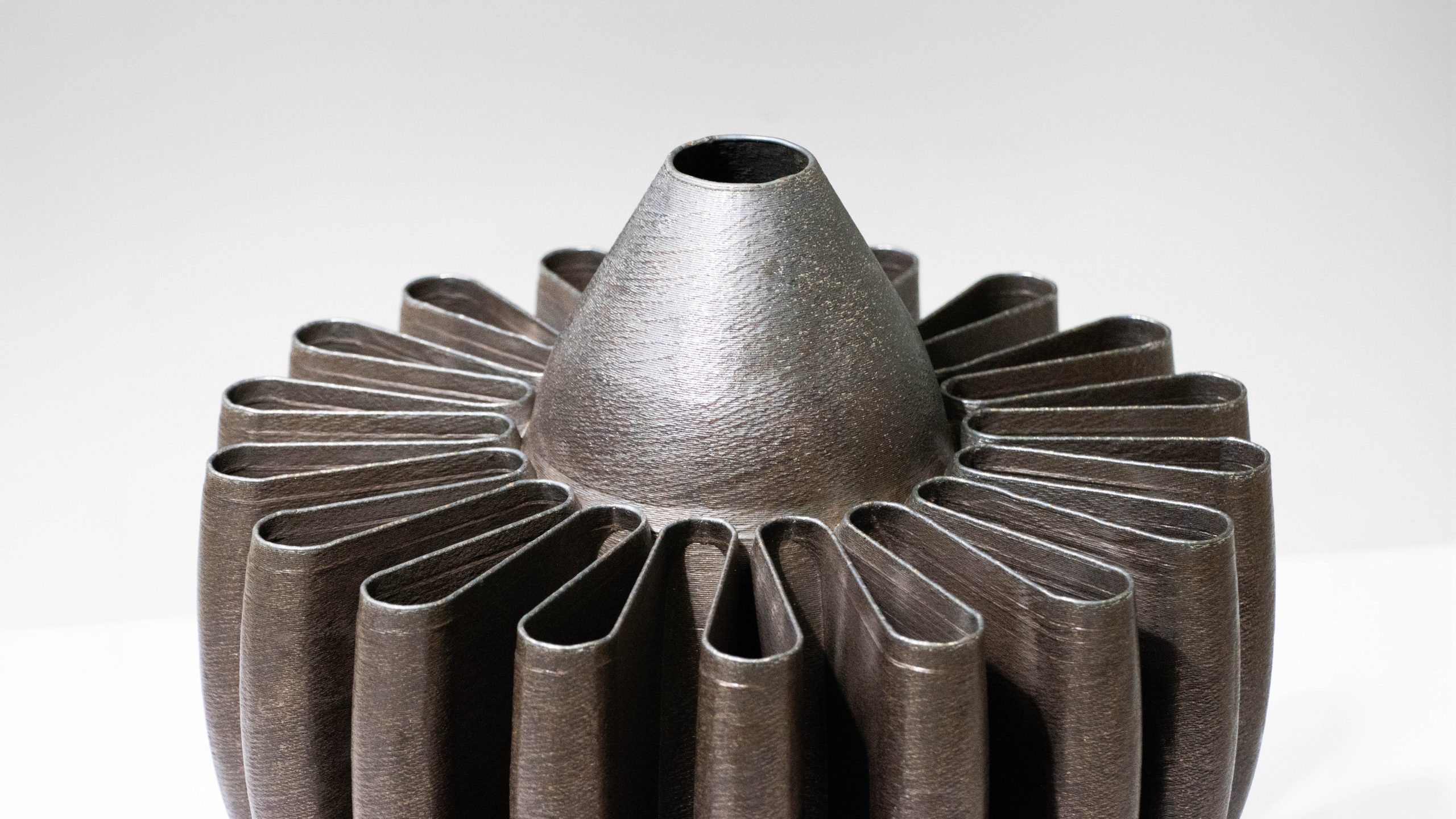
2. Pros of Additive Manufacturing
Additive manufacturing presents many advantages, so let’s explore some of them:
– Geometric complexity: The processes used to manufacture parts are often subject to the limitations of traditional manufacturing. In addition, traditional manufacturing often requires the use of multiple manufacturing processes, which increases production costs and the possibility of errors between processes. With additive manufacturing, parts can be designed without these steps and limitations. In addition, 3D printing can produce complex geometries that are not possible with other manufacturing techniques.
– Customization and design freedom: which is one of the major trends today in developing high-value products with complex designs, eliminates the unnecessary limitations of subtractive manufacturing processes.
– Previously unattainable results: it makes it possible to realize executions that are simply not possible with any manufacturing technology (subtractive or conformal) at various stages of the industrial value chain.
– Reduce time-to-market and costs: drastically reduce many of the current launch and validation phases, as well as possible errors throughout the production cycle and in intermediate processes. Manufacturers are less dependent on external suppliers and minimize the risk of supply chain operations.
– Smart material usage: Reduce material costs by adding material only where it is needed (topological optimization). This is very difficult to achieve with traditional manufacturing methods.
– Value chain optimization: Having an in-house additive manufacturing system speeds up design cycles by enabling rapid prototyping and the production of any part in much less time than it would take to order and receive it through traditional manufacturing processes.
3. Additive Manufacturing technologies
Additive manufacturing (AM), commonly referred to as three-dimensional (3D) printing, is recognized as one of the twelve disruptive technologies driving the fourth industrial revolution (Industry 4.0).
There are seven main types of 3D printing technologies, along with over 20 subtypes. These include Material Extrusion, Vat Polymerization, Powder Bed Fusion, Material Jetting, Binder Jetting, Directed Energy Deposition, and Sheet Lamination. In particular, powder bed fusion (PBF) and directed energy deposition (DED) are two key AM processes used to produce industrial components.
In the category of Powder Bed Fusion (PBF) techniques, a thin layer of metallic powder is spread over the build platform, and a laser or electron beam selectively melts the powder to create the desired shape one layer at a time. The process is repeated for each layer until the final part is complete.
Within the Powder Bed Fusion, metallic additive manufacturing processes including Selective Laser Sintering (SLS), Direct Metal Laser Sintering (DMLS), Selective Laser Melting (SLM), and Electron Beam Melting (EBM) fall under this category.
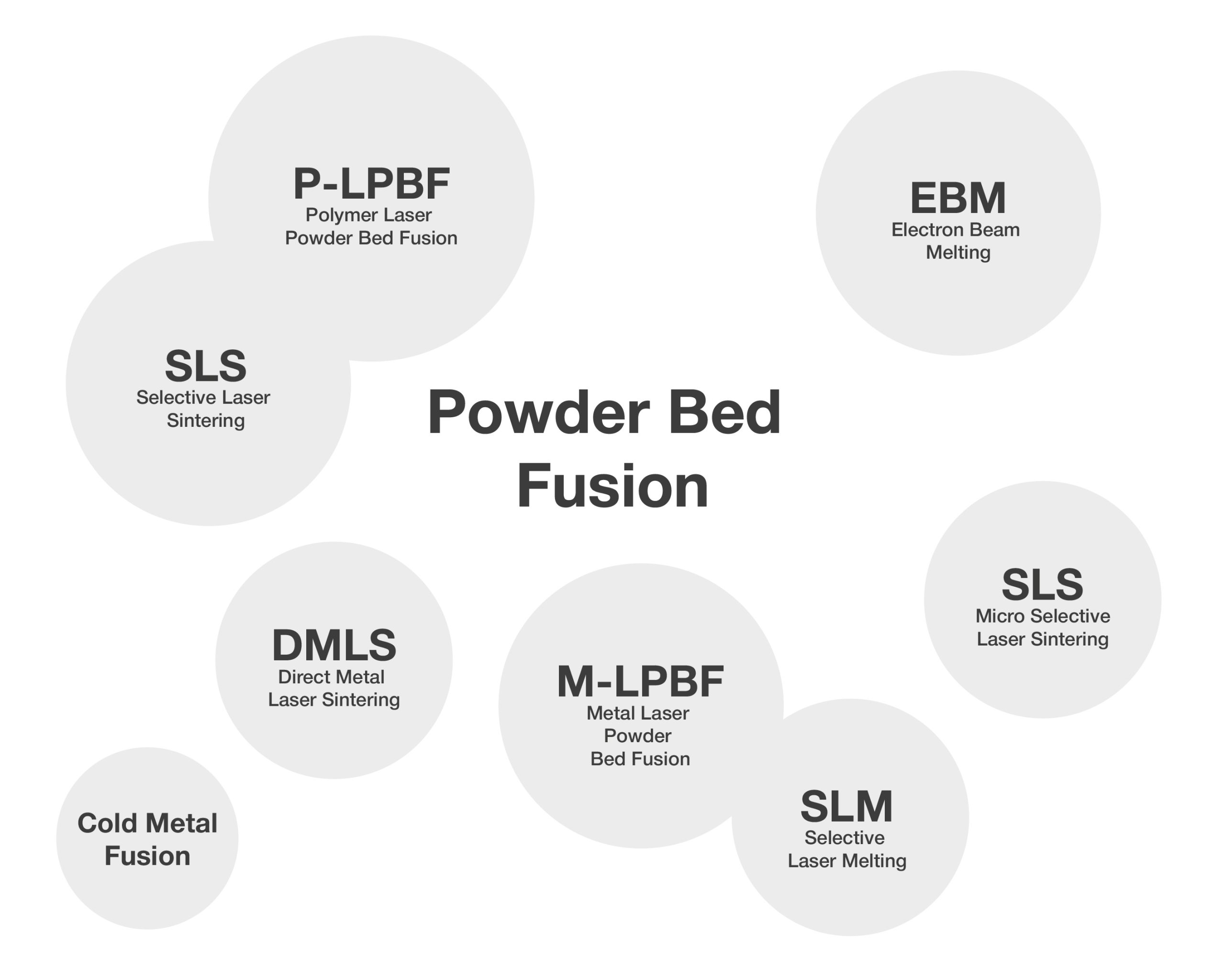
On the other hand, Directed Energy Deposition (DED) is a metal 3D printing process that consists of depositing a material (a powder or a metal wire) layer by layer that is melted by a concentrated energy source. Among the most prominent are WAAM, W-DED, L-DED, and ours, which is WL-DED.
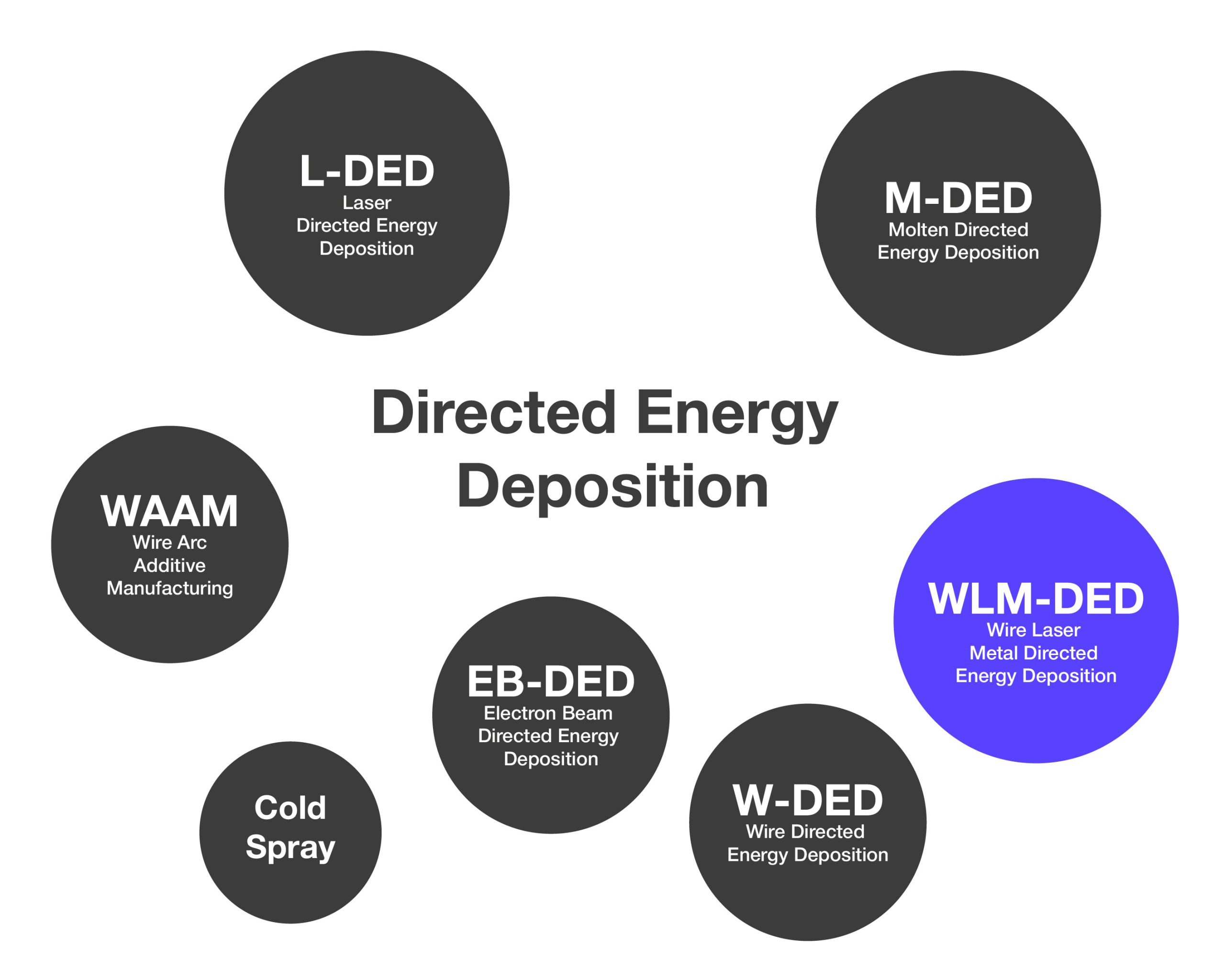
4. Directed Energy Deposition (DED): An advanced Additive Manufacturing process
Directed energy deposition (DED) is a branch of additive manufacturing (AM) processes where feedstock material, delivered in the form of powder or wire, is deposited onto a substrate while an energy source—such as a laser beam, electron beam, or plasma/electric arc—simultaneously creates a localized melt pool. This enables the material to be continuously deposited layer by layer.
The process involves precise movements in the X-Y plane to shape each layer according to a preprogrammed geometry. A Z-axis offset, determined by the specified layer height, is introduced incrementally between the deposition head and the substrate. This cycle is repeated to build successive cross-sections of the desired structure.
DED is a complex process influenced by numerous variables that dictate the thermal history and solidification of the deposited material. These factors significantly impact the microstructure, physical characteristics, and mechanical properties of the final component.
This technology offers distinct advantages and challenges, making it especially suitable for repairing or adding features to existing parts. DED is gaining significant traction in the industry due to its ability to produce near-net-shape, large freeform structures more quickly and cost-effectively than traditional casting and forging methods.
One of the most promising applications of DED is the repair of high-value or unique components. This approach provides a highly economical alternative to manufacturing replacements from scratch. Furthermore, DED enables the integration of different alloys during repairs, enhancing the service life and functionality of the components. These capabilities underscore the transformative potential of DED in modern manufacturing and repair applications.

5. Wire + laser, a new DED combination: WLM-DED
Meltio, a technology within the Directed Energy Deposition (DED) category, specializes in the Wire-Laser Metal DED process (WLM-DED). This laser-based wire feed technology enables the production of “near net shape” parts—components that are close to their final dimensions—requiring only minimal finishing. By significantly reducing the material discarded during rough machining operations, this approach minimizes waste. Coupled with its high input efficiency, the WL-DED process offers substantial savings in both material usage and overall waste associated with traditional machining methods.
The combination of using wire as feedstock and a laser as the energy source in DED is considered a new combination in the context of additive manufacturing due to its unique advantages and recent advancements in technology.
While DED itself has been in use for several years, the specific use of wire feedstock with a laser energy source is a relatively recent development and has gained increasing attention in various industries.
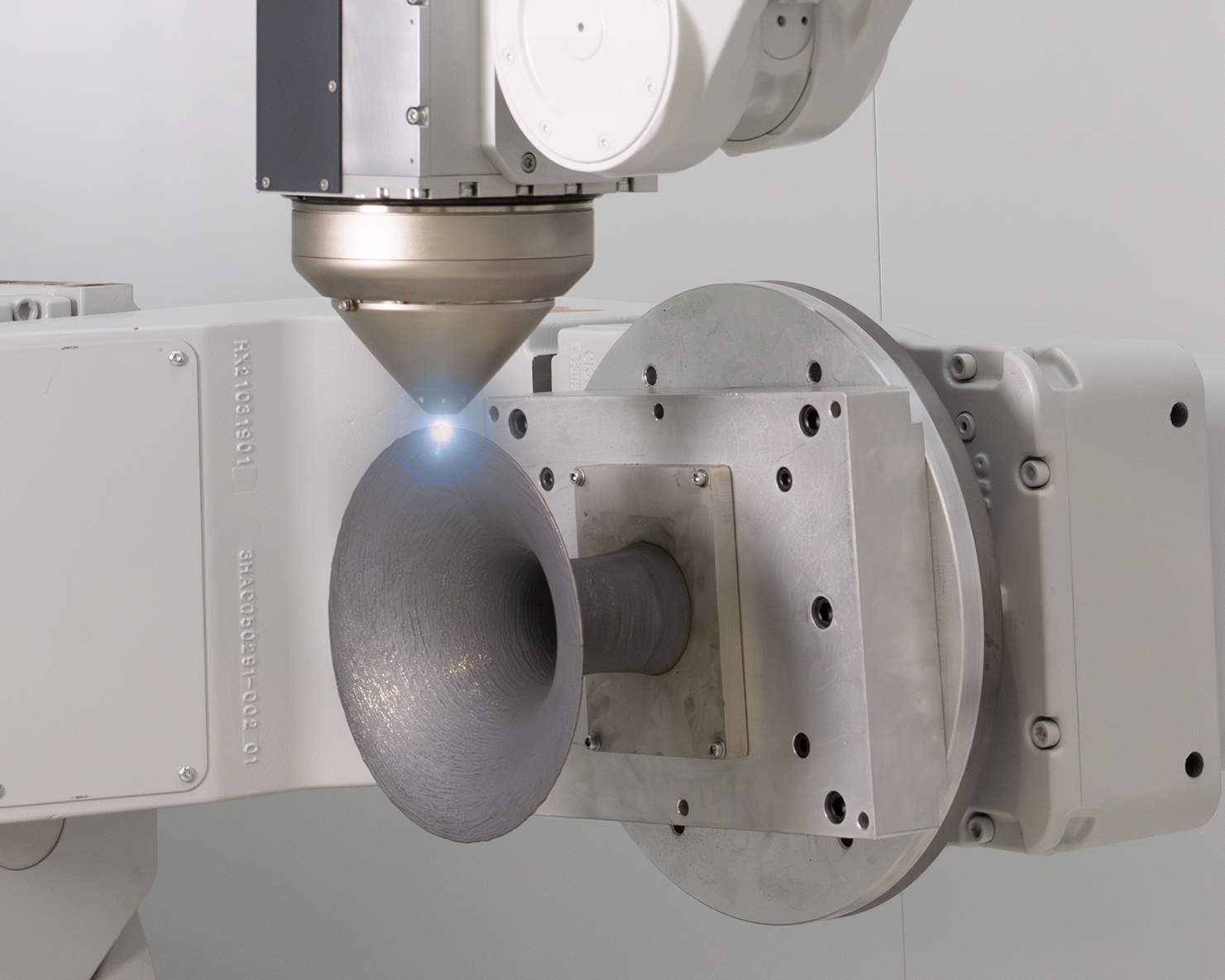
6. Why is this Wire-laser Metal combination a smart choice?
Here are some reasons why this combination is considered new and noteworthy:
– Material versatility: The use of wire feedstock offers a wider range of material options compared to other DED feedstock options, such as powder. This grants the deposition of a broader variety of alloys, making it well-suited for a diverse range of applications across different industries.
– Continuous deposition: The continuous feed of wire feedstock during the DED process allows for a seamless and uninterrupted additive build, resulting in increased efficiency and reduced production time. This continuous deposition also eliminates the need for frequent interruptions and manual handling, further streamlining the process.
– Large-scale applications: This combination is particularly well-suited for producing large-scale components due to the continuous feed and reduced need for support structures. It allows for the creation of sizable parts with reduced production time and cost-effectiveness.
7. The benefits of Meltio’s WLM-DED process
The use of wire feedstock with a laser energy source in DED has gained momentum in recent years, with increasing research and industrial applications. These features make it a new and promising option in the field of additive manufacturing, generating significant interest and exploration across various industries. Here are some advantages of why Meltio’s process stands out:
– Weight reduction: Meltio technology enables the use of dual materials in manufacturing, allowing for cost-effective production rather than solely focusing on weight reduction. For instance, the internal part can be made from an inexpensive material, while the external uses a higher-performance material tailored to specific mechanical requirements. Additionally, weight reduction can be achieved through topological optimization, a unique advantage of 3D printing, which minimizes material usage without compromising structural integrity.
– Hybrid manufacturing: Meltio’s hybrid manufacturing capabilities excel in producing parts with challenging geometries, such as curved pipes. This innovative process combines additive manufacturing with machining, enabling seamless transitions between printing and machining cycles. By machining during the printing process, Meltio technology ensures that even areas previously considered difficult to access can be reached and finished to precise specifications.
TIP: Discover Meltio’s hybrid manufacturing system: Meltio Engine Integration Kit for Vertical Machining Centers
– Large-scale applications: Meltio technology offers an efficient solution for repairing high-value or high-cost parts that have suffered damage. Instead of manufacturing the entire part anew, repairs can restore the component to full functionality, saving time and resources. Additionally, Meltio’s system can print new features onto existing parts, further reducing printing times and material costs. The Meltio Engine makes these processes faster and more economical while maintaining high-quality results.
As this technology continues to evolve, more industries are exploring its potential benefits and innovative uses.
TIP: Download the Meltio Applications catalog!
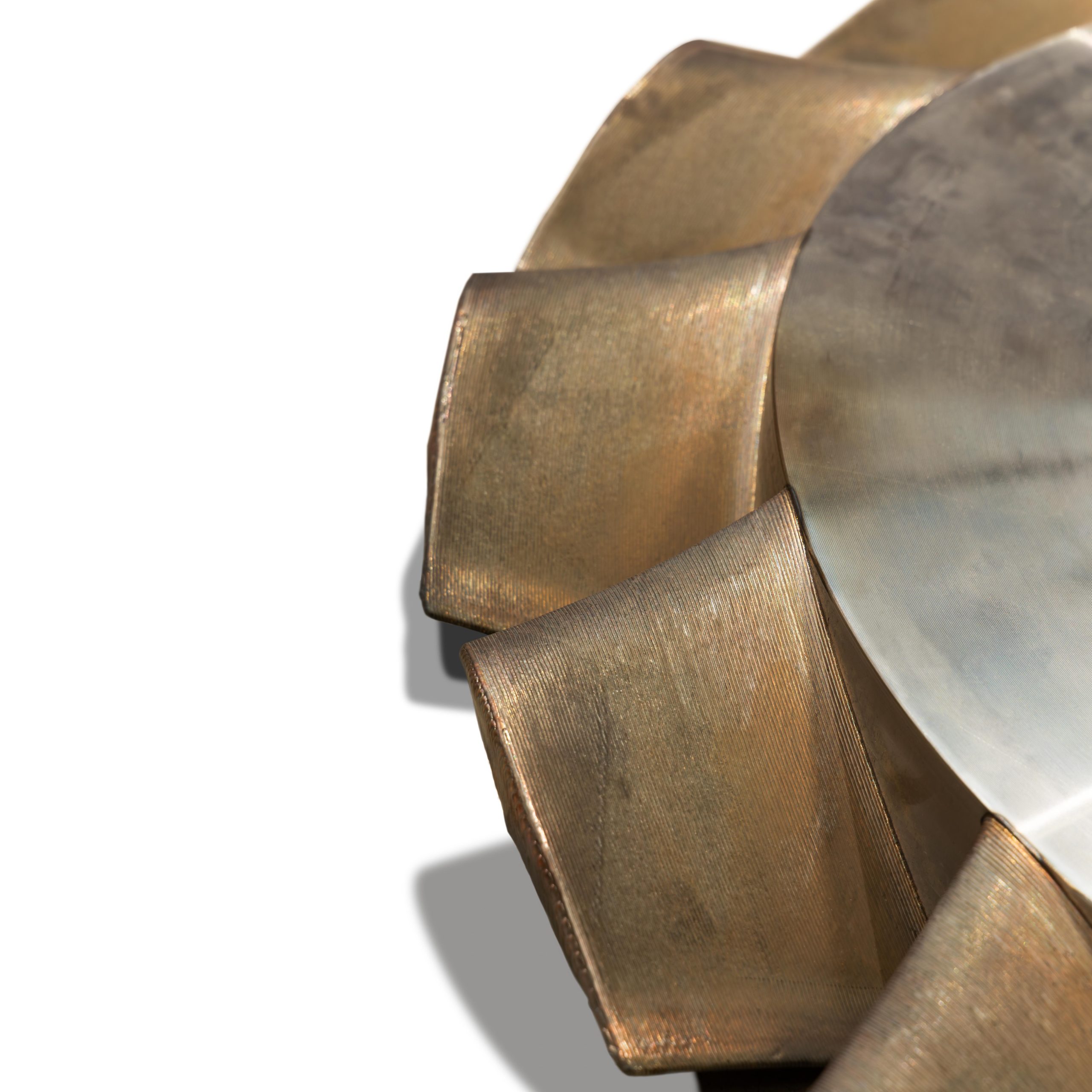
8. Conclusion
In summary, Directed Energy Deposition (DED) and more specifically Meltio’s wire-laser 3D printing technology represents the future of additive manufacturing due to its versatility, cost-effectiveness, and unique capabilities.
By combining laser-based precision with the ability to use wire materials, Meltio WLM-DED enables the creation of high-quality, complex components with reduced waste and material costs. Its compatibility with a variety of metals, ease of integration into existing production environments, and ability to produce both small and large-scale parts make it ideal for industries ranging from aerospace to automotive and beyond. Furthermore, its potential for repair and maintenance applications, alongside scalability and efficiency, positions Meltio DED as a transformative technology poised to redefine manufacturing standards and drive innovation.