As the Marine Renewable Energy (MRE) sector continues to expand, it is essential that innovation in manufacturing keeps pace to reduce costs and enhance the economic viability of emerging technologies. Additive manufacturing, commonly known as 3D printing, offers a promising avenue for rapid prototyping of marine hydrokinetic technologies, particularly in support of the U.S. Department of Energy’s Powering the Blue Economy™ initiatives.
In this blog, we will explore how the Meltio process facilitates the production of robust and corrosion-resistant parts specifically designed to endure harsh marine environments. Also, we’ll discover that, beyond improving performance, 3D printing offers rapid prototyping and cost-effective manufacturing solutions, unlocking significant innovation potential across various industries.
To do so, we’ll focus on the impressive results achieved in crafting a structural spar for an axial-flow tidal turbine blade, using Meltio’s advanced 3D printing technology.
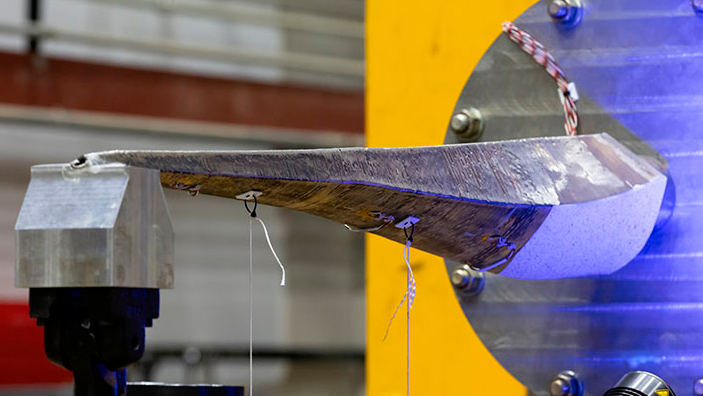
The 3D-printed stainless steel tidal turbine spar undergoes testing at NREL. Photo by Joe DelNero, NREL
1. Introduction to the Case Study: A Tidal Turbine Blade Case with Meltio Additive Manufacturing
The National Renewable Energy Laboratory (NREL) has adopted the Wire-Laser Metal Deposition (LMD) process from Meltio for the production of critical components made from Stainless steel.
In this specific project, NREL focused on the design and manufacture of a structural spar for an axial-flow tidal turbine blade, which is integral to harnessing energy from water movement. Traditionally, these components are machined from solid blocks of aluminium. However, the team sought to explore the advantages of 3D printing to achieve faster and more efficient production.
Specifically, the project aimed to design, model, develop, and manufacture a 3D-printed structural spar for an axial-flow tidal turbine blade, a key structural part inside the turbine blade, which is used to generate energy from the movement of water.
Think of it as the backbone of the blade, designed to handle the forces that the blade will face when it’s spinning in the water. Constructed from 316L stainless steel using the LMD process, this component is designed to withstand heavy loads and pressures from water currents without compromising structural integrity.
2. From concept to creation: From design to final product
2.1. Designing the Spar
First, the team had to create a design for the spar. They based it on a specific tidal turbine blade model called MHKF1 (named MHK-Family 1, or MHKF1). It will have a 2.5 m diameter rotor (see image below) with a rated power of 25 kW. The blades themselves are 1.05 m long and incorporate several novel design features to reduce cavitation, erosion, and noise generation.
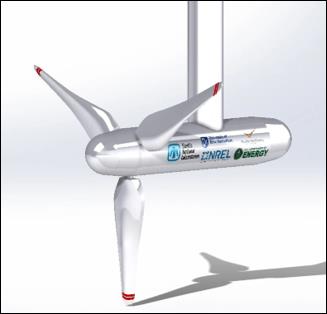
A computational rendering of the MHKF1 turbine with 2.5 m rotor diameter
Credits: Sandia National Laboratories
This design was very detailed because the spar had to fit inside the blade and handle the forces it would experience in the water. They used computer models to test how strong the design would be.
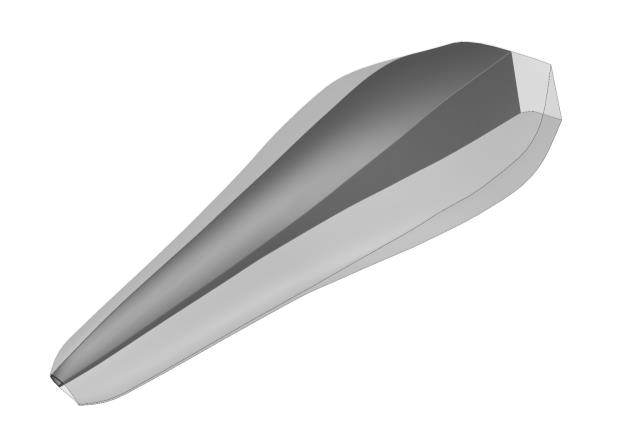
Geometric definition of structural spar within the MHKF1 blade
Early tests showed that the blade experienced significant bending and shear forces (3.9 kN·m and 5.6 kN), making it clear that strong, high-performance materials were needed to handle these forces. This remains true even if the blade is 3D-printed as a single part, due to the hydrodynamic loads it must withstand.
2.2. Material selection
The process of material selection for the tidal turbine blade spar was done carefully to ensure the spar could withstand the harsh marine environment and the loads it would face.
The spar is a critical structural part of the turbine blade, so the material had to meet several important criteria: strength, corrosion resistance, durability and manufacturability.
To determine the ideal AM processes for producing the MHKF1 blade, a decision matrix approach was taken (a scoring system where they listed all the important material properties (strength, resistance to corrosion, toughness, etc.). Key criteria for the manufacturing of the blade were given weights in terms of importance, ranging from 0 to 4, based on how important it was for the spar’s performance in the water.
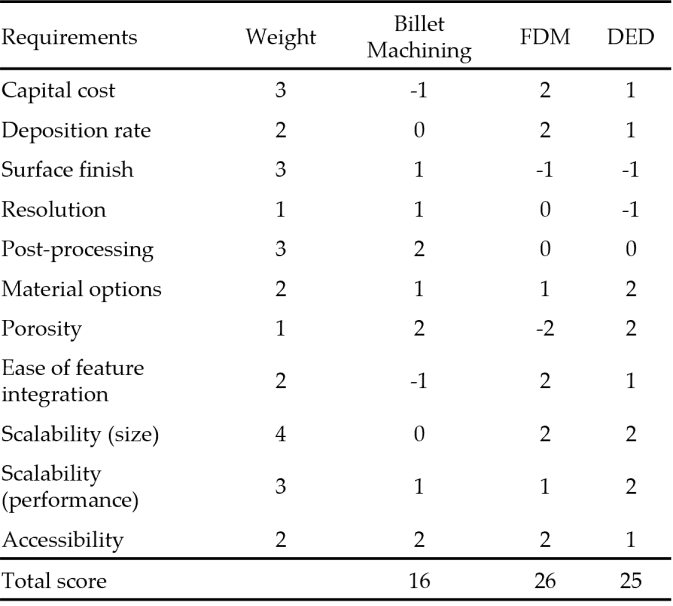
The AM Process Decision Matrix with billet machining as the reference manufacturing process
The team considered several materials, including polymers and metals. However, after deciding on the design and evaluating various metals, the team chose 316L stainless steel for several reasons:
- Corrosion resistance: 316L Stainless steel is very resistant to corrosion, which is perfect for the spar.
- High strength: It is a strong metal that can withstand the forces the spar will face, including heavy bending and twisting from the water currents.
- Compatibility with W-LMD Process: 316L Stainless steel works well with Meltio’s Laser Metal Deposition process. The metal can be fed in wire form and melted layer by layer to create the spar, and it provides the necessary strength once printed.
In the end, 316L Stainless Steel was selected because it provided the best combination of strength, corrosion resistance, and compatibility with the Meltio 3D printing process. This material choice ensured that the spar could handle the marine environment while being cost-effective and easy to manufacture with 3D printing. Furthermore, recommended tested parameters were given by Meltio.
TIP: Discover the full range of Meltio Materials and its properties by visiting the Meltio Materials page.
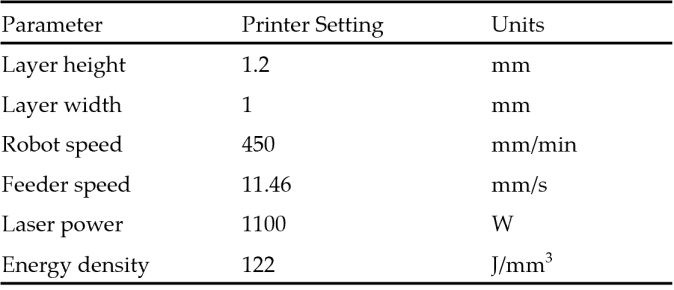
Printing Process Parameters: Recommended by Meltio for 316L Stainless Steel
2.3. Using Meltio’s W-LMD process with the Meltio Engine system
The structural blade spar was manufactured by Ai-Build with a Meltio wire-laser metal 3D Printer, the Meltio Engine mounted to a Kuka robotic system.
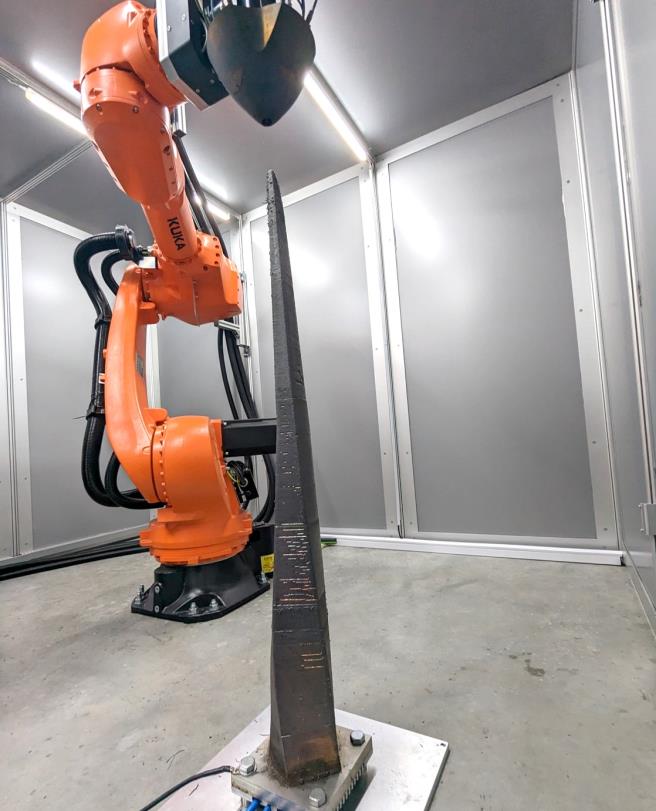
The structural box spar print, complete with the Kuka/Meltio LMD system.
Credits: Ai-Build
The printing was done using the Meltio W-LMD system, where a laser melts metal wire (in this case, Stainless steel) and deposits it layer by layer to create the part. The Meltio printer was mounted on a Kuka robotic arm, which helped guide the laser precisely along the shape of the spar.
The spar was printed with double walls and a 100% solid metal core for added strength. Extra layers were included at the base to facilitate easy removal from the printing plate. Throughout the process, 1 mm diameter 316L stainless steel wire was fed into the system, with the laser melting and precisely placing it to form the spar’s shape.
2.4. Challenges and limitations
Although the printing process went smoothly overall, there were some challenges:
- Surface defects: In some areas of the spar, especially where there were overhangs (sections of the part without support underneath), defects like waviness on the surface appeared. This happened because the molten steel sagged slightly without enough support below it. (see pictures A and B).
- Warpage of the base plate: After printing, they noticed that the base plate, where the spar was attached during the build, had warped due to the high heat involved in the LMD process. This warping created some challenges in removing the spar cleanly from the plate. (see picture C).
- Excess heat at the tip: As the spar tapered toward the tip, the cross-section became smaller, and the part didn’t have enough time to cool between layers. This caused excess metal to accumulate in certain spots, leading to surface defects. (see picture D).

Defects observed in the final print: (a) interior waviness, (b) exterior waviness, (c) base plate warpage and (d) excess wire at the tip
Photos: Phil Barden / Ai-Build // Paul Murdy / French Navy // Credits: Ai-Build and NREL
Solutions to these challenges
The final spar turned out to be structurally sound, despite the surface defects. The printed spar demonstrated that Meltio’s W-LMD process could produce large, complex parts suitable for marine environments, though a few areas could be improved:
- Reducing surface defects: The team suggested that in future prints, they could adjust the layer height, laser power, or even change the part’s orientation during printing to reduce these defects.
- Managing heat: They realized that by increasing the cooling time between layers near the tip or improving the calibration of the lasers, they could prevent some of the excess metal buildup and improve the quality of the print.
2.5. Post-processing phase
After the spar was printed, it went through a post-processing phase:
- Cleaning: The outer surfaces of the spar were cleaned using a wire wheel and a flap disc attached to a grinder. This smoothed out the rough surfaces caused by the printing process (see picture A).
- Drilling and tapping: The root of the spar (the base) needed mounting holes for bolts to attach it to the turbine. To avoid disrupting the printing process, these holes weren’t printed. Instead, they were drilled and tapped afterwards using CNC machining to ensure accuracy (see picture C).
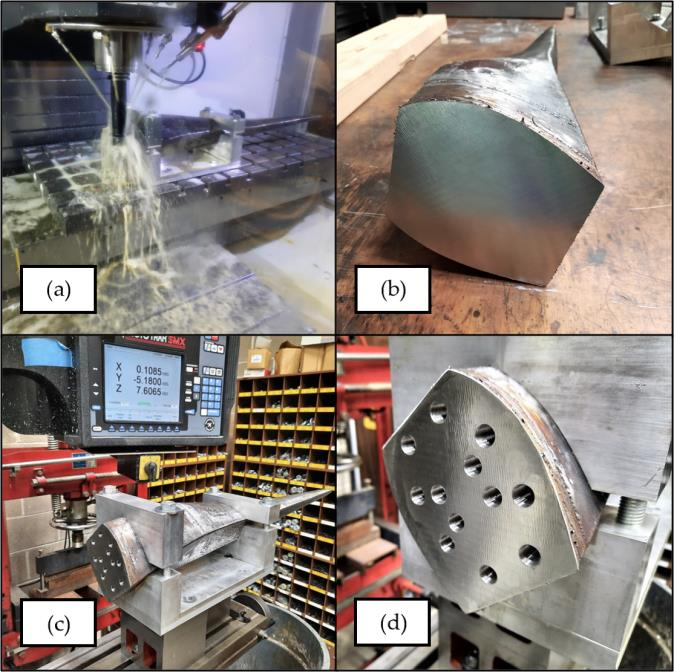
The final machine steps to complete the spar:
(a) base plate removal, (b) the resulting flat root surface, (c) drilling and tapping the root mount holes, and (d) the final completed root face.
Photos: Paul Murdy // Credits: NREL
2.6. Final machining and testing
Once the spar was printed and cleaned, the final step was to remove the base plate and make sure the root face was flat. Now, that the final machining processes are complete, the spar will be mounted to a test stand and subjected to a rigorous structural validation program and ensure it could handle the loads it would face in the real world.
“Structural validation is critical to ensuring that the spar will react to real-life forces in the way that our models predict,” Murdy said. “It also helps us understand how the novel additive manufacturing process differs from conventional steel manufacturing techniques and how we can account for it in future designs.”
3. Conclusion: A reliable design process that broadens the horizons for MRE technologies
The use of Directed Energy Deposition (DED) technology, and more specifically Meltio’s W-LMD in the development of complex marine structures, represents a significant advancement, particularly for the ocean energy sector.
The successful manufacturing of a full-scale structural spar for the MHKF1 turbine blade demonstrates the capability of DED to produce intricate geometries that are unachievable through conventional methods, thus supporting Powering the Blue EconomyTM initiatives of the U.S. Department of Energy Water Power Technologies Office.
Murdy said: “We’ve opened a really unique design space through 3D printing”. “This project has demonstrated that additive manufacturing has the potential to produce very strong, stiff structures that will be good for marine energy.”
While surface finish issues, thermal stress-induced warping, and other challenges inherent to DED were identified, these findings provide valuable insights for future iterations. The National Renewable Energy Laboratory’s innovative approach sets a new benchmark for both the marine and other industries, proving that robust, customized solutions can be delivered efficiently. This work also highlights the importance of addressing scalability and material limitations in extreme environments, which will undoubtedly guide the evolution of 3D-printed Marine Renewable Energy (MRE) components moving forward.
In conclusion, this research establishes a benchmark process for leveraging additive manufacturing in the development of marine hydrokinetic structures, setting the stage for future optimization and techno-economic analysis.
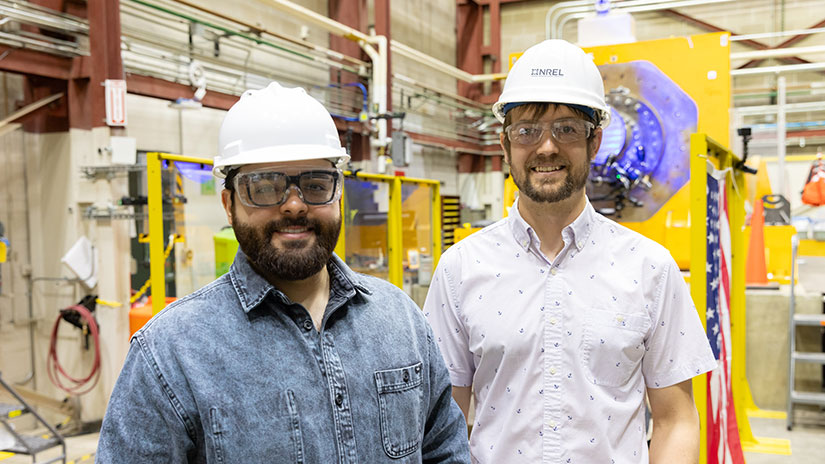