Upgrading an anti-cavitation valve
with additive manufacturing
Use case developed by Meltio
Upgrading an anti-cavitation valve
with additive manufacturing
Use case developed by Meltio
This use case presents an internal study of an Anti-Cavitation Valve, using metal additive manufacturing with Meltio’s technology. The traditional manufacturing method for a part like this typically involves multiple complex processes, such as casting and machining from solid blocks.
The results show that manufacturing with Meltio offers substantial reductions in production steps, costs, and lead times.
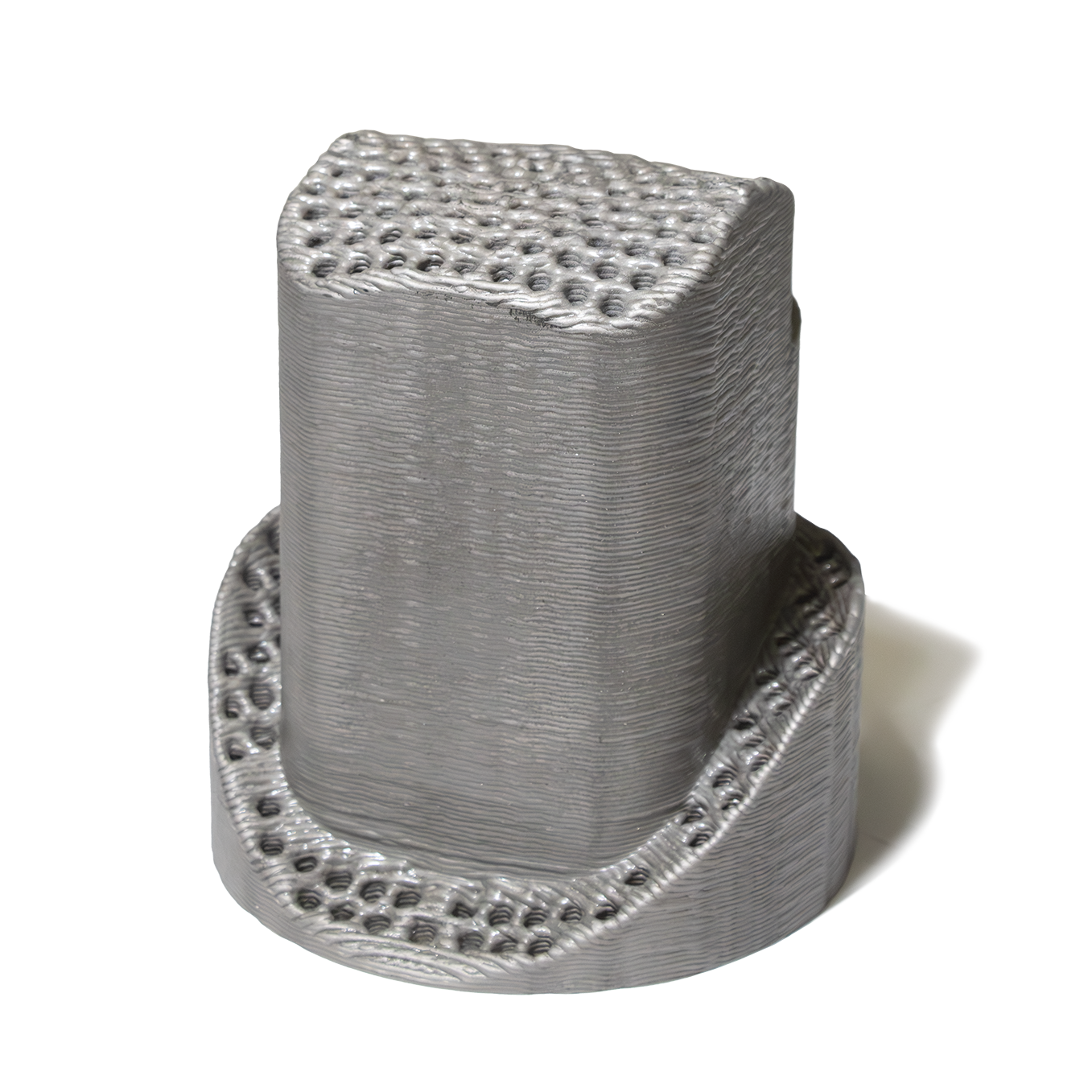
Preventing cavitation in harsh flow environments
An Anti-Cavitation Valve is a critical flow-control component engineered to prevent cavitation damage in fluid-handling systems. Cavitation, caused by vapor bubble formation and collapse due to low inlet pressure, can significantly reduce system performance and lead to part failure.
This valve is typically deployed in environments with corrosive fluids, high flow velocities, and variable pressure conditions, such as water treatment plants, chemical processing facilities, and power generation systems.
Designed for additive from the inside out
Traditionally manufactured through casting, machining, welding, and post-processing, this part demands complex internal geometries to manage fluid dynamics and resist cavitation. These internal features are hard to achieve without extensive tooling and assembly.
Using Meltio’s wire-laser metal 3D printing system, the component was redesigned for additive, featuring a honeycomb-shaped internal structure that enhances flow while eliminating the need for internal supports or secondary machining. The result: a more efficient design, fewer production steps, and faster delivery.

Advanced robotic metal 3D printing solutions
This application demonstrates how additive manufacturing not only enables internal features that would be impossible to machine, but also drastically reduces production time and manual labor. No welding, no assembly, and no internal post-processing were required.
Scenario | Material | Gas | Electricity | Total Cost |
---|---|---|---|---|
Bottle Gas (3.5 €/m³) | 221.38 € | 161.87 € | 61.67 € | 444.91 € |
Liquified Gas (2.38 €/m³) | 221.38 € | 110.07 € | 61.67 € | 393.11 € |
Optimized internal geometry for anti-cavitation
Corrosion-resistant and durable (SS316LSi)
No internal supports or welding
Faster production, lower cost
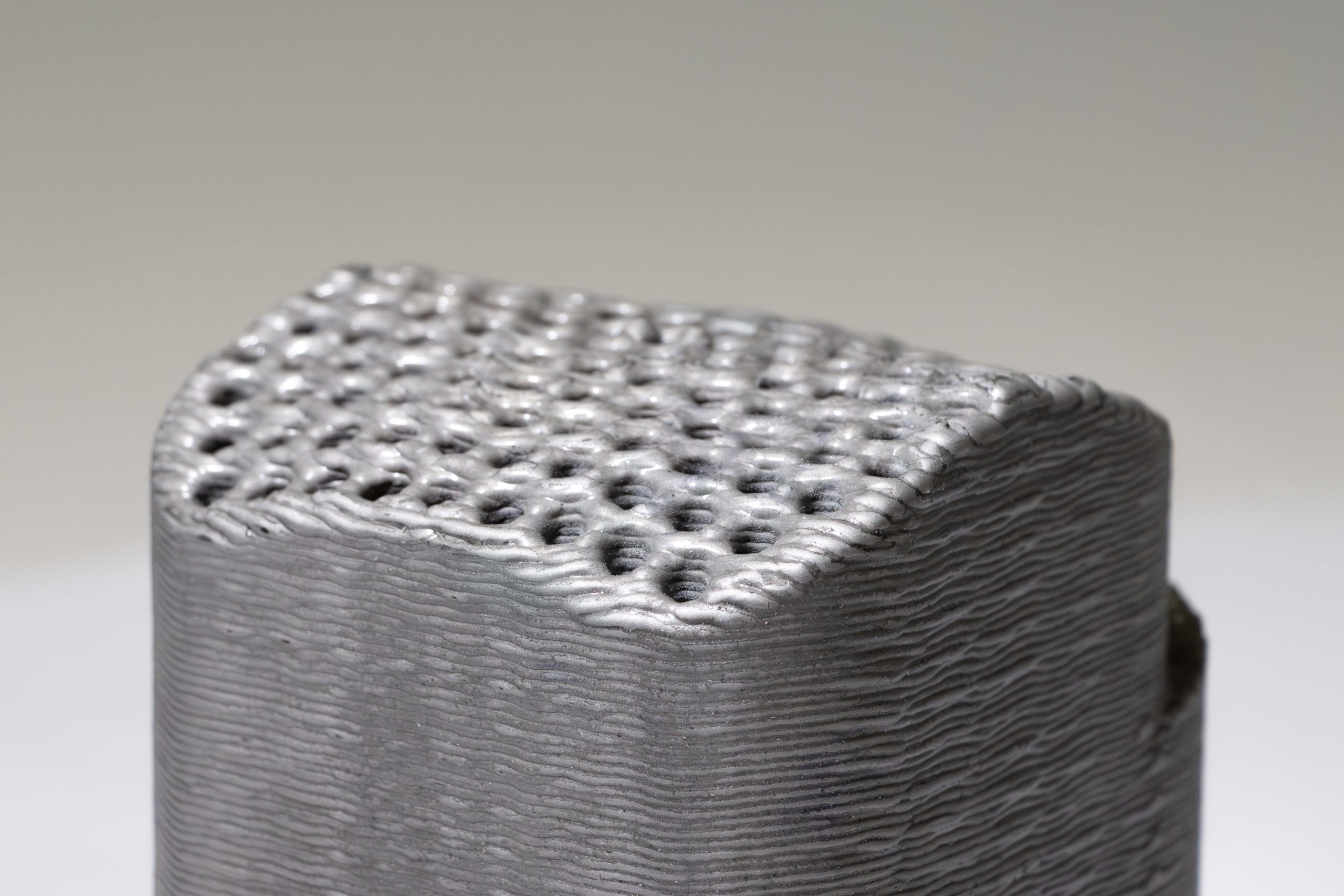
Meltio 3D Printing Solutions
Unlock the potential of metal 3D printing with Meltio. Your journey starts here.
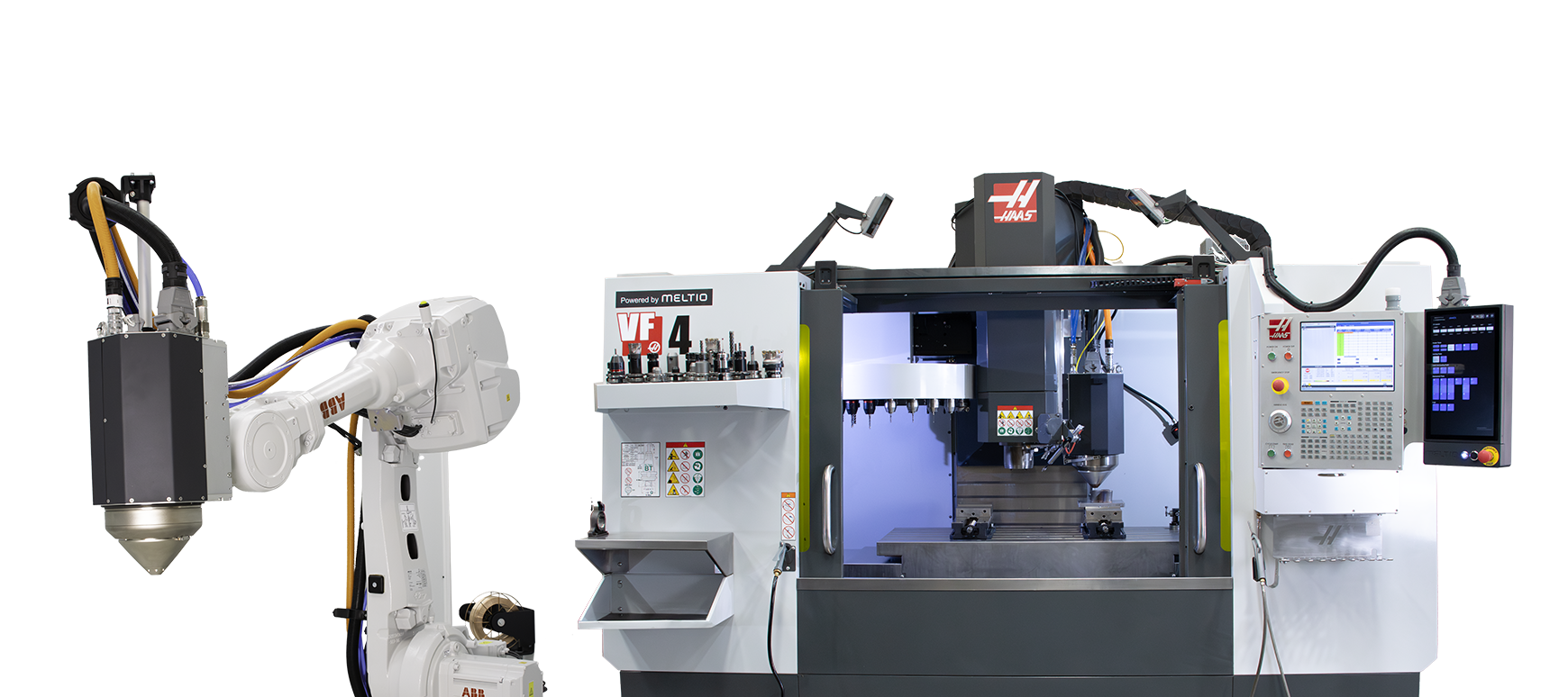
Meltio 3D Printing Solutions
Unlock the potential of metal 3D printing with Meltio. Your journey starts here.
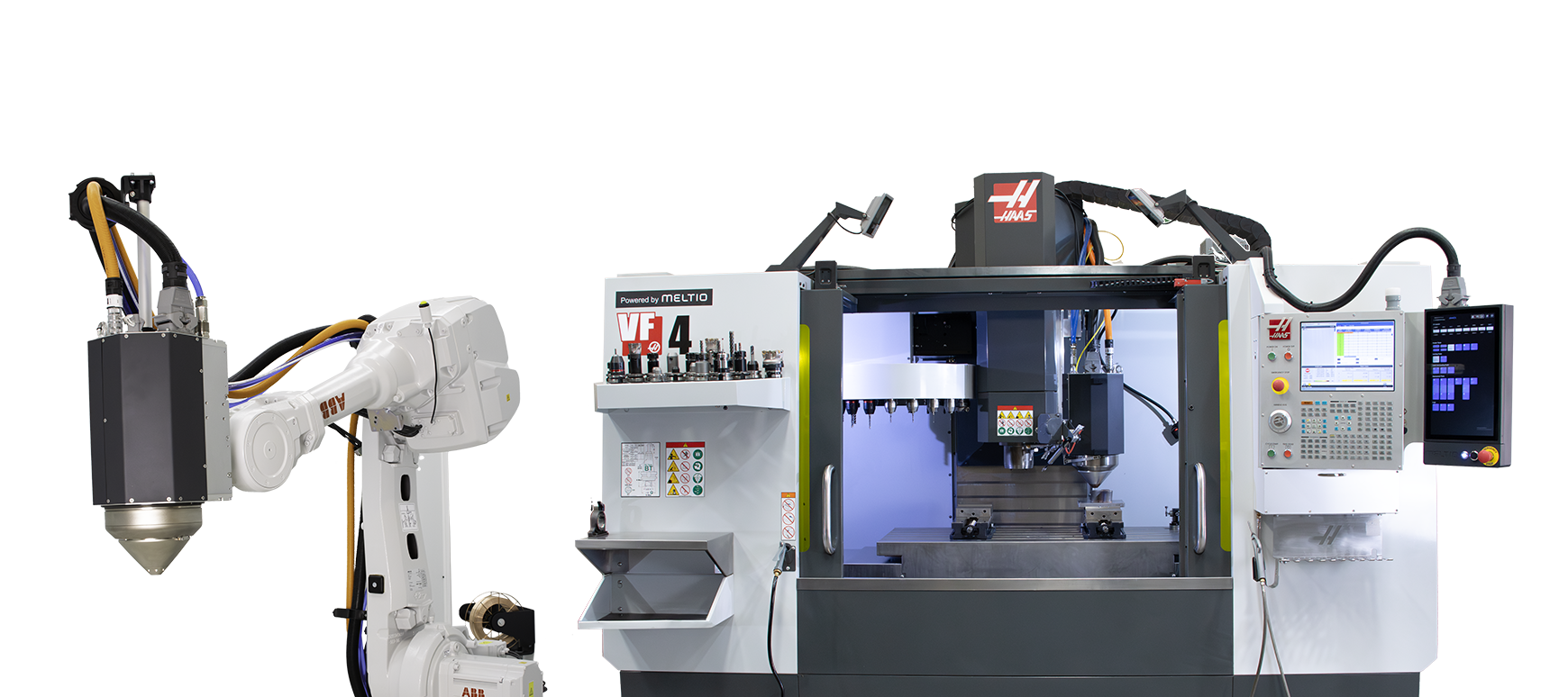
System: Meltio M600
Sector: Industrial
On-site, on-demand production
Material: Stainless Steel 316LSi
Wire feedstock proves more affordable and safer than powder-based alternatives.
Printing Time: 51h
Size: 150 x 150 x 180 mm
Weight: 12.6 kg
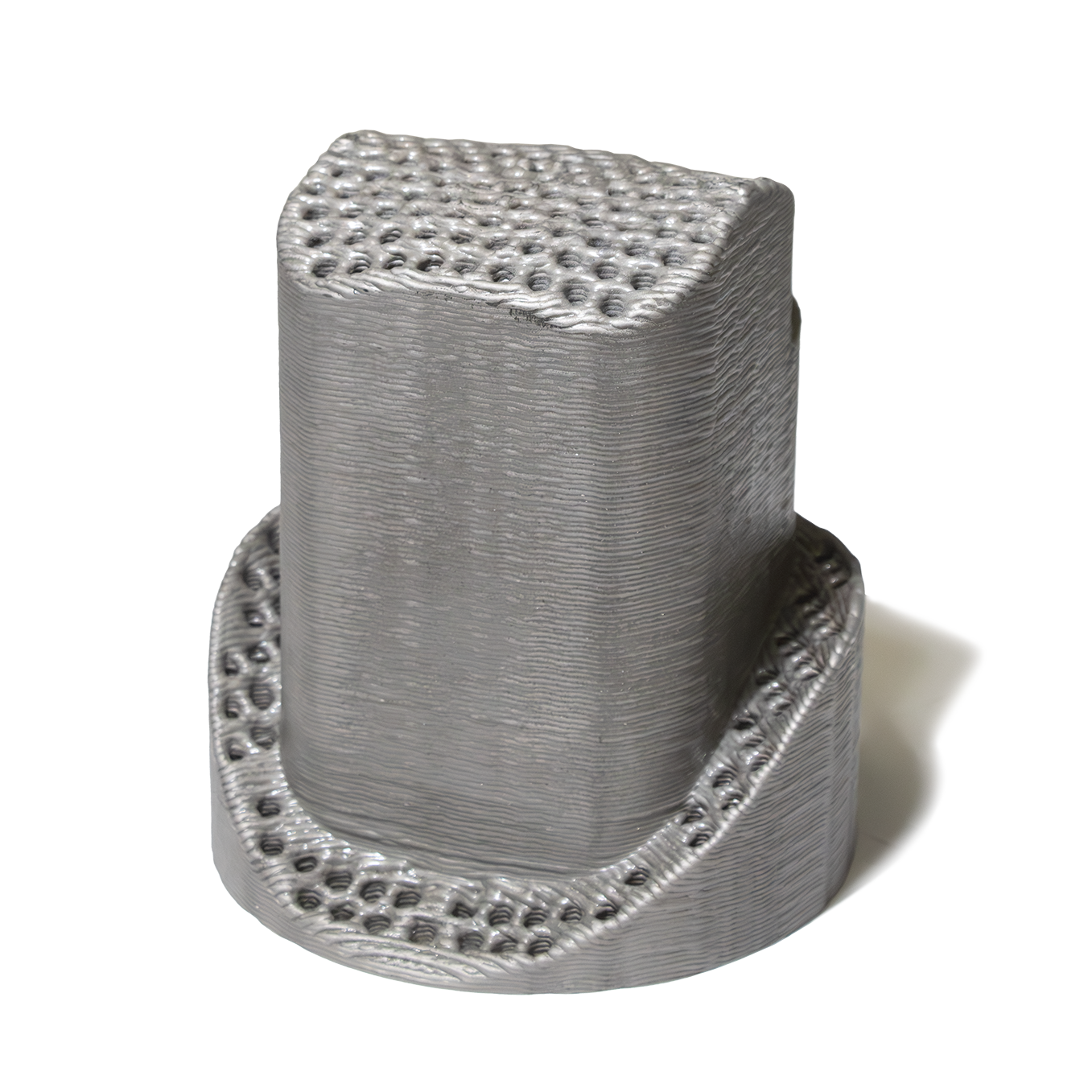
All about efficiency
Additive manufacturing with Meltio not only reduces cost and time, it also enables the creation of smarter, more resilient parts.
By extending this methodology to other components, Meltio reinforces a shift toward intelligent, flexible, and resource-efficient manufacturing.
Want to know more about printed parts properties?
Want to know more about printed parts properties?