Improving an inert bubble
with optimized component production
Case study developed by Meltio
Improving an inert bubble
with optimized component production
Case study developed by Meltio
This case study presents the internal evaluation of manufacturing a 150 mm diameter Adapter Plate for the Inert Bubble using Metal Additive Manufacturing with Meltio technology. The analysis compares three approaches: in-house production (Meltio LMD + partial machining), traditional full in-house machining, and outsourcing to a third-party supplier.
The results show that manufacturing with Meltio offers significant advantages in cost reduction, material efficiency, and production flexibility, making it the preferred option for low-volume or prototype parts.

Facing inefficiencies in conventional production
Traditional manufacturing methods came with several inherent drawbacks. Machining from solid bar stock generated significant material waste—over 40 kg per part—due to an extremely poor buy-to-fly ratio. The process also required lengthy machining times, particularly when relying on under-optimized CNC equipment.
For small production runs, these inefficiencies translated into high costs and low profitability. Furthermore, outsourcing increased dependency on external suppliers, introducing longer lead times and reducing production agility.
To sum up, problems to be solved were:
- High material waste during traditional machining (high buy-to-fly ratio).
- Increased costs for raw materials and consumables.
- Long machining times due to suboptimal CNC equipment.
- Higher dependence on external suppliers and longer lead times.
- Low profitability when producing small volumes.
The Meltio approach to modern fabrication
To overcome these limitations, Meltio’s manufacturing process was implemented. The strategy involved metal 3D printing a near-net shape of the Adapter Plate using LMD technology, followed by selective machining only on critical surfaces.
This drastically reduced the amount of material removed during finishing, slashing both waste and machining time. By combining additive and subtractive methods in-house, the team could optimize material use while maintaining the necessary precision in key areas of the part.
- Wire-LMD manufacturing: Metal 3D printing of the near-net shape with Meltio LMD, followed by selective machining of critical surfaces.
- Reduced machining needs: Most of the part remains in as-printed condition.
- Optimized buy-to-fly ratio: Achieved a much more efficient material usage compared to traditional methods.
The results were compelling. The Meltio’s method reduced total production cost to just €264.54
50% cheaper than traditional machining
over 60% cheaper than outsourcing
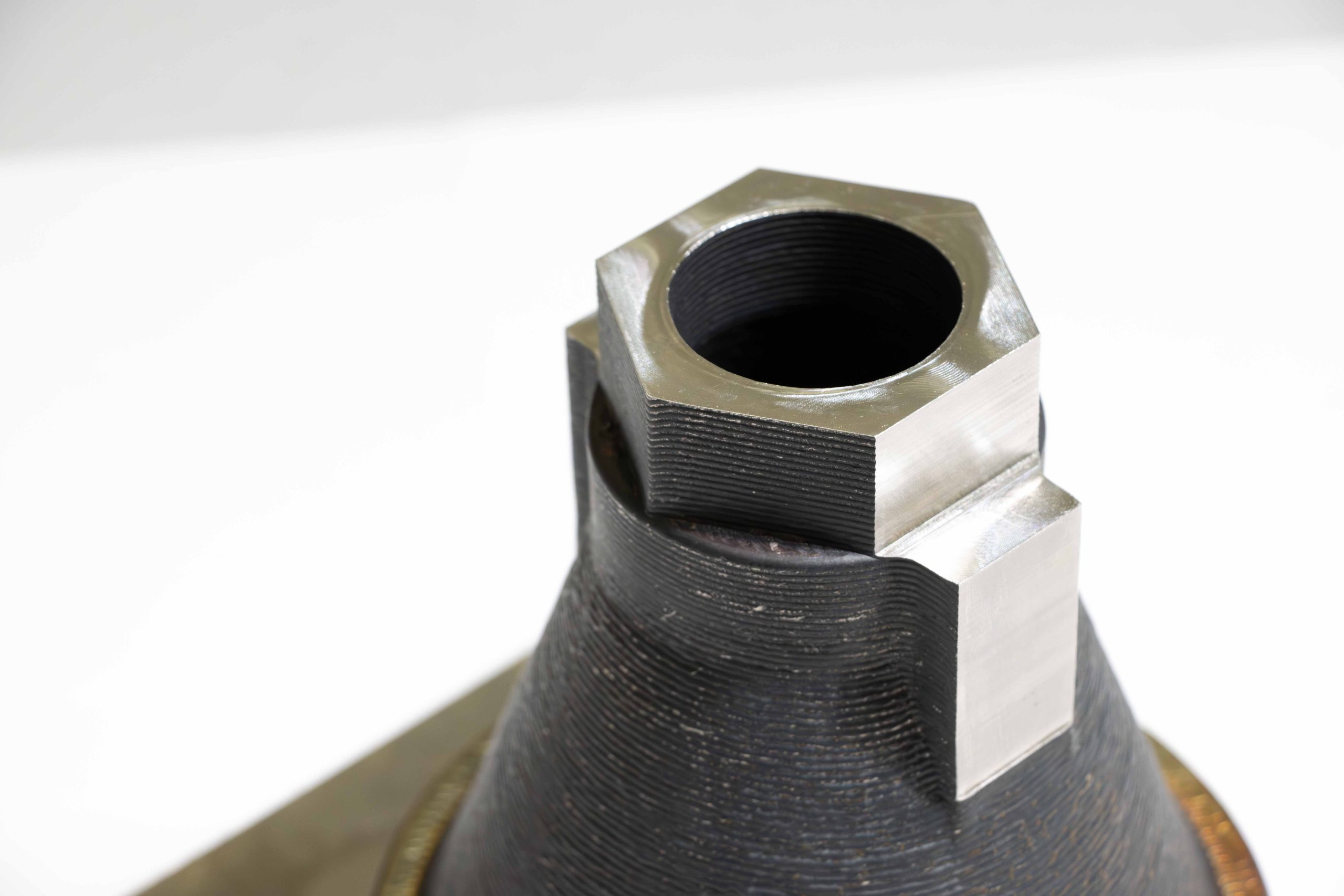
The buy-to-fly ratio improved dramatically to 1.11, indicating near-complete material utilization.
Additionally, the approach enhanced sustainability through minimal waste and offered a scalable solution for other small-batch applications. As the CNC setup is further optimized, even greater time and cost savings are expected. The flexibility of in-house metal 3d printing and machining also empowers faster iterations and prototyping without third-party delays.
Cost-effective prototyping and low-volume production
Significant cost savings
Enhanced sustainability through reduced material waste
Increased production flexibility
Potential for further efficiency improvements
Scalable solution for small-batch manufacturing
Meltio 3D Printing Solutions
Unlock the potential of metal 3D printing with Meltio. Your journey starts here.
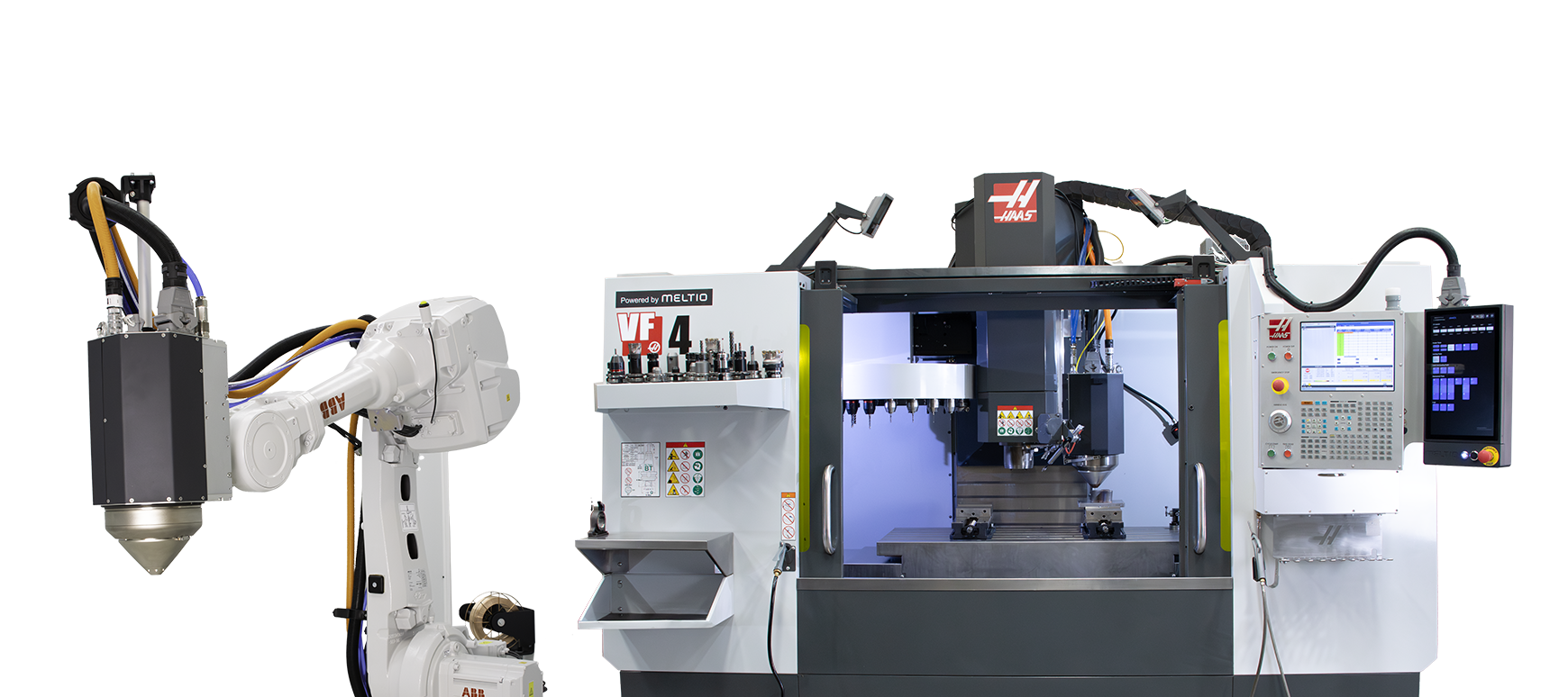
Meltio 3D Printing Solutions
Unlock the potential of metal 3D printing with Meltio. Your journey starts here.
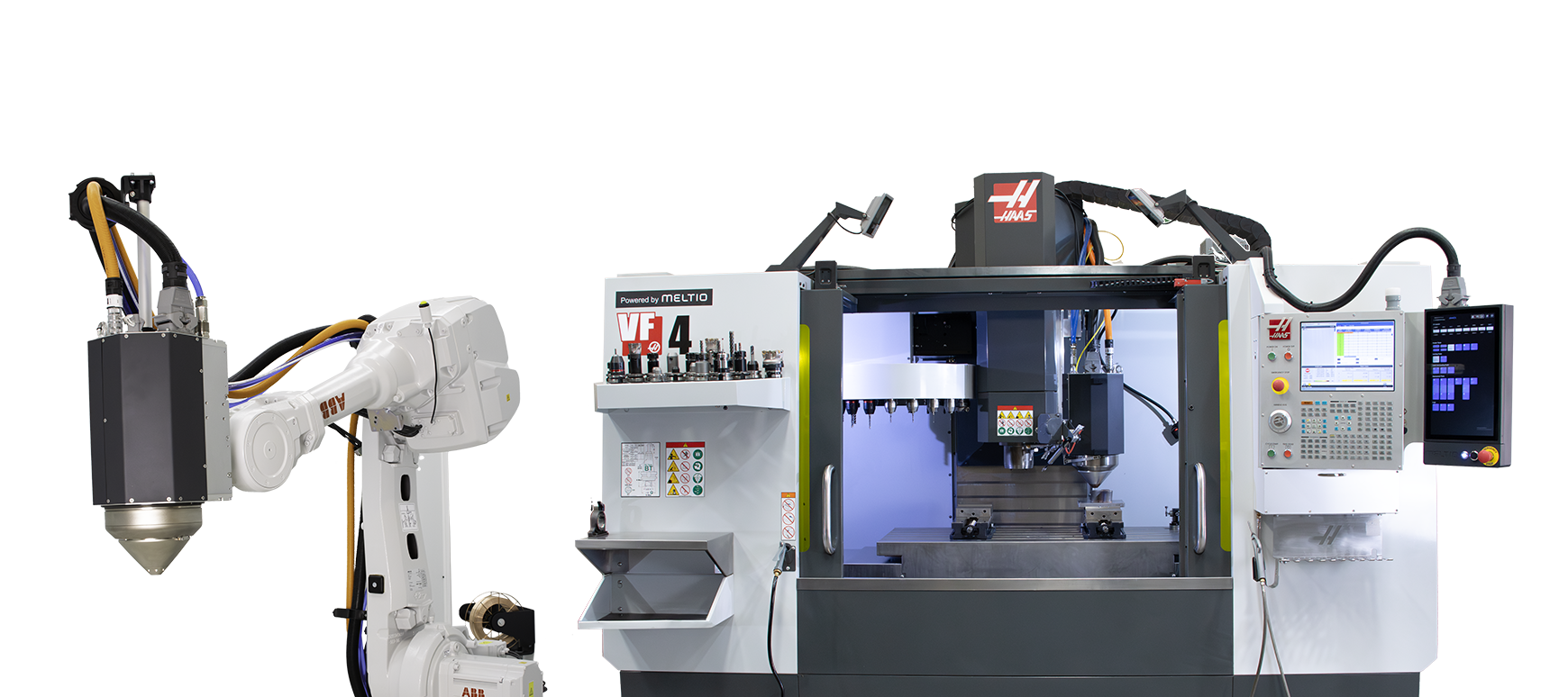
Tangible gains from an optimized process
8 hours printing time
264.54€ total cost
Method | Total cost (€) | Buy-to-Fly Ratio |
Meltio LMD + Partial Machining | 264.54€ | 1.11 |
Full traditional machining | 524.79€ | 19.74 |
Outsourcing to a supplier | 700.00€ | – |
System: Meltio M600
Printing is easier than ever thanks to the improved process control, advanced sensors and live monitoring allowing you to produce parts consistently 24/7.
Sector: Heavy Machinery
Meltio’s technology enhances the manufacturing process, delivering robust, high-precision components with improved sustainability and cost-effectiveness.
Material: 316L Stainless Steel
Wire feedstock proves more affordable and safer than powder-based alternatives.
Printing Time: 8 hours
4h partial machining
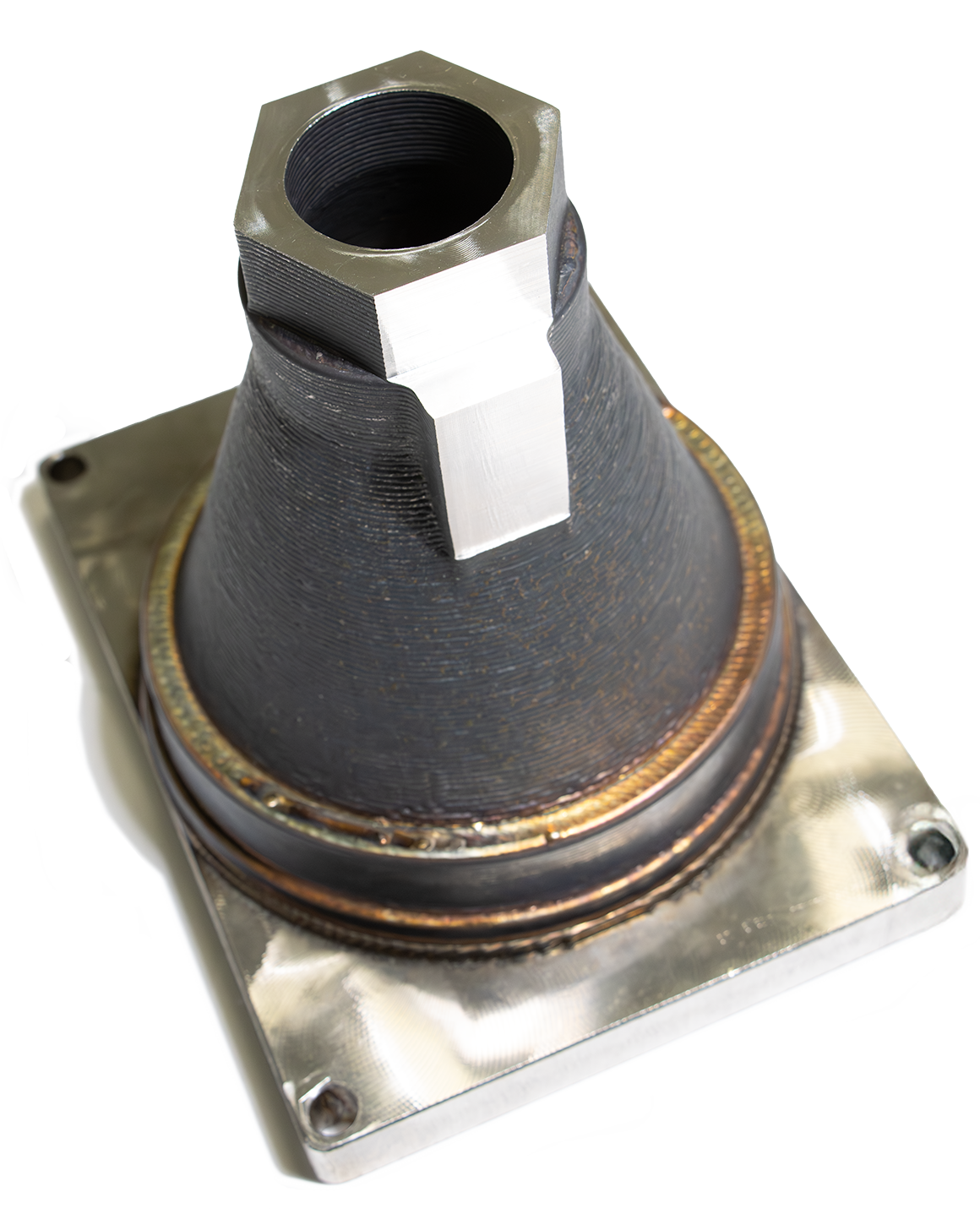
A forward-thinking manufacturing strategy
The Meltio manufacturing approach has proven to be a superior solution for producing the Adapter Plate, especially in low-volume scenarios. It brings together the best of additive and subtractive technologies, ensuring high efficiency, cost savings, and reduced environmental impact.
With plans to expand this method to similar parts, Meltio demonstrates a clear path toward smarter, more sustainable, and more adaptable production workflows.
Want to know more about printed parts properties?