On demand production
of eductors for naval systems
On demand production of eductors for naval systems
This entry continues our defense spare parts series, highlighting the redesign and additive manufacturing of an eductor — a fluid-pumping component often used in naval systems.
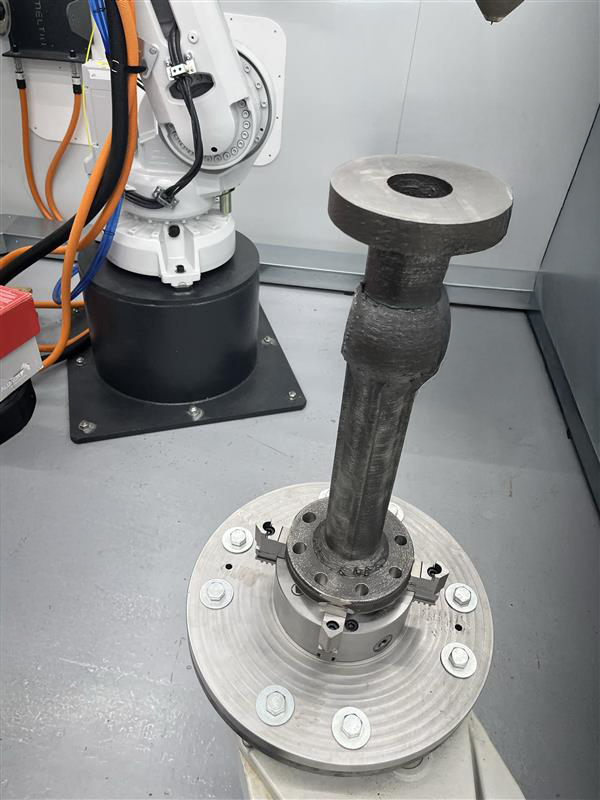
Eductors: The Hidden Workhorses of Naval Engineering
Eductors exploit the Venturi effect to move secondary fluids by creating low-pressure zones in high-speed primary flows. They operate without any moving parts or motors, making them simple, durable, and ideal for constrained systems.
High-wear and difficult to inspect
making preventive maintenance and replacements difficult to time
Usually in Cu-based alloys
involves long lead times and high costs for one-off units
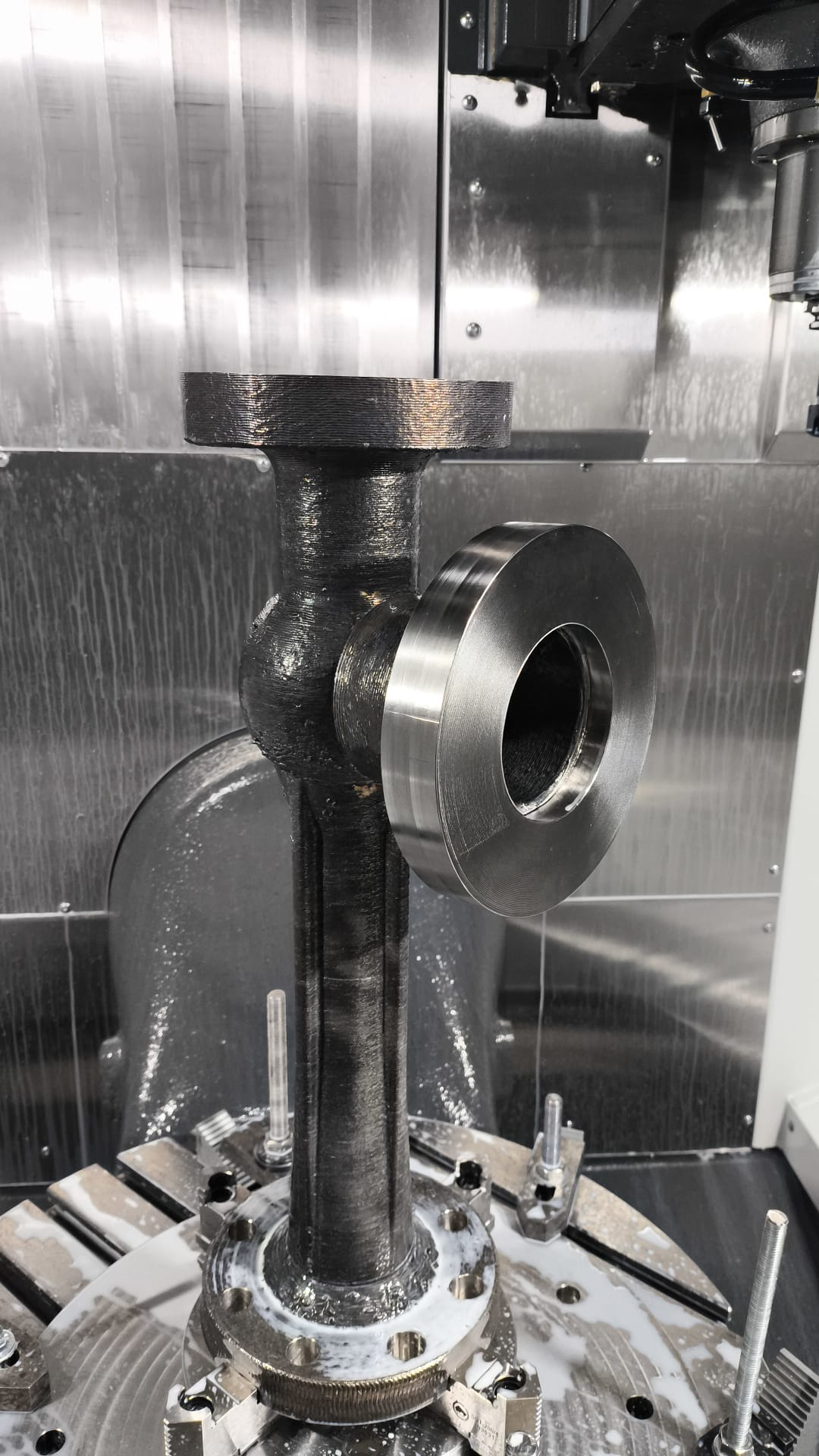
Meltio’s Additive Approach
Using its DED system, Meltio successfully printed an eductor using 316L stainless steel, replacing the need for casting. The part was printed in four distinct modules to ensure both printability and post-processing compatibility:
Main body (46h40m)
Printed with planar layers and tangent perimeters. The robot’s motion was optimized to avoid collisions, using a 35° cone limitation.
Top fixture (8h)
Radial strategy with linear infill. Requires a drilled side duct.
Suction duct (3h)
Built with non-planar strategy to minimize supports and improve surface finish
Side connection
Printed on Meltio M600, later welded to the main assembly. This could evolve into a threaded fixture to simplify final assembly.
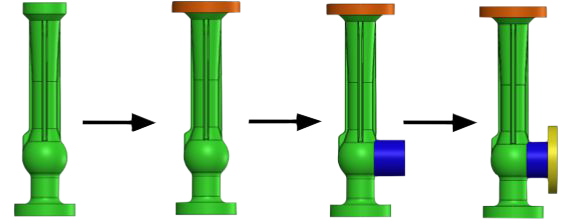
All segments were designed using Meltio Space, and the build followed a robust parameter set (1kW laser, 10 mm/s feed rate, 15 L/min argon shielding).
From Legacy Replica to AM-First Design
Two design iterations were produced:
- The first closely replicated the legacy casting, simplifying validation and testing.
- The second iteration was redesigned for additive manufacturing, with improved printability and machinability:
Optimized wall thickness
Elimination of overhangs
Integrated fixturing walls for CNC setup
Circular base to streamline multi-step printing
Drop-shaped holes for faster post-processing
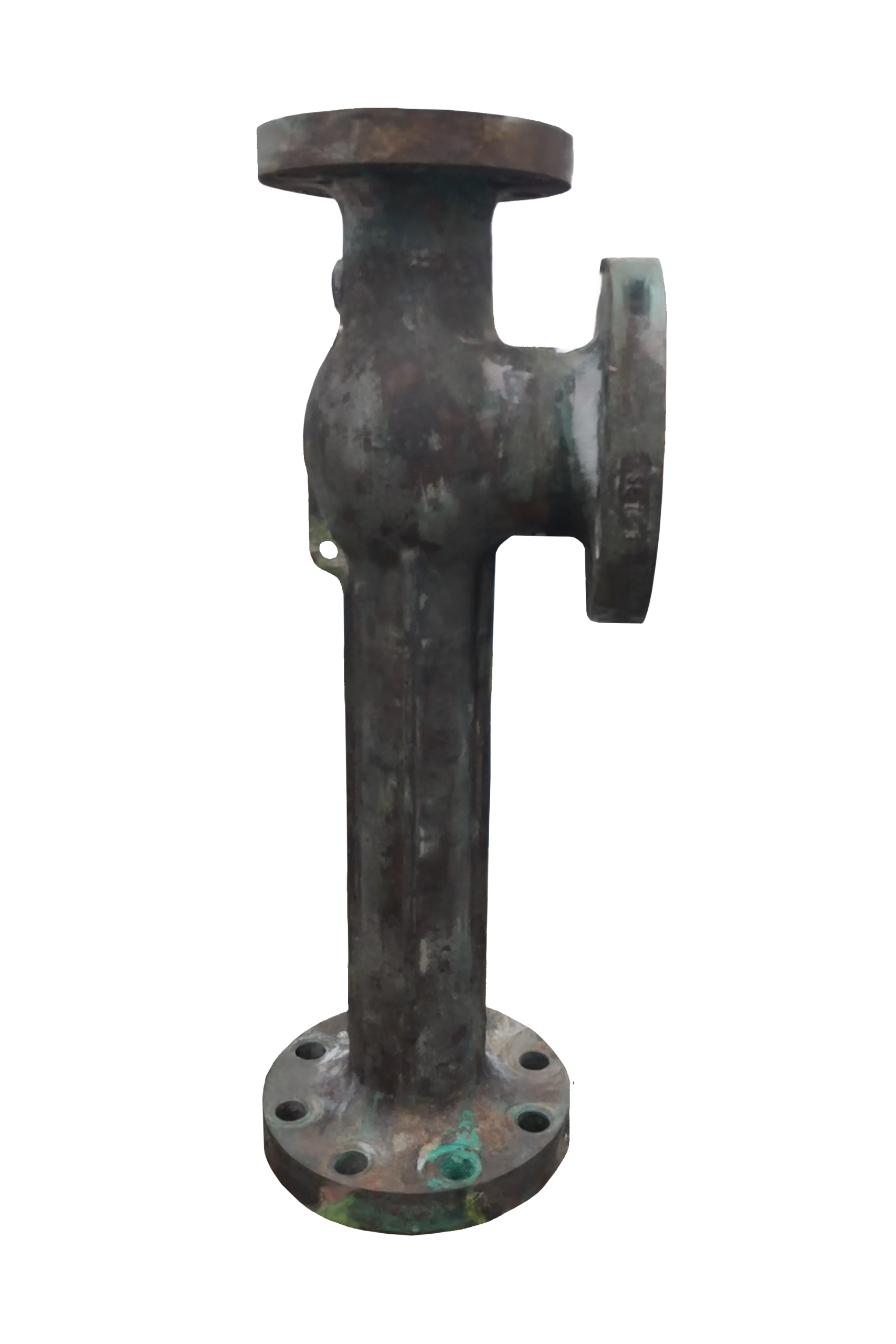
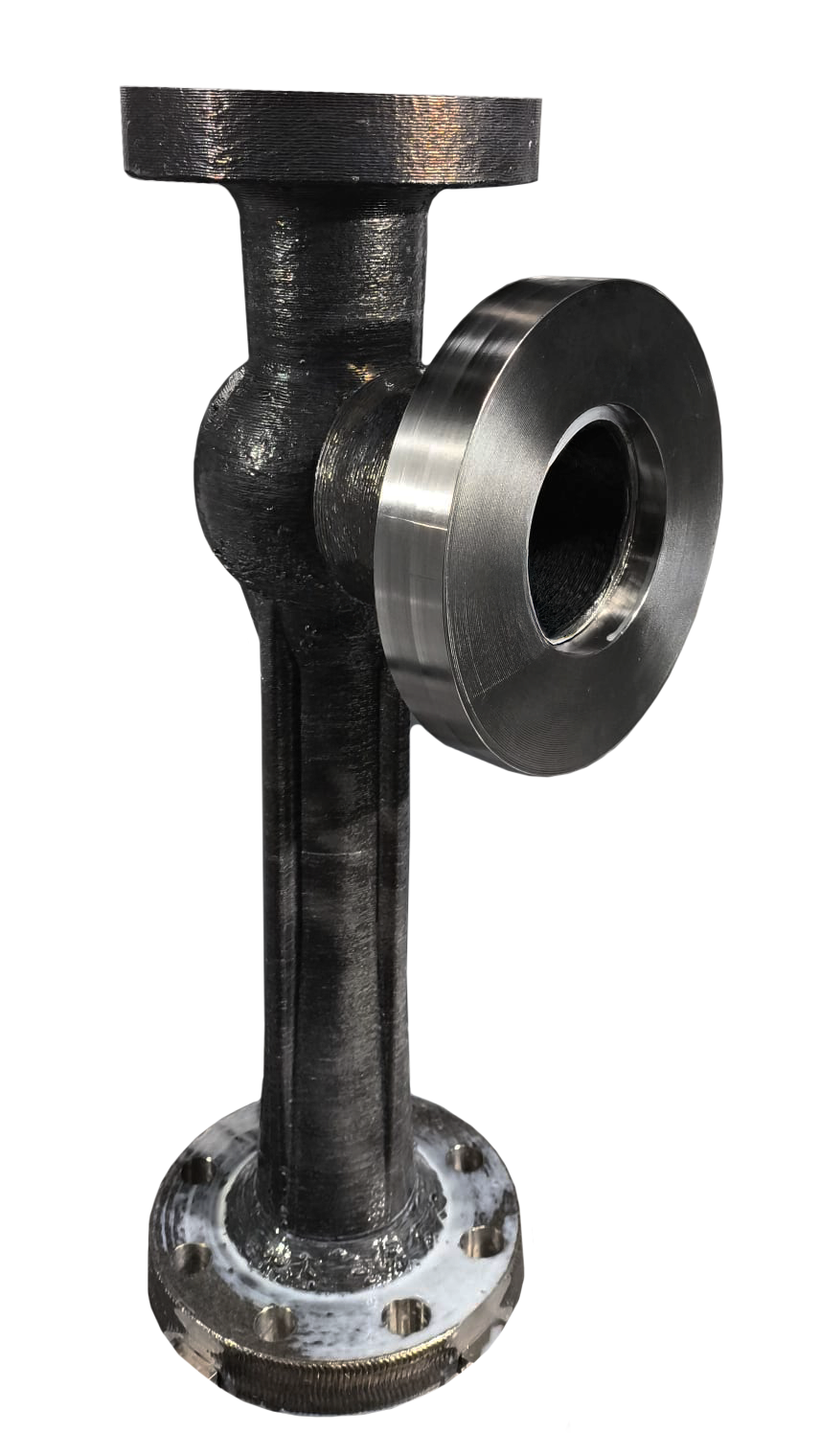
Meltio 3D Printing Solutions
Unlock the potential of metal 3D printing with Meltio. Your journey starts here.
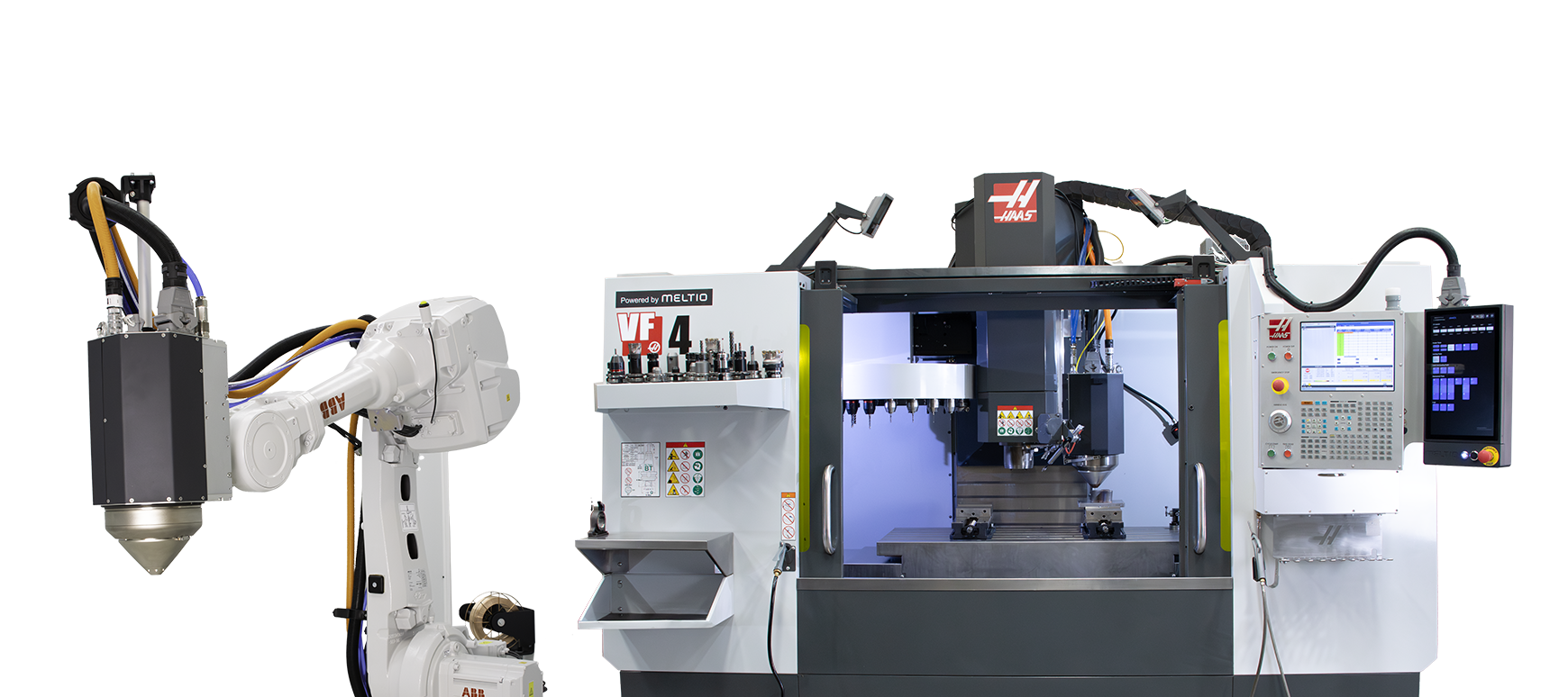
Meltio 3D Printing Solutions
Unlock the potential of metal 3D printing with Meltio. Your journey starts here.
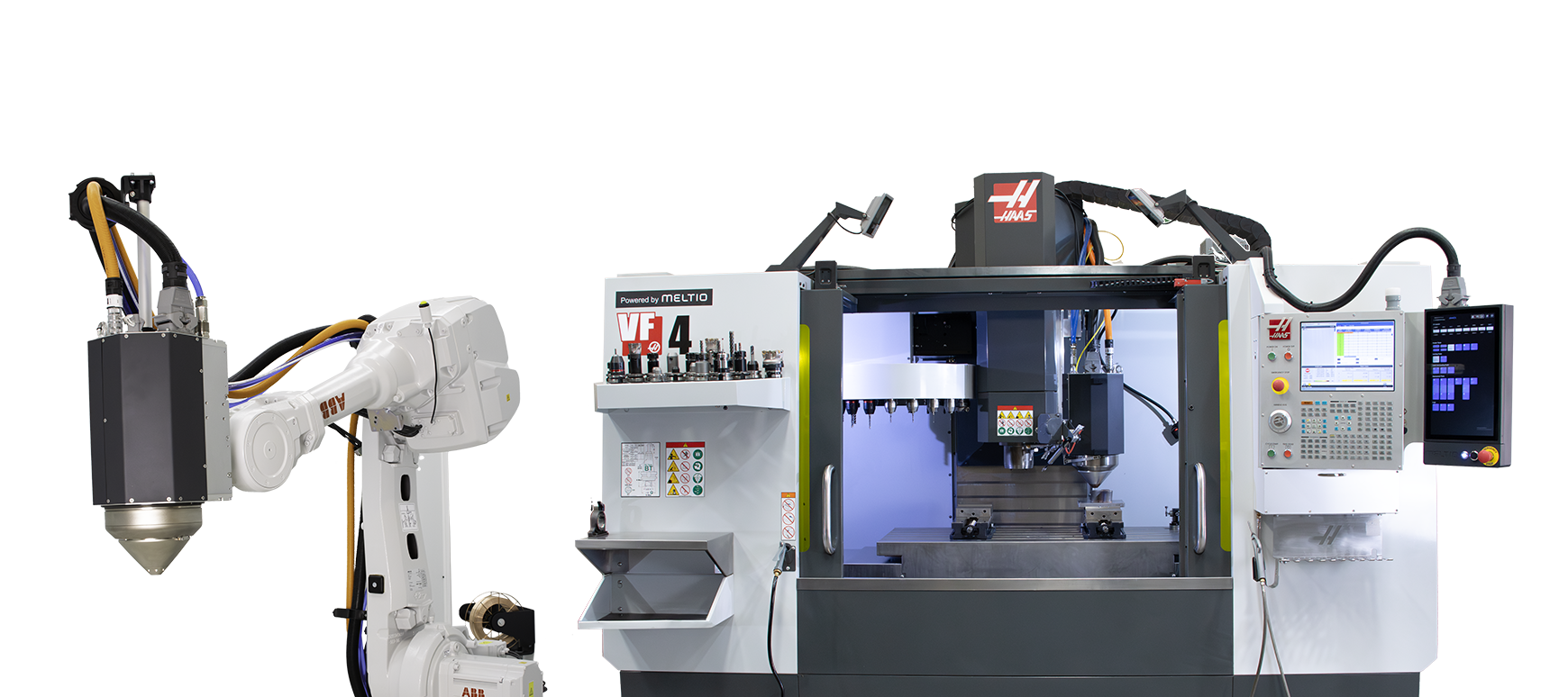
System: Meltio Engine for Robot integration
lt is the perfect platform for large and complex 3D printing, repair, cladding and feature addition.
Sector: Naval
On-site, on-demand production
Material: Stainless Steel 316L
Wire feedstock proves more affordable and safer than powder-based alternatives.
Printing Time: 58h
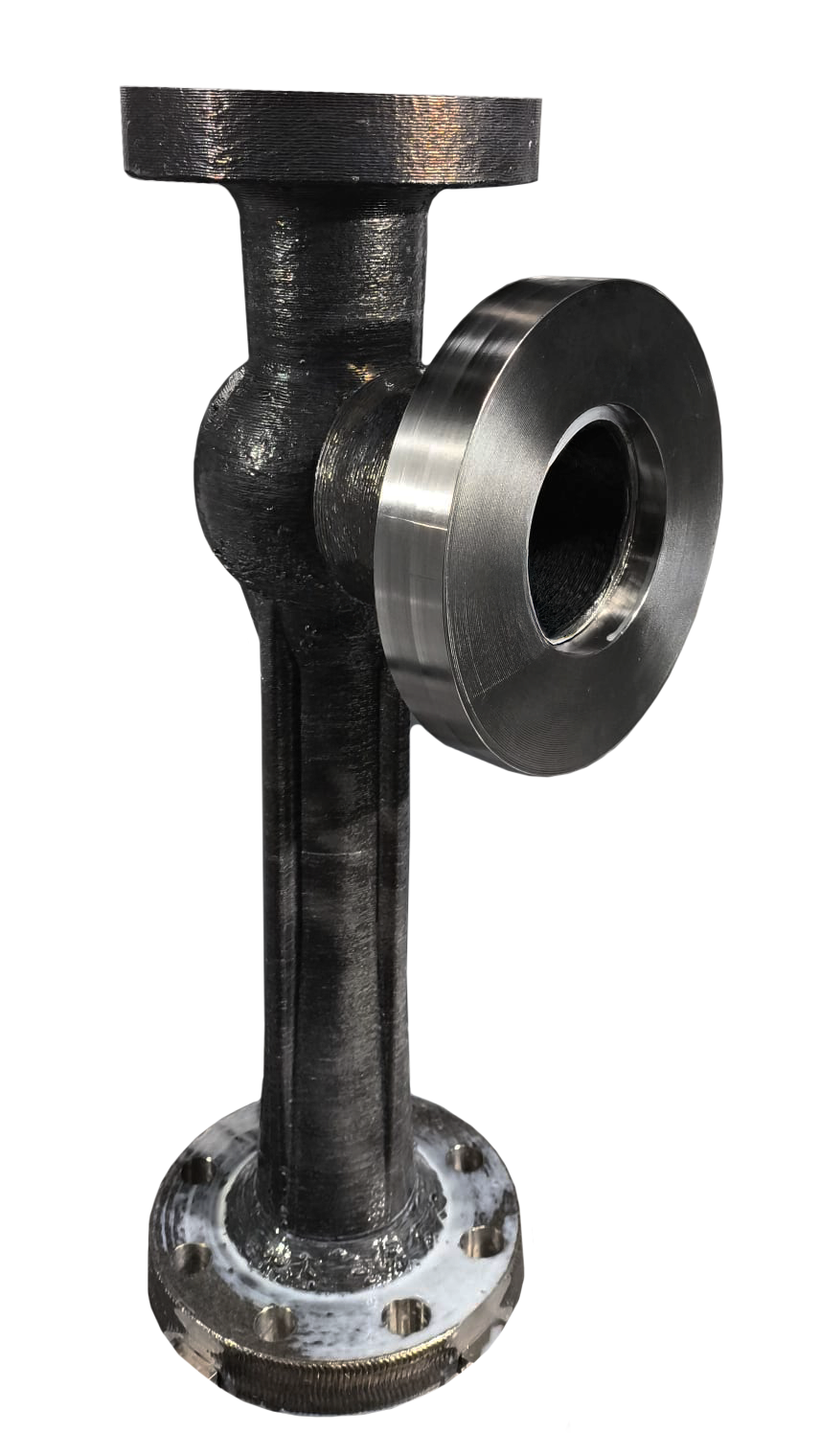
Strategic Advantages for Defense
With Meltio, digitally storing designs and manufacturing them on demand is a game-changer for defense readiness. Eductors, despite being niche components, become resilient to supply chain disruptions.
No molds. No waiting. Just functional parts, printed anywhere — from a naval base to a mobile AM unit.
Want to know more about printed parts properties?
Want to know more about printed parts properties?