The ADIVAT project (Transfer of Latest Generation Additive Manufacturing Technologies for Prototyping High Added Value Components for the Transport Sector), focuses on the transfer of knowledge in additive manufacturing technologies applied to the development of prototypes and final parts for the transport sector, mainly focused on the naval, railway and automotive industries. The unique wire-laser metal 3D printing solutions for industries developed by Meltio are participating in this project.
Throughout this blog, we will see what exactly the ADIVAT project consists of, which printing technologies are involved in this project and the action lines.
Steps to manufacture a metal printed part with AM
In this project, CETEMET, The Spanish Technology Centre of Metalmechanical and Transport, offers the possibility of manufacturing the part, component or prototype of any company interested in applying the additive manufacturing (AM) process. Any company interested in applying this new process can directly contact with the coordinator of the project, Dr. Julia Ureña Alcázar.
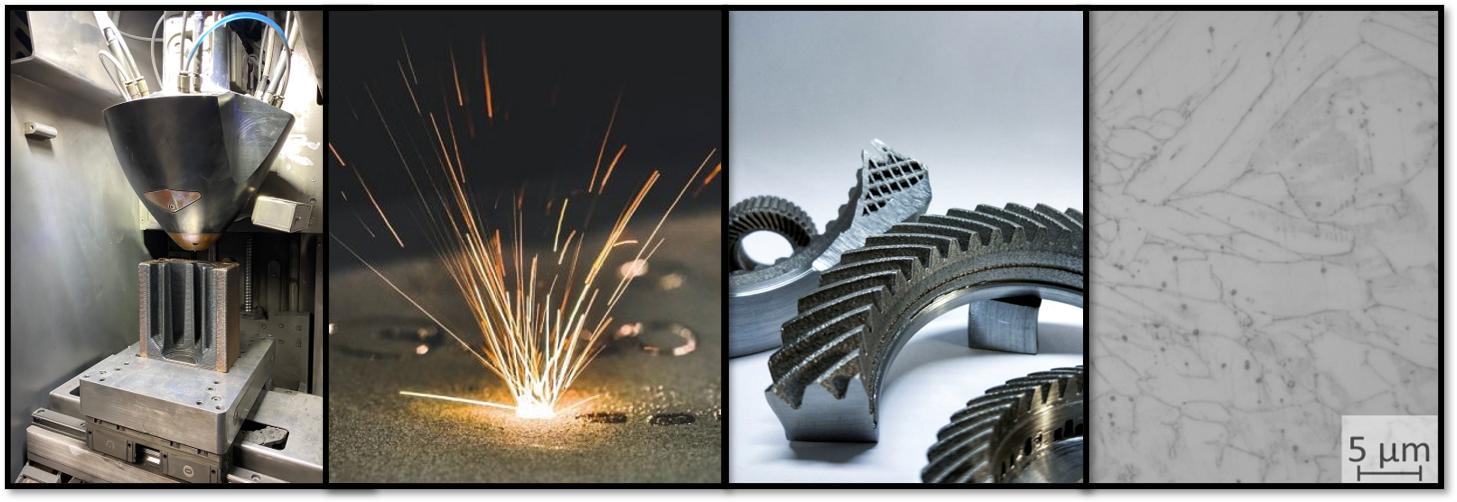
Technologies involved in this project
Laser Metal Deposition (LMD), a Directed Energy Deposition (DED) process
DED or LMD technology is based on direct energy deposition using a focused energy source (laser) to melt the material, which is deposited on a build plate, through a nozzle, while the energy source melts it. This procedure is carried out repeatedly, layer by layer. Each layer solidifies, creating the geometry previously defined in the CAD model.
DED technologies offer great advantages over other additive manufacturing technologies like the great variety of materials that can be processed, the improvement of the mechanical properties of the manufactured components, the high deposition ratio and the reduction of material needed in the process stand out.
TIP: Check the benefits of 3D printing metal parts using Meltio’s LMD process.
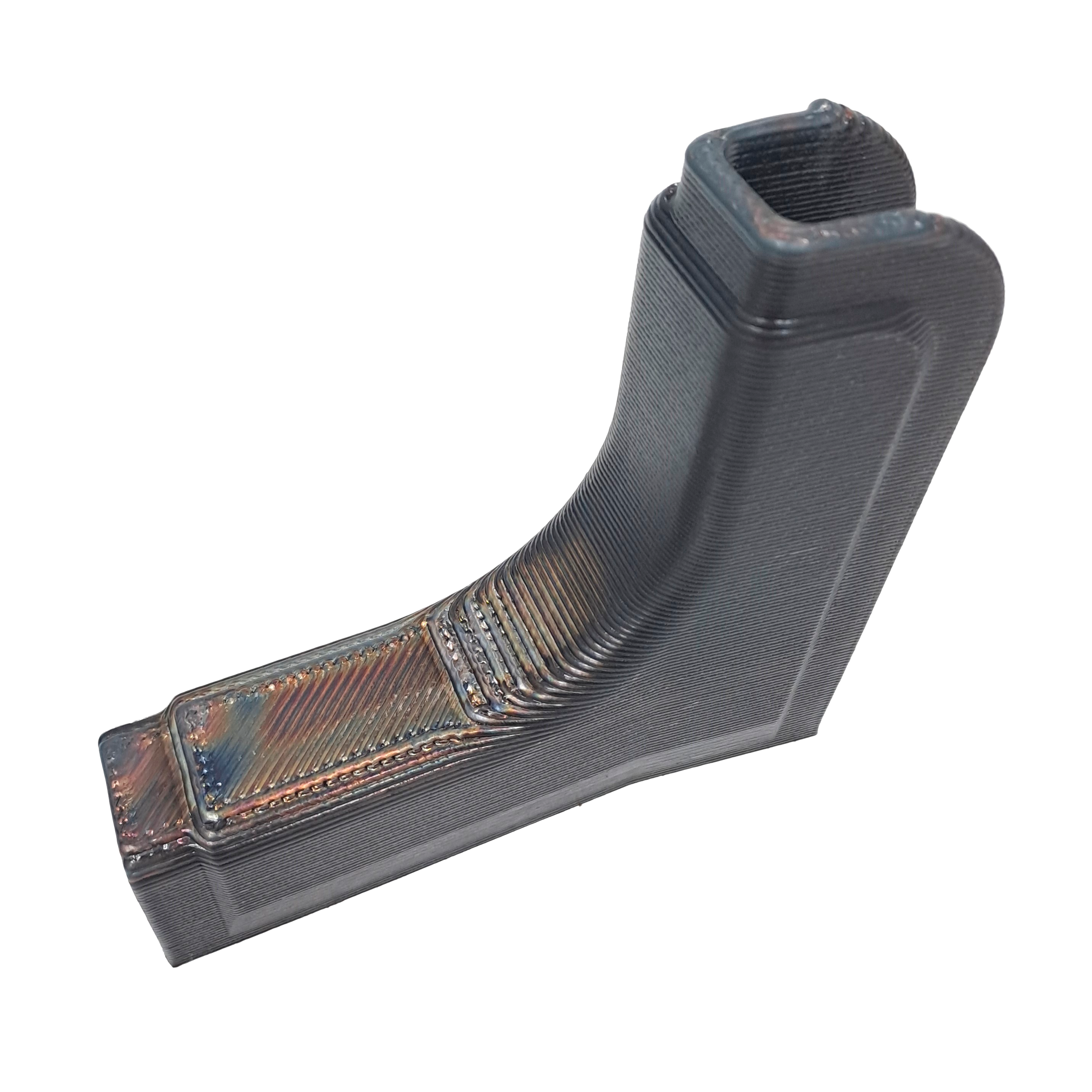
Industrial component of the railway sector (CAF DDS company) additively manufactured by DED-wire technology (printed part with wire-laser metal 3D printer Meltio M450 from Meltio) at CETEMET facilities.
In addition, there is equipment capable of manufacturing large parts, depending on the actual manufacturing volume of the machine. However, its main drawbacks are the difficulty of processing parts with complex geometries and the need for post-processing to achieve an optimalo surface finish. Its main use is focused on both the manufacturing and repair of parts or components and its application is increasingly common in various sectors such as industrial, aeronautical and aerospace, among others.
In this project, the technology will be applied to process metallic materials in wire format (DED-wire technology). Main materials that can be processed: Stainless steels, Tool steels, Nickel-based superalloys, Copper alloys and multi-material.
Laser Powder Bed Fusion (L-PBF):
L-PBF technology is a metal additive manufacturing method that uses selective laser melting in a powder bed to create metal parts with complex geometries. This technology allows a wide variety of metallic materials and alloys to be processed starting from powder material. This additive manufacturing method offers numerous advantages, including geometric complexity, reduced weight of the manufactured parts and the number of parts processed in a single production.
Possible disadvantages include the need for special peripheral equipment for the manufacturing process and the higher cost of the powder material. Laser powder bed fusion is present in sectors as diverse as the industrial, aerospace and prosthetic sectors, among others. Main materials to be processed: Stainless steels, Tool steels, Nickel-based superalloys, Titanium alloys and Aluminium alloys.

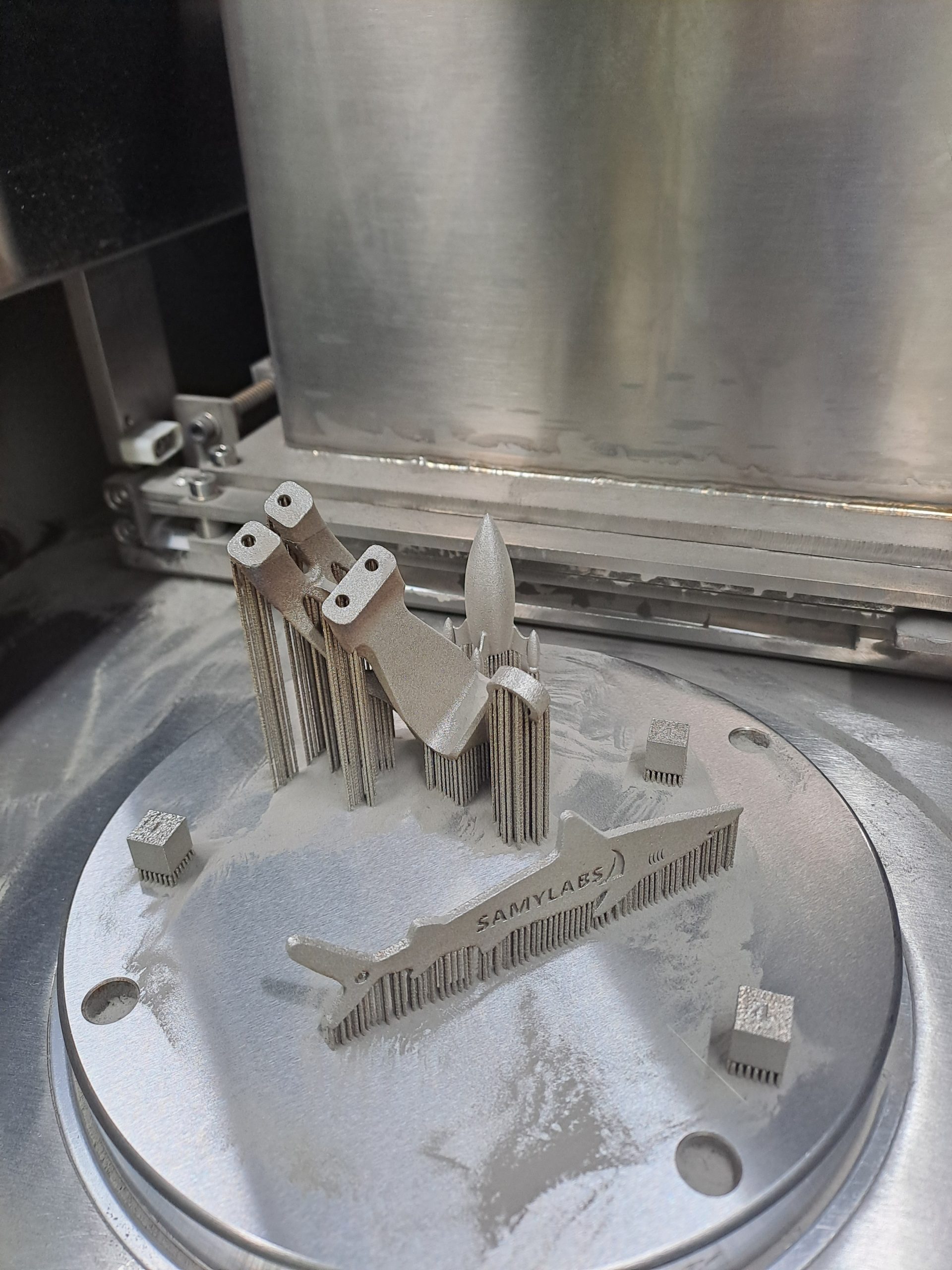
Material Extrusion (MEX), also known as Fused Deposition Modelling (FDM):
This process consists of the extrusion of a thermoplastic in filament format, which is melted and deposited on a previously deposited solid layer, in such a way that the heat of the molten material re-melts the solidified layer so that both adhere and form a single piece. It is a highly efficient process compared to traditional methods, which means savings in costs and processing time. Its numerous advantages include ease of use, the wide variety of processable polymers and the broad spectrum of possible applications, from functional prototyping to the manufacture of final parts ready for use. However, this technology has some limitations, especially with regard to the manufacture of cantilevered parts, for which the use of supports is necessary to maintain the geometry of the part during manufacturing. FDM technology is very present in the industrial field (automotive, aerospace, robotics) offering effective solutions at low cost.
TIP: Discover how to expand your manufacturing capabilities with the Meltio Engine Robot Integration here.
Action Lines
1. Application of the additive manufacturing process using technologies for the processing and development of metallic, polymeric and/or multi-material materials with improved properties.
2. Development of innovative products for companies in the transport sector, manufacturing customized products with tailored designs and established needs and requirements.
3. Design activities, topological optimization and simulation to support the manufacturing of complex components previously established by the project’s collaborating companies.
4. Boosting and strengthening the Technological Centre in the field of Additive Manufacturing and Advanced Materials, specifically the Department of Advanced Materials and its Advanced Manufacturing Laboratory, through the acquisition of new state-of-the-art manufacturing technology for processing metallic powder materials. Thanks to this project, the Centre is establishing a new line of research with powder bed technology (L-PBF) that allows the processing of metallic powder materials such as aluminium, titanium, steels or nickel-based superalloys.
5. Continuation of the Centre’s commitment to the generation of highly qualified employment and investment in innovation and new advanced technologies.
The ADIVAT project execution period is 2 years and runs from December 2023 to November 2025. The project has an accepted budget of €241,270.85.
An incentive has been received from the Andalusian Innovation and Development Agency IDEA, of the Andalusian Government, for an amount of € 176,270.85; 80 % co-financed by the European Union through the European Regional Development Fund, ERDF, for the implementation of the ADIVAT project, Transfer of Latest Generation Additive Manufacturing Technologies for Prototyping of High Added Value Components for the Transport Sector with the aim of promoting the collaboration of the agents of the Andalusian Knowledge System with the socio-productive fabric, following the line of action of Transfer of technologies and manufacturing processes.
The project is funded thanks to the 2022 call for grants for carrying out knowledge transfer activities between the Agents of the Andalusian Knowledge System and the productive fabric (Line 4.7) within the framework of the Andalusian Plan for Research, Development and Innovation (PAIDI 2020) initiative of the University, Research and Innovation body of the Junta de Andalucía. Project Reference: AT22CCTT_00017.
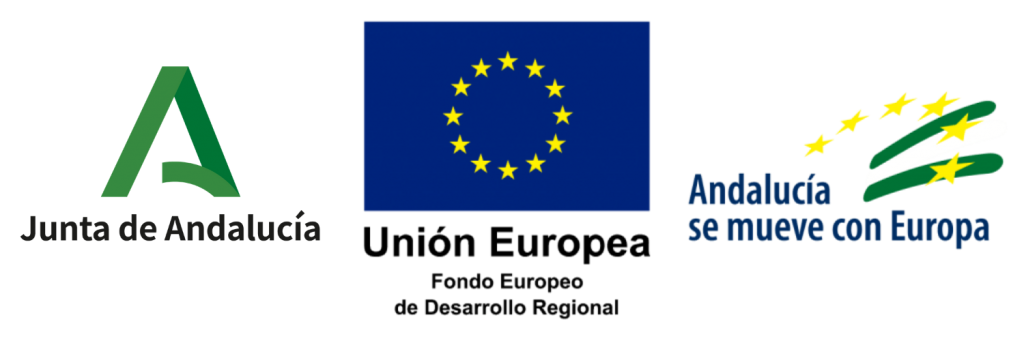