Meltio
Robot Cell
Advanced Additive Manufacturing System
An affordable turn-key solution powered by the Meltio Engine Integration kit for Industrial Robots. It is designed to provide industries with a secure and efficient solution for manufacturing metal 3D printed parts.
The Meltio Engine Robot Cell is the most versatile and capable solution for 3D printing, repair, cladding, and feature addition.
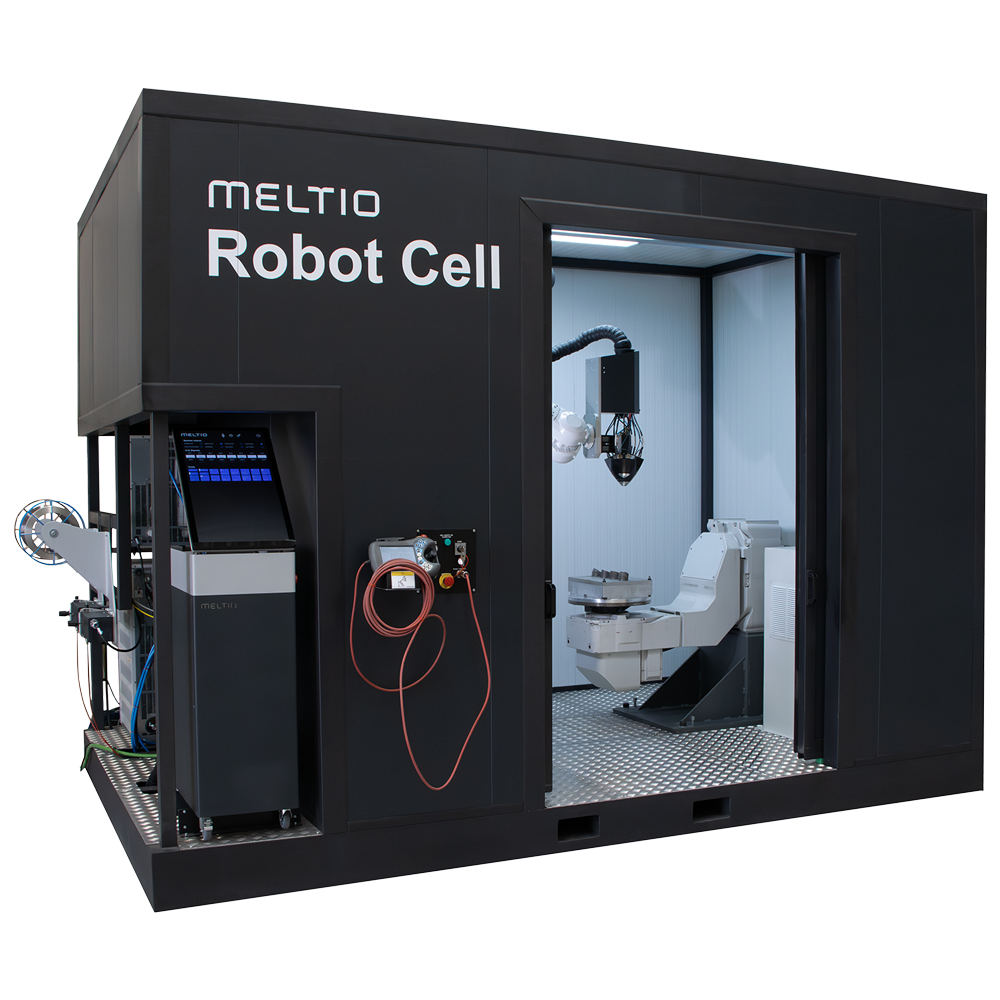
Efficiency Redefined
Reduce integration risk, product standardization and simplify the adoption of
technology, removing the lengthy integration process and long assembly lead times.
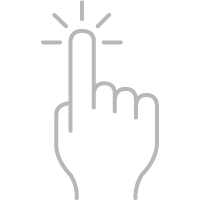
Plug and Play Installation
Allows the customer to receive a ready to use cell for robotic metal 3D printing.

Safe, Tested & Certified
In accordance with European CE and laser safety regulations and multiple quality controls.
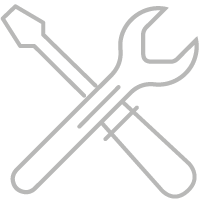
Best Components
Robot and positioner on a self-supporting platform, laser safe enclosure.
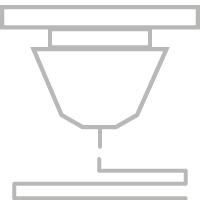
Focus on Printing
On-site training for enabling the end user to be successful with Meltio and develop applications in short time.
Technical Specifications
CLASS 1 Laser Product.
Meltio Space 1 (one) year subscription.
Large 3D Printing Volume with Continuous positioner axes interpolation.
All equipment and peripherals anchored on the platform.
Standard CE certification.
Steel platform with leveling points and wiring ducts.
All cell controls unified on single control panel.
Everything is sent integrated and tested.
The final reseller/integrator focuses work on training and enabling the client to manufacture parts.
Load and unload from truck with regular size and load forklift.
Includes 300x400mm actively cooled build platform and buildplates.
Power Input:
Three phase 400V 50Hz
5 poles (3W+N+PE)
Protection up to 50A 20kw peak power consumption
Average power consumption at 15-18 A: -> 7kw
Alternative Power Input Upon Request:
Three phase 440V 60Hz 5 poles (3W + N + PE)
Three phase 230V 60Hz 3 poles (3W)
General dimensions:
4.050 x 2.350 x 3.000 mm
Prepared to support the weight of the Cell and its components without deformations.
Includes leveling points.
Resistant to oxidation or protected for this purpose.
Ducts for wiring and integration elements, allowing a clean floor.
Laser safe enclosure according to IEC 60825-1 and IEC 60825-4.
Robot Cell product as Class 1 reducing the risks for the user.
Highly fire-resistant enclosure materials that do not
produce toxic particles.Specifically: B-s2,d0 according to UNE EN 13501-1
Single three-phase connector input.
All cell controls unified on single control panel:
– Cell Controls: Open doors and arm security
– Robot Controls: Motors On, Mode Selector and Emergency
Connected to the customer’s local network (LAN) for PC interconnectivity.
ABB’s SafeMove to avoid collisions with enclosure.
Safe environment for the end customer.
European CE and laser safety regulations.
UCKA in UK and UL in America to be evaluated.
Laser safe enclosure according to IEC 60825-1 and IEC 60825-4.
Fully Tested.
Specific Quality Controls before and after integration, ensuring maximum performance at its final destination.
Meltio Engine Control Unit.
Engine and Build Platform Water Chillers.
External Feeders, for spool holders and drums of +100kg
Inert Gas Supply options:
– Attachments for three 50L Argon bottles with non-return valves.
– Optional Meltio Gas Regulator
– Or Supplied by customer
* All these equipment and peripherals are anchored on this platform and may not exceed from the maximum dimensions of the self-supporting platform during transport.
Load:
500 kg max load (Standard)
No Positioner Interpolation:
2000 x 1000 x 1000 mm
Custom build platform not included
No positioner movement, only robot tool orientation
Positioner Interpolation:
⌀ 1000 mm x 1200 mm
Actively Cooled Build Platform:
Buildplate 300x400mm
Buildplate 150x200mm
Buildplate 120x100mm
* The cooling bed allows control of the temperature of the prints as wells to protect the positioner, hardware that cannot be over 70ºC on periods of more than 24h.
Updated and renewed User Interface.
Custom profiles without the need of writing macros, every possibility parametrized.
HD Webcam.
Compatible with Welding Camera.
Timeline for Sensors Analysis.
Live 3D model based on reading TCP positions from robot.
Profiles for Meltio Materials and Meltio Space.
Key Technical Features
CLASS 1 Laser Product.
Meltio Space 1 (one) year subscription.
Large 3D Printing Volume with Continuous positioner axes interpolation.
All equipment and peripherals anchored on the platform.
Standard CE certification.
Steel platform with leveling points and wiring ducts.
All cell controls unified on single control panel.
Everything is sent integrated and tested.
The final reseller/integrator focuses work on training and enabling the client to manufacture parts.
Load and unload from truck with regular size and load forklift.
Includes 300x400mm actively cooled build platform and buildplates.
Electrical requirements
Power Input:
Three phase 400V 50Hz
5 poles (3W+N+PE)
Protection up to 50A 20kw peak power consumption
Average power consumption at 15-18 A: -> 7kw
Alternative Power Input Upon Request:
Three phase 440V 60Hz 5 poles (3W + N + PE)
Three phase 230V 60Hz 3 poles (3W)
Structure and Enclosure
General dimensions:
4.050 x 2.300 x 3.000 mm
Self-supporting steel platform (4050 mm length x 2550 mm width).
Prepared to support the weight of the Cell and its components without deformations.
Includes leveling points.
Resistant to oxidation or protected for this purpose.
Ducts for wiring and integration elements, allowing a clean floor.
Laser safe enclosure according to IEC 60825-1 and IEC 60825-4.
Robot Cell product as Class 1 reducing the risks for the user.
Highly fire-resistant enclosure materials that do not
produce toxic particles.Specifically: B-s2,d0 according to UNE EN 13501-1
Integration and Safety
Single three-phase connector input.
All cell controls unified on single control panel:
– Cell Controls: Open doors and arm security
– Robot Controls: Motors On, Mode Selector and Emergency
Connected to the customer’s local network (LAN) for PC interconnectivity.
ABB’s SafeMove to avoid collisions with enclosure.
Safe environment for the end customer.
European CE and laser safety regulations.
UCKA in UK and UL in America to be evaluated.
Laser safe enclosure according to IEC 60825-1 and IEC 60825-4.
Fully Tested.
Specific Quality Controls before and after integration, ensuring maximum performance at its final destination.
Supplies Area
Meltio Engine Control Unit.
Engine and Build Platform Water Chillers.
External Feeders, for spool holders and drums of+100kg
Inert Gas Supply options:
– Attachments for three 50L Argon bottles with non-return valves.
– Optional Meltio Gas Regulator
– Or Supplied by customer
* All these equipment and peripherals are anchored on this platform and may not exceed from the maximum dimensions of the self-supporting platform during transport.
Load and Build Volume
Load:
500 kg max load (Standard)
No Positioner Interpolation:
2000 x 1000 x 1000 mm
Custom build platform not included
No positioner movement, only robot tool orientation
Positioner Interpolation:
⌀ 1000 mm x 1200 mm
Actively Cooled Build Platform:
Buildplate 300x400mm
Buildplate 150x200mm
Buildplate 120x100mm
* The cooling bed allows control of the temperature of the prints as wells to protect the positioner, hardware that cannot be over 70ºC on periods of more than 24h.
Engine Software
Updated and renewed User Interface.
Custom profiles without the need of writing macros, every possibility parametrized.
HD Webcam.
Compatible with Welding Camera.
Timeline for Sensors Analysis.
Live 3D model based on reading TCP positions from robot.
Profiles for Meltio Materials and Meltio Space.
Laser System Specifications
New! Meltio Engine Blue Integration kit
Laser System:
Blue Laser (Higher absorption and power efficiency; wider range of compatible materials than IR)
1000W 9 x 450 nm direct diode lasers
Printhead:
Robot Mounted 20.5 to 23 kg
Printhead Size (WxDxH):
262 x 272 x 572 mm
Control Unit:
Wall mounted, air-cooled 80.5 kg 600 x 300 x 800 mm. Separate wall mounted 27″ HMI
Cooling:
Water-cooled deposition head. Chiller lncluded
Print Envelope (WxDxH):
Depending on robot’s reach
Process Control:
Melt Pool Camera & Closed-loop wire modulation
Power Input:
200/240 V 3W+PE 380/415 V 3W+N+PE
Power Consumption:
9,2 kW peak 2-5 kw avg.
Slicer Software:
Meltio Space 1-year subscription lncluded
Feeder System:
Quad-point traction servomotor feeder, frictionless liners
Wire Feedstock:
Diameter: 0.8-1.2 mm / Spool Type: 8S300 External wire drum ready
Product Configurations:
Single or Dual Wire
Compatible Materials:
Stainless Steels, Carbon Steels, Tool Steels, Nickel Alloys, Titanium, Copper Alloys, Gold alloys and more
Meltio Engine IR Integration kit
Laser System:
Infrarred Laser
1200W 6 x 976 nm direct diode lasers + fibers & colimators
Printhead:
15.5 kg
Printhead Size (WxDxH):
230 x 310 x 710 mm
Control Unit:
Floor Mounted (Wheeled) 125 kg with 27″ HMI 390 x 650 x 1600 (deployed screen)
Cooling:
Water-cooled control unit and deposition head. Chiller included
Print Envelope (WxDxH):
Depending on robot’s reach
Process Control:
Closed-loop, wire modulation
Power Input:
200/240 V 3W+PE 380/415 V 3W+N+PE
Power Consumption:
2 – 5 kW peak depending on selected options
Slicer Software:
Meltio Space 1-year subscription lncluded
Feeder System:
Dual traction stepper motors + External Feeder (Push-pull system), conventional wire liners
Wire Feedstock:
Diameter: 0.8-1.2 mm / Spool Type: 8S300 External wire drum ready
Product Configurations:
Single or Dual Wire
Compatible Materials:
Stainless Steels, Carbon Steels, Tool Steels, Nickel Alloys, Titanium and more
New! Meltio Engine Blue Integration kit
General Specifications
Laser System:
Blue Laser (Higher absorption and power efficiency; wider range of compatible materials than IR)
1000W 9 x 450 nm direct diode lasers
Printhead:
Robot Mounted 20.5 to 23 kg
Printhead Size (WxDxH):
262 x 272 x 572 mm
Control Unit:
Wall mounted, air-cooled 80.5 kg 600 x 300 x 800 mm. Separate wall mounted 27″ HMI
Cooling:
Water-cooled deposition head. Chiller lncluded
Print Envelope (WxDxH):
Depending on robot’s reach
Process Control:
Melt Pool Camera & Closed-loop wire modulation
Power Supply
Power Input:
200/240 V 3W+PE 380/415 V 3W+N+PE
Power Consumption:
9,2 kW peak 2-5 kw avg.
Materials and Software
Slicer Software:
Meltio Space 1-year subscription lncluded
Feeder System:
Quad-point traction servomotor feeder, frictionless liners
Wire Feedstock:
Diameter: 0.8-1.2 mm / Spool Type: 8S300 External wire drum ready
Product Configurations:
Single or Dual Wire
Compatible Materials:
Stainless Steels, Carbon Steels, Tool Steels, Nickel Alloys, Titanium, Copper Alloys, Gold alloys and more
Meltio Engine IR Integration kit
General Specifications
Laser System:
Infrarred Laser
1200W 6 x 976 nm direct diode lasers + fibers & colimators
Printhead:
15.5 kg
Printhead Size (WxDxH):
230 x 310 x 710 mm
Control Unit:
Floor Mounted (Wheeled) 125 kg with 27″ HMI 390 x 650 x 1600 (deployed screen)
Cooling:
Water-cooled control unit and deposition head. Chiller included
Print Envelope (WxDxH):
Depending on robot’s reach
Process Control:
Closed-loop, wire modulation
Power Supply
Power Input:
200/240 V 3W+PE 380/415 V 3W+N+PE
Power Consumption:
2 – 5 kW peak depending on selected options
Materials and Sofware
Slicer Software:
Meltio Space 1-year subscription lncluded
Feeder System:
Dual traction stepper motors + External Feeder (Push-pull system), conventional wire liners
Wire Feedstock:
Diameter: 0.8-1.2 mm / Spool Type: 8S300 External wire drum ready
Product Configurations:
Single or Dual Wire
Compatible Materials:
Stainless Steels, Carbon Steels, Tool Steels, Nickel Alloys, Titanium and more
Meltio Space Software
This toolpath generator software is specifically developed for accelerated adoption of Meltio technology, revolutionizes the field of robotic additive manufacturing. With its intuitive design, users can quickly adapt to and leverage the benefits of robotic additive manufacturing without requiring expertise in robotics or programming.
Meltio Space Software
This toolpath generator software is specifically developed for accelerated adoption of Meltio technology, revolutionizes the field of robotic additive manufacturing. With its intuitive design, users can quickly adapt to and leverage the benefits of robotic additive manufacturing without requiring expertise in robotics or programming.
Meltio Robot Cell Applications
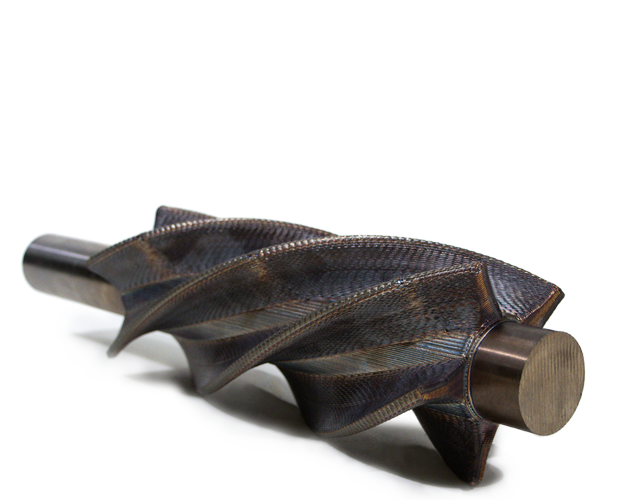
Rotary Screw Compressor
SS316L
Size:
75 x 75 x 230 mm cladded
Weight:
3 kg
Print time:
21h 16′
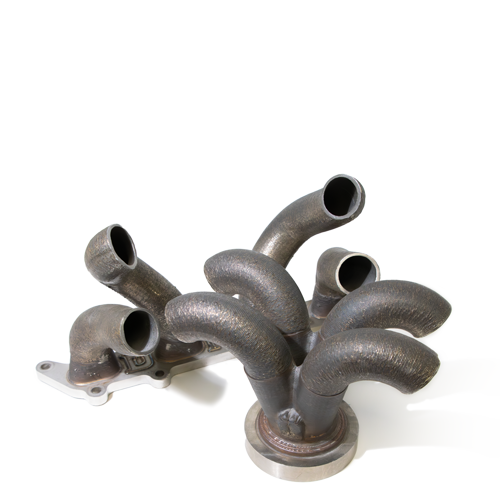
High Performance Exhaust Header
SS308L
Size:
160 x 326 x 190 mm
Weight:
4.5 kg
Print time:
19h 0.5′
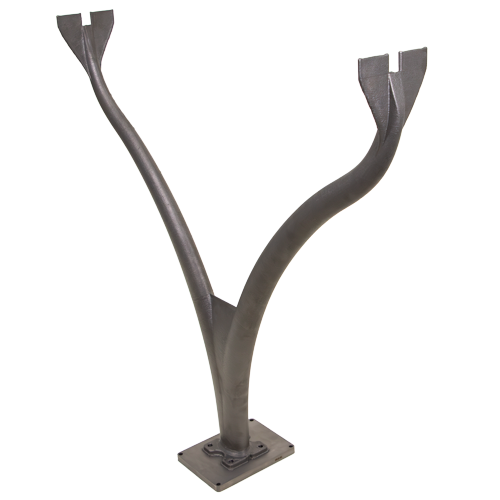
Belt Conveyor Support
SS316L
Size:
130 x 903 x 855 mm
Weight:
5 kg
Print time:
28h 15′
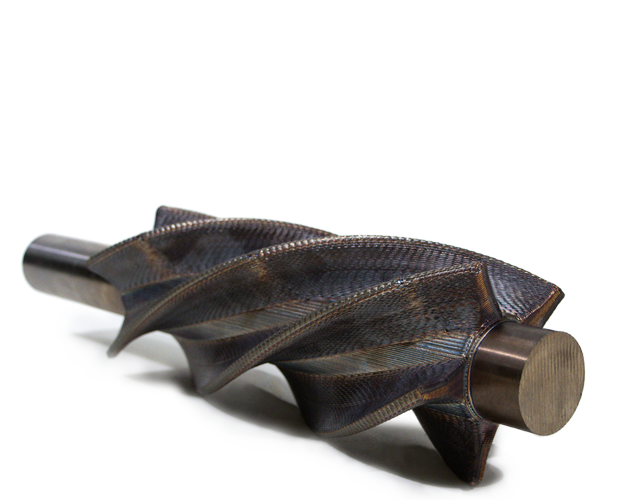
Rotary Screw Compressor
SS316L
Size:
75x 75 x 230 mm cladded
Weight:
3 kg
Print time:
21h 16′
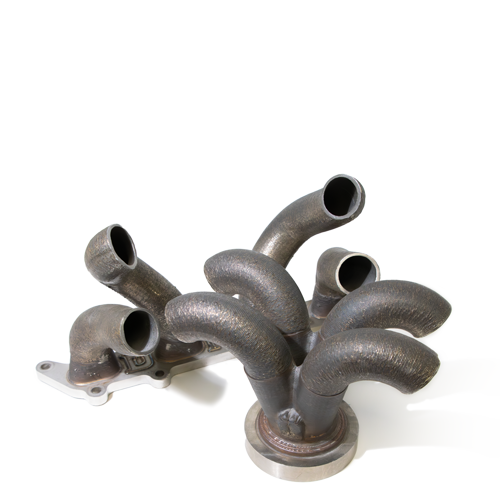
High Performance Exhaust Header
SS308L
Size:
160 x 326 x 190 mm
Weight:
4.5 kg
Print time:
19h 0.5′
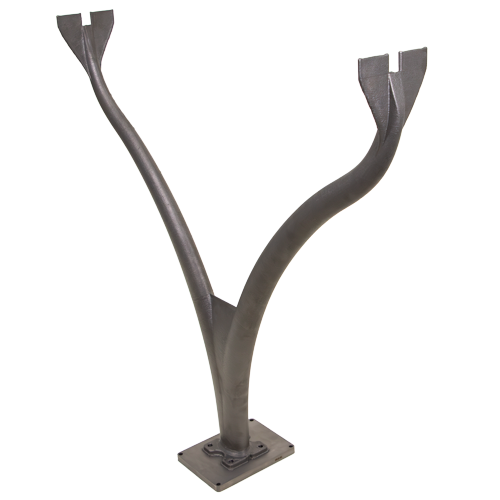
Belt Conveyor Support
SS316L
Size:
130 x 903 x 855 mm
Weight:
5 kg
Print time:
28h 15′
Webinar
Meltio Robot Cell
Meltio presents a webinar about our new Meltio Robot Cell, an affordable turn key solution for Meltio Engine Robot Integration.
Webinar
Meltio Robot Cell
Meltio presents a webinar about our new Meltio Robot Cell, an affordable turn key solution for Meltio Engine Robot Integration.
Laser Alignment System
The Laser Alignment System is a product developed by Meltio to aid the adoption of our state-of-the-art wire-laser deposition technology as well as to ensure print process reliability and enhance user experience.
Laser Alignment System
The Laser Alignment System is a product developed by Meltio to aid the adoption of our state-of-the-art Wire-laser deposition technology as well as to ensure print process reliability and enhance user experience.
Meltio Materials
Meltio’s Laser Metal Deposition process achieves exceptional material mechanical properties using single, dual and quad wire. Choose the ideal welding wire for your application: unlimited third-party commodity material or qualified Meltio Wire Materials that secure the user experience.
Meltio Materials
Meltio’s Laser Metal Deposition process achieves exceptional material mechanical properties using single, dual and quad wire. Choose the ideal welding wire for your application: unlimited third-party commodity material or qualified Meltio Wire Materials that secure the user experience.
Metal 3D Printing Experiences
Miguel Peñaranda
Additive Manufacturing Engineer / K3D
” We chose the Meltio product because we found the best balance between high deposition rates and good quality for the task at hand.
Meltio represents for us the right balance between a high deposition speed as well as a high printing size with the best feasible quality or resolution. “
K3D is a Dutch Service Bureau that prints different parts for end-users across various industries using a Meltio M450 and a Meltio Engine Robot Integration.
Get a Quote
Meltio Robot Cell
Receive a tailor-made offer within 1 – 2 business days.
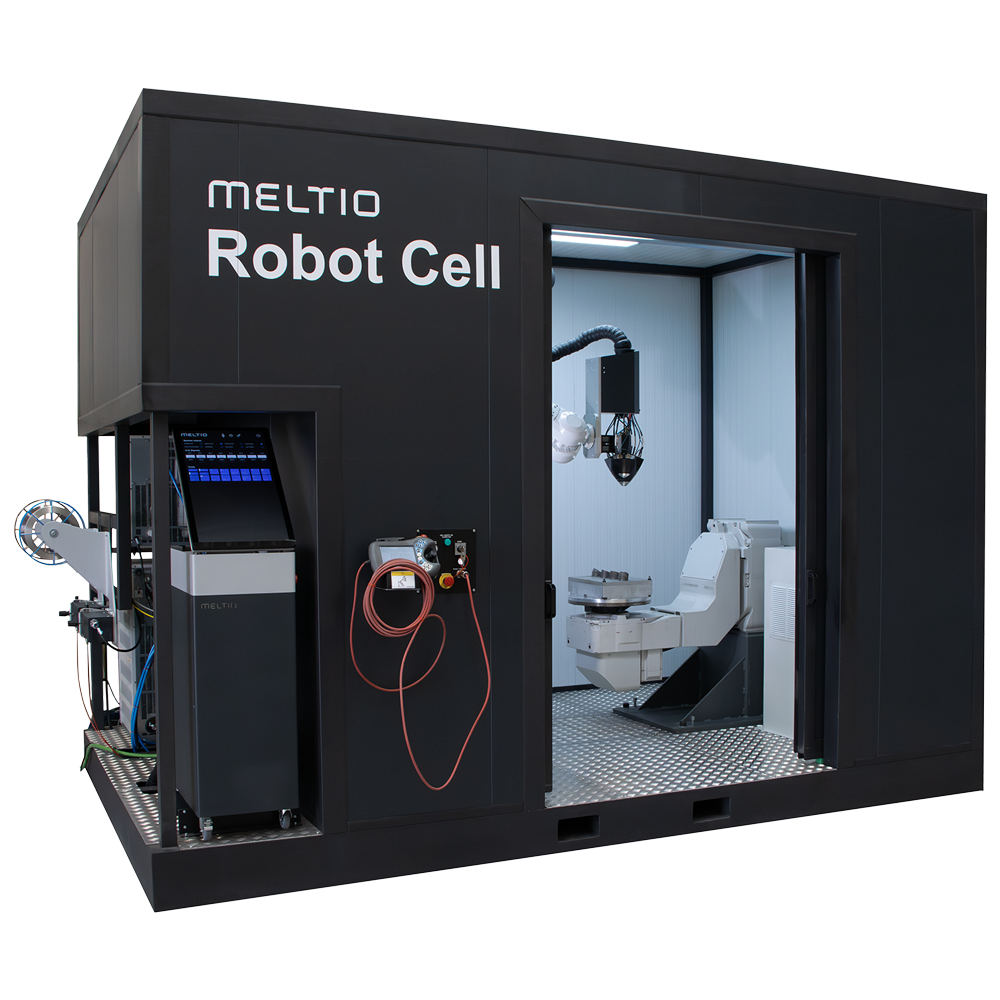