Webinars
Explore all our webinars and discover all our possibilities!
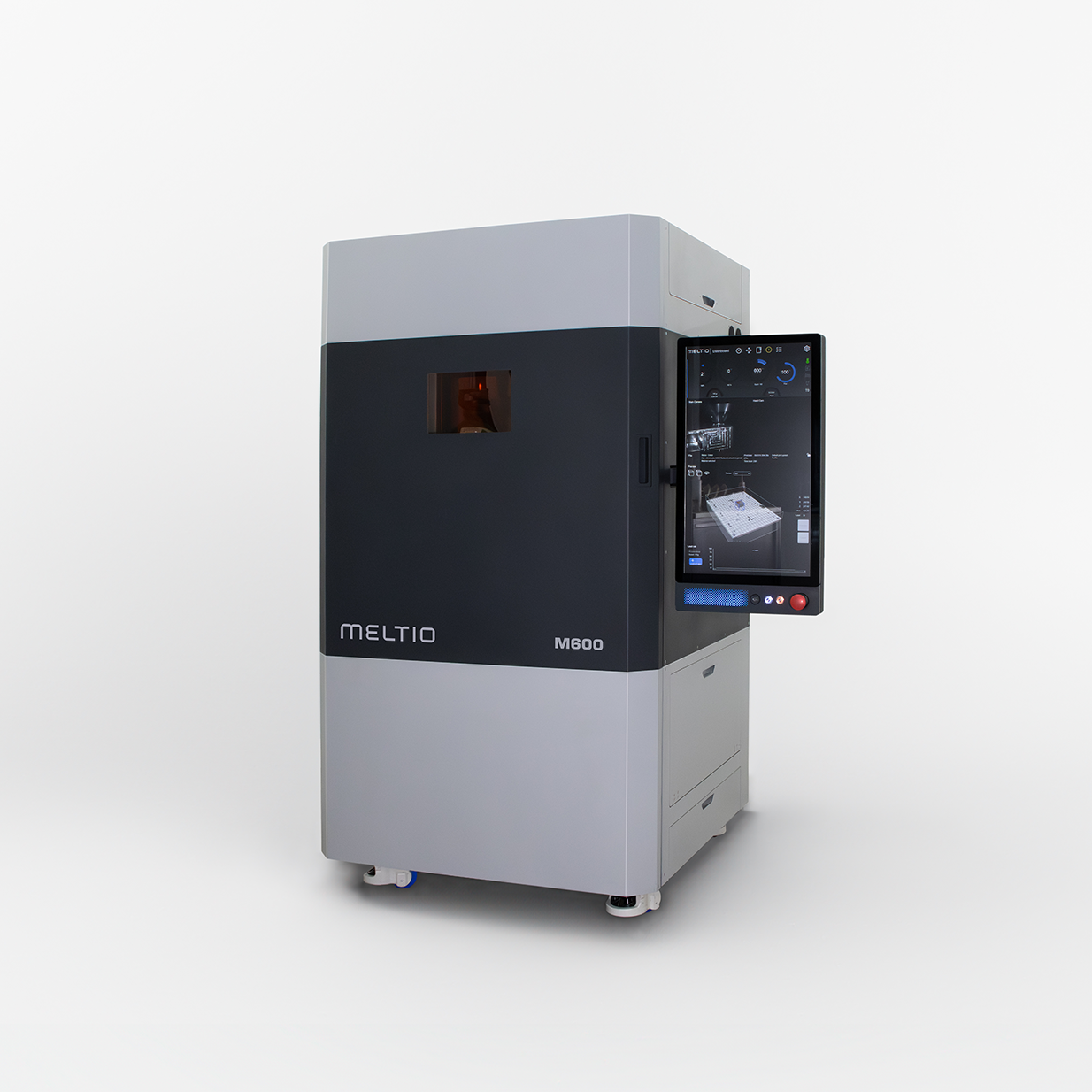
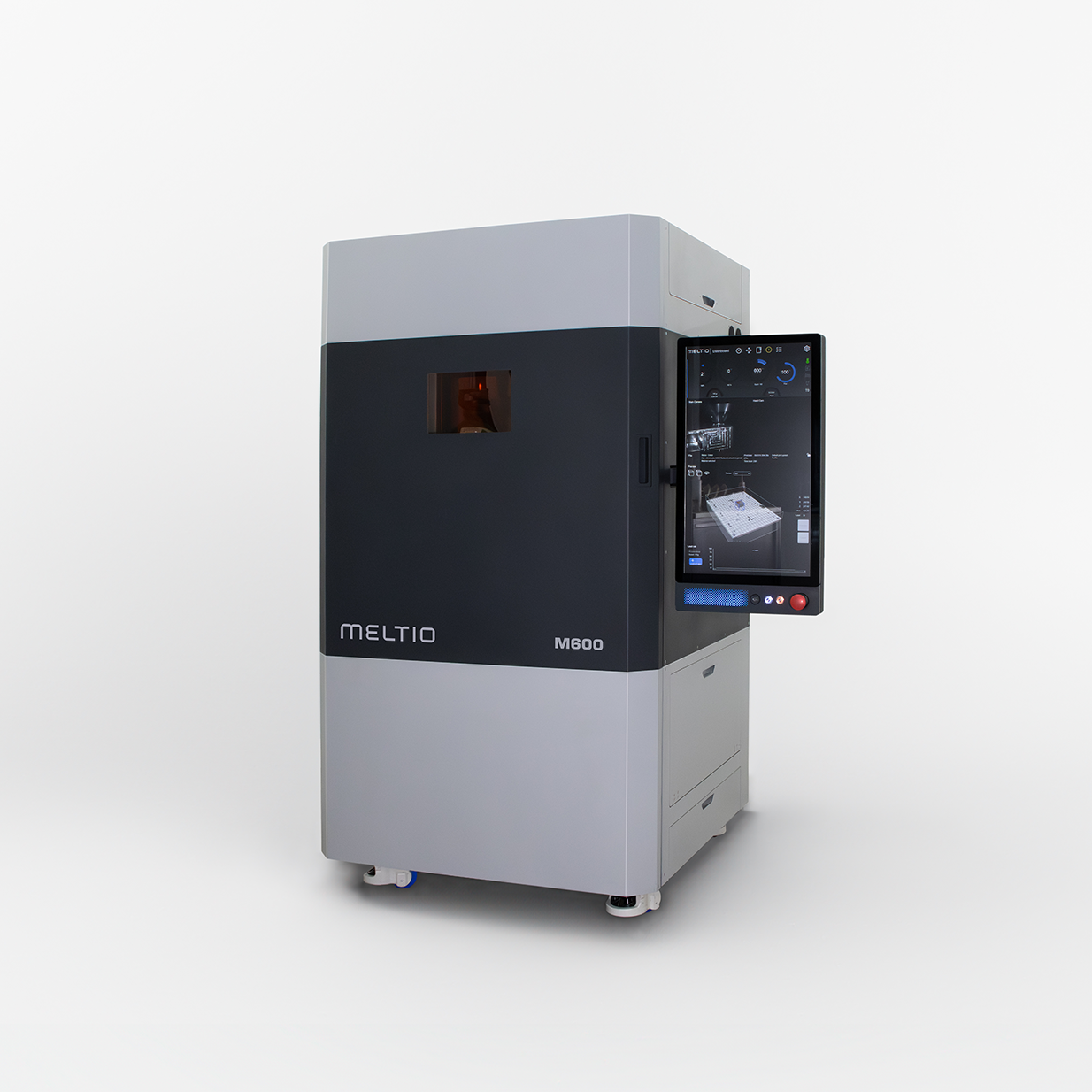
Keep up to date with our latest, webinars.
Guide
for Laser Wire
Deposition
Applications
Catalog
Guide
for Laser Wire
Deposition
Applications
Catalog
Not found application or sector?
How a French family business
is redefining metal manufacturing
Case study developed by Meltio
Improving an inert bubble
with optimized component production
Case study developed by Meltio
In the heart of Roubaix, northern France, a family-run company with over 60 years of machining excellence is reshaping the future of industrial metal fabrication. Gary Mécanique, founded in 1962, has long embraced technological advancement — from early CNC adoption in the 1970s to high-precision 5-axis machining today.
Now, in its latest evolution, the company is pioneering the use of robotic metal additive manufacturing with Meltio’s wire-laser DED technology — enabling the creation and repair of large, complex metal parts with unmatched flexibility and control.

A growing demand for complexity and speed
The industrial sectors Gary Mécanique serves — from defense and energy to automotive and aerospace — increasingly demand parts that are larger, more geometrically intricate, and faster to produce. Traditional processes like casting and welding come with high costs, long lead times, and rigidity in design. That’s where metal 3D printing, and specifically wire-laser DED, comes in.
“We wanted a solution that would allow us to produce large, custom parts internally — without the overhead of tooling, molds, or external delays. Meltio’s technology, combined with robotic freedom, gave us exactly that.”
To remain competitive and future-ready, Gary Mécanique needed a solution that would allow:
- Large-format part production without traditional casting constraints.
- Precision near-net-shape fabrication to reduce machining steps.
- In-house, cost-effective repair and rework operations.
- Material and geometry versatility without extensive retooling.
Material versatility meets geometry freedom
The company adopted Meltio’s wire-laser DED technology by integrating the Meltio Engine with a 6-axis Fanuc robot and a custom 2-axis positioner, allowing up to 8 degrees of freedom. This setup enables printing in 3-axis, 5-axis positioned, and 5-axis continuous modes — ideal for parts with complex geometries.
Materials: Compatible with various wires, including 316L stainless steel and ER70S6 steel.
Capability: Parts up to 2 meters in diameter and 2 tons in weight.
Versatility: Enables full part production, hybrid manufacturing, and component repair.
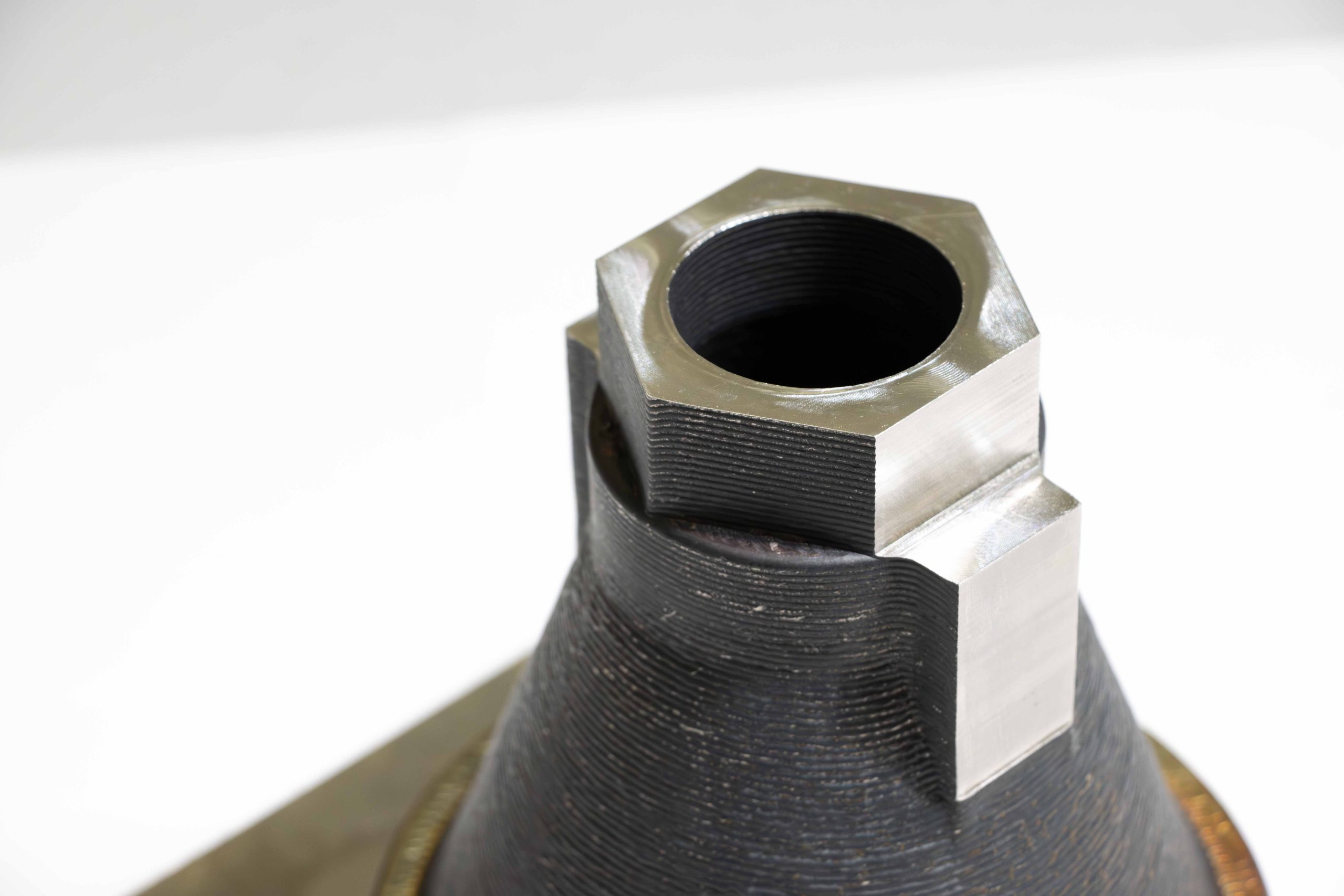
Meltio’s wire-laser technology (WLAM) allows the use of readily available, clean metal wire — from 316L stainless steel and ER70S6 steel to Inconel and even titanium or gold. Gary Mécanique has been using this to produce parts previously deemed impractical or expensive to fabricate traditionally.
Maximum flexibility
Reduced waste
On-demand production
Improved efficiency
Verified quality
Multi-material
Meltio 3D Printing Solutions
Unlock the potential of metal 3D printing
with Meltio. Your journey starts here.

CAROL IGUAL LAS PIEZAS COMO SON DEL MISMO SISTEMA SE PUEDEN PONER LAS 3 EN UNA MISMA LÍNEA Y 3 COLUMNAS. PONER LA INFO COMO ESTÁ EN LA PÁGINA DE PRIMANTE 3D: NOMBRE, MATERIAL TIEMPO DE IMPRESION, TAMAÑO Y VENTAJAS
System: Meltio Engine for Robot arms
Printing is easier than ever thanks to the improved process control, advanced sensors and live monitoring allowing you to produce parts consistently 24/7.
Sector: Heavy Machinery
Meltio's technology enhances the manufacturing process, delivering robust, high-precision components with improved sustainability and cost-effectiveness.
Material: Stainless Steel 316L
Wire feedstock proves more affordable and safer than powder-based alternatives.
Printing Time: 18 hours
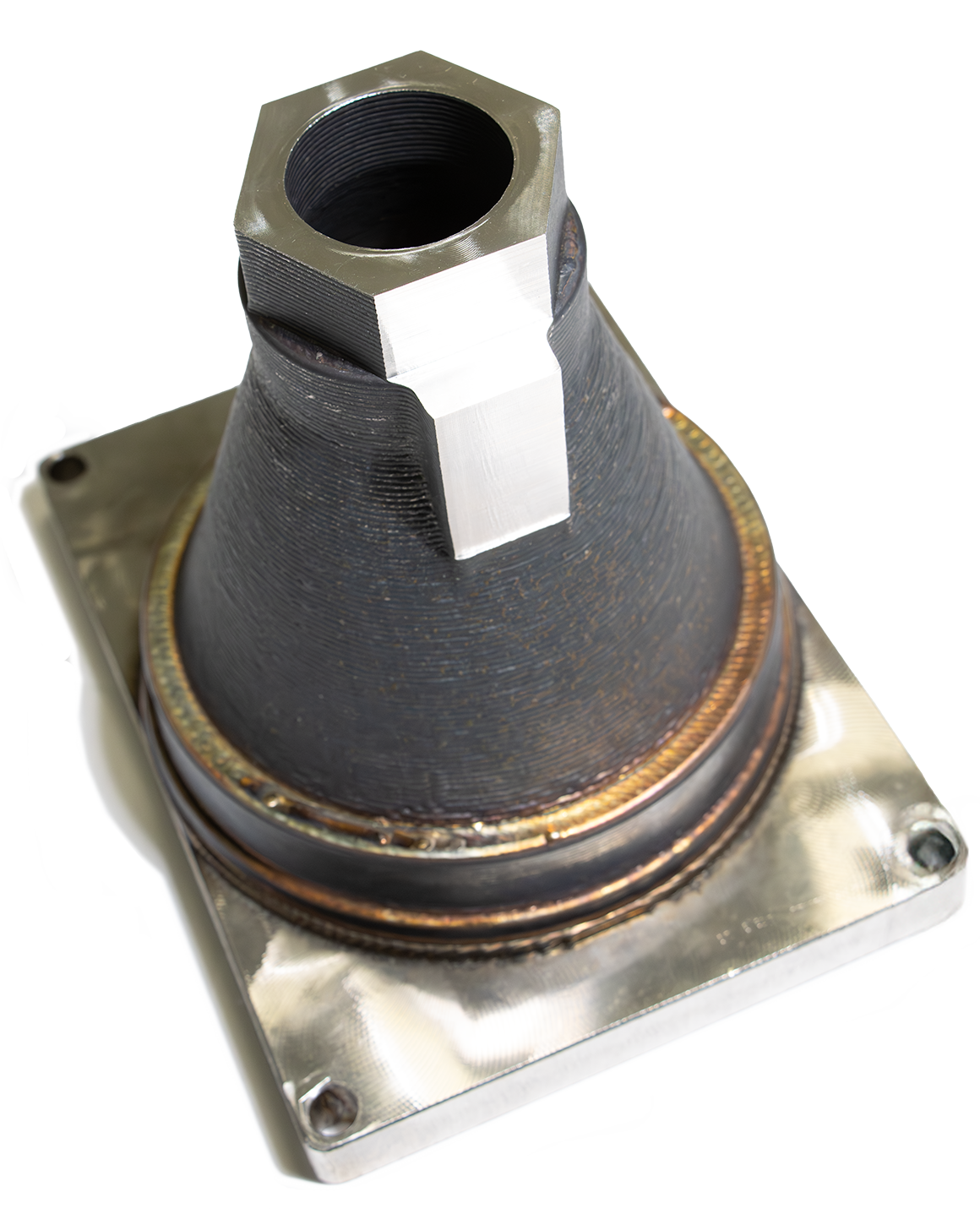
A part produced solely by additive manufacturing, it is easy to produce while allowing internal cooling and reduced mass.
System: Meltio Engine for Robot Arms
Printing is easier than ever thanks to the improved process control, advanced sensors and live monitoring allowing you to produce parts consistently 24/7.
Sector: Heavy Machinery
Meltio's technology enhances the manufacturing process, delivering robust, high-precision components with improved sustainability and cost-effectiveness.
Material: 316L Stainless Steel
Wire feedstock proves more affordable and safer than powder-based alternatives.
Printing Time: 8 hours
4h partial machining
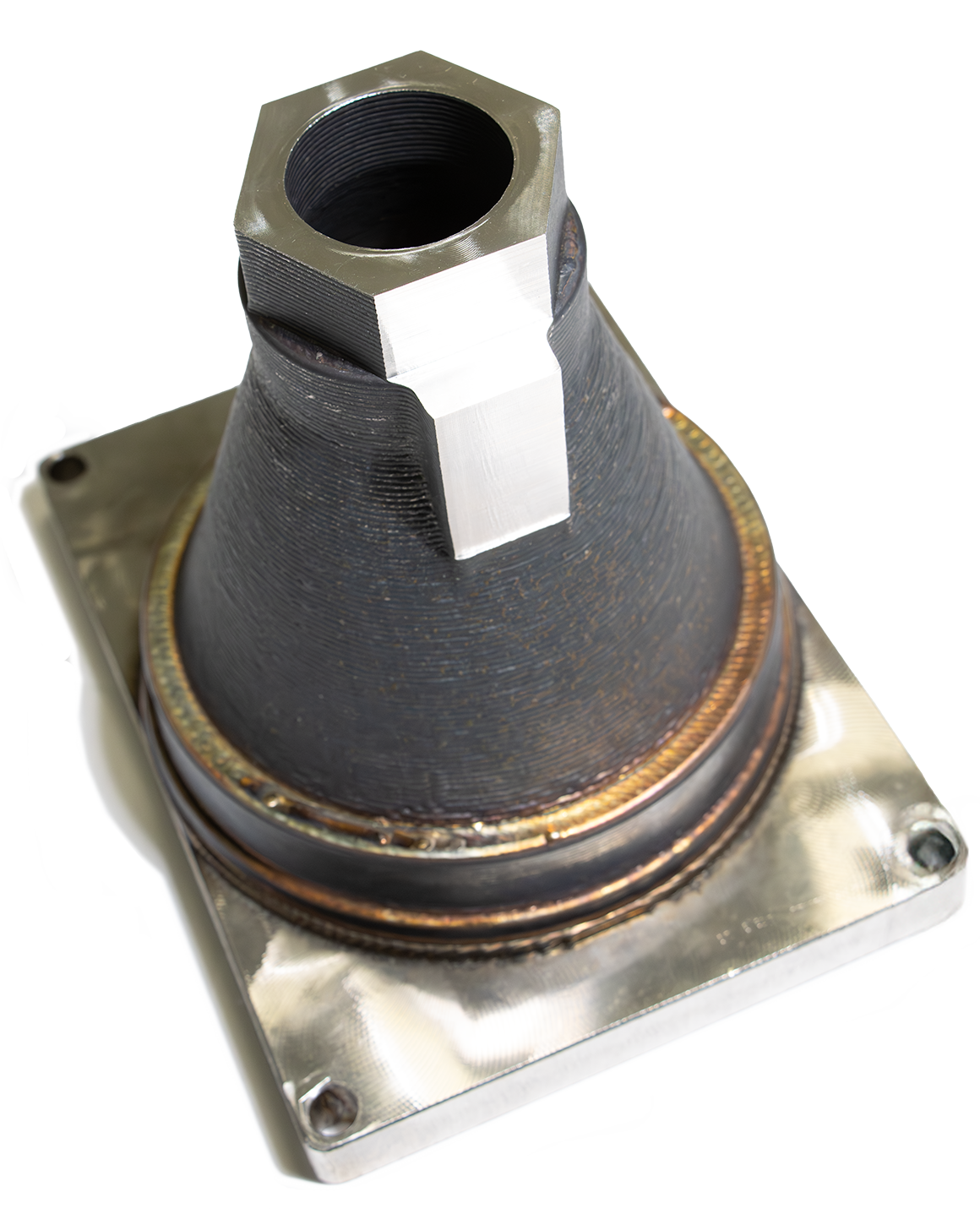
570mm propeller
System: Meltio M600
Sector: Heavy Machinery
Meltio's technology enhances the manufacturing process, delivering robust, high-precision components with improved sustainability and cost-effectiveness.
Material: 316L Stainless Steel
Wire feedstock proves more affordable and safer than powder-based alternatives.
Printing Time: 8 hours
4h partial machining
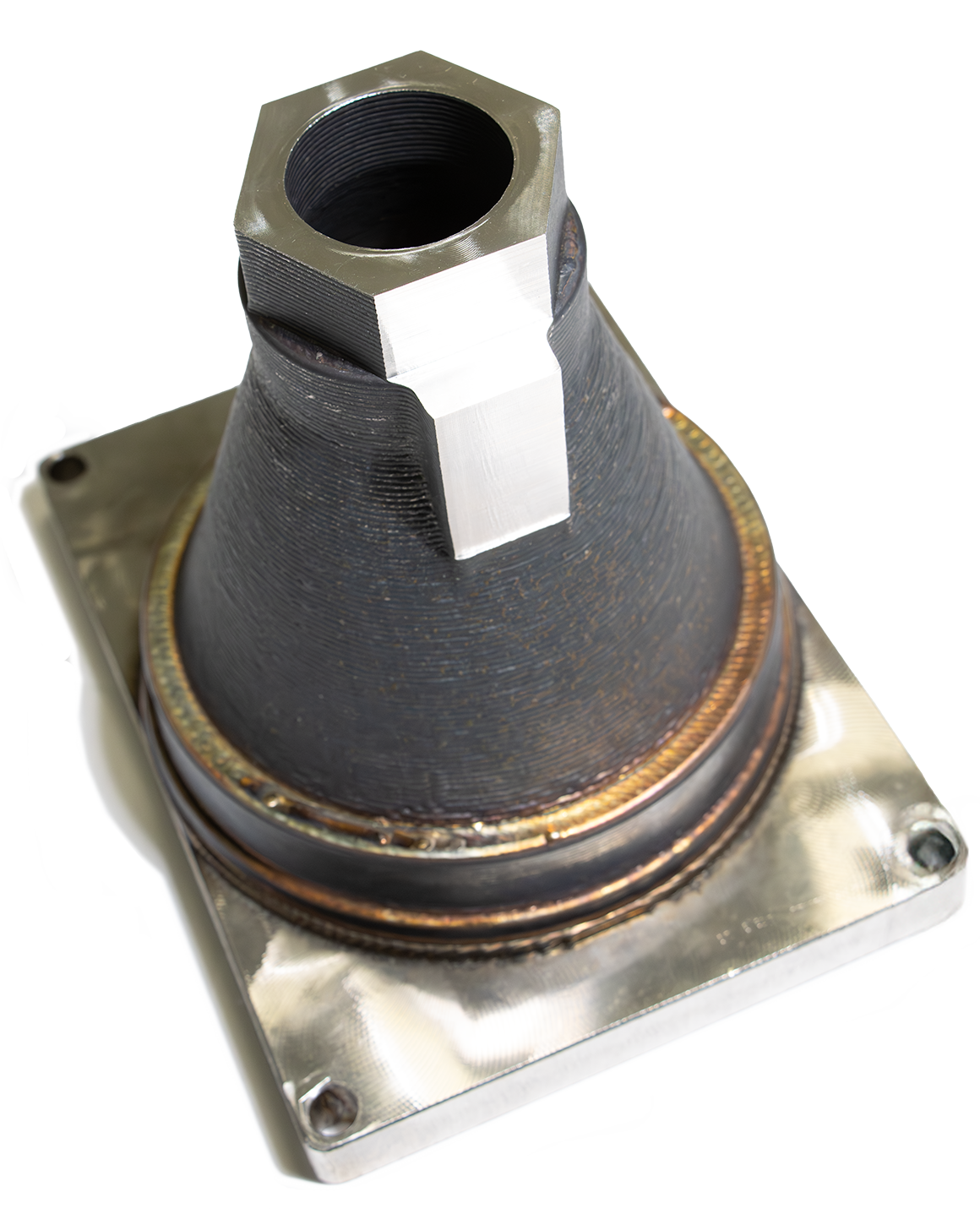
1-meter exhaust pipe
More than just manufacturing
One of the standout advantages for Gary Mécanique has been repair and rework. The Meltio setup allows existing parts to be reloaded into the machine for localized rebuilding — avoiding full remanufacturing. This not only cuts down cost and downtime but also contributes to a more sustainable production model.
And thanks to the near-net-shape capabilities of the DED process, machining time and material waste are significantly reduced.
“One common fear is mechanical strength,” says Justine. “But Meltio's technology undergoes rigorous testing — tensile, fatigue, tomography — ensuring the parts meet or exceed industrial requirements.”
A vision for the future
With Meltio’s wire-laser DED technology and robotic integration, Gary Mécanique has set a new benchmark for agility, precision, and scalability in metal manufacturing. The company continues to combine its traditional machining roots with cutting-edge innovation — delivering tailored, high-performance parts for a rapidly evolving industrial landscape.
“This isn’t just about technology — it’s about independence, flexibility, and pushing creative boundaries. Meltio is helping us make that possible.”
Want to know more about printed parts properties?
How a French family business
is redefining metal manufacturing
Case study developed by Meltio
Improving an inert bubble
with optimized component production
Case study developed by Meltio
In the heart of Roubaix, northern France, a family-run company with over 60 years of machining excellence is reshaping the future of industrial metal fabrication. Gary Mécanique, founded in 1962, has long embraced technological advancement — from early CNC adoption in the 1970s to high-precision 5-axis machining today.
Now, in its latest evolution, the company is pioneering the use of robotic metal additive manufacturing with Meltio’s wire-laser DED technology — enabling the creation and repair of large, complex metal parts with unmatched flexibility and control.

A growing demand for complexity and speed
The industrial sectors Gary Mécanique serves — from defense and energy to automotive and aerospace — increasingly demand parts that are larger, more geometrically intricate, and faster to produce. Traditional processes like casting and welding come with high costs, long lead times, and rigidity in design. That’s where metal 3D printing, and specifically wire-laser DED, comes in.
“We wanted a solution that would allow us to produce large, custom parts internally — without the overhead of tooling, molds, or external delays. Meltio’s technology, combined with robotic freedom, gave us exactly that.”
To remain competitive and future-ready, Gary Mécanique needed a solution that would allow:
- Large-format part production without traditional casting constraints.
- Precision near-net-shape fabrication to reduce machining steps.
- In-house, cost-effective repair and rework operations.
- Material and geometry versatility without extensive retooling.
Material versatility meets geometry freedom
The company adopted Meltio’s wire-laser DED technology by integrating the Meltio Engine with a 6-axis Fanuc robot and a custom 2-axis positioner, allowing up to 8 degrees of freedom. This setup enables printing in 3-axis, 5-axis positioned, and 5-axis continuous modes — ideal for parts with complex geometries.
Materials: Compatible with various wires, including 316L stainless steel and ER70S6 steel.
Capability: Parts up to 2 meters in diameter and 2 tons in weight.
Versatility: Enables full part production, hybrid manufacturing, and component repair.
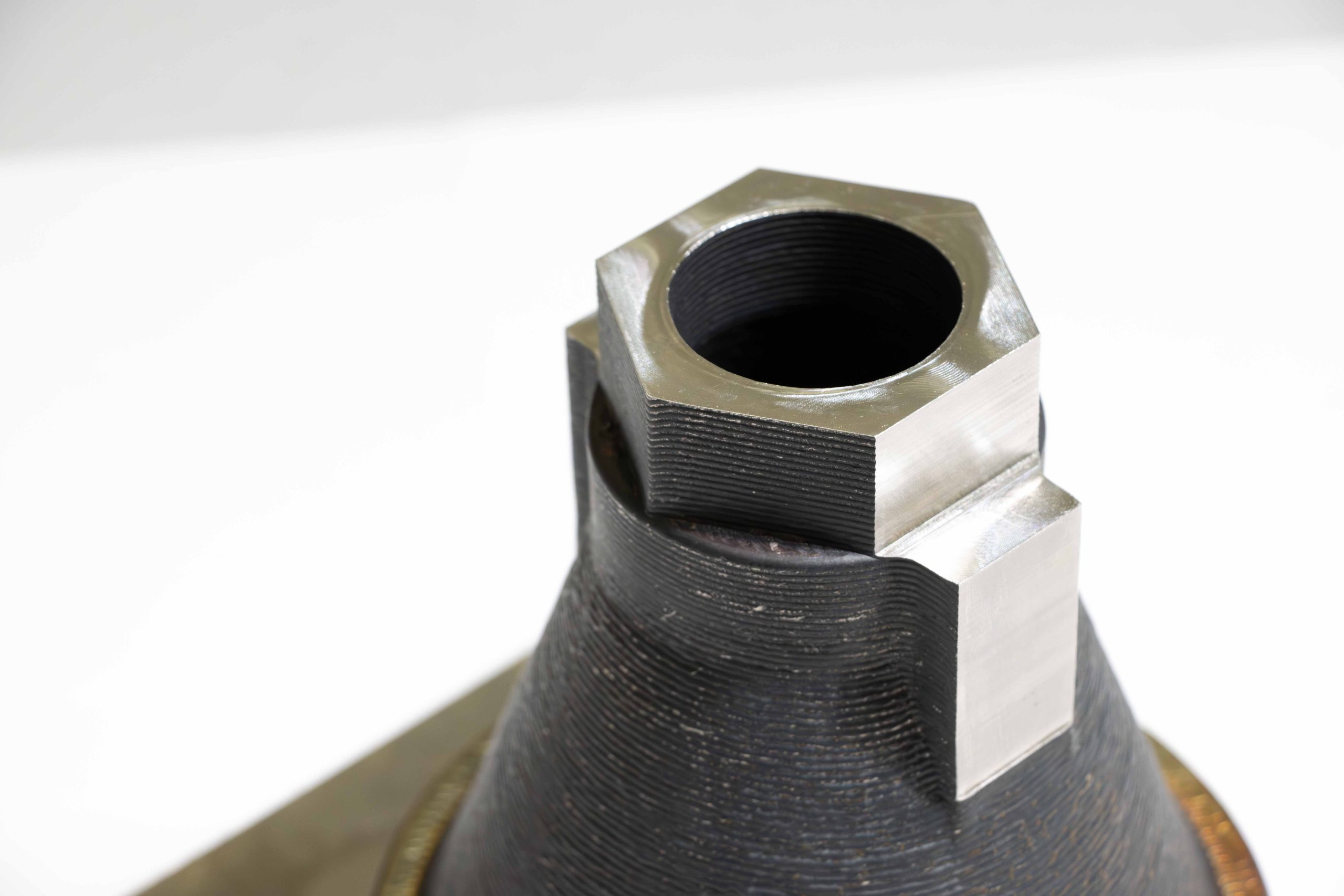
Meltio’s wire-laser technology (WLAM) allows the use of readily available, clean metal wire — from 316L stainless steel and ER70S6 steel to Inconel and even titanium or gold. Gary Mécanique has been using this to produce parts previously deemed impractical or expensive to fabricate traditionally.
Maximum flexibility
Reduced waste
On-demand production
Improved efficiency
Verified quality
Multi-material
Meltio 3D Printing Solutions
Unlock the potential of metal 3D printing
with Meltio. Your journey starts here.

CAROL IGUAL LAS PIEZAS COMO SON DEL MISMO SISTEMA SE PUEDEN PONER LAS 3 EN UNA MISMA LÍNEA Y 3 COLUMNAS. PONER LA INFO COMO ESTÁ EN LA PÁGINA DE PRIMANTE 3D: NOMBRE, MATERIAL TIEMPO DE IMPRESION, TAMAÑO Y VENTAJAS
System: Meltio Engine for Robot arms
Printing is easier than ever thanks to the improved process control, advanced sensors and live monitoring allowing you to produce parts consistently 24/7.
Sector: Heavy Machinery
Meltio's technology enhances the manufacturing process, delivering robust, high-precision components with improved sustainability and cost-effectiveness.
Material: Stainless Steel 316L
Wire feedstock proves more affordable and safer than powder-based alternatives.
Printing Time: 18 hours
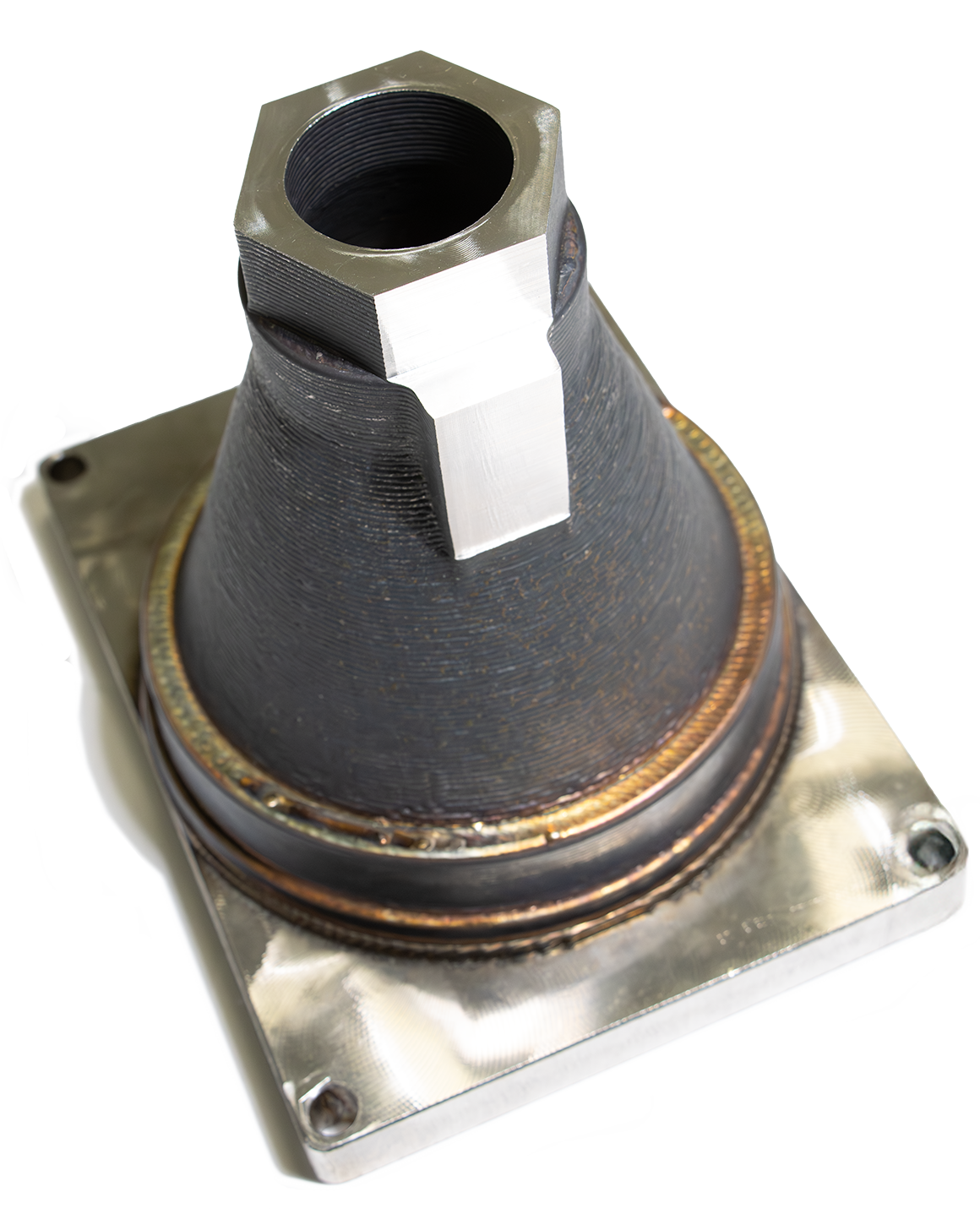
A part produced solely by additive manufacturing, it is easy to produce while allowing internal cooling and reduced mass.
System: Meltio Engine for Robot Arms
Printing is easier than ever thanks to the improved process control, advanced sensors and live monitoring allowing you to produce parts consistently 24/7.
Sector: Heavy Machinery
Meltio's technology enhances the manufacturing process, delivering robust, high-precision components with improved sustainability and cost-effectiveness.
Material: 316L Stainless Steel
Wire feedstock proves more affordable and safer than powder-based alternatives.
Printing Time: 8 hours
4h partial machining
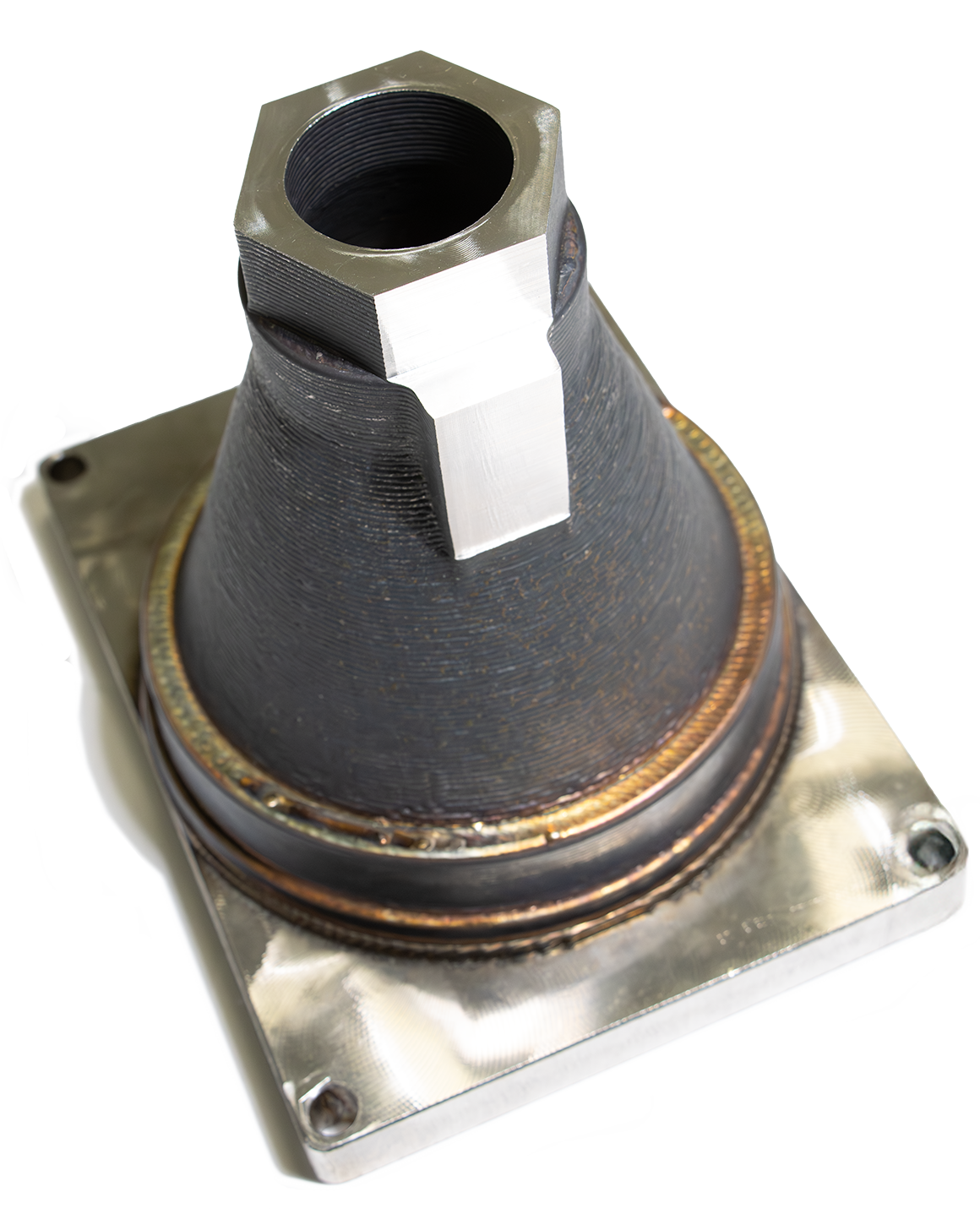
570mm propeller
System: Meltio M600
Sector: Heavy Machinery
Meltio's technology enhances the manufacturing process, delivering robust, high-precision components with improved sustainability and cost-effectiveness.
Material: 316L Stainless Steel
Wire feedstock proves more affordable and safer than powder-based alternatives.
Printing Time: 8 hours
4h partial machining
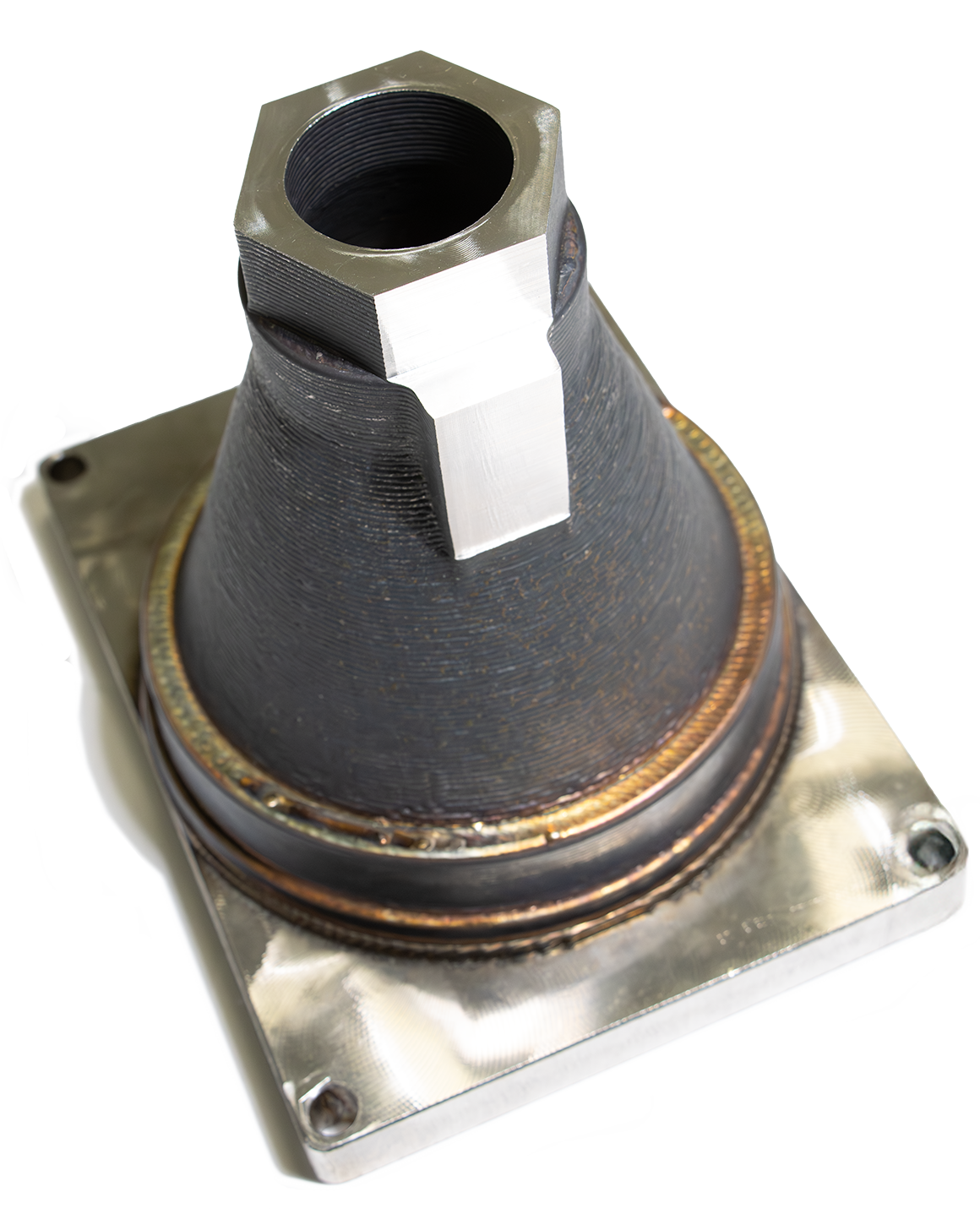
1-meter exhaust pipe
More than just manufacturing
One of the standout advantages for Gary Mécanique has been repair and rework. The Meltio setup allows existing parts to be reloaded into the machine for localized rebuilding — avoiding full remanufacturing. This not only cuts down cost and downtime but also contributes to a more sustainable production model.
And thanks to the near-net-shape capabilities of the DED process, machining time and material waste are significantly reduced.
“One common fear is mechanical strength,” says Justine. “But Meltio's technology undergoes rigorous testing — tensile, fatigue, tomography — ensuring the parts meet or exceed industrial requirements.”
A vision for the future
With Meltio’s wire-laser DED technology and robotic integration, Gary Mécanique has set a new benchmark for agility, precision, and scalability in metal manufacturing. The company continues to combine its traditional machining roots with cutting-edge innovation — delivering tailored, high-performance parts for a rapidly evolving industrial landscape.
“This isn’t just about technology — it’s about independence, flexibility, and pushing creative boundaries. Meltio is helping us make that possible.”
Want to know more about printed parts properties?
How a French family business
is redefining metal manufacturing
Case study developed by Meltio
Improving an inert bubble
with optimized component production
Case study developed by Meltio
In the heart of Roubaix, northern France, a family-run company with over 60 years of machining excellence is reshaping the future of industrial metal fabrication. Gary Mécanique, founded in 1962, has long embraced technological advancement — from early CNC adoption in the 1970s to high-precision 5-axis machining today.
Now, in its latest evolution, the company is pioneering the use of robotic metal additive manufacturing with Meltio’s wire-laser DED technology — enabling the creation and repair of large, complex metal parts with unmatched flexibility and control.

A growing demand for complexity and speed
The industrial sectors Gary Mécanique serves — from defense and energy to automotive and aerospace — increasingly demand parts that are larger, more geometrically intricate, and faster to produce. Traditional processes like casting and welding come with high costs, long lead times, and rigidity in design. That’s where metal 3D printing, and specifically wire-laser DED, comes in.
“We wanted a solution that would allow us to produce large, custom parts internally — without the overhead of tooling, molds, or external delays. Meltio’s technology, combined with robotic freedom, gave us exactly that.”
To remain competitive and future-ready, Gary Mécanique needed a solution that would allow:
- Large-format part production without traditional casting constraints.
- Precision near-net-shape fabrication to reduce machining steps.
- In-house, cost-effective repair and rework operations.
- Material and geometry versatility without extensive retooling.
Material versatility meets geometry freedom
The company adopted Meltio’s wire-laser DED technology by integrating the Meltio Engine with a 6-axis Fanuc robot and a custom 2-axis positioner, allowing up to 8 degrees of freedom. This setup enables printing in 3-axis, 5-axis positioned, and 5-axis continuous modes — ideal for parts with complex geometries.
Materials: Compatible with various wires, including 316L stainless steel and ER70S6 steel.
Capability: Parts up to 2 meters in diameter and 2 tons in weight.
Versatility: Enables full part production, hybrid manufacturing, and component repair.
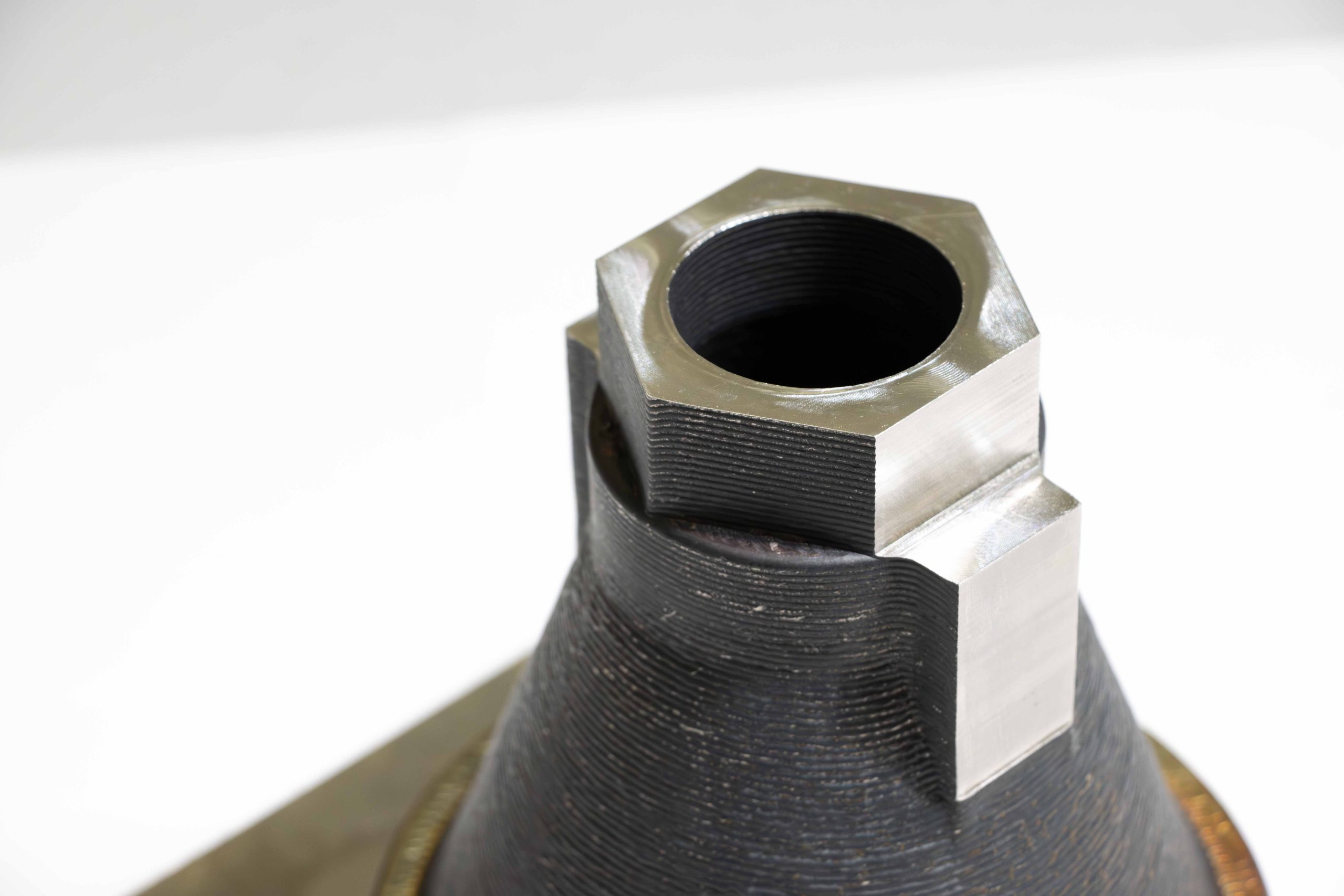
Meltio’s wire-laser technology (WLAM) allows the use of readily available, clean metal wire — from 316L stainless steel and ER70S6 steel to Inconel and even titanium or gold. Gary Mécanique has been using this to produce parts previously deemed impractical or expensive to fabricate traditionally.
Maximum flexibility
Reduced waste
On-demand production
Improved efficiency
Verified quality
Multi-material
Meltio 3D Printing Solutions
Unlock the potential of metal 3D printing
with Meltio. Your journey starts here.

CAROL IGUAL LAS PIEZAS COMO SON DEL MISMO SISTEMA SE PUEDEN PONER LAS 3 EN UNA MISMA LÍNEA Y 3 COLUMNAS. PONER LA INFO COMO ESTÁ EN LA PÁGINA DE PRIMANTE 3D: NOMBRE, MATERIAL TIEMPO DE IMPRESION, TAMAÑO Y VENTAJAS
System: Meltio Engine for Robot arms
Printing is easier than ever thanks to the improved process control, advanced sensors and live monitoring allowing you to produce parts consistently 24/7.
Sector: Heavy Machinery
Meltio's technology enhances the manufacturing process, delivering robust, high-precision components with improved sustainability and cost-effectiveness.
Material: Stainless Steel 316L
Wire feedstock proves more affordable and safer than powder-based alternatives.
Printing Time: 18 hours
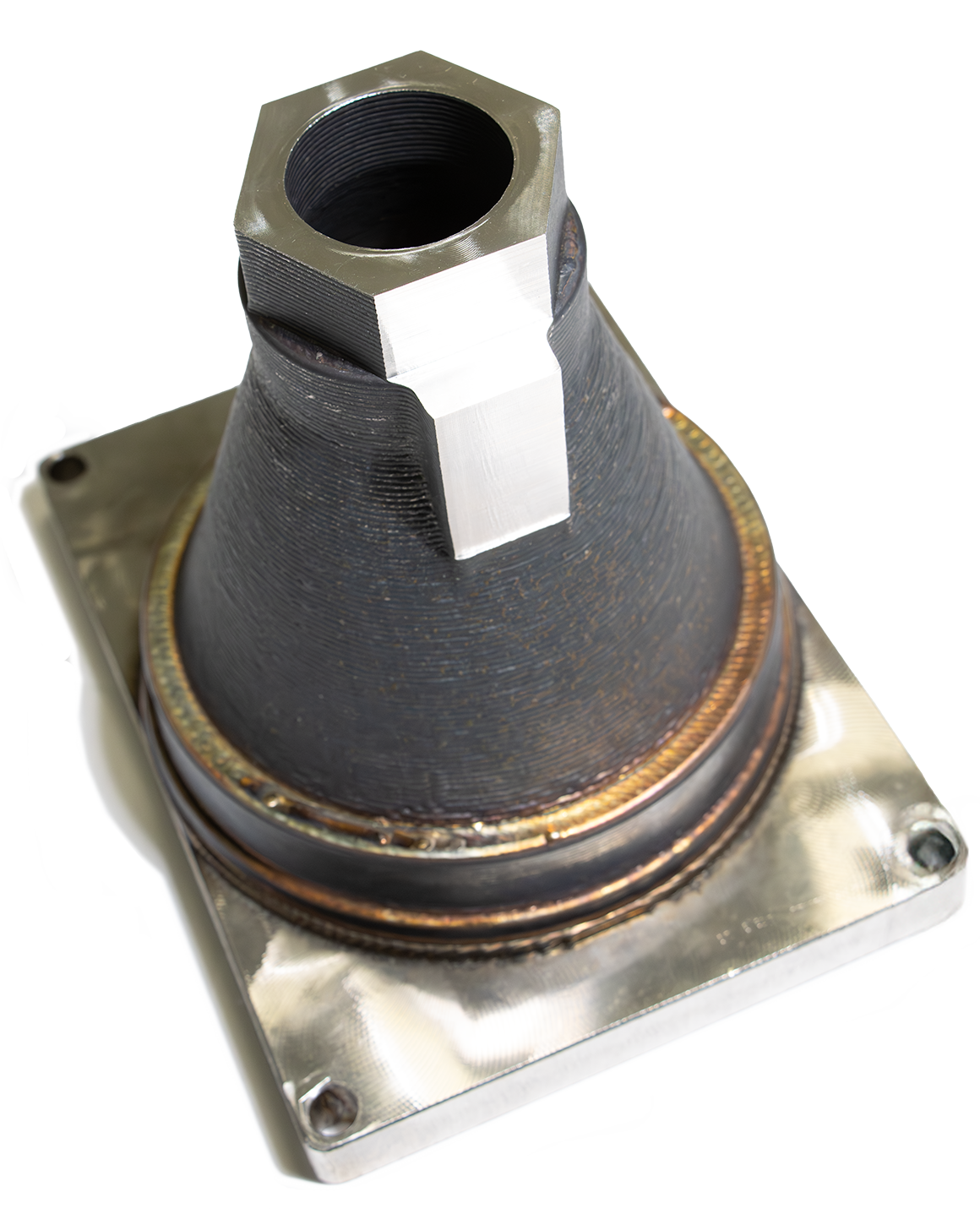
A part produced solely by additive manufacturing, it is easy to produce while allowing internal cooling and reduced mass.
System: Meltio Engine for Robot Arms
Printing is easier than ever thanks to the improved process control, advanced sensors and live monitoring allowing you to produce parts consistently 24/7.
Sector: Heavy Machinery
Meltio's technology enhances the manufacturing process, delivering robust, high-precision components with improved sustainability and cost-effectiveness.
Material: 316L Stainless Steel
Wire feedstock proves more affordable and safer than powder-based alternatives.
Printing Time: 8 hours
4h partial machining
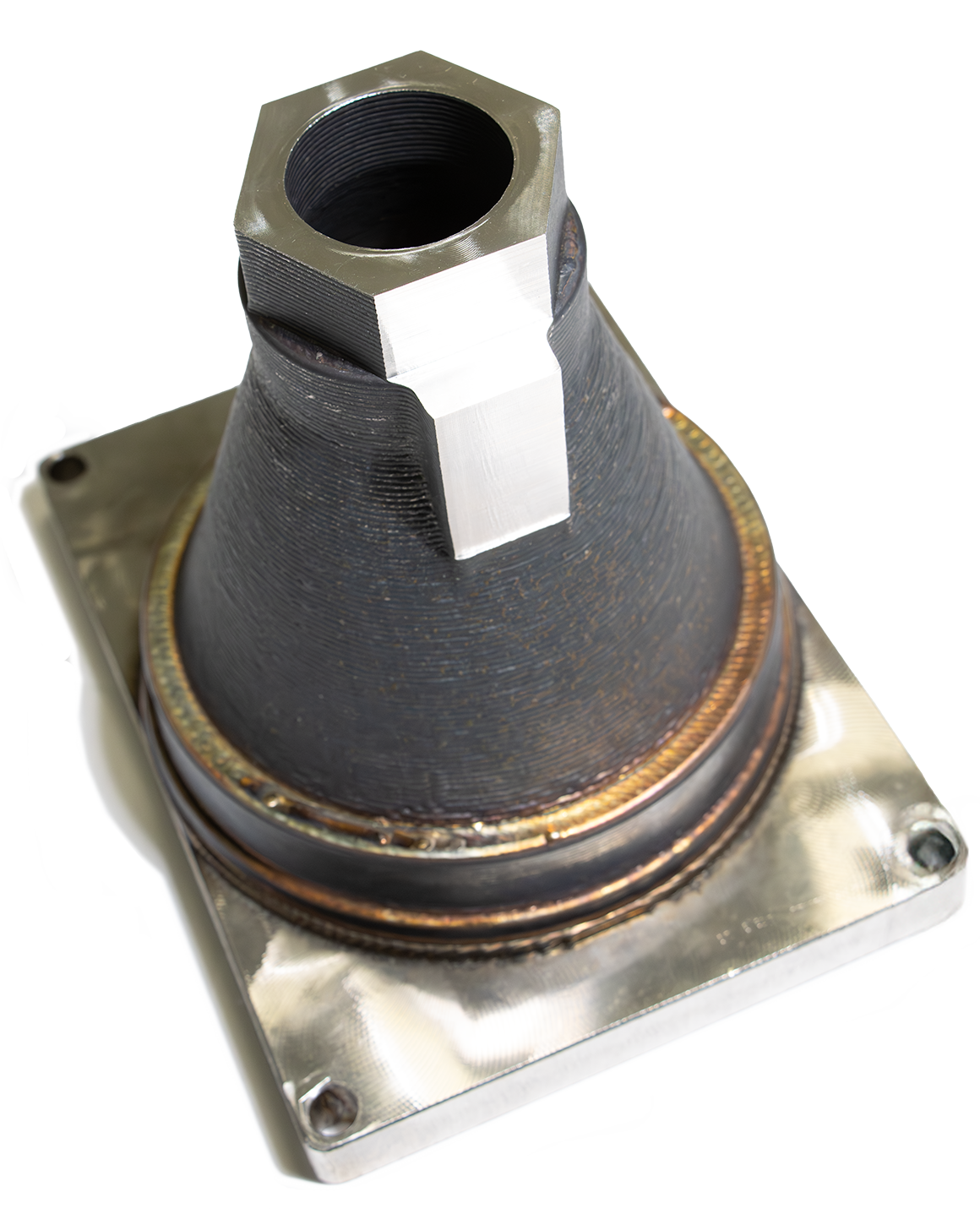
570mm propeller
System: Meltio M600
Sector: Heavy Machinery
Meltio's technology enhances the manufacturing process, delivering robust, high-precision components with improved sustainability and cost-effectiveness.
Material: 316L Stainless Steel
Wire feedstock proves more affordable and safer than powder-based alternatives.
Printing Time: 8 hours
4h partial machining
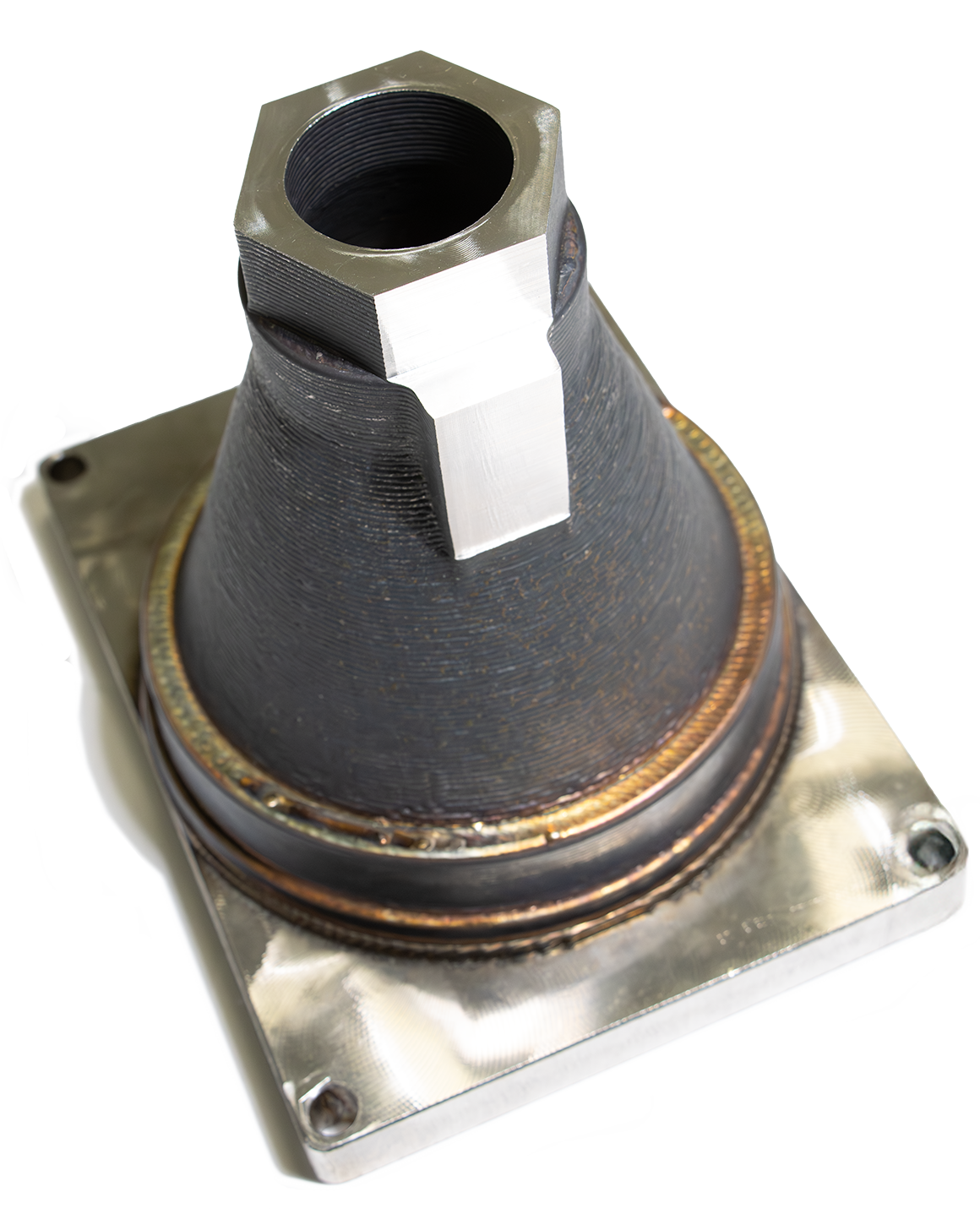
1-meter exhaust pipe
More than just manufacturing
One of the standout advantages for Gary Mécanique has been repair and rework. The Meltio setup allows existing parts to be reloaded into the machine for localized rebuilding — avoiding full remanufacturing. This not only cuts down cost and downtime but also contributes to a more sustainable production model.
And thanks to the near-net-shape capabilities of the DED process, machining time and material waste are significantly reduced.
“One common fear is mechanical strength,” says Justine. “But Meltio's technology undergoes rigorous testing — tensile, fatigue, tomography — ensuring the parts meet or exceed industrial requirements.”
A vision for the future
With Meltio’s wire-laser DED technology and robotic integration, Gary Mécanique has set a new benchmark for agility, precision, and scalability in metal manufacturing. The company continues to combine its traditional machining roots with cutting-edge innovation — delivering tailored, high-performance parts for a rapidly evolving industrial landscape.
“This isn’t just about technology — it’s about independence, flexibility, and pushing creative boundaries. Meltio is helping us make that possible.”
Want to know more about printed parts properties?
How a French family business
is redefining metal manufacturing
Case study developed by Meltio
Improving an inert bubble
with optimized component production
Case study developed by Meltio
In the heart of Roubaix, northern France, a family-run company with over 60 years of machining excellence is reshaping the future of industrial metal fabrication. Gary Mécanique, founded in 1962, has long embraced technological advancement — from early CNC adoption in the 1970s to high-precision 5-axis machining today.
Now, in its latest evolution, the company is pioneering the use of robotic metal additive manufacturing with Meltio’s wire-laser DED technology — enabling the creation and repair of large, complex metal parts with unmatched flexibility and control.

A growing demand for complexity and speed
The industrial sectors Gary Mécanique serves — from defense and energy to automotive and aerospace — increasingly demand parts that are larger, more geometrically intricate, and faster to produce. Traditional processes like casting and welding come with high costs, long lead times, and rigidity in design. That’s where metal 3D printing, and specifically wire-laser DED, comes in.
“We wanted a solution that would allow us to produce large, custom parts internally — without the overhead of tooling, molds, or external delays. Meltio’s technology, combined with robotic freedom, gave us exactly that.”
To remain competitive and future-ready, Gary Mécanique needed a solution that would allow:
- Large-format part production without traditional casting constraints.
- Precision near-net-shape fabrication to reduce machining steps.
- In-house, cost-effective repair and rework operations.
- Material and geometry versatility without extensive retooling.
Material versatility meets geometry freedom
The company adopted Meltio’s wire-laser DED technology by integrating the Meltio Engine with a 6-axis Fanuc robot and a custom 2-axis positioner, allowing up to 8 degrees of freedom. This setup enables printing in 3-axis, 5-axis positioned, and 5-axis continuous modes — ideal for parts with complex geometries.
Materials: Compatible with various wires, including 316L stainless steel and ER70S6 steel.
Capability: Parts up to 2 meters in diameter and 2 tons in weight.
Versatility: Enables full part production, hybrid manufacturing, and component repair.
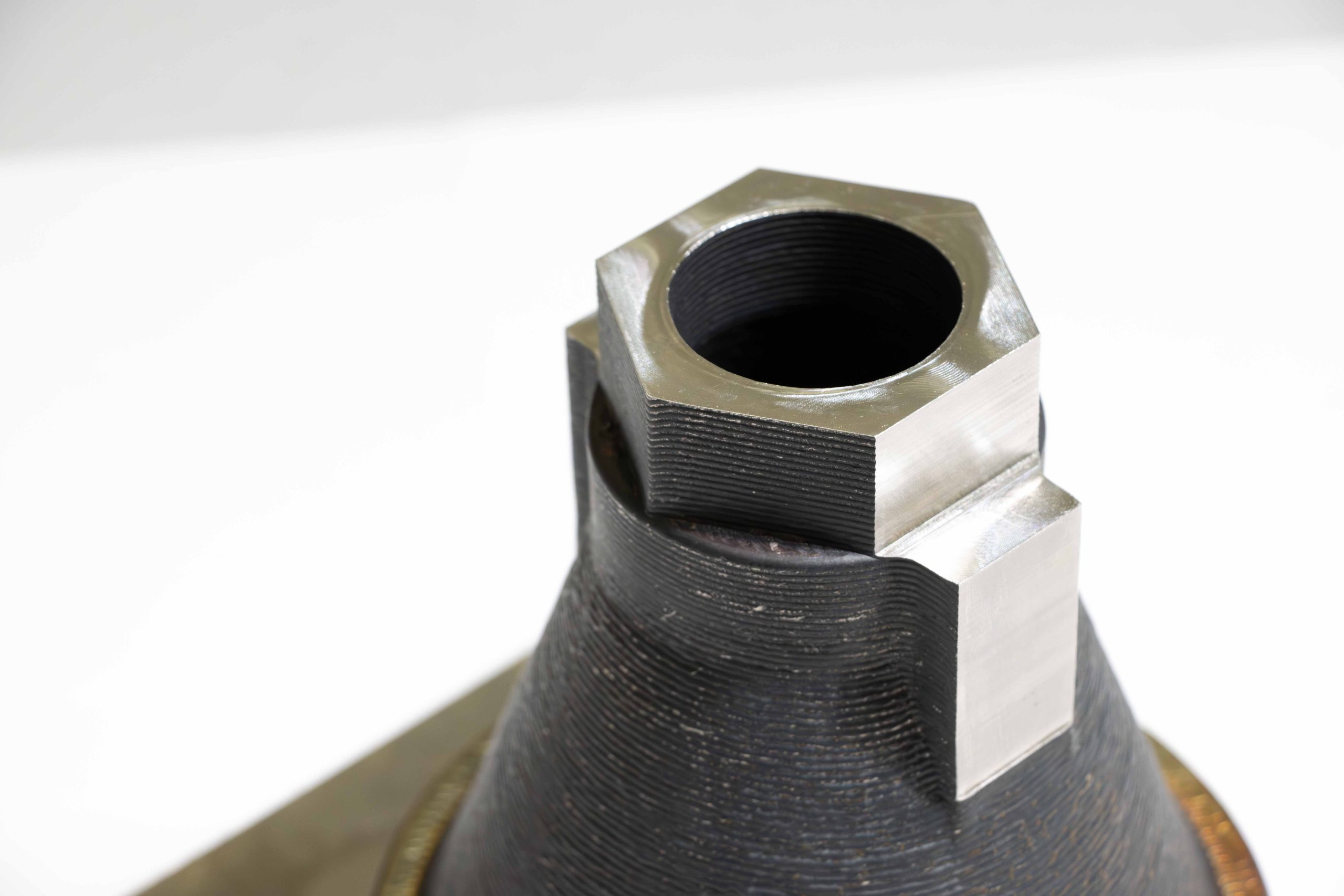
Meltio’s wire-laser technology (WLAM) allows the use of readily available, clean metal wire — from 316L stainless steel and ER70S6 steel to Inconel and even titanium or gold. Gary Mécanique has been using this to produce parts previously deemed impractical or expensive to fabricate traditionally.
Maximum flexibility
Reduced waste
On-demand production
Improved efficiency
Verified quality
Multi-material
Meltio 3D Printing Solutions
Unlock the potential of metal 3D printing
with Meltio. Your journey starts here.

CAROL IGUAL LAS PIEZAS COMO SON DEL MISMO SISTEMA SE PUEDEN PONER LAS 3 EN UNA MISMA LÍNEA Y 3 COLUMNAS. PONER LA INFO COMO ESTÁ EN LA PÁGINA DE PRIMANTE 3D: NOMBRE, MATERIAL TIEMPO DE IMPRESION, TAMAÑO Y VENTAJAS
System: Meltio Engine for Robot arms
Printing is easier than ever thanks to the improved process control, advanced sensors and live monitoring allowing you to produce parts consistently 24/7.
Sector: Heavy Machinery
Meltio's technology enhances the manufacturing process, delivering robust, high-precision components with improved sustainability and cost-effectiveness.
Material: Stainless Steel 316L
Wire feedstock proves more affordable and safer than powder-based alternatives.
Printing Time: 18 hours
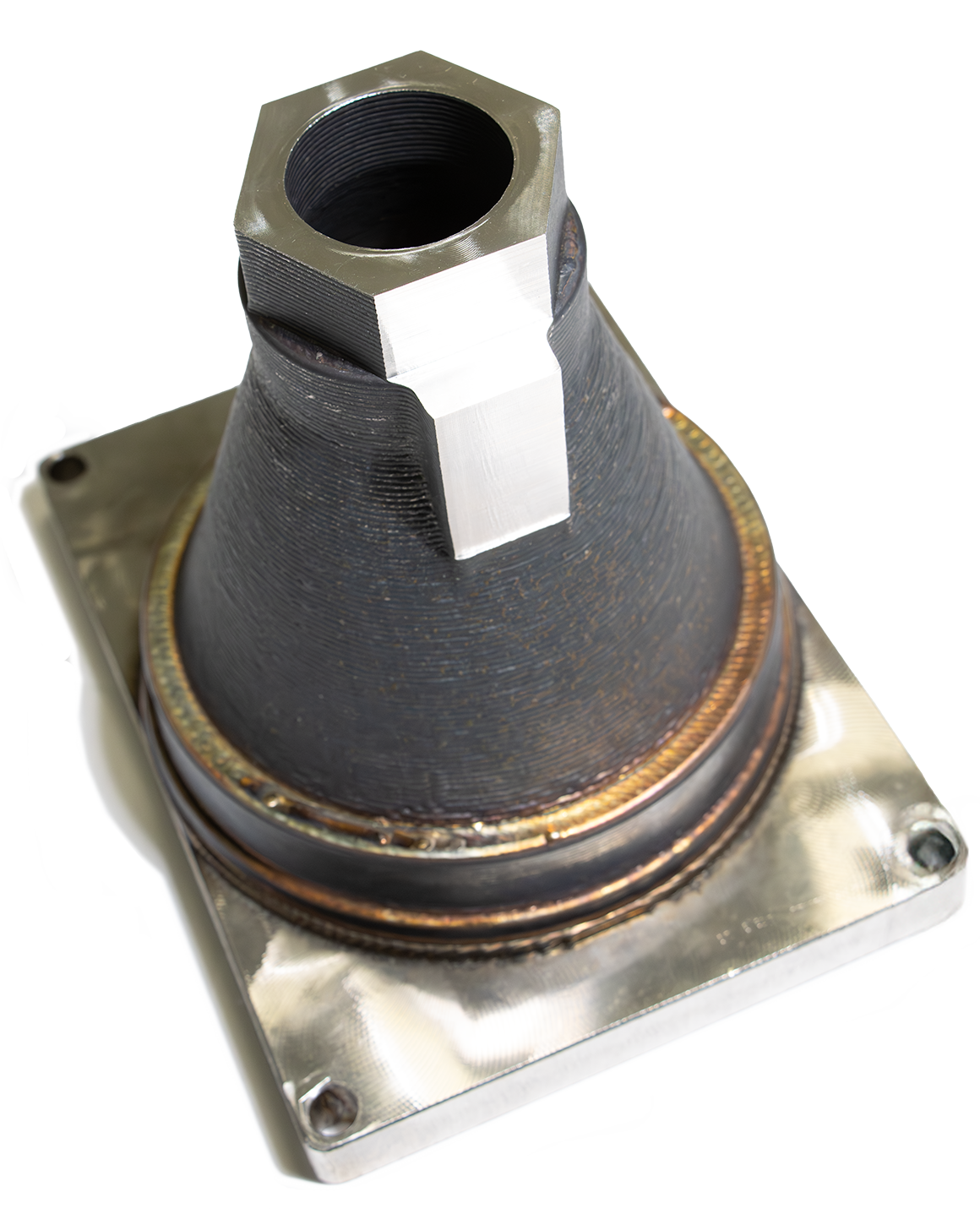
A part produced solely by additive manufacturing, it is easy to produce while allowing internal cooling and reduced mass.
System: Meltio Engine for Robot Arms
Printing is easier than ever thanks to the improved process control, advanced sensors and live monitoring allowing you to produce parts consistently 24/7.
Sector: Heavy Machinery
Meltio's technology enhances the manufacturing process, delivering robust, high-precision components with improved sustainability and cost-effectiveness.
Material: 316L Stainless Steel
Wire feedstock proves more affordable and safer than powder-based alternatives.
Printing Time: 8 hours
4h partial machining
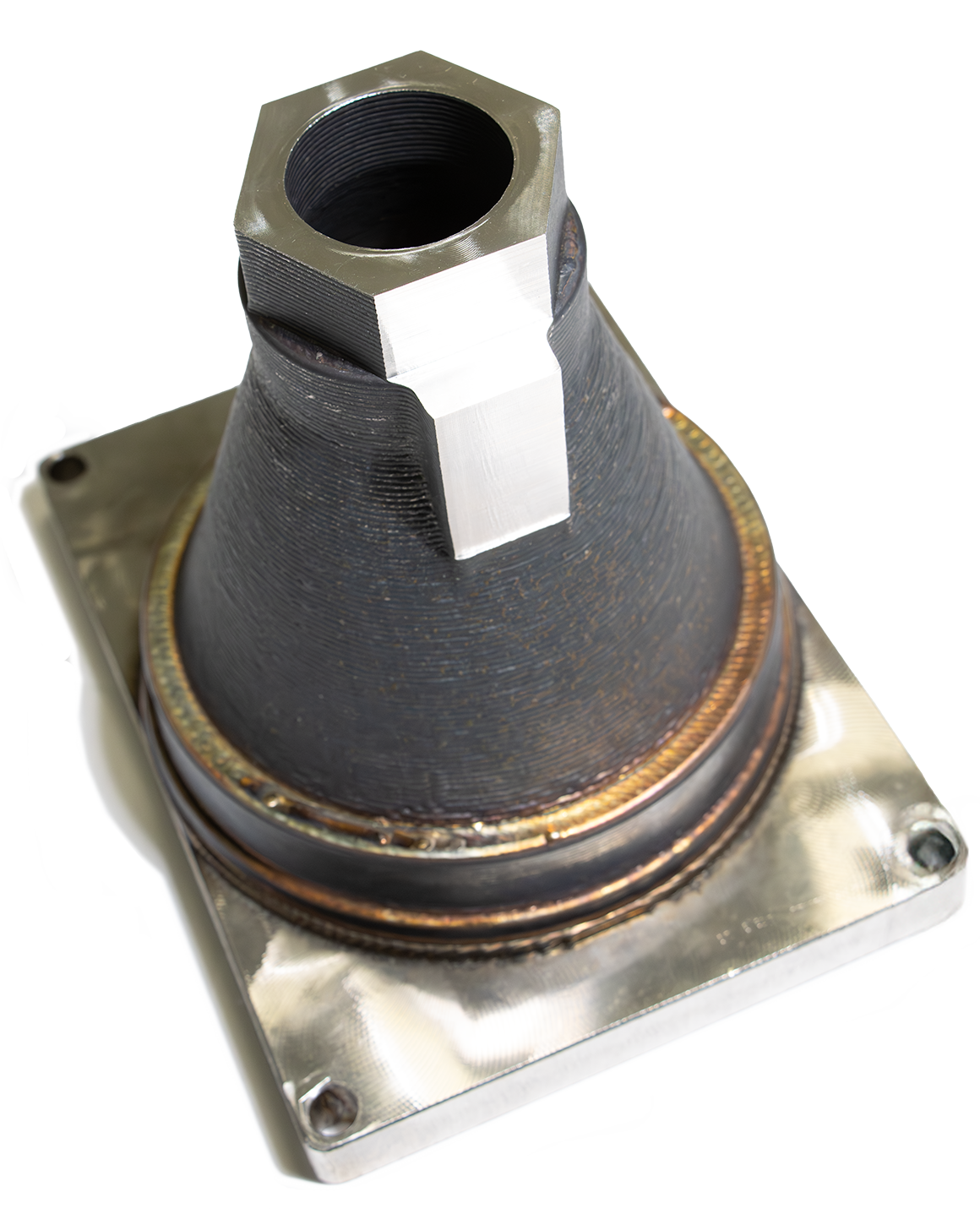
570mm propeller
System: Meltio M600
Sector: Heavy Machinery
Meltio's technology enhances the manufacturing process, delivering robust, high-precision components with improved sustainability and cost-effectiveness.
Material: 316L Stainless Steel
Wire feedstock proves more affordable and safer than powder-based alternatives.
Printing Time: 8 hours
4h partial machining
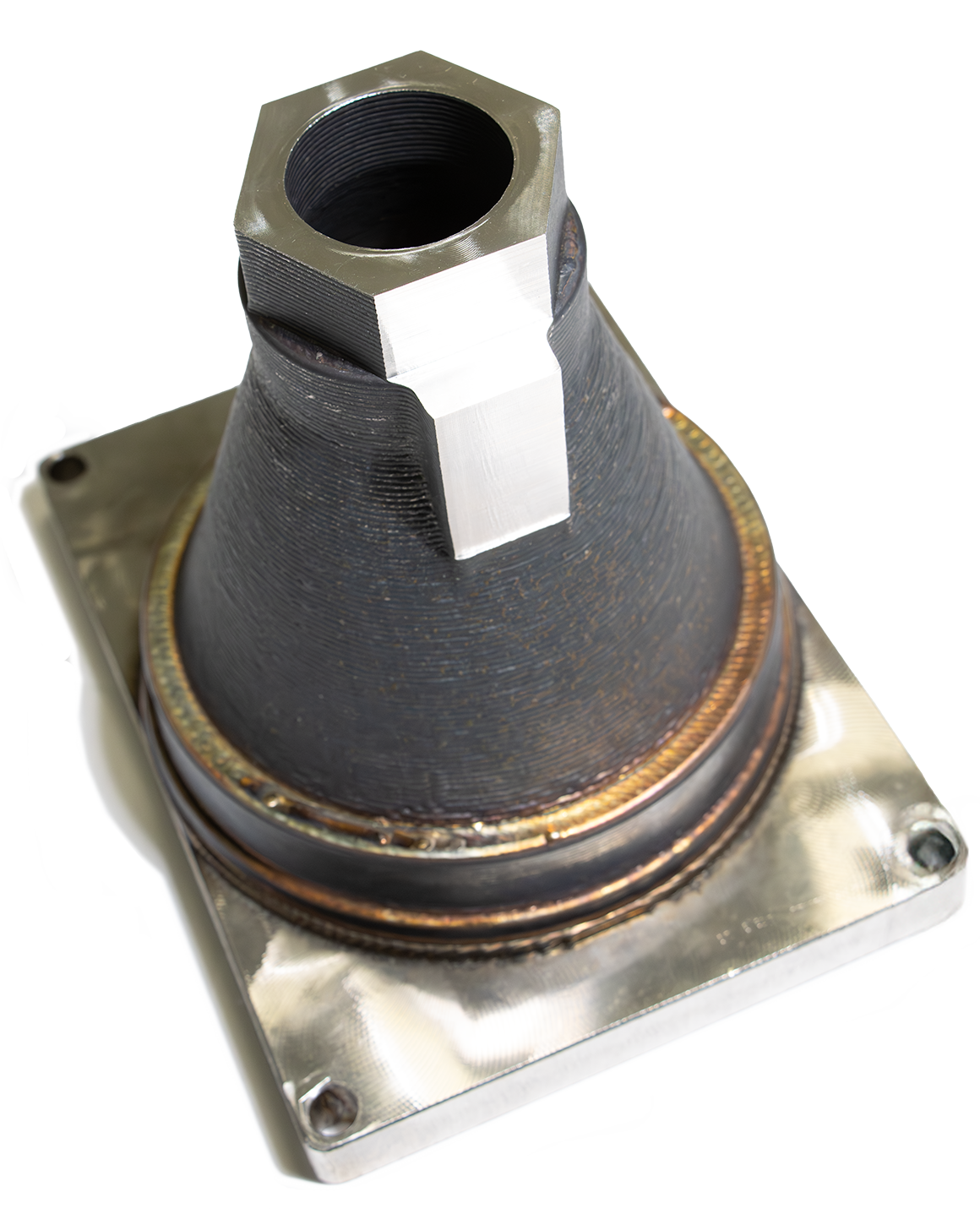
1-meter exhaust pipe
More than just manufacturing
One of the standout advantages for Gary Mécanique has been repair and rework. The Meltio setup allows existing parts to be reloaded into the machine for localized rebuilding — avoiding full remanufacturing. This not only cuts down cost and downtime but also contributes to a more sustainable production model.
And thanks to the near-net-shape capabilities of the DED process, machining time and material waste are significantly reduced.
“One common fear is mechanical strength,” says Justine. “But Meltio's technology undergoes rigorous testing — tensile, fatigue, tomography — ensuring the parts meet or exceed industrial requirements.”
A vision for the future
With Meltio’s wire-laser DED technology and robotic integration, Gary Mécanique has set a new benchmark for agility, precision, and scalability in metal manufacturing. The company continues to combine its traditional machining roots with cutting-edge innovation — delivering tailored, high-performance parts for a rapidly evolving industrial landscape.
“This isn’t just about technology — it’s about independence, flexibility, and pushing creative boundaries. Meltio is helping us make that possible.”
Want to know more about printed parts properties?
How a French family business
is redefining metal manufacturing
Case study developed by Meltio
Improving an inert bubble
with optimized component production
Case study developed by Meltio
In the heart of Roubaix, northern France, a family-run company with over 60 years of machining excellence is reshaping the future of industrial metal fabrication. Gary Mécanique, founded in 1962, has long embraced technological advancement — from early CNC adoption in the 1970s to high-precision 5-axis machining today.
Now, in its latest evolution, the company is pioneering the use of robotic metal additive manufacturing with Meltio’s wire-laser DED technology — enabling the creation and repair of large, complex metal parts with unmatched flexibility and control.

A growing demand for complexity and speed
The industrial sectors Gary Mécanique serves — from defense and energy to automotive and aerospace — increasingly demand parts that are larger, more geometrically intricate, and faster to produce. Traditional processes like casting and welding come with high costs, long lead times, and rigidity in design. That’s where metal 3D printing, and specifically wire-laser DED, comes in.
“We wanted a solution that would allow us to produce large, custom parts internally — without the overhead of tooling, molds, or external delays. Meltio’s technology, combined with robotic freedom, gave us exactly that.”
To remain competitive and future-ready, Gary Mécanique needed a solution that would allow:
- Large-format part production without traditional casting constraints.
- Precision near-net-shape fabrication to reduce machining steps.
- In-house, cost-effective repair and rework operations.
- Material and geometry versatility without extensive retooling.
Material versatility meets geometry freedom
The company adopted Meltio’s wire-laser DED technology by integrating the Meltio Engine with a 6-axis Fanuc robot and a custom 2-axis positioner, allowing up to 8 degrees of freedom. This setup enables printing in 3-axis, 5-axis positioned, and 5-axis continuous modes — ideal for parts with complex geometries.
Materials: Compatible with various wires, including 316L stainless steel and ER70S6 steel.
Capability: Parts up to 2 meters in diameter and 2 tons in weight.
Versatility: Enables full part production, hybrid manufacturing, and component repair.
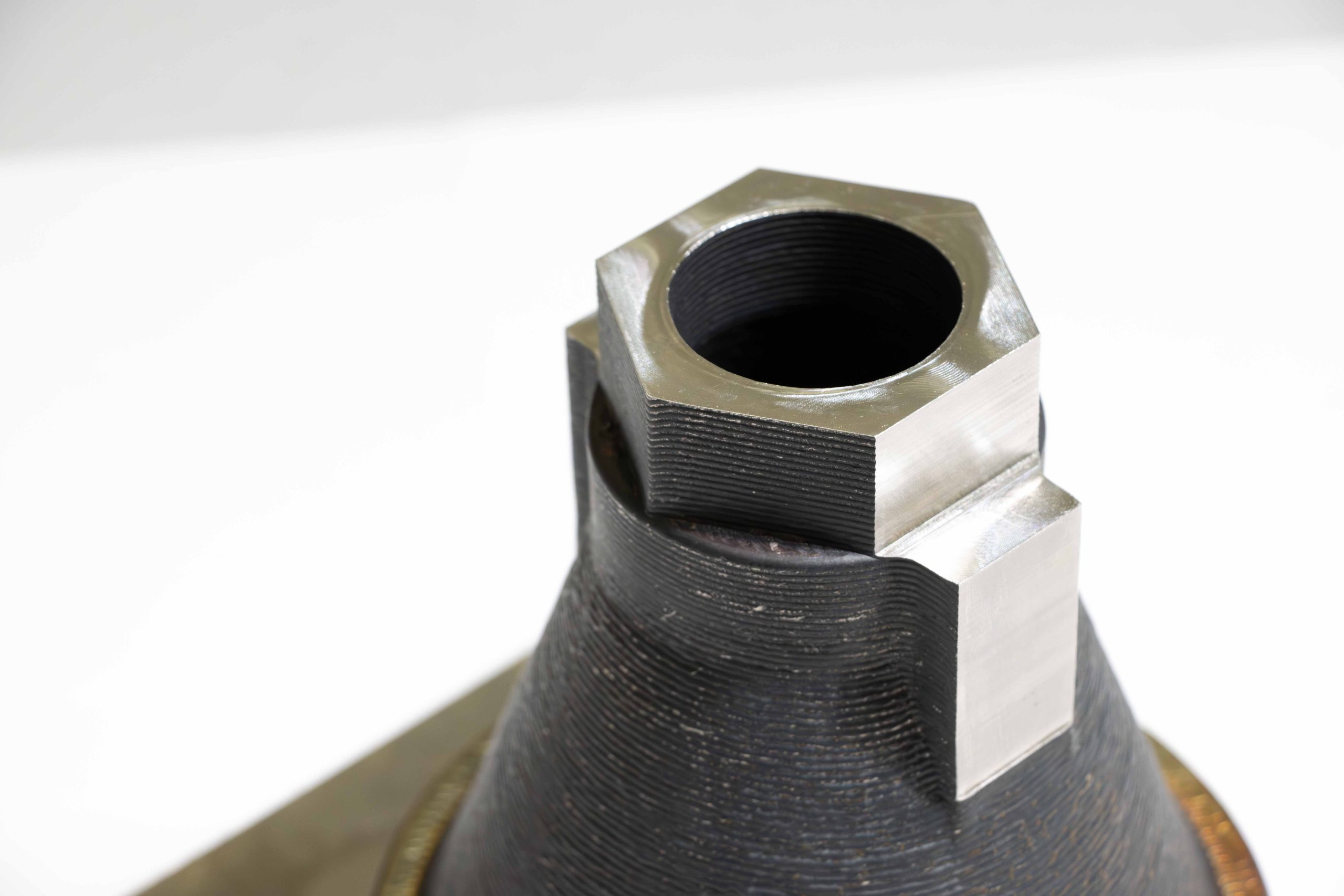
Meltio’s wire-laser technology (WLAM) allows the use of readily available, clean metal wire — from 316L stainless steel and ER70S6 steel to Inconel and even titanium or gold. Gary Mécanique has been using this to produce parts previously deemed impractical or expensive to fabricate traditionally.
Maximum flexibility
Reduced waste
On-demand production
Improved efficiency
Verified quality
Multi-material
Meltio 3D Printing Solutions
Unlock the potential of metal 3D printing
with Meltio. Your journey starts here.

CAROL IGUAL LAS PIEZAS COMO SON DEL MISMO SISTEMA SE PUEDEN PONER LAS 3 EN UNA MISMA LÍNEA Y 3 COLUMNAS. PONER LA INFO COMO ESTÁ EN LA PÁGINA DE PRIMANTE 3D: NOMBRE, MATERIAL TIEMPO DE IMPRESION, TAMAÑO Y VENTAJAS
System: Meltio Engine for Robot arms
Printing is easier than ever thanks to the improved process control, advanced sensors and live monitoring allowing you to produce parts consistently 24/7.
Sector: Heavy Machinery
Meltio's technology enhances the manufacturing process, delivering robust, high-precision components with improved sustainability and cost-effectiveness.
Material: Stainless Steel 316L
Wire feedstock proves more affordable and safer than powder-based alternatives.
Printing Time: 18 hours
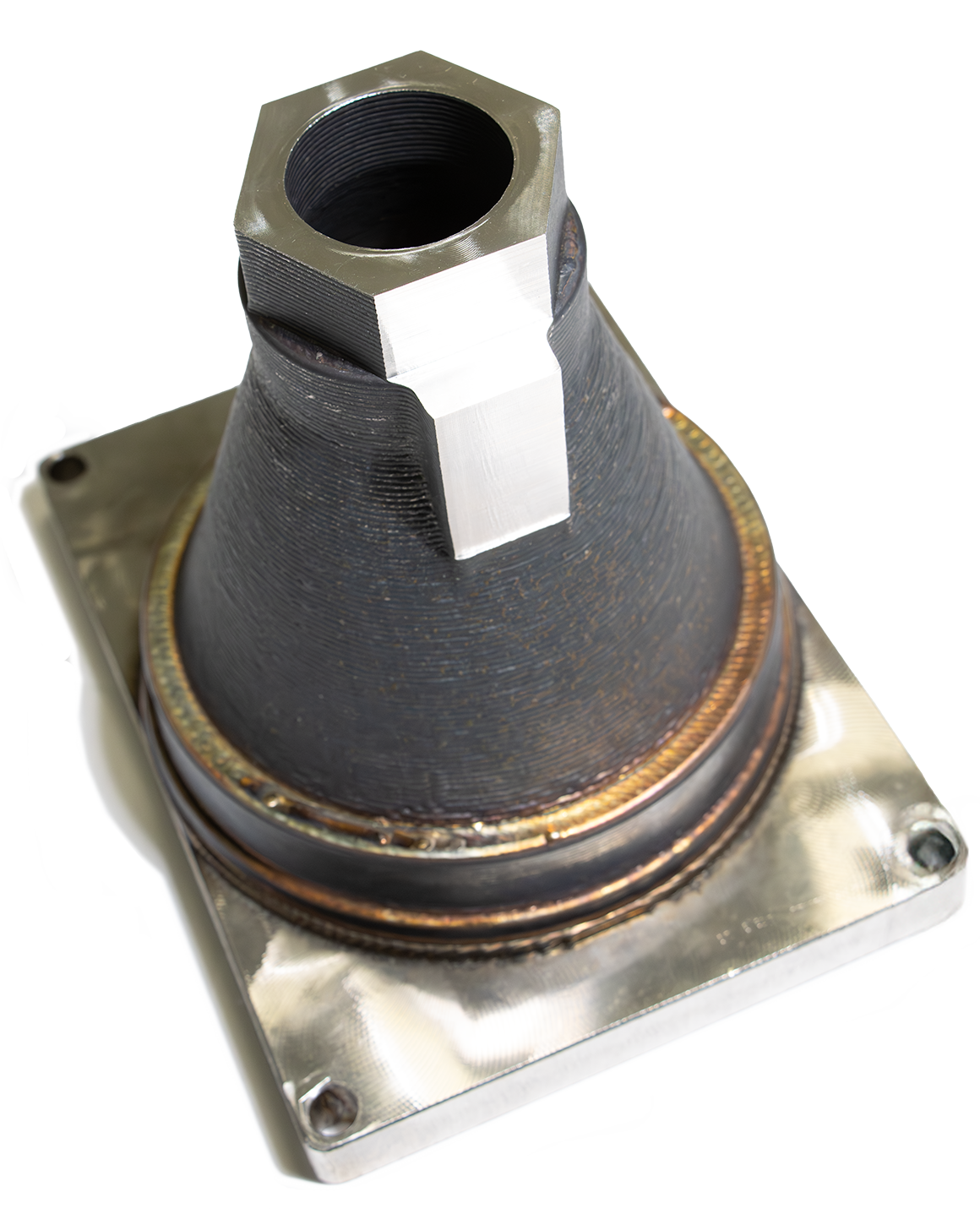
A part produced solely by additive manufacturing, it is easy to produce while allowing internal cooling and reduced mass.
System: Meltio Engine for Robot Arms
Printing is easier than ever thanks to the improved process control, advanced sensors and live monitoring allowing you to produce parts consistently 24/7.
Sector: Heavy Machinery
Meltio's technology enhances the manufacturing process, delivering robust, high-precision components with improved sustainability and cost-effectiveness.
Material: 316L Stainless Steel
Wire feedstock proves more affordable and safer than powder-based alternatives.
Printing Time: 8 hours
4h partial machining
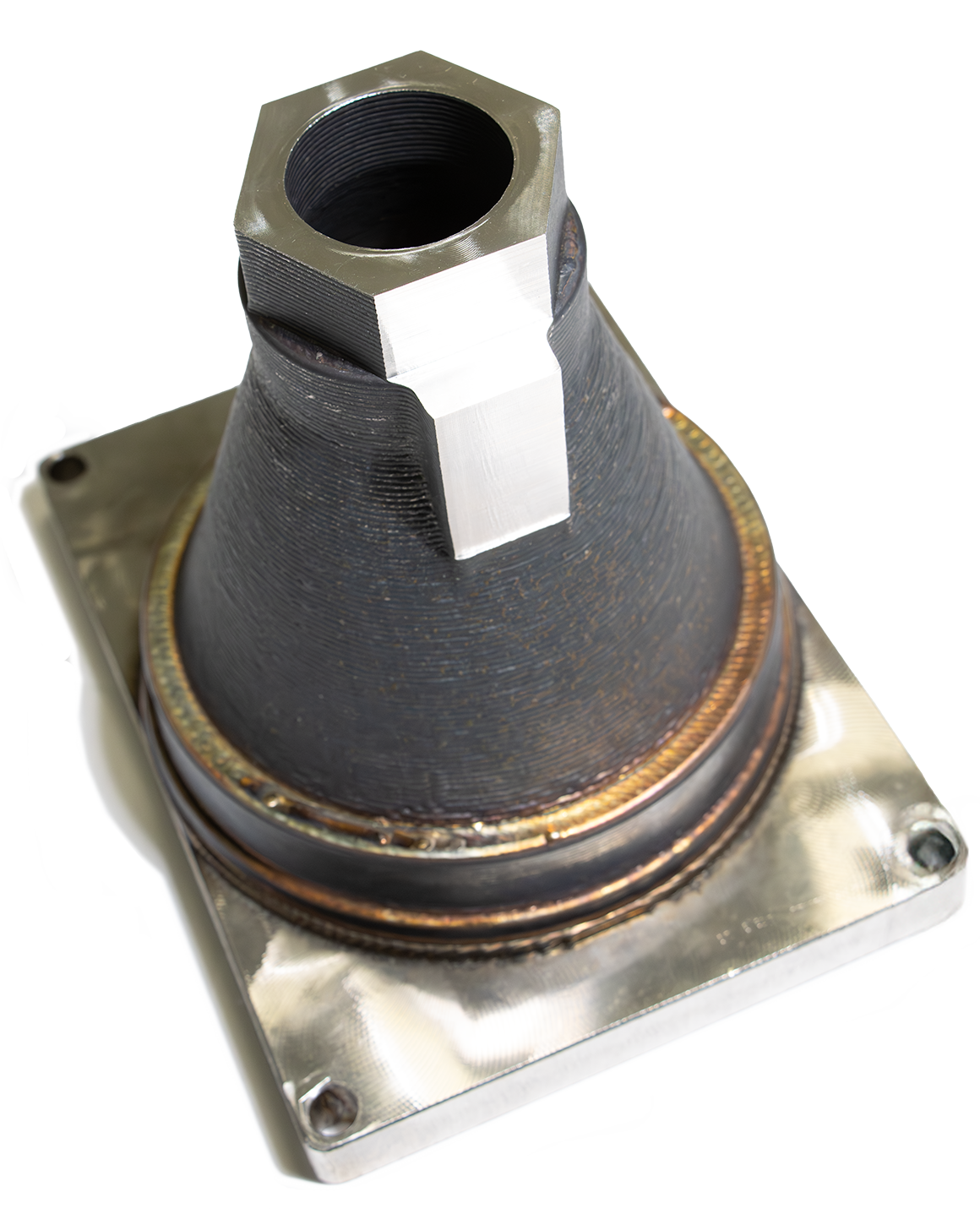
570mm propeller
System: Meltio M600
Sector: Heavy Machinery
Meltio's technology enhances the manufacturing process, delivering robust, high-precision components with improved sustainability and cost-effectiveness.
Material: 316L Stainless Steel
Wire feedstock proves more affordable and safer than powder-based alternatives.
Printing Time: 8 hours
4h partial machining
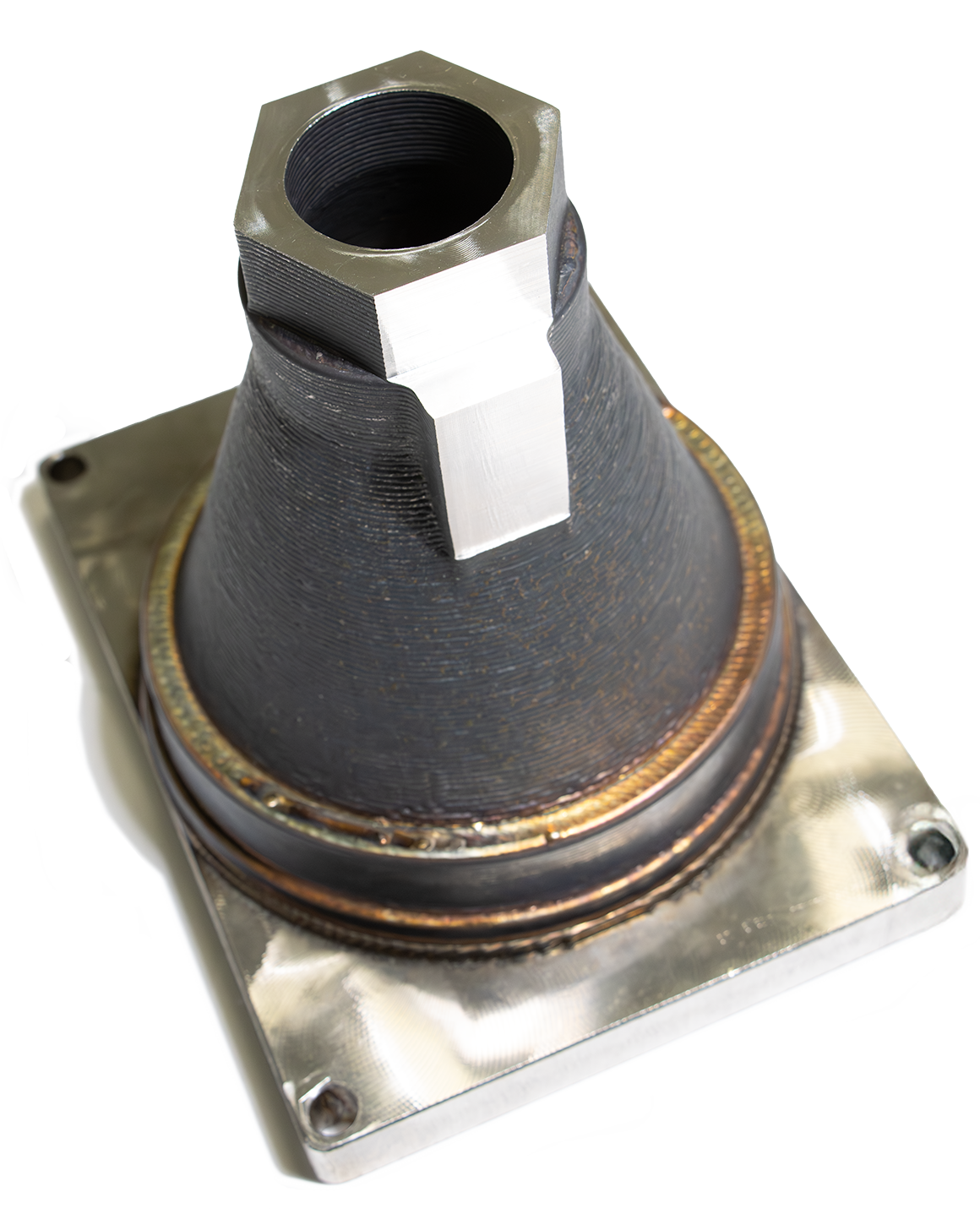
1-meter exhaust pipe
More than just manufacturing
One of the standout advantages for Gary Mécanique has been repair and rework. The Meltio setup allows existing parts to be reloaded into the machine for localized rebuilding — avoiding full remanufacturing. This not only cuts down cost and downtime but also contributes to a more sustainable production model.
And thanks to the near-net-shape capabilities of the DED process, machining time and material waste are significantly reduced.
“One common fear is mechanical strength,” says Justine. “But Meltio's technology undergoes rigorous testing — tensile, fatigue, tomography — ensuring the parts meet or exceed industrial requirements.”
A vision for the future
With Meltio’s wire-laser DED technology and robotic integration, Gary Mécanique has set a new benchmark for agility, precision, and scalability in metal manufacturing. The company continues to combine its traditional machining roots with cutting-edge innovation — delivering tailored, high-performance parts for a rapidly evolving industrial landscape.
“This isn’t just about technology — it’s about independence, flexibility, and pushing creative boundaries. Meltio is helping us make that possible.”
Want to know more about printed parts properties?
Not found application or sector?