The Spanish multinational is Leading the Present to Manufacture the Future including new expanded facilities in Spain with its unique metal additive manufacturing (AM) solutions: Meltio Engine Robot Integration; Meltio Engine CNC Integration; Meltio M450 metal 3D printer; Meltio Robot Cell and its slicer software, Meltio Space / Meltio Horizon
Meltio launches a series of video testimonials: real stories from our trusted clients who are already printing the future of manufacturing together with Meltio and its unique technology.
Check here Meltio testimonials from the market: https://meltio3d.com/testimonials/
The mission of the Metal AM company is to provide all industries around the world with the ultimate wire-laser metal additive manufacturing technology to create and repair reliable and highly dense metal parts (stainless steels, titanium, nickel, Inconel and many other materials).
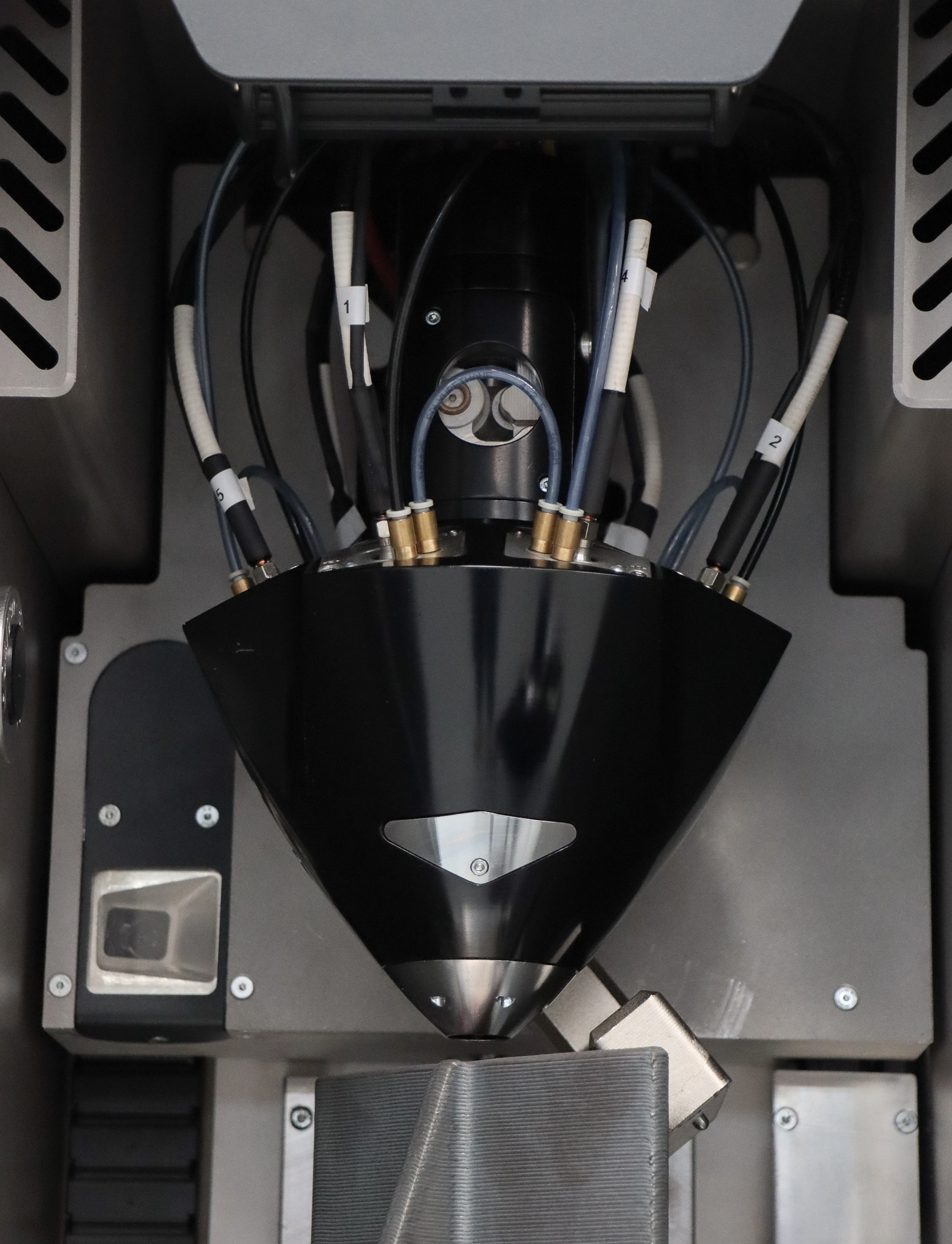
Meltio is revolutionizing the way of manufacturing and repairing metal parts achieving very reliable results and extraordinarily dense parts with its additive manufacturing technology. Industries such as automotive, aerospace, oil and gas, mining, research centers, universities, and others in more than 60 countries already enjoy Meltio’s solutions.
Meltio’s technology continues to grow worldwide. A few days before the end of 2023 and welcoming 2024, the metal AM multinational has successfully completed the launch of new products expanding its family of hardware and software in response to the growing demand for additive manufacturing from different industrial applications to create and repair metal parts. Its metal wire-laser technology enables aerospace, automotive, defense, mining, oil and gas, engineering, and other industries to streamline their production lines.
Meltio remains focused on growth: new expanded facilities and new plans for more wire-laser metal 3D printing innovation by 2024 to exceed + 300 systems sold worldwide.
They also gain flexibility by using Meltio’s equipment 7 days per week, 24 hours a day in their industrial manufacturing centers anywhere in the world. The mission of the Metal AM company is to provide all industries around the world with the ultimate wire-laser metal additive manufacturing technology to create and repair reliable and highly dense metal parts (stainless steels, titanium, nickel, Inconel, and many other materials).
These are Meltio’s main milestones in 2023:
300+ Systems Sold
The Spanish multinational dedicated to the development of its unique and patented wire-laser metal 3D printing technology has just celebrated a very remarkable ephemeris: Meltio has exceeded 300 systems sold worldwide.
Ángel Llavero López de Villalta, CEO of Meltio, says: “This milestone of exceeding 300 Meltio systems sold worldwide confirms that the industry is embracing our metal 3D printing solutions for manufacturing and repairing metal parts. It is a recognition of the efforts of the entire Meltio team and a confirmation that we are on the right path of innovation to offer the market new Meltio solutions that respond to their production needs, flexibility, and reliability in industrial manufacturing processes“.
Meltio launches a series of video testimonials: real stories from our trusted clients who are already printing the future of manufacturing together with Meltio and its unique technology companies like Hirudi, Sivó, Holcim, Cetemet, Roez, and others have participated in these testimonials.
54 Total Worldwide Partners
Meltio has increased the number of partners during this year. The total number of total worldwide technology distributors and system integrators is 54. Currently, Meltio’s sales department covers more than 50 countries thanks to its partners.
3 Product Launches
Meltio Robot Cell
Meltio has launched the Meltio Robot Cell, a turn-key metal 3D printing solution to boost the performance of industrial robotic arms in a safer, more reliable, and highly accurate way by controlling the entire process including its slicing software, Meltio Space.
The Meltio Robot Cell includes an ABB robotic arm that is transformed into a metal 3D printer and it works with an open hardware platform that lets Meltio attach its metal 3D deposition head to any brand of robotic arm. In this case, it’s done to improve user experience by introducing a standardization approach through the Meltio Robot Cell.
The robot and positioner are installed on a self-supporting platform, as well as a laser-safe enclosure together with the Meltio Engine, Meltio Space, and accessories. With the Meltio Robot Cell, the company is fulfilling most of the applications that industry and integrators need when printing industrial metal parts, and this is the reason this standardization matches with the possibility of building custom integrations with the help of Meltio partners.

Meltio Space
Meltio revolutionizes the ability of a robotic arm to manufacture 3D-printed metal parts with its ultimate Meltio Space software, which enables highly accurate and reliable designs. Meltio Space is a toolpath generator software for the Meltio Engine Robot Integration with an easy-to-use interface for planar, non-planar, and variable extrusion toolpaths.
By offering a user-friendly interface and comprehensive features, this advanced robot slicer simplifies the use of Meltio’s wire-laser metal 3D printing technology of the most popular robotic brands with a built-in robot library and post-processors for ABB, Kuka, FANUC, and Yaskawa.
Meltio Space is a toolpath generator software for the Meltio Engine Robot Integration with an easy-to-use interface for planar, non-planar, and variable extrusion toolpaths. It also includes 2-axis workpiece positioner interpolation, kinematics simulation, collisions check, and cell configuration.
Meltio Space slicer revolutionizes the world of 3D printing by going beyond the constraints of traditional 3-axis systems. With its integration of 6-axis robotic manipulators and 2-axis workpiece positioners, it opens up a whole new realm of possibilities for metal 3D printing. The comprehensive coordination, multi-axis toolpath generation, and enhanced design freedom provided by Meltio Space propel the industry forward, empowering users to create intricate, customized, and highly detailed metal parts like never before.
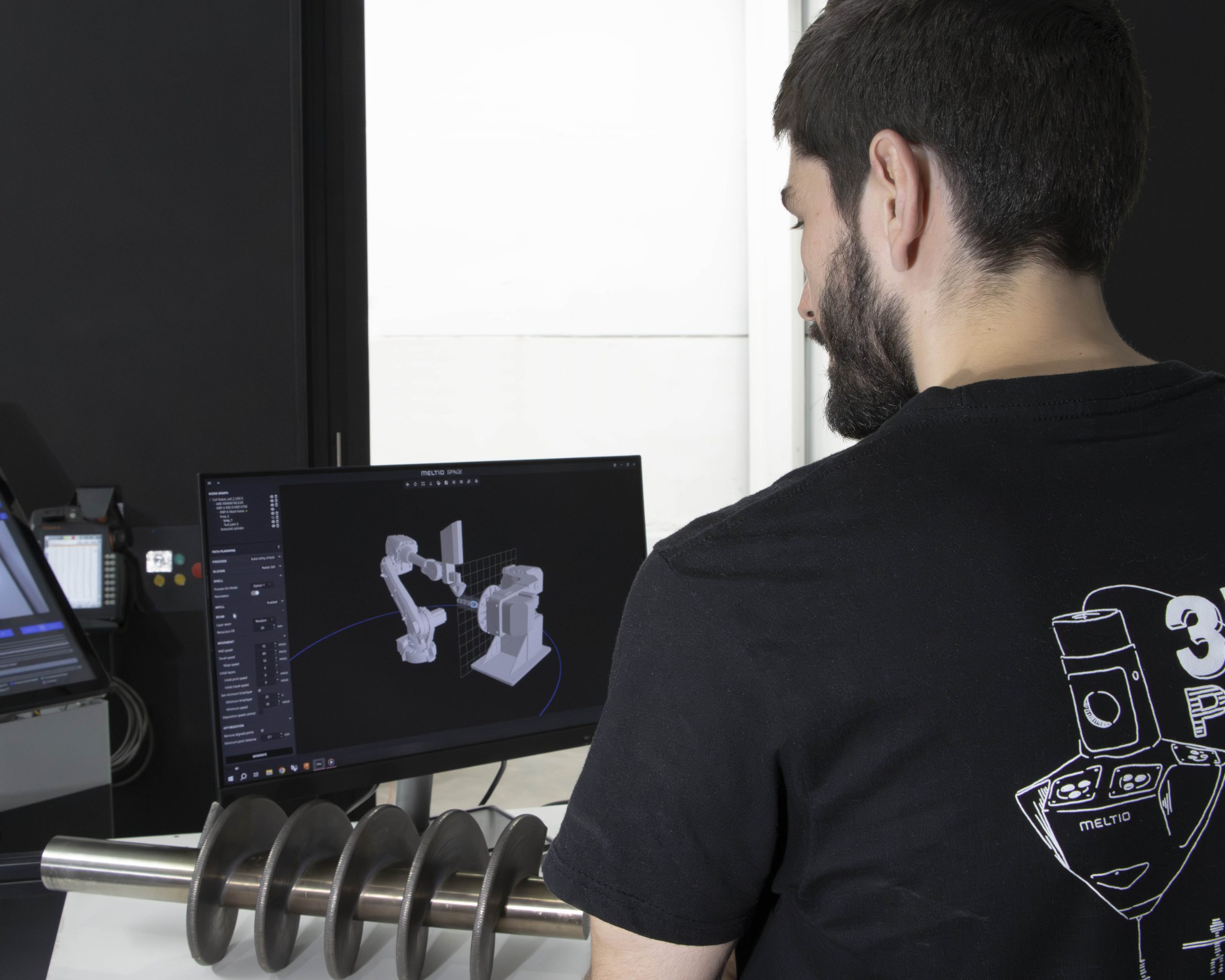
Meltio Horizon
Meltio offers its proprietary toolpath generator software, Meltio Horizon, which provides a user experience tailored around its plug-and-play metal 3D printer, the Meltio M450.
The new software uses the laser-wire metal deposition process with the Meltio M450. Meltio users had previously been reliant on third-party fused filament fabrication (FFF) slicers to prepare toolpaths for the Meltio M450.
With the Meltio Horizon software, all of the material-related settings are directly in the slicing software, enabling full control and a single profile. This also enables users to create more specialized printing profiles, with the power to directly control the laser and hot wire on a per-slicing-feature basis, rather than being set for the full part.
This slicer is currently only compatible with the Meltio M450 metal 3D printer. For Meltio engines (CNC and robot integration), the company is currently working on developing its open software ecosystem partnerships that allow the generation of five-axis G codes.
Xtech
Meltio together with its U.S. distributor Phillips Corporation have received the prestigious recognition of the U.S. Army xTech International Advanced Manufacturing and Materials, which brings together a forum of international companies and academic institutions and where more than 300 technology companies from different countries participate.
The award aims to involve the best technology players from around the world, in this case in the 3D printing sector, to contribute their solutions to the U.S. Department of Defense and participate in the development of its Defense program. This year’s theme was Advanced Manufacturing and Materials.
The U.S. Department of Defense has awarded the unique and patented metal 3D printing technology of the Spanish multinational metal additive manufacturing leader, Meltio, which means recognition as a “strategic technology partner” in the current and future development plans in the military and security field.
This is the first time that a Spanish company has received this award in the field of additive manufacturing, which allows printing and repairing parts using 3D printing, solving possible logistical problems and providing manufacturing autonomy while improving the supply chains of parts in the defense sector.
This award consolidates Meltio’s relationship with the U.S. Army and increases its possibilities of having a relationship with other U.S. defense departments and also with armies of other countries.
Ángel Llavero López de Villalta, CEO of Meltio, said: “ The award we have received is recognition to Meltio’s professionals and gives reliability to our technology. For us, the military sector is a sector that allows us to bring together all the applications of our disruptive metal 3D printing technology. It is an opportunity for Meltio to develop a dual application for the civil and military sectors. “
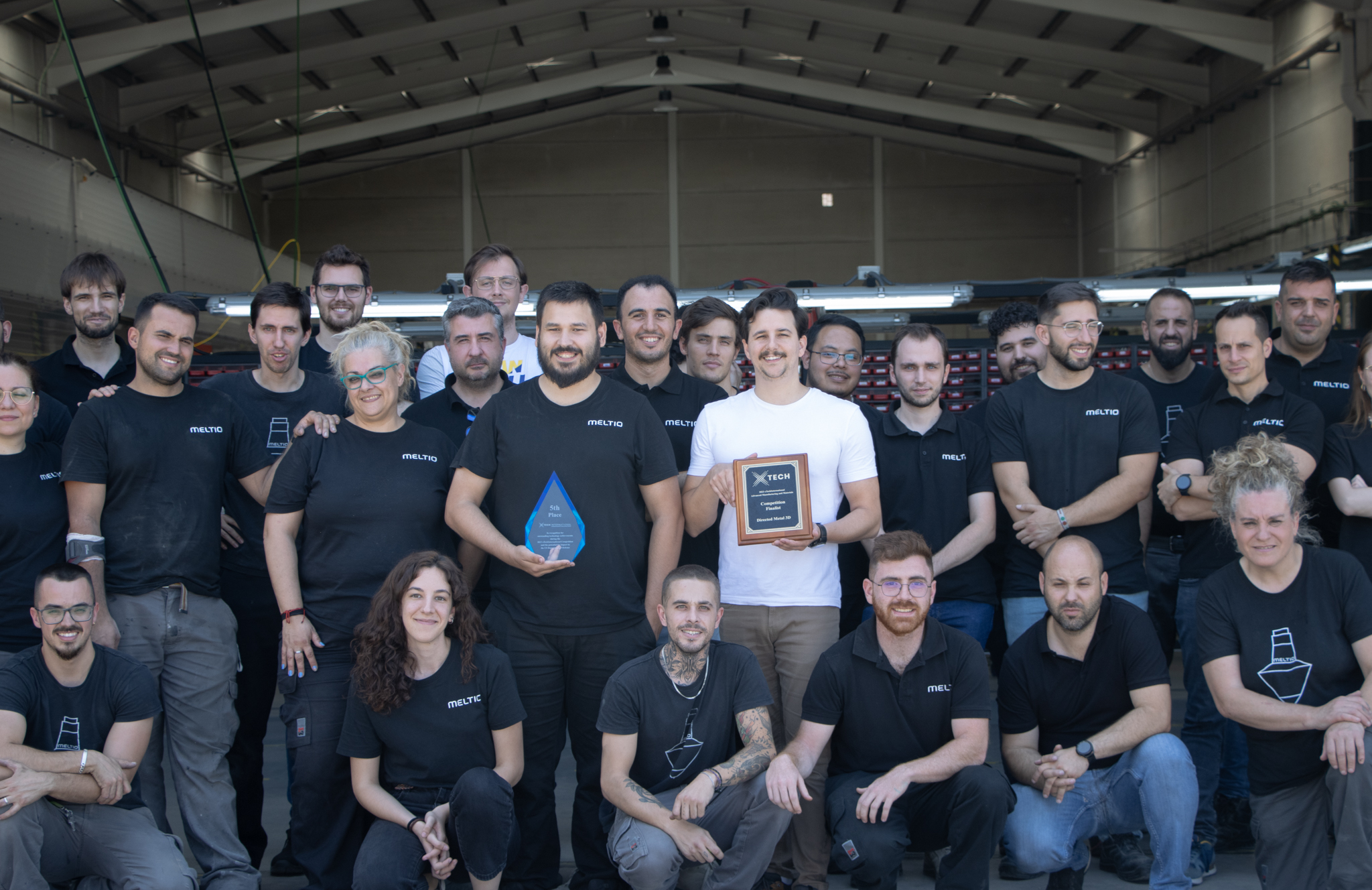
The U.S. Department of Defense has recognized the Meltio Engine CNC Integration, together with our sales partner in the US, Phillips Corporation:
“ This is a technology with a very robust capability for fabrication and near-net shape part production. It offers a very valuable approach using standard welding wire that is already available in the U.S. Department of Defense’s manufacturing environments. A coil of wire can be made into a near net shape for any part, thus avoiding the need for large stocks of shapes/forms/sizes of raw material. ”
US Navy use case
Meltio together with Phillips Corporation – a global manufacturing solutions leader based in the US – have worked together to install for the first time on a US Navy ship a metal 3D printing solution for the onboard manufacture of spare parts and repairs. The Phillips Additive Hybrid powered by Haas took the laser metal deposition technology of Meltio and integrated it with the world-renowned Haas CNC vertical machining centers control mill onboard the USS Bataan ship.
This new project represents a further step towards demonstrating an industrially useful application in the marine sector thanks to the accessible wire-laser metal 3D printing technology developed by Meltio. Meltio collaborates with Haas on other hybrid system projects in other industries and different countries. The Hybrid system provides subtractive and additive manufacturing. The US Navy is using a combination of these in this particular project for the USS Bataan ship.
The equipment, installed under a joint effort between the Commander, the Naval Surface Force Atlantic, and the Naval Sea Systems Command (NAVSEA) Technology Office, includes the Phillips Additive Hybrid system, which integrates a Meltio wire-laser metal deposition head on a Haas TM-1 computer numerical control mill.
The Haas TM-1 platform has been proven to operate reliably in an afloat environment aboard several aircraft carriers. Integrating the Meltio deposition head with the Haas TM-1 provides both an additive and subtractive manufacturing capability within the same system – increasing efficiency and reducing waste when compared with typical machining.
Ángel Llavero López de Villalta, CEO of Meltio, says: “ For us, the fact that the US Navy has incorporated Meltio’s wire-laser metal 3D printing solution and Haas hybrid equipment thanks to Phillips Corporation on board the US Navy ship to manufacture spare parts and repair them is the consequence of years of effort and a great vision that we had at Meltio.
“ The introduction of additive manufacturing (AM) into naval operations supports readiness and self-sufficiency, ” states Rear Adm. Brendan McLane, commander, Naval Surface Force Atlantic. “ These printers can help the Navy overcome both obsolescence issues for ships and systems that have service lives measured in decades and directly contribute to enhanced operational availability of our systems and ships, ” says NAVSEA Chief Engineer Rear Adm. Jason Lloyd.
The Phillips Additive Hybrid system prints 316L stainless steel, a prevalent material in US Navy ship systems. While stainless steel additive manufacturing onboard naval ships is new, it also represents an advancement in providing sailors with industrial-level manufacturing capabilities to print individual parts for systems that previously had not been readily available without procuring the entire system at a significantly greater cost.