Meltio Engine Integration Kit
for Vertical Machining Centers
The most affordable hybrid manufacturing solution, fitting almost any Vertical Machining Center in the market. Enable metal 3D printing and machining of complex geometries in a single process step.
The Meltio Engine is the ideal complement for near-net shape manufacturing, repair and feature addition.

Machining and Additive Manufacturing Platform
Install metal additive capabilities directly to your Vertical Machining Center and 3D print to near net shape and finish machining in a single part setup.
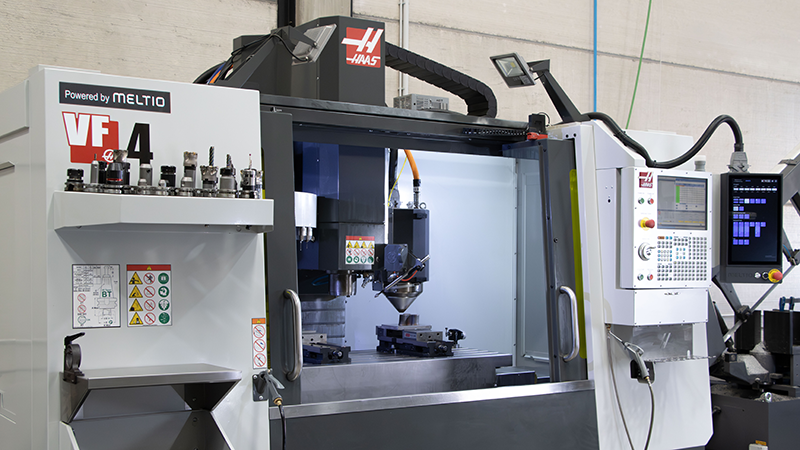
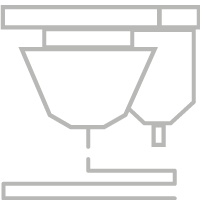
Hybrid Manufacturing
Create highly complex parts with machining tolerances in the same process.
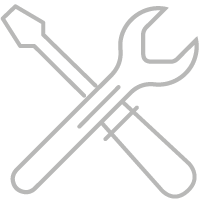
Part Repair
Cost-effective component repair, part augmentation, and feature addition.
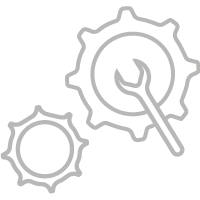
Retrofitting
Provide new capability to any CNC machine by turning it into an hybrid metal manufacturing system.
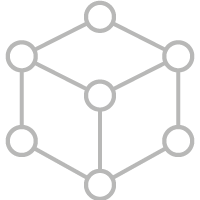
Geometry Freedom
No inherent constraints when the working envelope is only limited by the size of the motion system.
Technical Specifications
New! Meltio Engine Blue Integration kit
Laser System:
Blue Laser (Higher absorption and power efficiency; wider range of compatible materials than IR)
1000W 9 x 450 nm direct diode lasers
Printhead:
Mounted on the right side of the spindle 32.5 to 35 kg
Printhead Retracted Size (WxDxH):
280 x 332 x 684 mm
Printhead Unretracted Size (WxDxH):
280 x 332 x 943 mm
Control Unit:
Mounted on machining center, air-cooled 80.5 kg 600 x 300 x 800 mm. 17″ HMI screen placed beside CNC controller
Cooling:
Water-cooled deposition head. Chiller lncluded
Print Envelope (WxDxH):
Depending on the machining center
Process Control:
Melt Pool Camera & Closed-loop wire modulation
Power Input:
200/240 V 3W+PE 380/415 V 3W+N+PE
Power Consumption:
9,2 kW peak 2-5 kw avg.
Slicer Software:
Meltio relies on its Software Partners Ecosystem for the Hybrid process, including additive and subtractive
Visit Meltio Software Partners for more info
Feeder System:
Quad-point traction servomotor feeder, frictionless liners
Wire Feedstock:
Diameter: 0.8-1.2 mm / Spool Type: 8S300 External wire drum ready
Product Configurations:
Single or Dual Wire
Compatible Materials:
Stainless Steels, Carbon Steels, Tool Steels, Nickel Alloys, Titanium, Copper Alloys, Gold alloys and more
Meltio Engine IR Integration kit
Laser System:
Infrarred Laser
1200W 6 x 976 nm direct diode lasers + fibers & colimators
Printhead:
Mounted on the right side of the spindle 45 kg
Printhead Retracted Size (WxDxH):
255 x 320 x 1075 mm
Printhead Unretracted Size (WxDxH):
255 x 320 x 1135 mm
Control Unit:
Floor Mounted (Wheeled) 125 kg with 27″ HMI screen 390 x 650 x 1600 (deployed screen)
Cooling:
Water-cooled control unit and deposition head. Chiller included
Print Envelope (WxDxH):
Depending on the machining center
Process Control:
Closed-loop, wire modulation
Power Input:
200/240 V 3W+PE 380/415 V 3W+N+PE
Power Consumption:
2 – 5 kW peak depending on selected options
Slicer Software:
Meltio relies on its Software Partners Ecosystem for the Hybrid process, including additive and subtractive
Visit Meltio Software Partners for more info
Feeder System:
Dual traction stepper motors + External Feeder (Push-pull system), conventional wire liners
Wire Feedstock:
Diameter: 0.8-1.2 mm / Spool Type: 8S300 External wire drum ready
Product Configurations:
Single or Dual Wire
Compatible Materials:
Stainless Steels, Carbon Steels, Tool Steels, Nickel Alloys, Titanium and more
New! Meltio Engine Blue Integration kit
General Specifications
Laser System:
Blue Laser (Higher absorption and power efficiency; wider range of compatible materials than IR)
1000W 9 x 450 nm direct diode lasers
Printhead:
Mounted on the right side of the spindle 32.5 to 35 kg
Printhead Retracted Size (WxDxH):
280 x 332 x 684 mm
Printhead Unretracted Size (WxDxH):
280 x 332 x 943 mm
Control Unit:
Mounted on machining center, air-cooled 80.5 kg 600 x 300 x 800 mm. 17″ HMI screen placed beside CNC controller
Cooling:
Water-cooled deposition head. Chiller lncluded
Print Envelope (WxDxH):
Depending on the machining center
Process Control:
Melt Pool Camera & Closed-loop wire modulation
Power Supply
Power Input:
200/240 V 3W+PE 380/415 V 3W+N+PE
Power Consumption:
9,2 kW peak 2-5 kw avg.
Materials & Software
Slicer Software:
Meltio relies on its Software Partners Ecosystem for the Hybrid process, including additive and subtractive
Visit Meltio Software Partners for more info
Feeder System:
Quad-point traction servomotor feeder, frictionless liners
Wire Feedstock:
Diameter: 0.8-1.2 mm / Spool Type: 8S300 External wire drum ready
Product Configurations:
Single or Dual Wire
Compatible Materials:
Stainless Steels, Carbon Steels, Tool Steels, Nickel Alloys, Titanium, Copper Alloys, Gold alloys and more
Meltio Engine IR Integration kit
General Specifications
Laser System:
Infrarred Laser
1200W 6 x 976 nm direct diode lasers + fibers & colimators
Printhead:
Mounted on the right side of the spindle 45 kg
Printhead Retracted Size (WxDxH):
255 x 320 x 1075 mm
Printhead Unretracted Size (WxDxH):
255 x 320 x 1135 mm
Control Unit:
Floor Mounted (Wheeled) 125 kg with 27″ HMI screen 390 x 650 x 1600 (deployed screen)
Cooling:
Water-cooled control unit and deposition head. Chiller included
Print Envelope (WxDxH):
Depending on the machining center
Process Control:
Closed-loop, wire modulation
Power Supply
Power Input:
200/240 V 3W+PE 380/415 V 3W+N+PE
Power Consumption:
2 – 5 kW peak depending on selected options
Materials and Software
Slicer Software:
Meltio relies on its Software Partners Ecosystem for the Hybrid process, including additive and subtractive
Visit Meltio Software Partners for more info
Feeder System:
Dual traction stepper motors + External Feeder (Push-pull system), conventional wire liners
Wire Feedstock:
Diameter: 0.8-1.2 mm / Spool Type: 8S300 External wire drum ready
Product Configurations:
Single or Dual Wire
Compatible Materials:
Stainless Steels, Carbon Steels, Tool Steels, Nickel Alloys, Titanium and more
Applications
Meltio Engine Integration kit for Vertical Machining Centers

Aircraft Bracket
Titanium 64
Size:
109.6 x 160.8 x 34.8 mm
Weight:
1.50 kg
Print time:
13h 33′
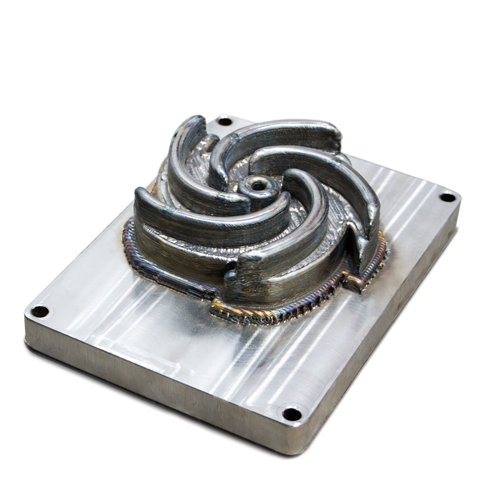
Semi-Open Impeller
Stainless Steel 316L + Nickel 625
Size:
73 x 48 x 17 mm
Weight:
Stainless Steel 316L: 1.46 kg + Nickel 625: 0.1 kg
Print time:
10h

Gas Turbine Blade Repair
Nickel 625
Size:
65 x 29 x 6 mm
Weight:
0.015 kg
Print time:
6h 16′

Aircraft Bracket
Titanium 64
Size:
109.6 x 160.8 x 34.8 mm
Weight:
1.50 kg
Print time:
13h 33′
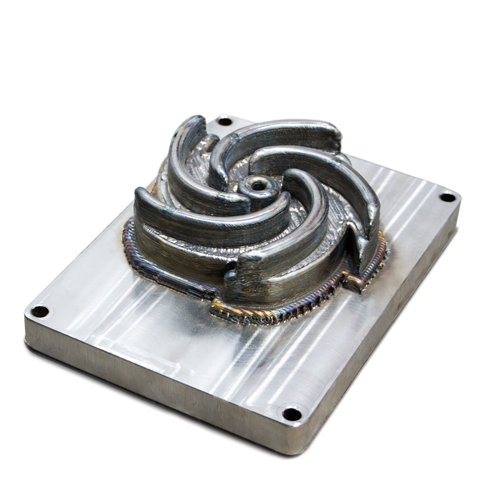
Semi-Open Impeller
SS316L
Size:
73 x 48 x 17 mm
Weight:
Stainless Steel 316L: 1.46 kg + Nickel 625: 0.1 kg
Print time:
10h

Gas Turbine Blade Repair
Nickel 625
Size:
65 x 29 x 6 mm
Weight:
0.015 kg
Print time:
6h 16′
Wire LMD for the Machine Shop
Join us for an insightful webinar held together with Phillips Corporation to discover cutting-edge advancements in metal 3D printing and its game-changing applications for machine shops.
Wire LMD for the Machine Shop
Join us for an insightful webinar held together with Phillips Corporation to discover cutting-edge advancements in metal 3D printing and its game-changing applications for machine shops.
Meltio Materials
Meltio’s Laser Metal Deposition process achieves exceptional material mechanical properties using single, dual and quad wire. Choose the ideal welding wire for your application: unlimited third-party commodity material or qualified Meltio Wire Materials that secure the user experience.
Meltio Materials
Meltio’s Laser Metal Deposition process achieves exceptional material mechanical properties using single, dual and quad wire. Choose the ideal welding wire for your application: unlimited third-party commodity material or qualified Meltio Wire Materials that secure the user experience.
Metal 3D Printing Experiences
Francesc Martínez
R&D Integrations Director / Sivó
” If we compare with other makers of laser, with Meltio we’ve had the clearer deposition in thousands of parts, and that is nice to see. We can also make some parts that are impossible to make without Meltio’s technology.
We can produce one part with one configuration, then another one with a total different one. Without Meltio’s technology, we wouldn’t be able to do it because the costs would be too high. “
Sivó is a Spanish company specialized in the repair of glass molds using a Meltio Engine CNC Integration.
Get a Quote
Meltio Engine Integration kit for Vertical Machining Centers
Receive a tailor-made offer within 1 – 2 business days.
