Cost and time saving solutions
through robotic metal 3D printing
Case study developed by DPR Automatismos
Cost and time saving solutions through robotic metal 3D printing
Case study developed by DPR Automatismos
In the competitive world of industrial automation, efficiency is everything. For DPR Automatismos, a leading Spanish integrator of robotic 3D metal printing solutions, this meant solving one of the most persistent bottlenecks in mold manufacturing: inefficient internal cooling.
By harnessing the power of Meltio’s wire-laser metal deposition technology, DPR produced a large-scale, fully functional mold insert featuring conformal cooling channels—geometry that traditional methods simply couldn’t manufacture. This use case demonstrates how additive manufacturing isn’t just enhancing legacy processes; it’s redefining what’s possible.
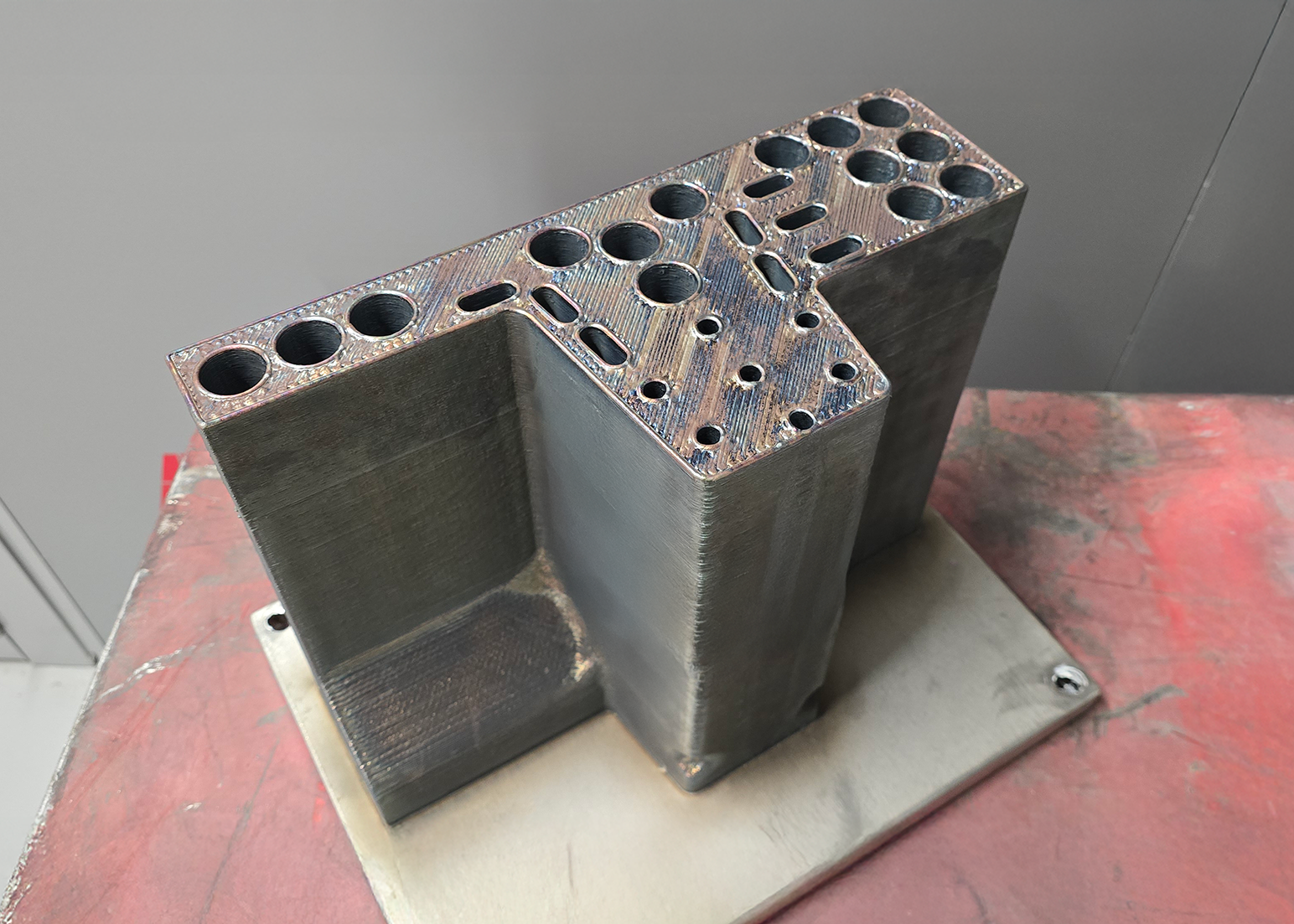
Tackling Thermal Challenges in Mold Design
A leading industrial client approached DPR Automatismos with a recurring issue:
Inefficient cooling
Resulting in prolonged cycle times and inconsistent product quality.
Tradicional cooling channels
They are no longer effective or viable for their increasingly complex mold geometries.
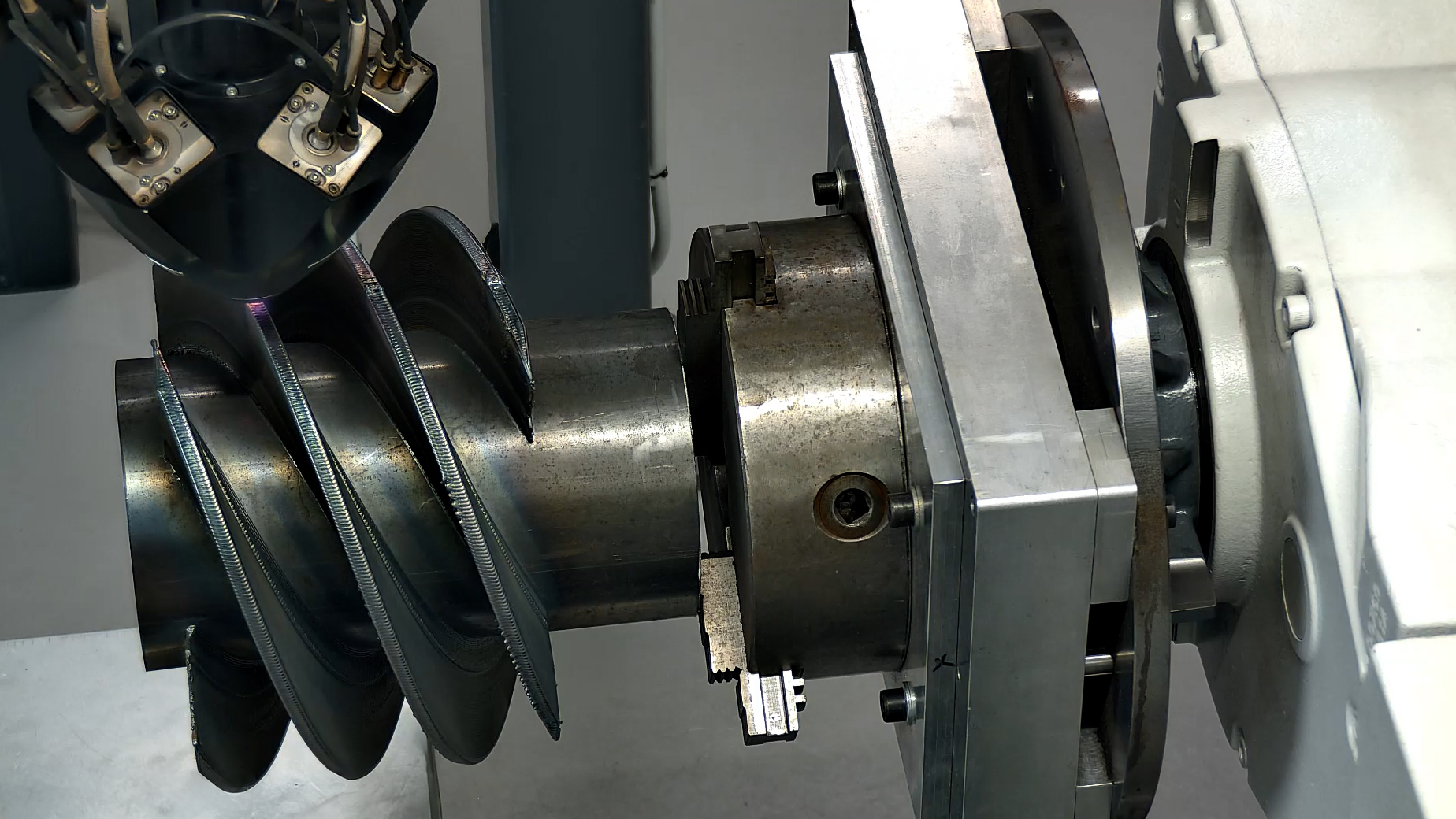
Why Robotic DED Was the Key Enabler
Enables integration of complex internal cooling channels
Maintains full structural integrity of the part
Eliminates the need for multi-part assembly
Robotic integration provides reach and flexibility
Ideal for geometries unachievable by machining
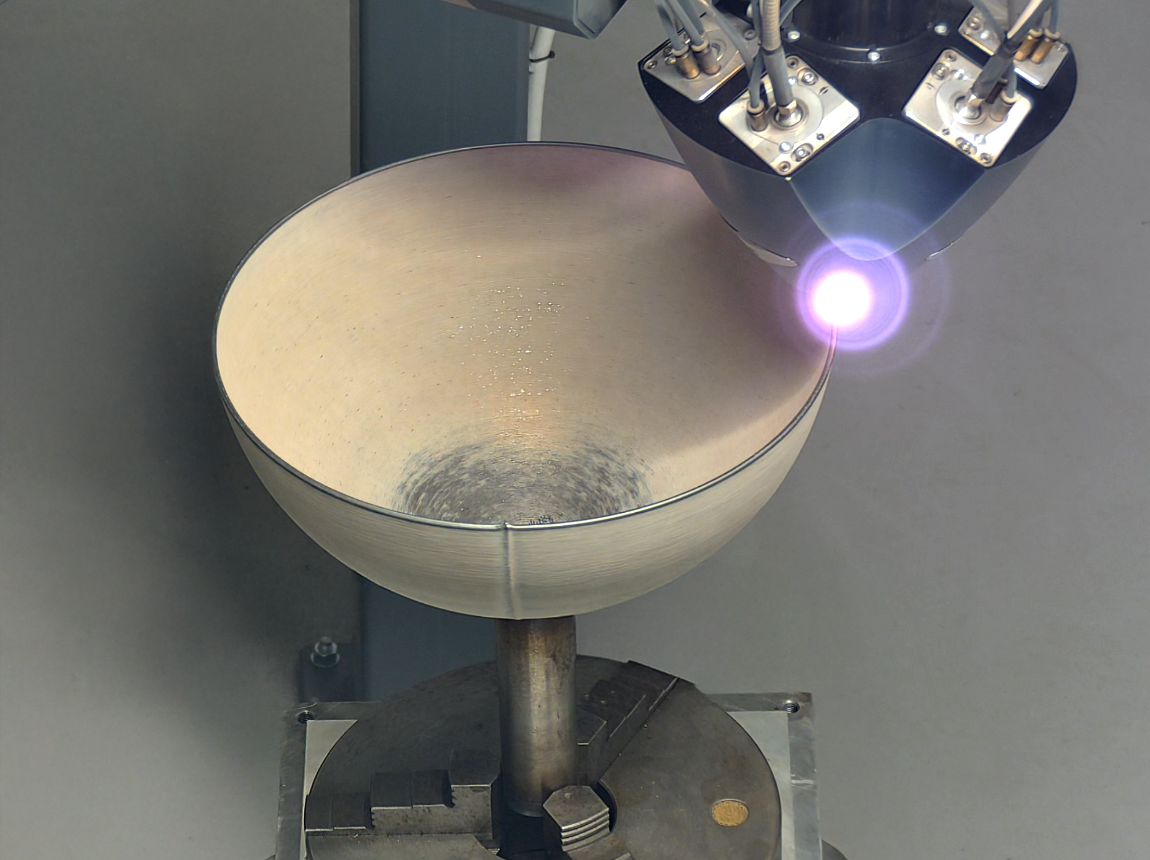
“This project validates how robotic metal 3D printing enables design freedom and functionality that traditional methods simply can’t match. We’re excited about the future of this technology in tooling.”
Meltio 3D Printing Solutions
Unlock the potential of metal 3D printing with Meltio. Your journey starts here.
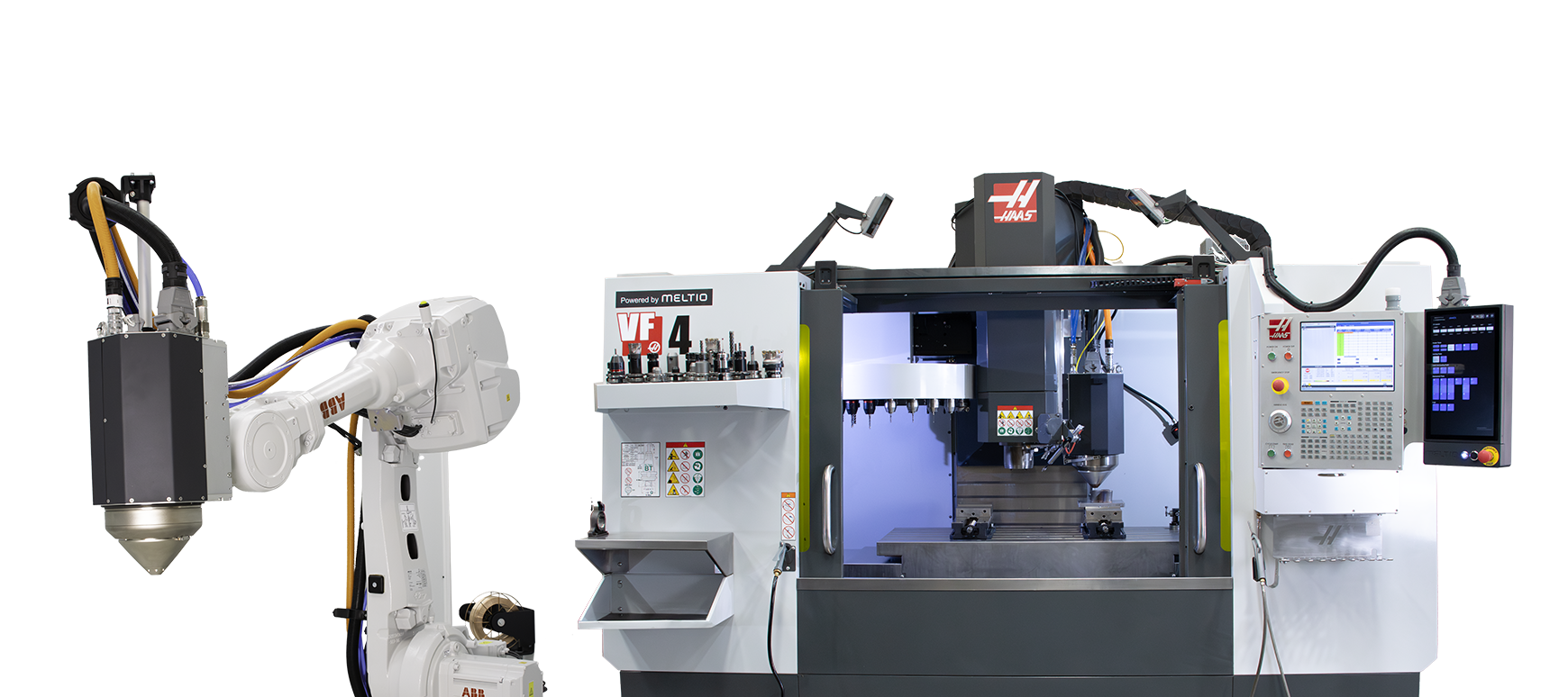
Meltio 3D Printing Solutions
Unlock the potential of metal 3D printing with Meltio. Your journey starts here.
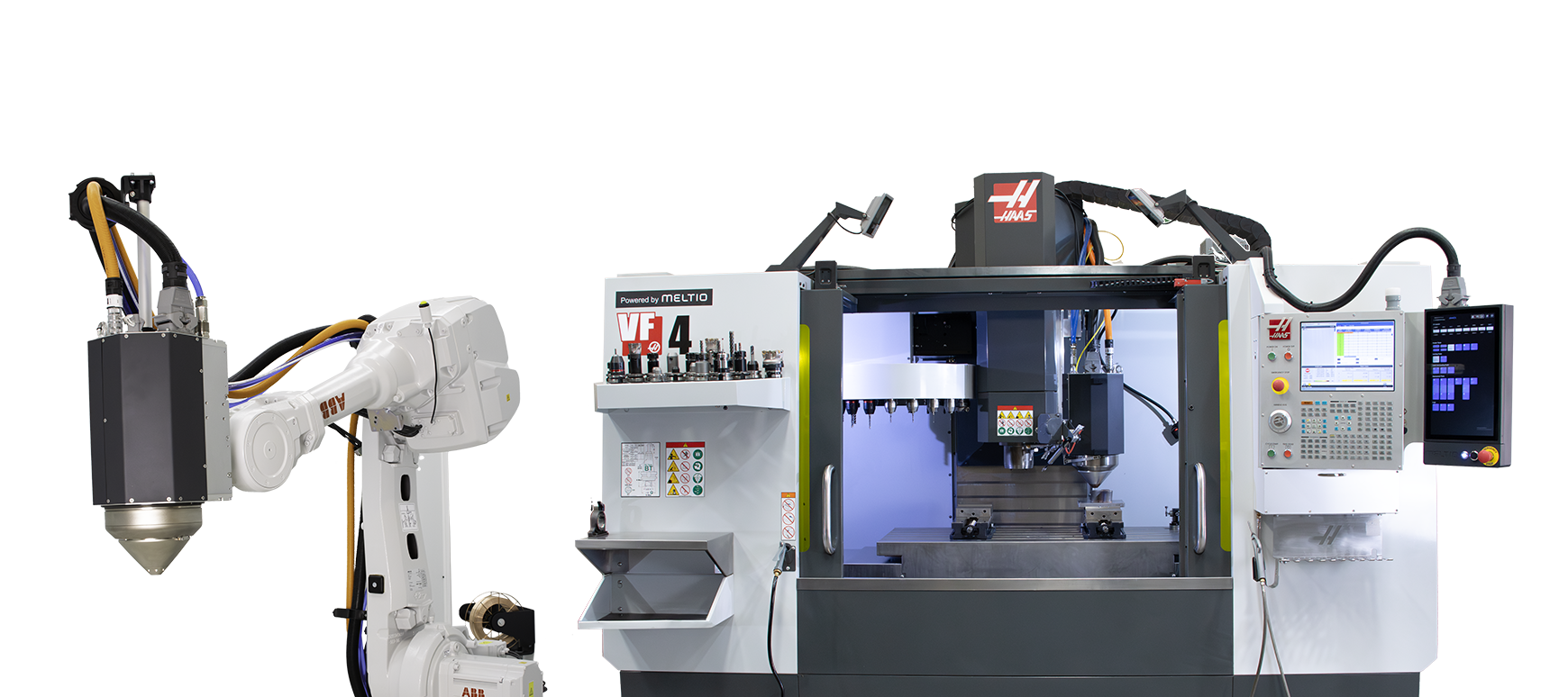
System: Meltio Engine Robot Integration
lt is the perfect platform for large and complex 3D printing, repair, cladding and feature addition.
Sector: Naval
On-site, on-demand production
Material: Stainless Steel 316L
Wire feedstock proves more affordable and safer than powder-based alternatives.
Printing Time: 30h
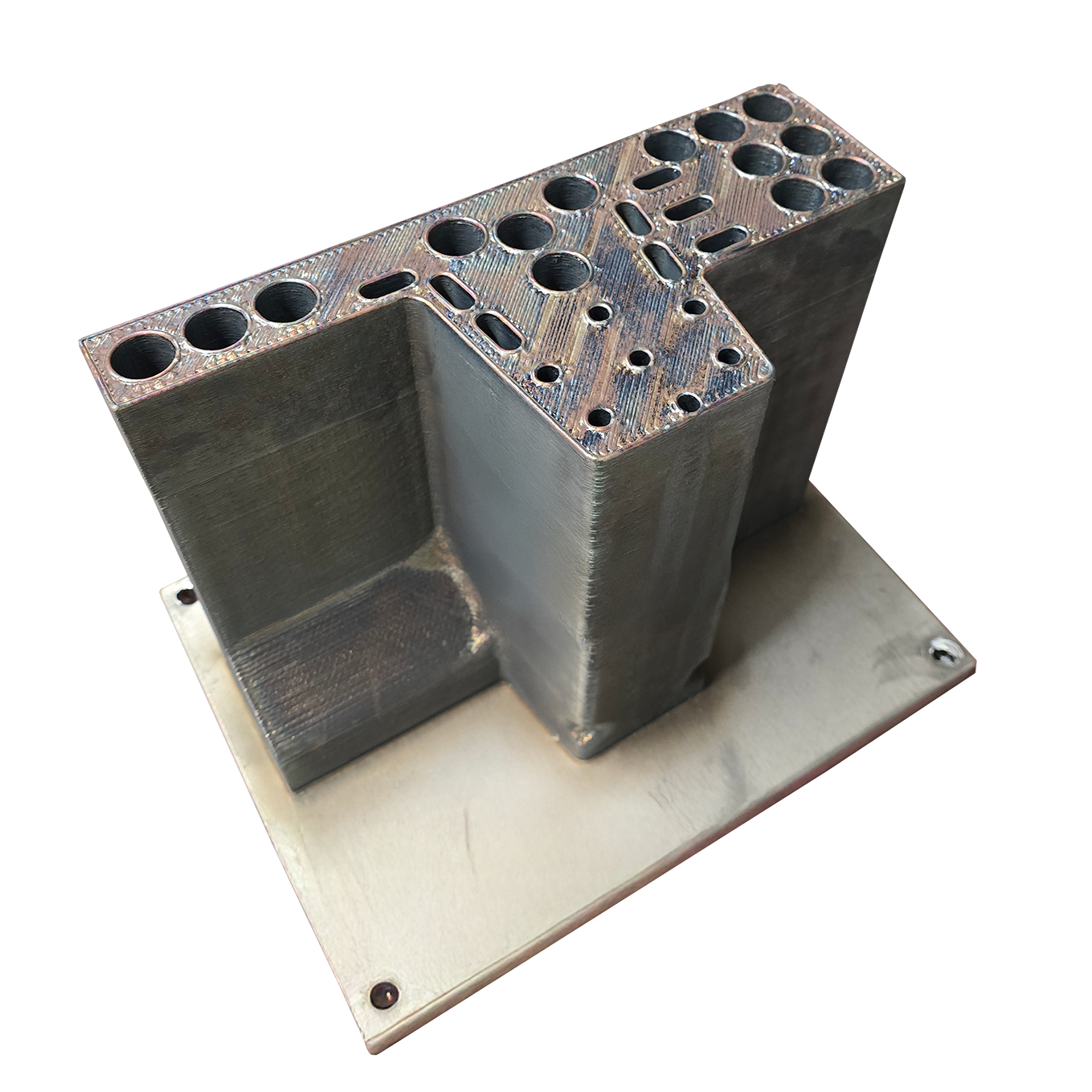
Validated Performance and Scalable Opportunity
The success of this proof-of-concept confirmed the feasibility of printing large-scale metallic components with internal features.
It marks a step-change in how tooling components can be produced, opening new opportunities for customers across plastics, die casting, and hot stamping industries.
DPR plans to scale this approach to other mold types and insert designs, continuously optimizing based on real-world testing.
Unlocking new applicatinons and industries
Redefines tooling production standards
Want to know more about printed parts properties?
Want to know more about printed parts properties?